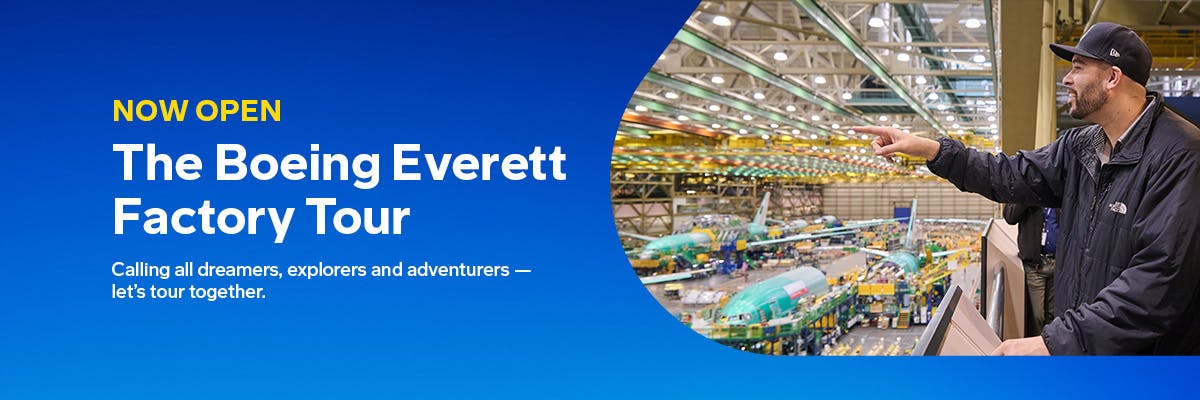
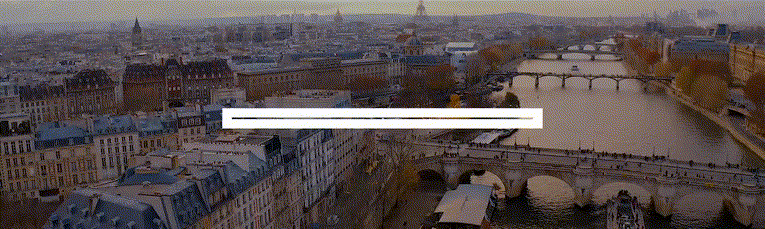
Let's Tour Together
Step inside the world's largest factory for a behind-the-scenes look at the Boeing Everett Factory and 777 assembly line. Each tour is an 80-minute guided experience with a front row view of current airplane production, the Everett site’s history and the central role it plays in the future of commercial aviation.
Pro-Tip: Tickets sell out quickly. We recommend booking tickets in advance, either online or through the Call Center: +1 (800) 464-1476
Tour Schedule: Offered Thursday – Monday. Select 'Buy Tickets' to check availability.
Know Before You Go
Safety requirements.
- Children/Youth must be at least 4 feet (48in/122cm) tall to go on the tour.
- Carrying children on the tour is not allowed for safety reasons.
- Children/Youth under 16 must be accompanied by an adult.
Restricted Items
This is a hands-free tour. Complimentary lockers are available to use in the lobby. Please store all belongings before your tour time begins. Items NOT allowed on the Boeing Everett Factory Tour:
- No purses, handbags, waist pouches or backpacks
- No binoculars and electronics including cameras, video equipment or drones
- No phones or tablets
- No food or drinks
- No smoking or vaping
Refunds and Restrictions
- If guests do not arrive promptly for their scheduled tour the reservation will be forfeited*. We strongly recommend guests arrive at least 30 minutes before their tour start time.
- Refunds will be provided with at least 24-hour notice of cancellation. No refunds will be made within 24 hours of your scheduled tour.
- In order to request a reservation modification of any kind, please call Boeing Future of Flight Customer Service at +1 (800)-464-1476 .
* If an emergency arises, we will attempt to reschedule your tour if you call at least one hour in advance of your scheduled tour time (depending on availability).
The Boeing Company reserves the right to cancel the tour at any time for any reason.
Accessibility
- Boeing Future of Flight is an accessible facility. Please contact Boeing Future of Flight Customer Service in advance at [email protected] or call +1 (800) 464-1476 for special accommodations requests, including booking our wheelchair-accessible bus tour. For more information regarding our accessibility accommodations, please visit our Accessibility page.
- Participation on the Boeing Everett Factory Tour requires traveling approximately .3 miles (.5km) round trip. There are flights of stairs to navigate; however, elevators are accessible on all floors at Boeing Future of Flight and the Boeing Everett Factory Tour.
Restrooms are not available during the tour. Please plan ahead by using the restrooms at Boeing Future of Flight before your tour start time.
Stay in the Know!
Join our email list to be the first to know about new experiences, events and promotions.
Step inside Boeing's South Carolina Dreamliner factory

For most of its history, Boeing has been synonymous with the Seattle area. Although the global aerospace company has facilities across the U.S. and abroad, it was founded in Seattle, and for most of its history, it built its commercial aircraft at two Seattle-area factories.
In 2011, Boeing opened a third commercial factory, this one in Charleston, South Carolina.
The new location came to be after Boeing purchased the South Carolina-based operations of two suppliers in 2008 and 2009: Vought Aircraft Industries and Global Aeronautica, which built components for Boeing.
Boeing absorbed both operations and combined them, before opening a final 787 assembly and delivery line on the site two years later.
Want more airline-specific news? Sign up for TPG's free biweekly Aviation newsletter .
The Charleston site operates alongside Boeing's Everett factory in Washington state, which produces wide-body commercial jets.
Boeing said that it needed the second assembly line in order to "expand our production capability to meet the market demand for the airplane" and that it chose the Charleston site due to the component work already being done on the property.
However, the announcement came during a period of turbulent relations with its Washington-based union, leading to allegations that the plane-maker was attempting to illegally circumvent the union. Boeing has since allegedly fought any effort by Charleston workers to unionize.
Boeing said in 2020 that it would consolidate 787 production in Charleston instead of splitting it between South Carolina and Washington, a move which was completed the following year.
TPG had a chance to tour the factory last December ahead of an event marking United Airlines' new order for up to 200 airplanes .
Saying that Boeing makes the Dreamliners at its factory is a bit misleading because Boeing — just like Airbus, Embraer and other airframe makers — doesn't actually manufacture much of the plane itself.
More: The 787 Dreamliner: What are the differences between an -8, -9 and -10?
Instead, the company outsources components to specialized manufacturers, while building a few parts itself. Then, Boeing gathers each of the components and assembles them as the final product.
So really, the Charleston facility is more of an assembly plant.
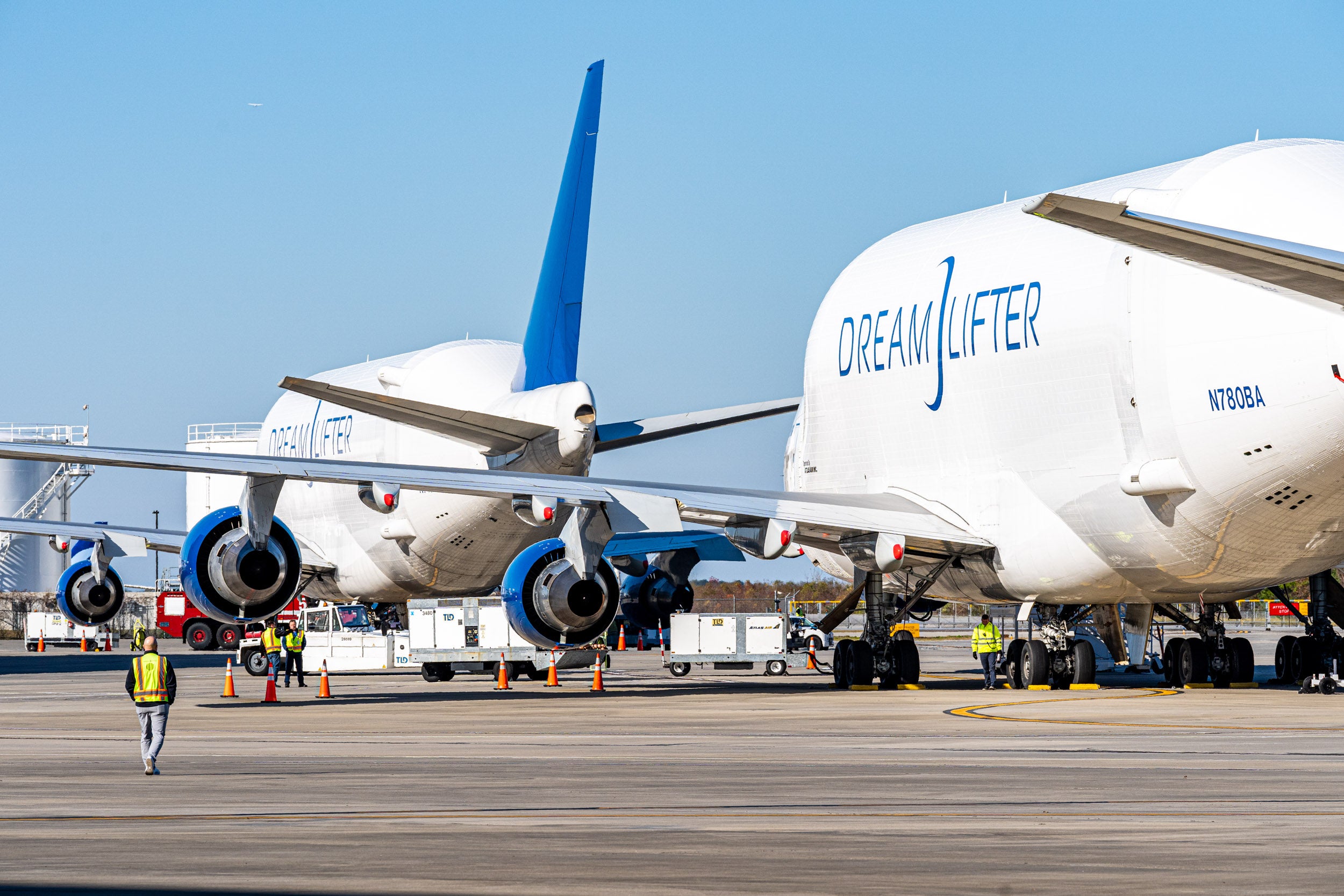
Because of this, as you drive around the facility, which is located on the grounds of the airport, you won't only see 787s in various states of completion. You'll also spot a rare aircraft type: Boeing's custom "Dreamlifter."
The Dreamlifter is a converted 747-400 with roughly triple the cargo volume thanks to its bulbous hull. Boeing designed the type in the mid-2000s specifically to transport large components for the 787 — such as wings — from suppliers to its manufacturing plant. Other oversized cargo aircraft at the time were too small.
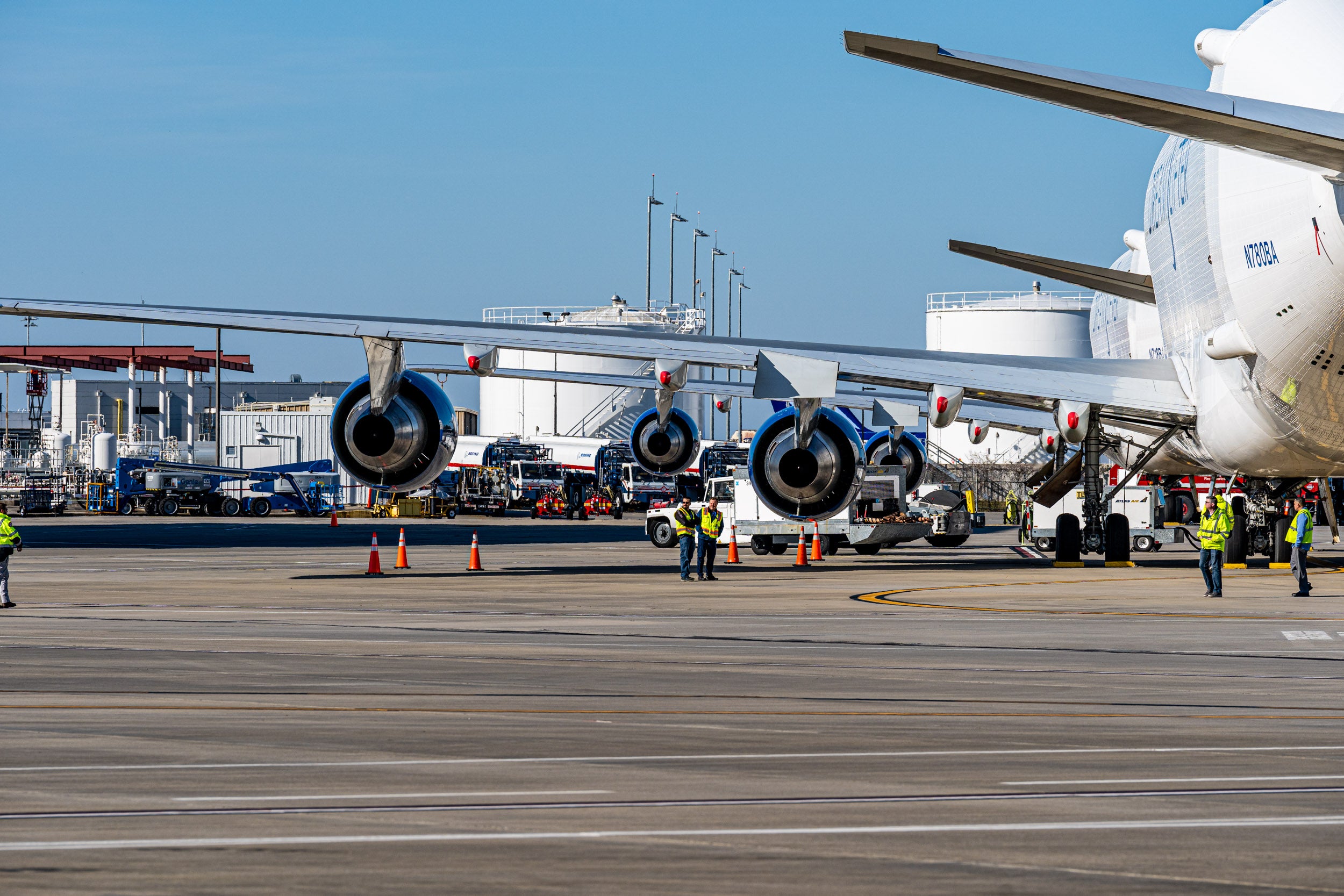
The four Dreamlifters, which are operated for Boeing by cargo carrier Atlas Air, primarily pick up Dreamliner wings, made by Mitsubishi Heavy Industries in Japan, as well as several fuselage sections, frames, horizontal stabilizers and other parts from Leonardo in Italy, and drop them off in Charleston.
The Dreamlifters also deliver disassembled sections of the main fuselage, which are built by several suppliers including Spirit AeroSystems in Wichita, Kansas, Leonardo in Italy and Kawasaki in Japan. Meanwhile, thousands of other components are shipped using a variety of modes of transportation.
During TPG's visit, two of the Dreamlifters were on-site.
Boeing still builds some components itself, though — in particular the aft section, or back, of the airplane.
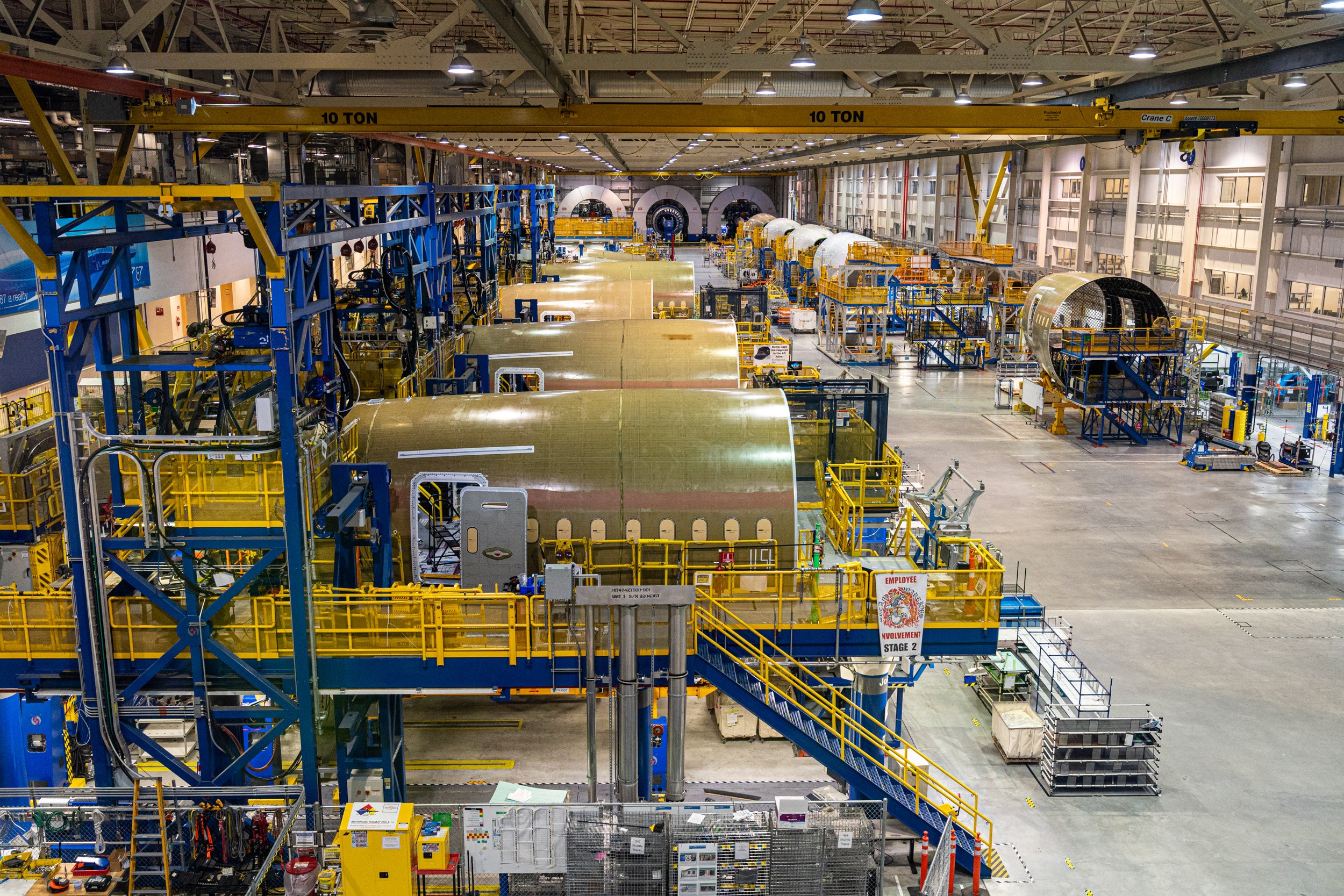
Unfortunately, Boeing asked us to agree not to photograph some parts of the facility, since it uses proprietary technology and methods in the manufacturing process. Still, we were able to get a look and take photos in some areas.
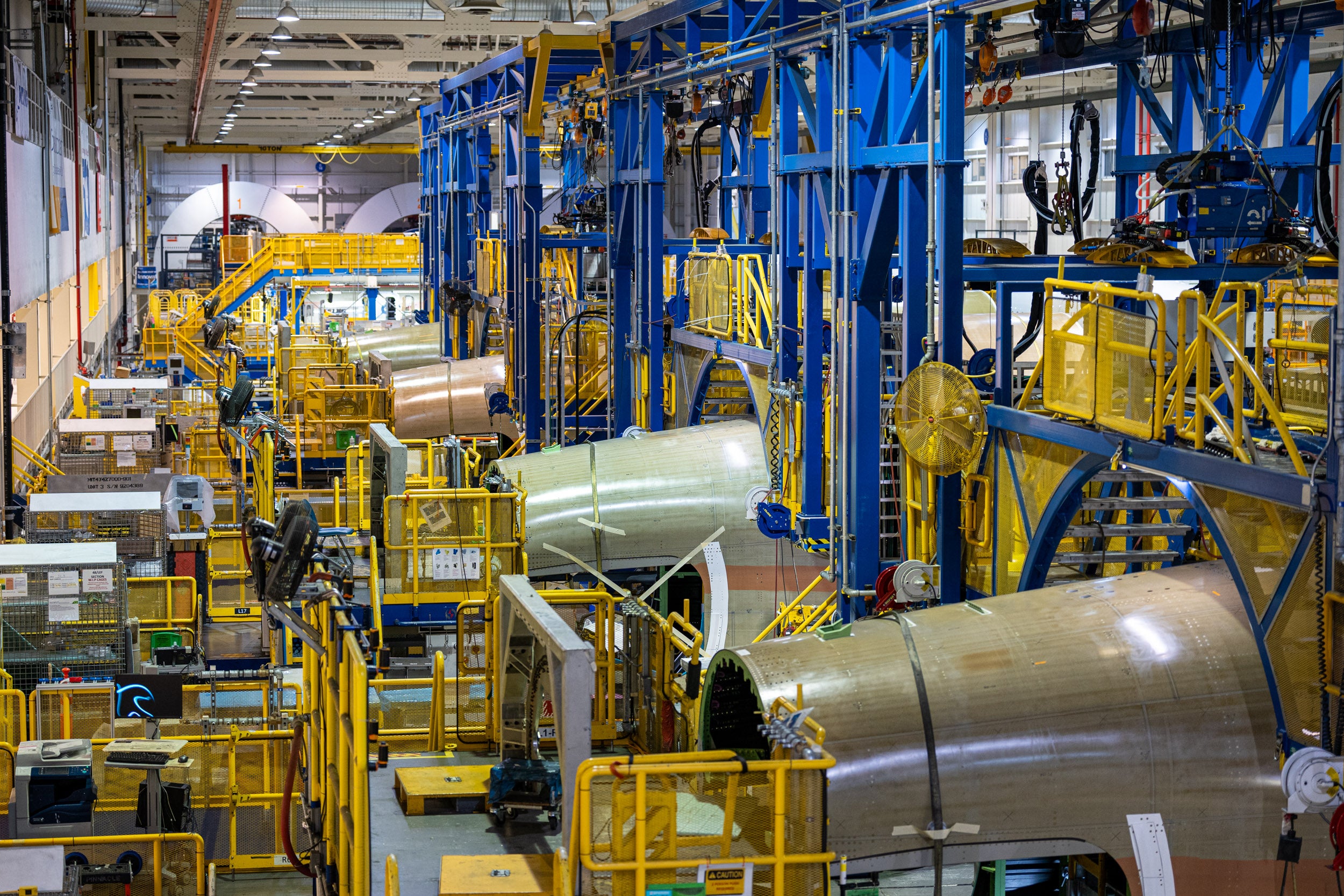
Once the aft section is completed, workers bring it over to a final assembly building.
There, the aft section is joined to the fuselage, and the wings and other structures are attached to the main body. The plane moves down the assembly line, and the aircraft interiors are installed, along with flight control systems. The vertical stabilizer has already been painted by the time the plane enters final assembly, and the livery is applied to the rest of the aircraft once it completes its run through the assembly line.
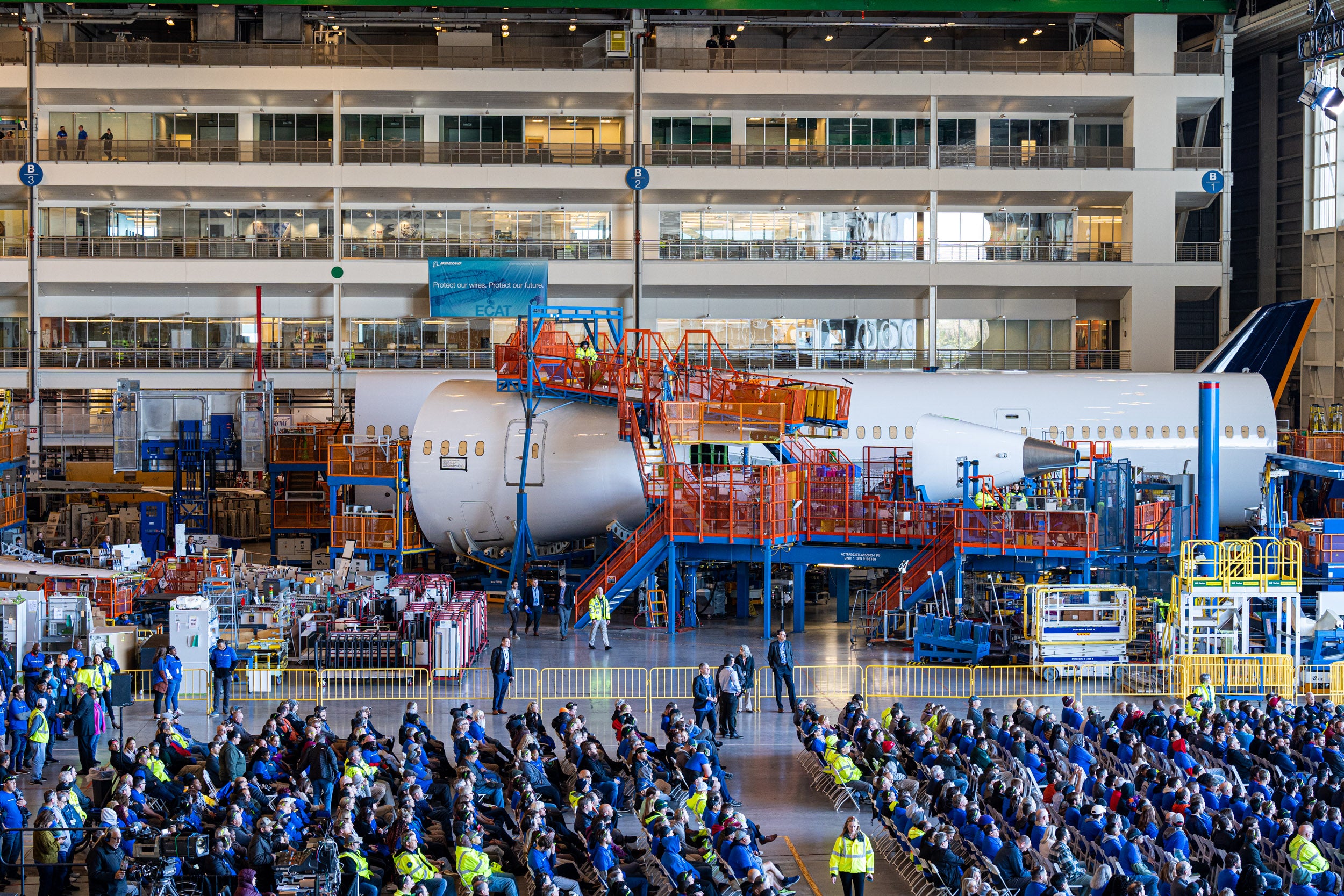
Finishing touches are put on, and each individual airplane is flown for a grueling test program before being delivered. During TPG's tour, a 787-9 bound for Turkish Airlines landed after returning from nearly three hours of testing over the Atlantic Ocean.
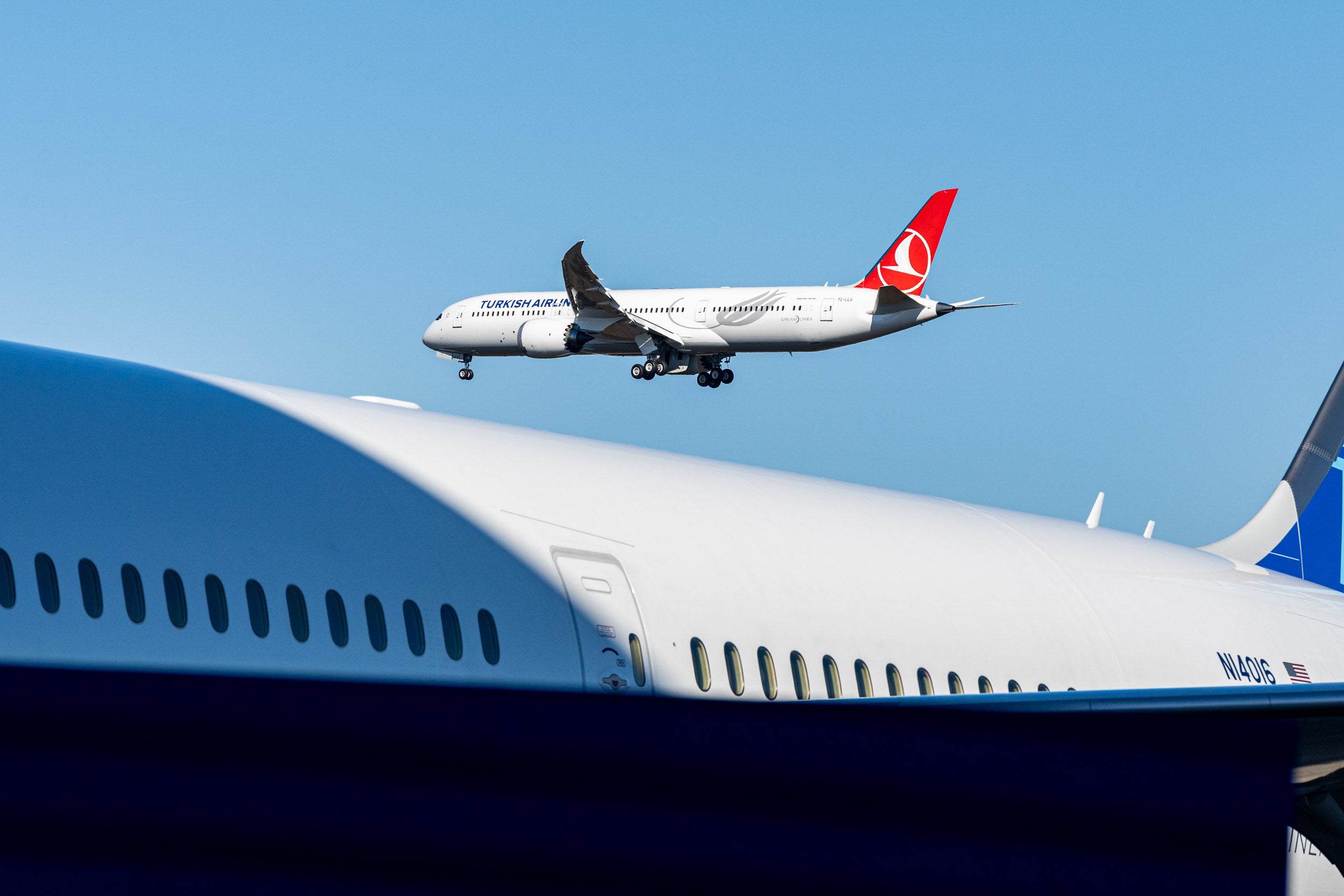
The Charleston facility has 787s parked all around waiting to be delivered. The Federal Aviation Administration ordered 787 deliveries to pause in mid-2021 after numerous concerns arose surrounding Boeing's quality control process in Charleston. Deliveries resumed late last summer .
Because of the year-plus pause in deliveries, which came just as air travel demand was beginning to return following pandemic-era lows, Boeing is working to get a backlog of completed airplanes to airline customers.
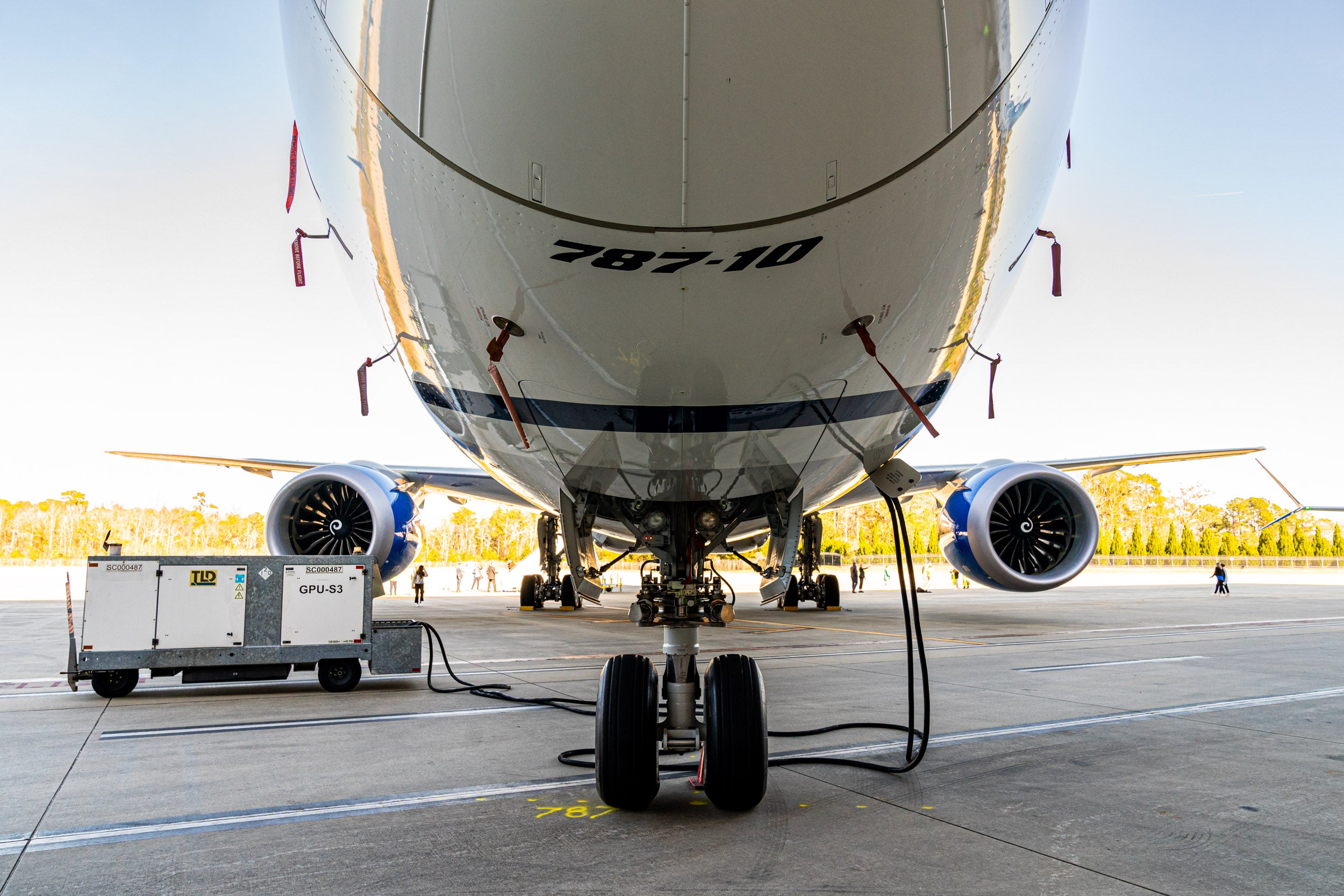
Between the pandemic and the delivery pause, the company also slowed the production line. Boeing is targeting a rate of five completed Dreamliners each month, according to Lisa Fahl, senior director of quality.
The line peaked at 14 new airplanes per month between Charleston and Everett, Fahl said, suggesting that output could scale up in the future.
It's not clear when production will speed up, but as United's order demonstrates, there's heavy demand for new Dreamliners — and there will likely continue to be for years to come.
Sign Up for Updates

787 Dreamliner Factory: North Charleston, SC
Virtual site tours.
See innovation in action with a series of Virtual Site Tours hosted by Boeing. Students will be transported around the U.S . to visit unique Boeing facilities, where they’ll learn more about the people and products leading the way to the future of air travel. Each video is paired with a companion activity that incorporates project-based learning, student collaboration, and hands-on STEM problem-solving.
Learn about the 787 Dreamliner
Want to know how aerospace innovations get off the ground? Get an inside look at the Boeing South Carolina facility where the energy-efficient 787 Dreamliner is built. Watch as many diverse teams come together to create an airplane that lives up to Boeing’s principles of safety, quality, and integrity. After watching the virtual tour, download the DreamLearners activity, to learn what it’s like to bring aircraft design to life with a fun paper airplane activity.
“Skills in STEM are critical in careers like aerospace engineering and advanced manufacturing”
Sign up for updates.
Travel news, reviews and intel for high-flyers
Sign up for our weekly newsletter
Go behind the scenes at boeing: factory tours are back.
Boeing's Everett factory, renowned as the largest building in the world by volume, once again opened its doors to the public on October 5
by Enrique Perrella
November 1, 2023
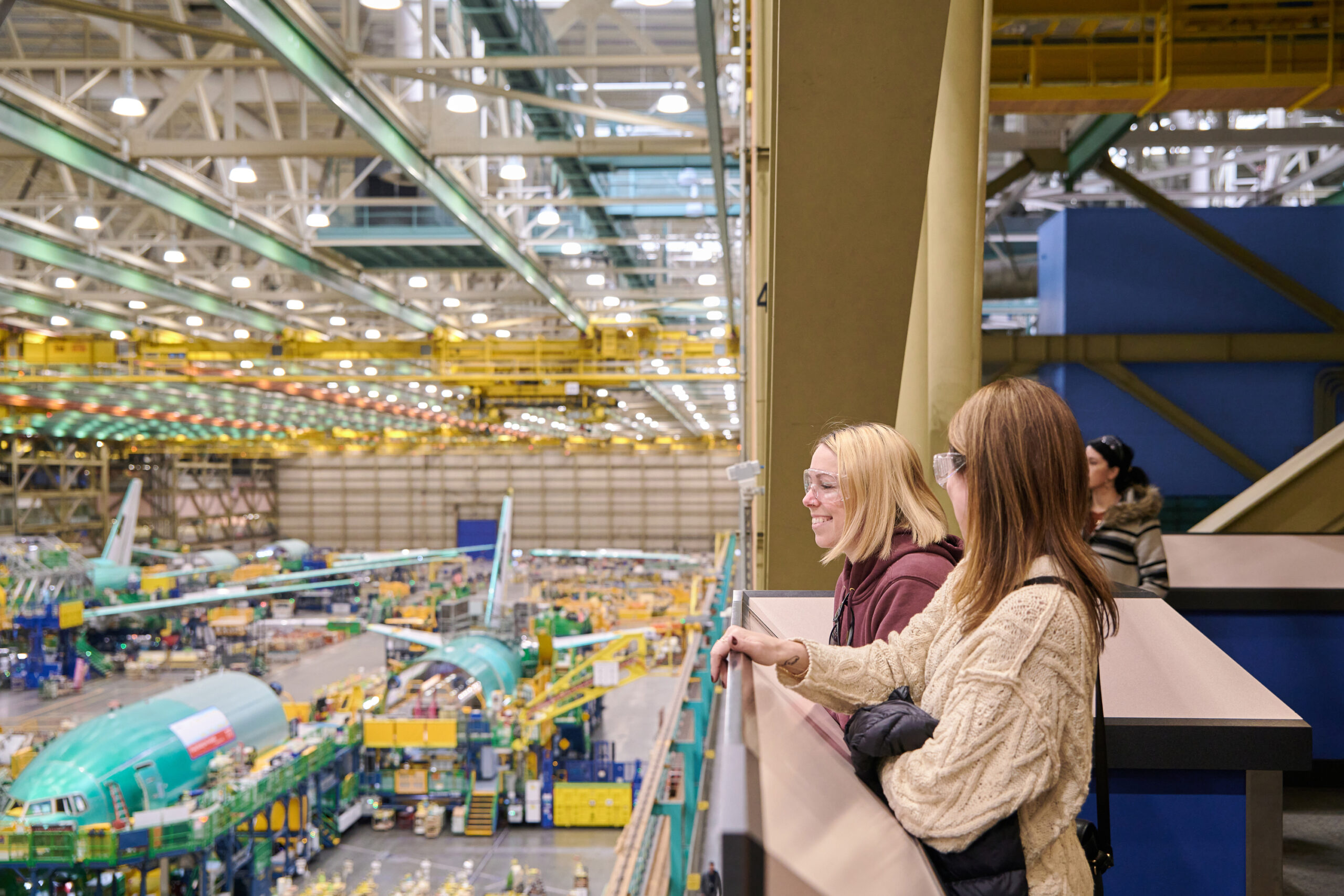
Photo: Courtesy of Boeing Commercial Airplanes
After a lengthy hiatus due to the COVID-19 pandemic, the Boeing Factory Tours are back, offering aviation enthusiasts and curious minds a chance to witness the magic of aircraft production.
For years, the Boeing Factory Tour has been a sought-after experience, attracting more than six million visitors from around the globe since its inception in 1968. The tour provides a glimpse into the fascinating world of aviation, with a behind-the-scenes look at the assembly line of iconic Boeing aircraft, which included the 747, 767, 777, and 787 Dreamliner.
Christi Medlyn, Boeing Future of Flight general manager, shared the excitement surrounding the reopening with Business Traveler USA .
“We’ve been closed for the tour portion of the experience for three and a half years. In the meantime, we invested in this space to give people a great brand experience for Boeing. It’s not just about airplane manufacturing; it’s about the full enterprise,” she explained.
A Renewed Factory Tour
Boeing’s Future of Flight location has undergone a transformation over the past few years to complement the factory tour. It now offers an immersive experience that covers various aspects of Boeing’s operations, including sustainable fuels, autonomous flight, and satellite technology.
In addition, hands-on activities and STEM learning opportunities have been introduced, allowing visitors to engage with drones and robots.
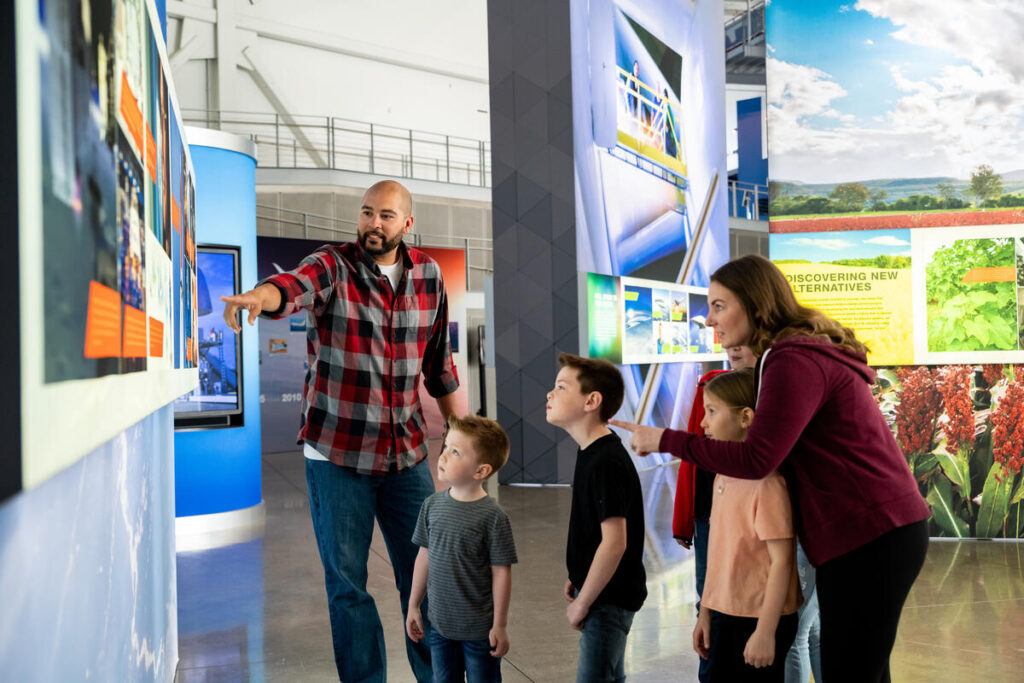
Visitors will notice several enhancements to the Boeing Factory Tour experience. The new route through the factory offers a unique perspective, taking guests from the Boeing Future of Flight Museum to the massive Everett factory, where tens of thousands of employees support airplane production.
The tour also includes access to the site’s underground system of factory tunnels and an observation balcony providing an exclusive, sweeping view of the current 777 assembly line where Boeing’s future flagship, the 777X, will also be manufactured. Lufthansa and Emirates are the first two airlines expecting to take delivery of the new variant of the Triple Seven.

Photo: Boeing 777X. Courtesy of Boeing Commercial Airplanes
Furthermore, visitors are treated to a comfortable bus tour that takes them through various sections of the airport tarmac. The journey starts from the area where new planes are fueled for the first time and continues to where Boeing 737 fuselages arrive on train wagons from Wichita, Kansas.
Sometimes, brand-new Boeing 777s without engines can be spotted, and other rare planes like Boeing 767 military tankers can be seen as they are prepared for delivery. During every portion of the tour, a knowledgeable guide provides detailed explanations of every aspect and responds to any questions from curious visitors.
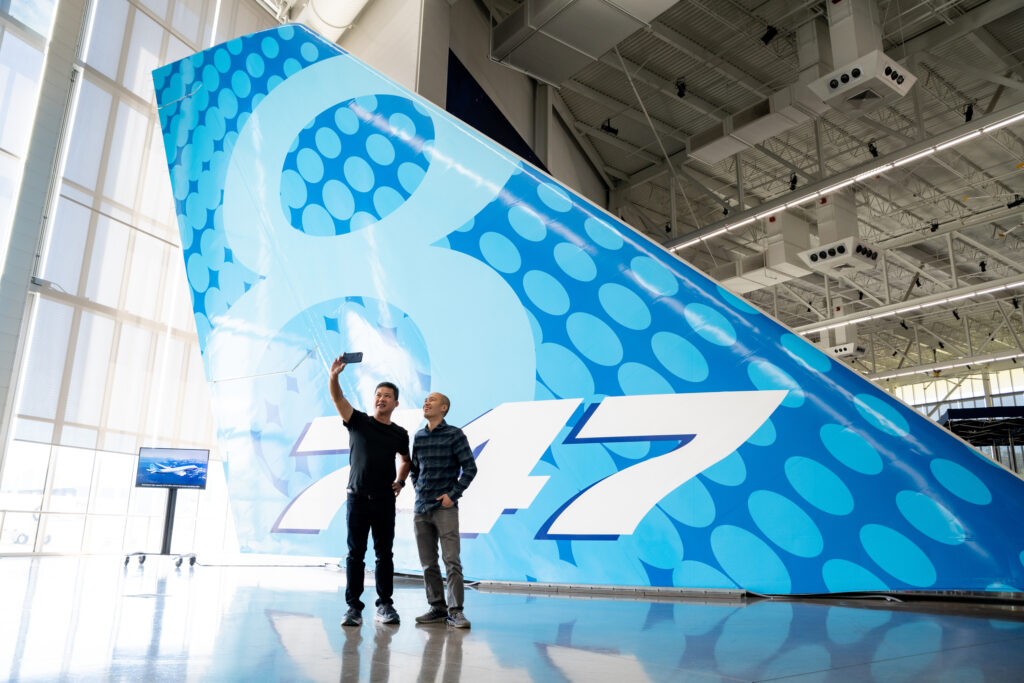
However, the tour isn’t the only attraction. Boeing Future of Flight features the Boeing Gallery, showcasing nearly 150 past, current, and future Boeing products and services, including the intriguing Passenger Air Vehicle (PAV) or personal flying car.
The Above and Beyond exhibit offers immersive simulations, and visitors can snap selfies with the Destiny Module from the International Space Station.
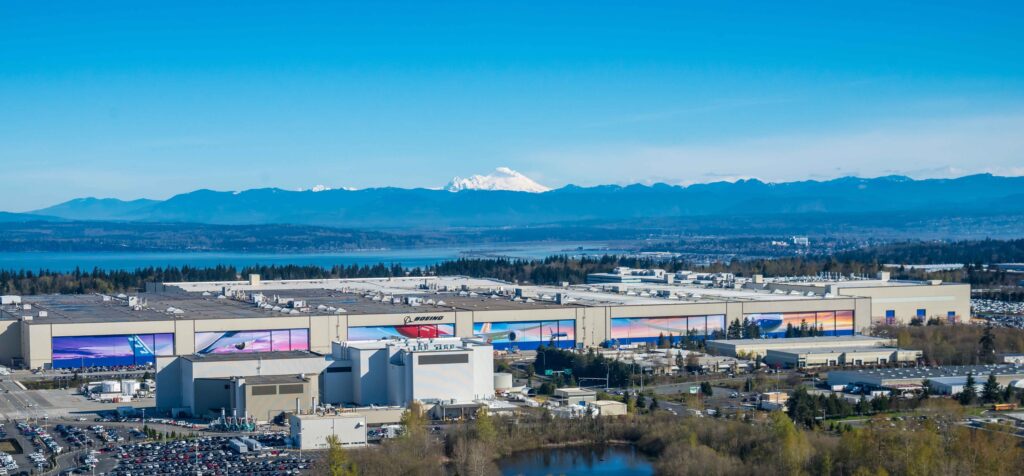
The open-air Sky Deck provides breathtaking views of Paine Field, the factory, and the enchanting North Cascade Mountains in the distance. It’s not unusual to spot brand-new planes parked on the deck, preparing for their journey into the skies.
And for those looking to take home a piece of aviation memorabilia, the Boeing store offers a wide range of souvenirs, from sweatshirts to scale model jets, coffee mugs, and vintage Boeing pilot jackets for kids and adults.
Overwhelming Response
The reopening of the Boeing Factory Tours has been met with overwhelming demand. Visitors have expressed their excitement and appreciation for the improved experience.
“It has been overwhelmingly positive, as we have been sold out every day. The pent-up demand and excitement around our product has been contagious. We are pleased with the positive visitor reviews received so far,” Christi Medlyn said.
“We’ve invested in every aspect of the experience, from the script to the exhibit content. We’ve added new elements and updated the storytelling.”
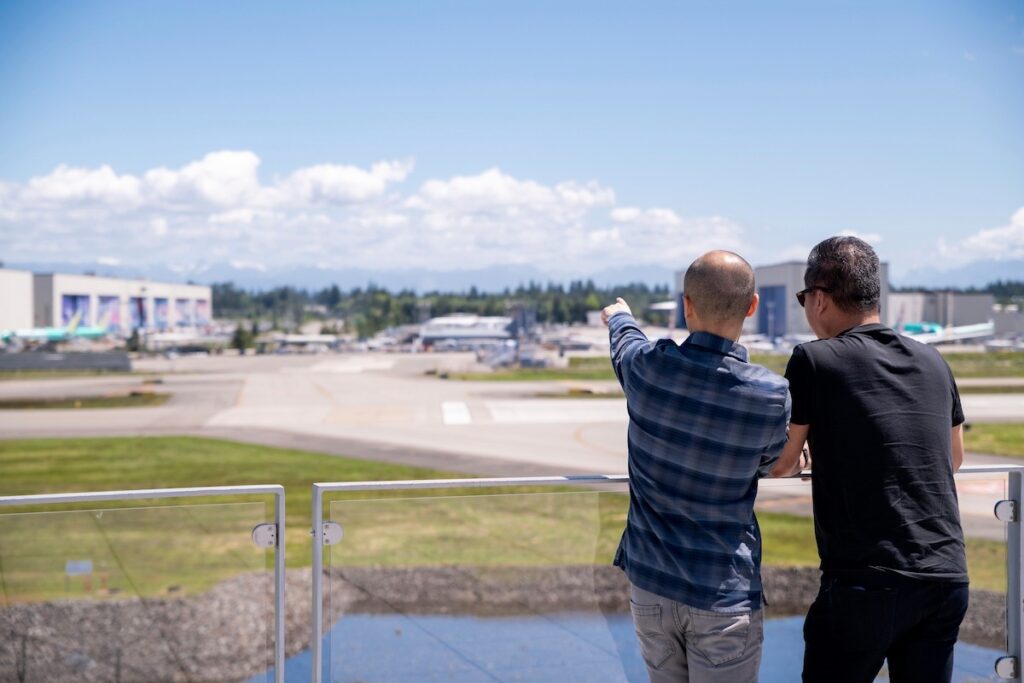
“Even though the experience is a bit different from the last time, we have made significant investments in every aspect. You will see the difference even while walking down the booth hallways,” Medlyn added.
Focus on the Boeing 777
While the tour has shifted its focus from the 747 to the 777 experience, it continues to captivate visitors, old and new, with its rich history and innovations in the world of aviation.
With the entire assembly line for the 787 Dreamliner now operational at Boeing’s South Carolina plant, the facility at Paine Field is exclusively dedicated to the Triple Seven family of planes. This includes the present 777 Freighter, along with the new 777X, along with the occasional 767 Freighter.
“After the 747 and the 787 were no longer being manufactured in Paine Field, we had to alter our route,” Medlyn explained. “As a result, we are now focusing on improving the 777 experience while incorporating new elements that highlight the entire family of Boeing Commercial Airplanes. We aim to discuss sustainability and introduce fresh perspectives to our storytelling.”
“So, we looked at everything from the script to the exhibit content. We added a little bit of Boeing history that you’ll see in the theater experience through a video at the beginning of the tour.”
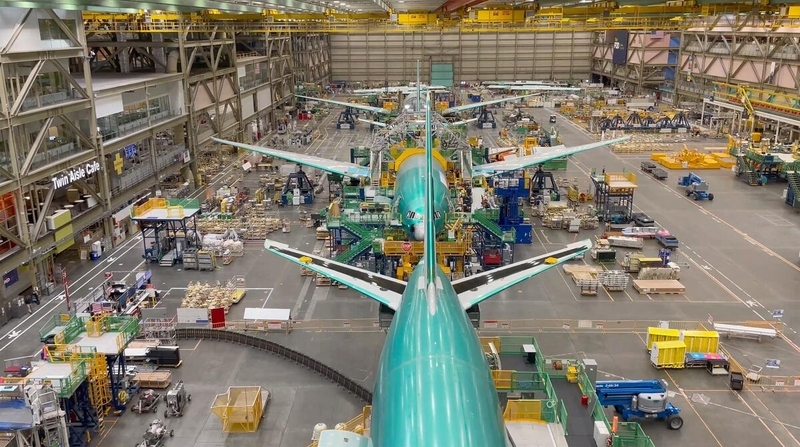
Whether you’re a seasoned aviation enthusiast or just curious about the marvels of flight, the Boeing Factory Tours are ready to deliver an unforgettable experience you’ll be eager to share with your friends for months to come.
So, mark your calendars, aviation fans, because this is a rare opportunity to step inside the world of Boeing, where dreams of flight become reality. The Everett factory, Boeing’s crown jewel, is ready to inspire and educate once again.
Most Popular
Related stories.
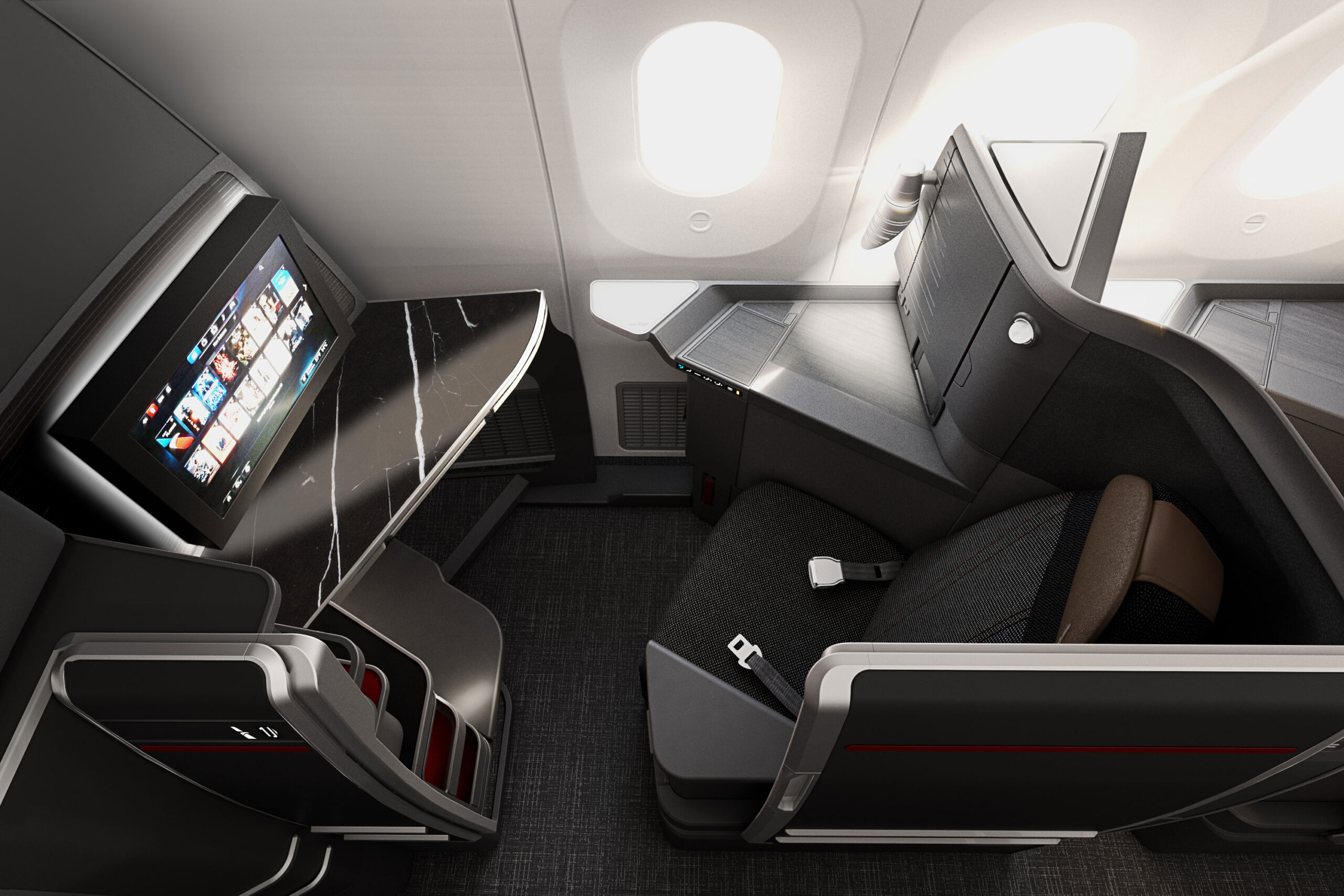
American Airlines Launches New Amenity Kits, Bedding, Flagship Suite
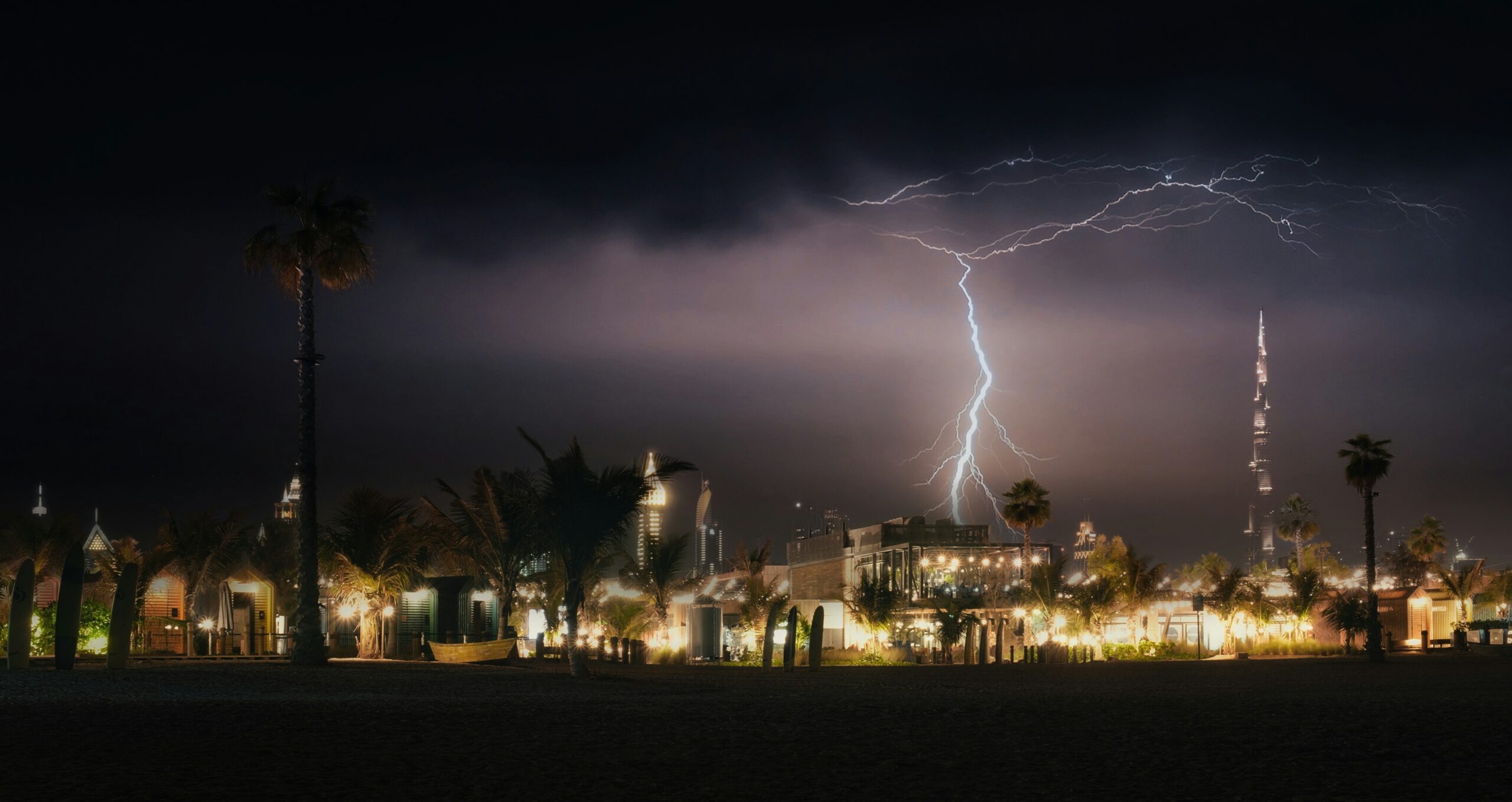
Emirates President Apologizes for Flight Disruptions Amidst Historic UAE Storms

Alaska Airlines Named the Best Airline in the Country by WalletHub
Privacy overview.
- Shop Back Issues
- Aircraft For Sale
- Destinations
- Learn To Fly
Flying Brands
- The Ultimate FLYING Giveaway
- I.L.A.F.F.T. Podcast
- Modern Flying
- Helicopters
- The New Owner
- Avionics and Apps
- Instrument/accessories
- Retrofit avionics
- Oem avionics
- Portable/handhelds
- Aviation Gear
- Pilot supplies
- Aviation apps
- Flight School Guide
- Learn to Fly
- NIFA/SAFECON
- What A CFI Wants You To Know
- Flight planning
- I.L.A.F.F.T.
Boeing Factory Tours to Resume
Washington state’s top attraction will be available to the public for the first time since 2020..

January, 2015: Boeing employees continue work building a Boeing 787 jets at its Everett factory. [Credit: Shutterstock]
The Boeing factory tour, part of the company’s Future of Flight experience in Mukilteo, Washington, will soon be back. The tour, put on hold in March 2020 during the COVID-19 pandemic, is set to resume next week. The tours give the visitors a look at Boeing from the inside out.
“Our Boeing tour guides are brand ambassadors and are a diverse group of employees who are knowledgeable and passionate,” said Norman Mah, Boeing spokesperson. “The guides provide the public an inside look at the airplane assembly process with opportunities to learn about The Boeing Company’s deep roots in the Puget Sound area.”
The tour begins at the Boeing Future of Flight Aviation Center with a short video on the history of the aircraft manufacturing giant and a safety briefing. Because it is a working factory, there are rules, such as no photography, including phones.
Visitors are bused to the factory and allowed to access a balcony that provides a bird’s-eye view of the famous assembly facility that has produced some of the most iconic aircraft in history, such as the Boeing 777, 787 Dreamliner, 767, and the 747 that revolutionized commercial air travel.
This is not the same tour that was done pre-pandemic, says Mah noting “The company has made enhancements including an updated route and accompanying visual components throughout the experience.”
The tour takes approximately 80 minutes and includes a bus tour of the Boeing campus. Mah recommends buying tickets early, as the tours often sell out weeks in advance.
The factory building itself is a modern marvel, owning the record for largest building in the world by volume at 98 million cubic feet. The structure spans some 98.3 acres.
The tours begin Thursday, October 5. It is recommended that tickets be purchased in advance as they are the No. 1 tourist attraction in Washington, drawing some 300,000 annually.
“We are thrilled to reopen our factory tour experience to pilots and enthusiasts who want to see how Boeing airplanes are assembled and learn about the company’s role as a global leader in aviation,” Mah said.
Ticket prices vary, and there are discounts for Boeing employees and seniors over 65 with valid ID.

More From Aircraft
This 1970 piper pa-28-140 cherokee cruiser is a period-perfect ‘aircraftforsale’ top pick, navigating the aircraft ownership learning curve through type clubs, forum stresses more work needed to meet ga unleaded fuel goals, this 2023 cirrus sf50 g2+ vision jet is a fully integrated ‘aircraftforsale’ top pick, aviation groups push back on proposal targeting new york helicopter operations, this 1980 piper pa-23-250 aztec f is a short-field, load-carrying ‘aircraftforsale’ top pick, new to flying, already have an account.
Photo tour: Behind the scenes at Boeing's 787 factory in South Carolina
NORTH CHARLESTON, S.C. -- It’s been a busy month for Boeing’s Dreamliner assembly line here.
Boeing’s newest and biggest variant of its 787 Dreamliner widebody aircraft -- the 787-10 -- rolled out of the South Carolina facility on Feb. 17 , with President Trump on hand for the festivities.
Just two days prior, production workers at the North Charleston facility voted against unionizing . The result was seen as a victory for Boeing, which campaigned against the effort.
Boeing’s South Carolina facility also remained in the aviation industry news last week as Korean Air took delivery of its first-ever Dreamliner here amid a splashy handover ceremony .
The recent run of events has helped turn a spotlight on Boeing's North Charleston assembly line.
Boeing broke ground there in 2009 and commenced operations in 2011. Today, the jetmaker’s South Carolina facilities include more than 4 million square feet of space spread across nearly 900 acres. That’s up from about 900,000 square feet on only 240 acres at the time of the groundbreaking.
“We are very excited about our site,” says Darrel Larson, Director of Operations - 787 Aft Body, at Boeing’s North Charleston operation.
Korean Air shows off new Boeing Dreamliner in South Carolina
Boeing’s North Charleston factory is capable of producing all three variants of the Dreamliner – the 787-8, 787-9 and 787-10 – though Larson says “we’re going to focus on -9s and -10s here in South Carolina.”
For now, the plant will continue to churn out Dreamliners, though Larson suggested Boeing’s holdings in the region give the company flexibility for future needs.
“We have a lot of land here to do whatever the company needs to do,” he said while speaking to reporters here last Tuesday (Feb. 21).
Curious to see it for yourself?
So far, tours of the South Carolina facility are not open to the public. But Today in the Sky was on hand earlier this month for a behind-the-scenes tour with other outlets. You can tag along virtually by checking out the photo gallery at the top. Or, check out our other embedded galleries to see photos from other recent events there.
TWITTER : You can follow Today in the Sky editor Ben Mutzabaugh at twitter.com/TodayInTheSky
ARCHIVES : Boeing adding paint facility in South Carolina, acquires land | S.C. Boeing expansion to continue apace in 2014 | Aerospace is South Carolina’s stealthiest industry | Is the Lowcountry poised to rival the Upstate in manufacturing?
Trump on hand as Boeing unveils newest, biggest Dreamliner yet
The world's 20 longest Dreamliner routes
AIR & SPACE MAGAZINE
Inside boeing’s 787 factory.
The Dreamliner’s quiet revolution
Stephen Joiner
/https://tf-cmsv2-smithsonianmag-media.s3.amazonaws.com/filer/Quiet-Revolution-airframe-FLASH.jpg)
I’ve been warned. “The cool factor in here is pretty awesome,” says Kim Westenskow, Boeing’s 787 factory superintendent, Position 4, as she escorts me to the assembly line in the company’s Everett, Washington plant. But that’s not the first thing that strikes you about this voluminous workspace, 380 feet wide and 10 football fields long. It’s the absence of industrial racket. The Dreamliner’s molded composite constituents are bolted together, and the holes are bored to the whir of air-driven, fluid-cooled, diamond-tipped drills. The aluminum 747 a few doors down requires drilling more than a million holes in metal, a process accompanied by ear-splitting fusillades of rivet guns and hammers. “They’re the other guys,” Westenskow explains. “The loud ones. We’re the quiet bunch.”
Between Position 0 and Position 4 on the line, disjointed wings and fuselage segments from around the world merge into a glossy white wide-body ready for the paint hangar and some major airline’s corporate livery. Westenskow enumerates the segments while extemporizing an atlas of global outsourcing: “Forward portion’s from Spirit Aerosystems in Wichita. Vertical fin’s from Boeing fabrication division in Tacoma. Tail cone’s from Japan, the horizontal stabilizer and fuselage segments are from Alenia in Italy.” The precision specs involved in 787 assembly impose upon Boeing’s worldwide partners a conformity undreamt of by the United Nations. With a passing glance, it’s impossible to distinguish 787 composite components cured in an enormous autoclave in southern Italy from those produced in the American heartland or at a Japanese aerospace giant.
Under the scrutiny of quality control engineers at Boeing, however, the contrasts have sometimes been stark. Alenia Aeronautica improperly torqued shims used to fill gaps in the airplane’s horizontal stabilizer. The errors threatened the component’s structural integrity, briefly halting 787 test flights in 2010. The year before, Boeing discovered that the skin of Alenia’s composite fuselage segments had wrinkles caused by internal stringers that were out-of-spec, necessitating patches to existing segments and design reworks for future production. While outside analysts report that Boeing is satisfied with Alenia’s improved performance over the past year, particularly the fuselage segments made in Grottaglie, the company maintains tentative plans to shift initial primary production of the stabilizer for the 787-9 variant back to Seattle.
From 2008, when he became 787 program manager at Boeing’s Everett, Washington factory, to February, when he handed off the job to Larry Loftis, all of those problems and more landed on the desk of Scott Fancher. By the time Fancher took over the project, the 787 was mid-season in an industrial soap opera. Fancher had spent his previous three decades with the company in its military divisions, working on staples including the F/A-18 Hornet and exotica like the airborne laser program. “It was a bit unusual for them to bring someone from the military business over to commercial,” he acknowledges, “so clearly I expected this was going to be a challenge.”
“Challenge” is one word for what confronted him. Overweight, over-budget, and overdue are others, with footnotes for striking unions, stressed-out customer airlines, and structural cracks. The 787 is in many ways a clean-slate departure from Boeing’s aluminum airliner fleet; its composite structure, intended to lower operating costs by reducing weight and therefore fuel usage, and features emphasizing passenger comfort, inherited from the Sonic Cruiser concept of the 1990s, had never before been built. The innovations turned the project into a saga of technical tribulation and continual organizational gut-checking. Now that the official EIS (entry into service) is history, expect some of that drama, and the thousands of aviation blog posts it spawned, to begin a slow fade. Though Fancher laughs when he remarks that most development projects in aviation “seem a lot easier after some time has passed,” he’s right. Few today remember the problems the now-sainted 747 faced: Engine faults necessitated grounding the first 20 production models for months, and recalling the airplane delivered to launch customer Pan Am.
At the assembly line’s present rate, 3.5 Dreamliners roll out each month. By contrast, in the same time span, Boeing produces 1.5 747s. By the end of next year, with additional production boosts, the planned addition of a “surge line” in Everett and production from Boeing’s Charleston, South Carolina assembly facility, every month 10 back-ordered Dreamliners will wing into the waiting arms of an airline. Only the 737 is produced in larger volume (currently 35 rollouts monthly).
In this economy’s low light, it looks like glimmers of job creation. But Boeing is cautious about projecting the 787’s employment potential. For one thing, as its novel construction process is tweaked, existing workers get more efficient. “As we improve at assembling this airplane,” Westenskow says, “we’ll actually need less people to build each one, not more.”
At Position 0, newly arrived composite components pause for 24 hours so their temperatures will stabilize. Tolerances for assembly are so tight that even minute variations—slight contraction caused by exposure to cold on the flight from a manufacturing center to here—can affect the process. At Position 1, the big pieces come together, Westenskow says: “All five at once: two wings and three fuselage segments.” The FBJ (Final Body Join) tool, a multi-tentacle jig, cradles the constituents and uses indoor GPS and laser measurement devices to mate them with automated accuracy. Position 2 finishes the electrical connections among the segments and installs the floors. Position 3 fits the interiors. Position 4 tests all functions.
The strikingly svelte 787 wing, displayed overhead in the jig that mates it to the fuselage, looks like a gallery exhibit. Westenskow points, tracing the aesthetically pleasing curve. Produced by Mitsubishi Heavy Industries in Japan, its carbon-fiber–aluminum hybrid structure is as mean as it is lean. Exactly how thin the wing is, Boeing won’t say. But Everett workers chosen to squeeze up into it must pass a physical qualifications test “which includes a very small hole,” Westenskow says. With line speed-ups looming, the wing join process is the key to making delivery commitments. If things slow down here, everything else stops.
It has happened before. Unlike aluminum airplanes with substantial spars spanning the connection between wing and fuselage, or wing join, the Dreamliner’s mostly composite wings bolt directly to the fuselage in a complex connection called the “side-of-body join.” Two years ago, stress tests revealed cracks in the center wing box (where each wing joins the airplane’s body inside the fuselage), bringing the vast project to a standstill for months. A time-consuming redesign to the fittings that support the connection at stringer (stiffening rods on each wing’s upper skin) attachment points was proved through exhaustive testing. Westenskow calls the team now implementing the modification at Position 1 “the best mechanics in the program.” That would be Erwin Arlantico and crew. They bear the sobering responsibility of attaching 787 wings.
Hard-wired for intensity appropriate to his job description, Arlantico rapid-fires remarks over one shoulder as I hustle to keep up with him. “A bad day on this project is any bad hole,” he says, pointing out the drill jigs clamped to the fuselage where the titanium wing fittings bolt. In constructing aluminum airliners, most holes Boeing made in a single shot. “But carbon fiber is a very different beast,” Arlantico says. Drilling each hole for the more than 500 fasteners that attach the wings is a three-step process, beginning with a small index hole and culminating in a final bore to excruciatingly tight specs. The relationship between the fuselage hole to the bolt hole in the wing mount fitting is non-negotiable: “Even 1/5,000th of an inch of misalignment,” Arlantico says, “and you won’t be able to fit the bolt in.” The carbon fiber structure is unforgiving of the slightest inelegance with high-speed, diamond-tipped drills. A minute elongation of the hole can sear the fiber, instigating de-lamination in the 150-layer, molded composite sandwich. Don’t bother asking what if. “We’d have to patch every single layer,” Arlantico says stoically.
Any number of interested parties monitors Arlantico’s crew as they go about this exacting and critical procedure. “Our customers are welcome to their airplane at any time,” Westenskow explains. With offices just steps from the Everett line, representatives of airlines with Dreamliners in assembly often inspect this team’s work. “All Nippon Airways is the toughest customer we have,” Arlantico remarks. “Very picky, very meticulous.”
Takeo Kikuchi, ANA’s general manager of the U.S.A. Engineering Office at Boeing, admits to high standards. “We don’t like to place pressure on the Boeing workers,” he e-mails, “but I do believe our presence reminds the workers that the customer is aware and watching their work.” Kikuchi and his team closely track the construction process and apply ANA’s acceptance standards to “every inch of the airplane.” Kikuchi is obviously proud of his company’s status as the 787’s launch customer; ANA took delivery of the first Dreamliner last September. “We provided input and had a great opportunity to help make the 787 a better airplane for ANA,” Kikuchi says, “which in turn makes it a better airplane for other airlines as well.” Boeing and ANA generally agree on concepts of safety and reliability, but opinion sometimes diverges over other points—for example, special reinforcements, or “doublers,” installed as part of custom reworks to address manufacturing issues on a given airplane. Though such reworks are allowed by the certification process, ANA has balked. “We don’t like to take a new airplane with any custom-designed structure or doublers,” Kikuchi explains. “Those are tough days, when we have to have these discussions with Boeing, as this can have schedule impact.”
Kikuchi is thoughtful about his role as man-in-the-middle between a major airline in Japan and Boeing’s corporate culture. “To be frank, [it’s] a great challenge,” he says. “Located here within Boeing, I understand what is truly going on here. The ANA team in Japan does not and often finds other things difficult to understand.” Kikuchi strives to make sure each party gets what the other is thinking.
As a Dreamliner progresses through the line at Everett, hundreds of people lay hands on it. But this workforce doesn’t look like the one you might encounter at final assembly of the aluminum airliners known as Boeing’s heritage fleet. On the 787 line, a conspicuously next-gen ambiance prevails: “Very, very young,” Westenskow says of her workers. “Very adaptive, very computer-literate, very able to communicate with engineering.” She laughs and adds, “Most of them couldn’t buck a rivet because most have never built airplanes that way.”
Scott Fancher, program manager at the Everett plant at the time of my visit, is proud of keeping attrition on the 787 relatively low compared with other programs’ staffing losses. “First of all, we can’t burn people out. We have to make sure they have healthy and robust family lives in addition to their work lives,” he says. Fancher says his 787 team, all the way to the rank-and-file on the line, stay cool under fire, and he attributes this to nature as much as nurture. “Certainly, we looked toward the best of Boeing to come work on this program,” he says. “But a natural selection process occurred too.” The intense flame surrounding development environments like the 787 drives off particular psyches while attracting others. Fancher strongly believes people who thrive on the cutting edge instinctively migrate toward it. In the case of the 787, many of those turned out to be new hires from outside, mentored by more experienced workers.
Standing in the center fuselage segment surrounded by Gunnar Lofstedt and his crew of electricians, I get the feeling I don’t listen to the same bands they do. I also have an impression of events running in reverse. Instead of installing stuff, they’re busily removing intricate wiring bundles. Elements of the 787 construction are still in continual flux. Triggered by data collected in ongoing test flights and early revenue service with ANA, “change incorporation” involves everything from simple tweaks of cabin entertainment to wiring. From the electrochromic window dimmers to the fly-by-wire flight controls, almost everything on the 787 is electronic, so the slightest engineering afterthought dictates changes in wiring. But in the Dreamliner’s modular construction scheme, fuselage segments arrive from the manufacturer already pre-stuffed with 60 miles of it—installed days ago. In 787 time, that’s so last week.
“We do data, we do everything,” Lofstedt says. “A single harness might go to 10 different systems.” One fiber optic bundle extends from nose to tail, over the crown in the ceiling, then down under the floor. The bundles of color-coded spaghettini look crazy-making enough as they thread along the bare fuselage wall; imagine fully extricating a built-in wiring harness from an assembled wide-body. Isolate a few strands, incorporate the change, then weave the bundles back through a warren of conduits, access ducts, and ceiling voids to all the right connectors, without bending certain cables beyond specs. It’s the hard way, but Lofstedt and his crew proved it’s easier and faster to change the wiring by pulling the harness than do it with the harness installed. “We can pull an entire wiring bundle out of the plane in one day and put it back in in two or three,” he says.
But nothing stops to wait for them. As a 787 moves down the line, it accumulates other crews installing components even as Lofstedt’s 24 electricians incorporate changes. Which begins to sound confusing. “It starts to get very crowded very fast,” Lofstedt confirms. They’ve lingered in the airplane making revisions as late as Position 4, the final stop before rollout. To buy more time, they now begin incorporating changes way back at 0.
Examples of design modifications to the 787 include several initiated by ANA’s input, such as the addition of an automotive-style spray window washer. Unlike most Boeing airliners, 787 cockpit side windows don’t slide open to permit the flight crew to clean the windscreen; they have to rely on airport ground workers. “We shared that we fly into some airports where no ground equipment is available to gain access to clean the windows,” Takeo Kikuchi says. “Boeing reviewed our request, looked at the data we shared, and added the system.”
Four floors up, the staff of the 787 Production Integration Center (PIC) have a commanding view of the assembly line. But it pales compared with the total picture of the process they get from the 10-foot-high, 40-foot-long video wall before them. Raw data relating to the production of 787 components around the world merges in the room like a confluence of swift-running mountain streams. It’s displayed in larger-than-life fashion to 25 “focals”—each a point person for a specific duty—occupying computer terminals in the PIC, 24/7. “We get involved in everything you can imagine,” says Tox Popnoe, the center’s energetic manager. “Anything that affects the production or the schedule of the 787 program.”
Seventy percent of Dreamliner components are outsourced to manufacturers worldwide. Kinks in the supply chain, mostly resulting, Boeing admits, from insufficient oversight or stress testing of its myriad suppliers, have plagued the program from the start. From fasteners to flight guidance software, from Foggia, Italy, to Charleston, South Carolina, delivery delays or component quality-control failures have incited increasingly hardball measures from Boeing, up to and including buying the under-performing partner outright and upgrading operations to Boeing standards. To monitor the health of the chain, the integration center eyeballs production of the larger components on which day-to-day assembly of the Dreamliner relies, from manufacture to installation.
The Integrated Production Visibility (IPV) software figuratively perches on the shoulders of makers of fuselage segments, wings, and other major structures. “We track our Tier One partners: the Japanese, the Italians, and the domestic partners,” Popnoe says. The IPV window displays a real-time pictorial representation of each supplier’s factory flow, from the beginning of production to the time the component ships. “It’s an incredible dashboard,” Popnoe says. “We can tell where all the problem areas are, regardless of geographic location. We know how many jobs they have to complete and whether they have any issues.” Color-coded graphs divulge all at a glance: Green is “on-plan,” yellow is off-plan by one to two days, red is off-plan by two days or more.
“Issues” is a big word in here. Any major one with a supplier manifests as a colored icon on a racetrack display with a 48-hour finish line. “A major issue is defined as anything that affects a shipment coming to final assembly,” Popnoe says. “Someone can call here 24/7 and say ‘Hey, I’ve got this engineering issue in Japan and we need help to ship this section on time.’ That’s when the red light really goes on.” As the icon moves down the timeline, people in the room hand off the problem to shifts around the clock until it’s resolved—and sometimes that must be done in just hours to avoid line delays.
The production trail and present location of every 787 in process at Everett shows up on a “chicken tracks” display on the video wall. Digital maps update the current positions of all four Dreamlifters, the radically modified 747-400s that transport major assemblies of the 787. The big airplanes are in frequent transit and, as production ramps up, will fly almost constantly.
To the people monitoring the progress of 787 components, a major earthquake is just one more issue. Popnoe points out a screen displaying seismic data worldwide. If a quake strikes near a 787 production facility, Boeing knows immediately. The urgency is not limited to potential shipment interruptions. Delicately calibrated equipment at sites producing the composite wing and other components is not exactly temblor-friendly. “Our quality requirement states that if a facility has calibrated tooling on the program and there’s a 5.0 quake within a 50-mile radius, we have to go in and verify the tooling is still properly calibrated,” Popnoe explains. Otherwise, misalignment could occur in fuselage segments or wing-to-body joins. With 35 percent of the 787 produced in quake-prone Japan, that’s a real concern, particularly after the March 2011 Tohoku earthquake and tsunami. (After the earthquake, production equipment was recalibrated at Mitsubishi Heavy Industries.) Hurricanes are also tracked here, and a news window keeps the integration center apprised of political uprisings or labor strikes around the world that might affect 787 final assembly in Everett or South Carolina.
Production data in the PIC pipeline flows both ways at Boeing. “People downstream know what work is coming at them,” Popnoe says. “And we assimilate it up to our leaders, who make the educated decisions about how to keep the project on track and on schedule.”
The first Dreamliner is carrying ticket-buying passengers. The airliner—which received the 2011 Robert J. Collier Trophy, awarded for the greatest achievement in aeronautics in America—is already sold out through 2019, and Boeing assembly lines are shifting into overdrive to turn them out at a rate outpacing any other wide-body in the industry. Today Fancher declares flatly, “We firmly believe the 787 represents the biggest sea change in commercial aviation since the introduction of the 707.” Feedback from the global traveling public is not yet in. But on a publicity tour flying various Japanese citizens’ groups to celebrate the first delivery to All Nippon Airways, Fancher got a sample of Japan’s take on its new airliner. Even in heavy weather, “thousands of people came out to see the 787 everywhere we went,” he says. During a stop at Yokohama, Fancher ducked into the terminal to grab a cup of coffee and was soon recognized by 787 fans. One woman approached excitedly with a little girl in tow, he recalls. Fancher marvels: “She said, ‘Please, can you take a picture with my daughter?’ This woman had driven three hours and stood out in a cold driving rain to see the 787.”
When I spoke to him in Everett, the program manager was still smiling over the airliner’s rock-star reception. But there was a production system to ramp up, 873 Dreamliners on back order to 60 customers around the world, and the next variant of the airplane in development already. As soon as delivery number one was in the hands of ANA, “we breathed a big sigh of relief,” Fancher reported. “For maybe three days. Then back to hard work.”
Frequent contributor Stephen Joiner writes about aviation from his home in southern California.
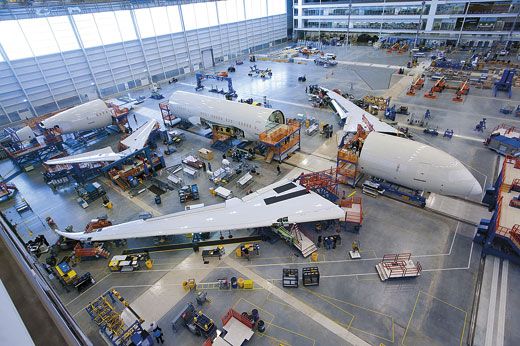
Get the latest stories in your inbox every weekday.
Boeing Factory Tour: 787 Dreamliner and 777 Worldliner
By david parker brown.
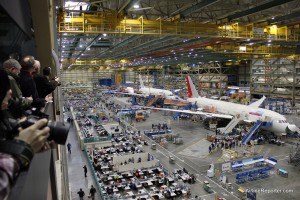
The Boeing 787 Dreamliner line inside the Boeing Factory. Here are 787s for Air India, JAL and China Southern.
During the Boeing 747-8 Intercontinental event, invited guests were allowed into factory to not only take a look at the Boeing 747-8I and 747-8F , but also the Boeing 777 Worldliner and Boeing 787 Dreamliner.
This is a huge treat, since Boeing normally doesn’t allow people to take photos inside the factory, but this time, cameras were allowed and I had a hard time cutting over 300 photos down to just 26.
I already posted photos being on the factory floor with the 747-8, but now it is time to share some photos of the 787 and 777. Unfortunately, we still weren’t allowed down on the factory floor with the 787, but we were able to get up close and personal with the 777 line.
VIEW ALL 26 PHOTOS OF THE 777 AND 787 LINES
David Parker Brown
EDITOR-IN-CHIEF & FOUNDER - SEATTLE, WA. David has written, consulted, and presented on multiple topics relating to airlines and travel since 2008. He has been quoted and written for a number of news organizations, including BBC, CNN, NBC News, Bloomberg, and others. He is passionate about sharing the complexities, the benefits, and the fun stuff of the airline business. Email me: [email protected]
Couldn’t get link to photos to work.
Pretty cool those cubicles of engineers and workers right there on the floor and not in some building a mile away. I bet every square inch of space has been planned out to maximize efficiency in that factory!
Weird, I just tried it and it seemed to work. Goes to Flickr: http://www.flickr.com/photos/airlinereporter/sets/72157626136516053/
But yes, it is amazing to see everyone in action. It is a well oil machine, that is for sure.
Oops. You were right. I could see them b/c they were all in private setting. Try again!
Really enjoyed the pictures, David. Thanks so much! They’re such beautiful machines to look at – I never get tired of it. Thanks also for the shots that show what it was like to be on the tour. Not as good as being there, but good enough to let us live vicariously through you!
you have the best job in the world!… lol
here I am, sat at work, ignoring my email and looking at your pictures!
Excellent photos. I wish I can see in person those 787 Dreamliner and 777 Worldliner
I wonder what would be the size of the sheds of which the factory is built. Truly amazing !
Leave a Reply Cancel Reply
Your email address will not be published. Required fields are marked *
- Share full article
Advertisement
Supported by
Boeing Defends Safety of 787 Dreamliner After Whistle-Blower’s Claims
After a Boeing engineer went public with safety concerns, the company invited reporters to its South Carolina factory and top engineers vouched for the plane.

By Mark Walker and Niraj Chokshi
Reporting from Boeing’s factory in North Charleston, S.C.
Boeing sought on Monday to reassure the public of the safety of its 787 Dreamliner plane days before a whistle-blower is scheduled to testify before Congress about his concerns regarding the jet’s structural integrity.
In a briefing for reporters at the factory in North Charleston, S.C., where the plane is assembled, two top Boeing engineers said the company had conducted exhaustive tests, inspections and analyses of the plane, both during its development and in recent years, and found no evidence that its body would fail prematurely.
The presentation came just under a week after The New York Times reported the allegations by the whistle-blower, Sam Salehpour, who works as a quality engineer at Boeing and is set to testify before a Senate panel on Wednesday. Mr. Salehpour said that sections of the fuselage of the Dreamliner, a wide-body plane that makes extensive use of composite materials, were not properly fastened together and that the plane could suffer structural failure over time as a result. The Federal Aviation Administration is investigating his allegations.
Mr. Salehpour’s claims instantly created another public-relations problem for Boeing, which has been facing intense scrutiny over its manufacturing practices after a panel came off a 737 Max during an Alaska Airlines flight in January.
Mr. Salehpour said that the gaps where sections of the Dreamliner’s fuselage were fastened together did not always meet Boeing’s specifications, something that he said could weaken the aircraft over time. The Boeing engineers disagreed with his assessment, without naming him. They said the plane had gone through extensive testing that showed that, in about 99 percent of cases, the gaps met the specifications. Even if the gaps exceeded the specifications by a reasonable amount, they would not affect the plane’s durability, the engineers added.
“Not only did we interrogate those airframes — we were taking out fasteners, we were looking for damage, we’re also doing the approval inspections to understand the build condition, and we didn’t find any fatigue issues in the composite structure,” said Steve Chisholm, a vice president and the functional chief engineer for mechanical and structural engineering at Boeing.
Mr. Chisholm said the company had put the Dreamliner through extensive tests that turned up no evidence of fatigue in the jet’s composite structure. A 787 airframe was subjected to testing that put it through 165,000 “flight cycles,” the equivalent pressurization and depressurization of as many flights. That figure far exceeded the plane’s expected life span and the airframe still showed no signs of fatigue, he said.
The 787 plane with the highest number of cycles belongs to a Japanese airline, All Nippon Airways, which received it in late 2012, according to Boeing. That aircraft has been through about 16,500 cycles, the company said.
In a statement on Monday, Debra S. Katz, a lawyer for Mr. Salehpour, urged caution about accepting Boeing’s assertions about the Dreamliner as fact.
“We cannot speak or respond to data that we haven’t seen, but Boeing has always said ‘just trust us’ when it comes to safety,” Ms. Katz said. “It’s clear that standard is no longer sufficient, and any data provided by Boeing should be validated by independent experts and the F.A.A. before it is taken at face value.”
Mr. Salehpour is scheduled to testify on Wednesday before the Senate Homeland Security and Governmental Affairs Committee’s investigations subcommittee. Separately that day, the Senate Commerce Committee is planning to hold a hearing with experts who were involved in producing a recent F.A.A. report that faulted Boeing’s safety culture .
Boeing began investigating problems with gaps in the Dreamliner about five years ago, eventually discovering that some between adjoining parts of the plane’s body did not meet its own specifications of being less than five-thousandths of an inch thick. That led the company to pause deliveries for about 18 months as it inspected its processes and planes, making changes where appropriate. That work involved removing thousands of fasteners from planes in its inventory and inspecting the size of the gap between the two materials each fastener held together.
The company said that about 1 percent of all gaps inspected failed to meet specifications. The company also said that research and testing over the past few years had found that the larger gaps posed no threat to the plane’s long-term durability.
The company noted that 671 Dreamliners had gone through thorough six-year maintenance checks, while eight had gone through 12-year checks, and it said that none of those checks found any signs of premature fatigue. Boeing said it did not believe that Dreamliners currently being flown by its customers were in need of any modification.
Mark Walker is an investigative reporter focused on transportation. He is based in Washington. More about Mark Walker
Niraj Chokshi writes about aviation, rail and other transportation industries. More about Niraj Chokshi
Boeing: A Company in Turmoil
A Whistle-Blower’s Claims: A Boeing engineer who went public with safety concerns about the company’s 787 Dreamliner told a Senate panel that he was concerned that shortcuts the company was taking would eventually lead to a crash if they continued unchecked.
Dish Soap to Help Build Planes?: An F.A.A. audit of the production of the 737 Max raised a peculiar question. Was it really appropriate for a major supplier to be using Dawn dish soap and a hotel key card as part of its manufacturing process?
‘Shortcuts Everywhere’: Quality issues have plagued Boeing even after two fatal crashes. Many employees blame the company’s focus on increasing production speed .
A Major Reshuffle : Boeing said that it was overhauling its leadership amid its most significant safety crisis in years, announcing sweeping changes that included the departure of its chief executive, Dave Calhoun , at the end of the year.
Alaska Airlines Flight 1282: After a section of a plane blew out 10 minutes after it took off , there was increased scrutiny on the plane’s manufacturer: Boeing . The Justice Department has since launched a criminal investigation .
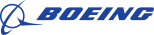
787 Quality Information
At a glance.
Boeing is fully confident in the 787 Dreamliner because of the comprehensive work done to ensure the quality and long-term safety of the aircraft. Claims about the structural integrity of the 787 are inaccurate.
The issues raised have been subject to rigorous engineering examination under U.S. Federal Aviation Administration oversight. This analysis has validated that the aircraft will maintain its durability and service life over several decades, and these issues do not present any safety concerns.
Boeing continues to monitor these issues under established regulatory protocols and encourages all employees to speak up when issues arise. Retaliation is strictly prohibited at Boeing.
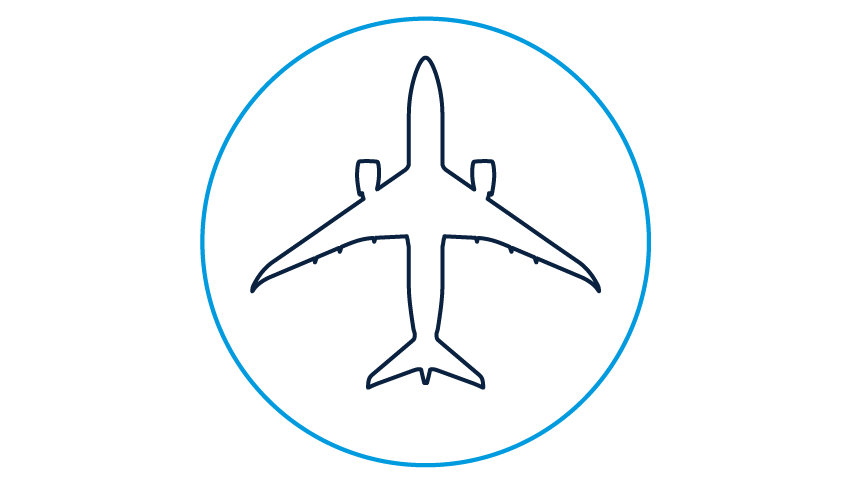
1,100 787s operating globally. In service, a 787 currently flies about 600 flight cycles per year on average and will operate safely for many decades before retirement
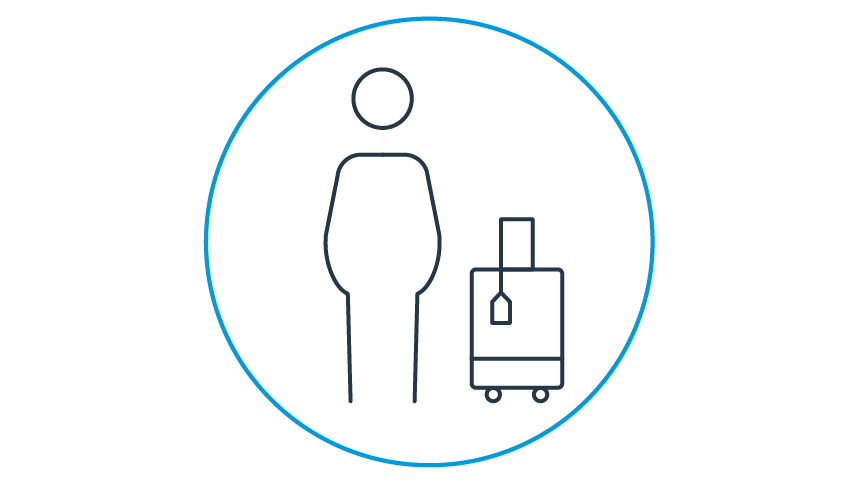
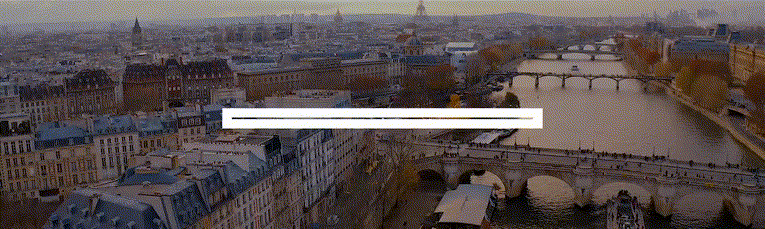
As of April 2024, the 787 Dreamliner family has safely transported more than 875 million passengers on more than 4.2 million revenue flights
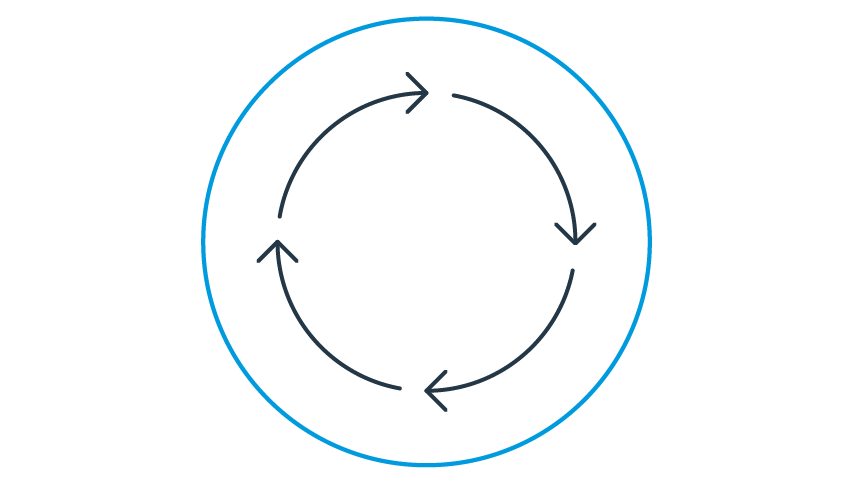
165,000 flight cycles of simulated in-service conditions during rigorous testing phases, 3.75 times the design service objective, with no findings of composite airframe fatigue
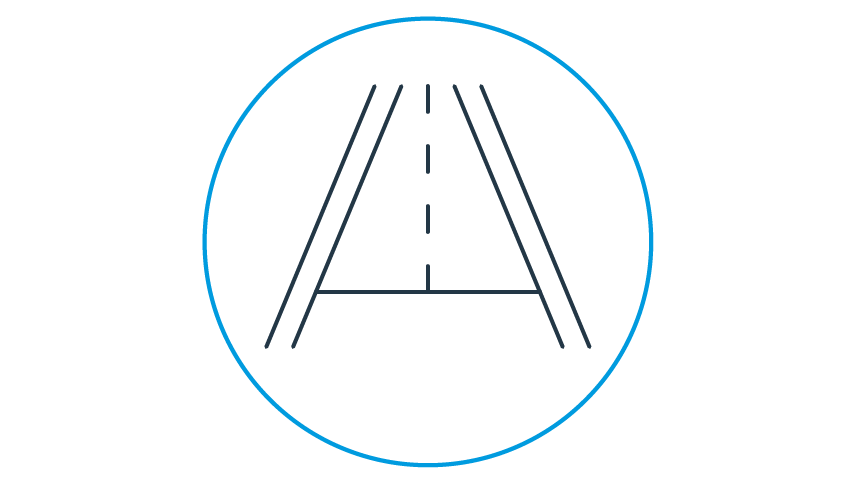
The highest-cycle 787 in service has accumulated about 16,500 flight cycles since 2012
787 dreamliner structural testing program.
The multiyear 787 full-scale test program, from August 2010 to September 2015, was more robust than any conducted on a previous Boeing commercial airplane. While the FAA and other regulatory authorities require the company to do this testing for certification, Boeing has its own more demanding standards for certain parameters. Testing is taken very seriously because it gives the company and its customers confidence for the life of the program. To confirm performance and life cycle of the composite 787 fuselage, Boeing tested a full-scale airplane and a forward fuselage section simulating up to 165,000 flight cycles, including pressurization , – about 3.75 times the jet’s design service objective– with no findings of composite airframe fatigue. The cycles of pressurization and depressurization are the contributors to fatigue on metal airplanes. In service, a 787 currently flies about 600 flight cycles per year on average and will operate safely for many decades before retirement. Supported by a 1.2 million-pound (544,000-kilogram) test rig, the airplane’s wings, fuselage and tail were attached to load fittings. Hydraulic jacks then applied loads to the airplane, which pushed and pulled the wings and fuselage to simulate all phases of flight and evaluated the durability of the airplane in a variety of conditions over lifetimes of service. During each second of testing, thousands of data points were collected to ensure all parts of the airplane performed as expected. With data analyzed during five years of fatigue testing, Boeing validated the robustness of the airplane and applied learnings to fine-tune maintenance recommendations for customers. Test results validated earlier modeling and associated expectations about the robustness of the 787 design and composite fuselage. Additionally, from September 2008 through March 2010, Boeing completed static tests of the airplane structure, where the airframe was first subjected to limit load , the highest loads any airplane would encounter in service. Next, during ultimate load testing, the airplane was subjected to 150% of the highest loads any airplane would encounter in service. The wings were flexed upward by about 25 feet (7.6 meters), and the fuselage was pressurized to 150% of its maximum operating condition. The full airplane full-scale static test and the full airplane full-scale fatigue test were performed in addition to many other static and fatigue tests, including major fuselage sections and outboard wing, as well as more than 100,000 smaller-scale tests.
Watch: 787 Fatigue Testing
Photos: 787 static and fatigue testing.
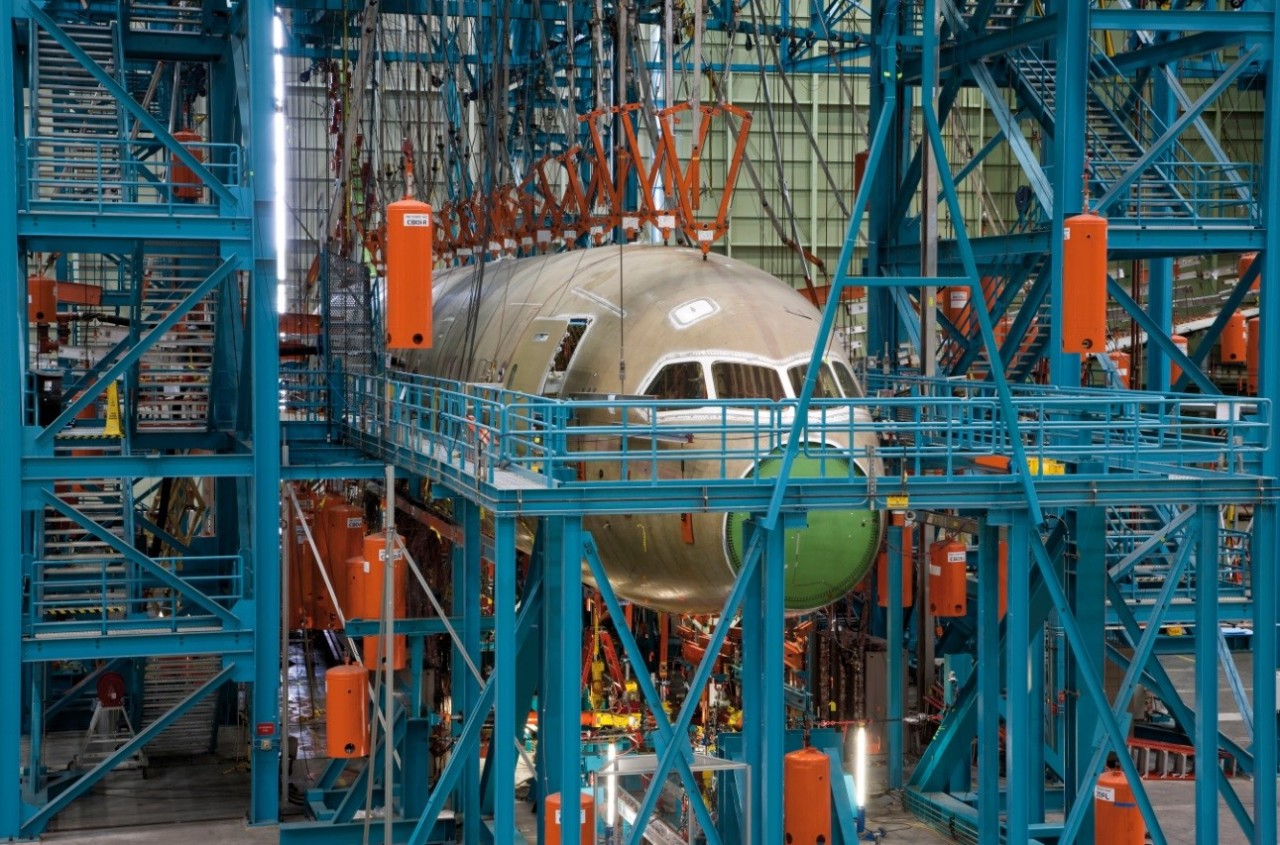
- Static image
- Fatigue image
787 manufacturing
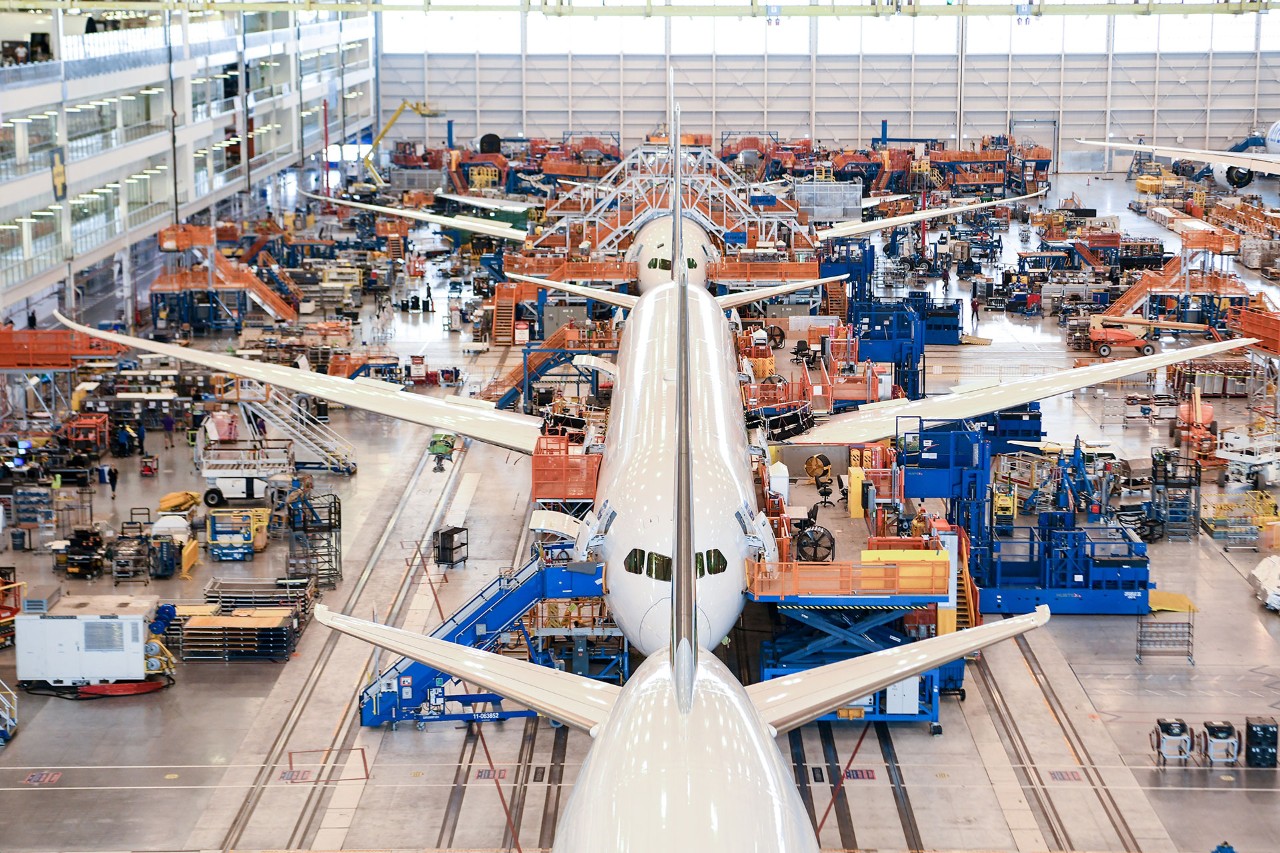
Based on the data analysis from this extensive fatigue testing, a 787 can safely operate for more than 30 years before it would need to enter more conservative maintenance routines for extended service. The full-service life could be as long as 40 to 50 years, depending on the operator and their maintenance plan. Since the 787 program launched 20 years ago, Boeing has worked to improve production processes and incorporate the latest manufacturing techniques. This continuous improvement has resulted in higher quality and has had no impact on durability or safe longevity of the airframe. The Boeing team’s work has included exhaustive testing and analysis to ensure that manufacturing process updates maintain the performance, full projected lifespan and strength of the airplane. There are thousands of different join-up points across the airplane. Boeing has detailed design specifications that define allowable gaps and fit-up force at any given join. Fit-up forces are the forces applied to parts to ensure they mate up properly prior to any shimming or assembly. This force can vary from join to join and location to location. The comprehensive approach used to evaluate improvements to our production process includes and encourages dissenting viewpoints. This work has been completed with full transparency and under the oversight of the FAA.
787 join verification
From October 2020 to August 2022, as a result of employees identifying potential issues on the 787, Boeing slowed production and stopped delivering 787s to ensure each airplane met its exacting engineering specifications. Boeing incorporated the join inspection and verification activity into the production system so that airplanes coming off of the production line meet these specifications. For the in-service fleet, based on comprehensive analysis no safety issues have been identified related to composite gap management and our engineers are completing exhaustive analysis to determine any long-term inspection and maintenance required, with oversight from the FAA. Based on the analysis and any future inspection, the 787 will maintain its strength, durability and service life.
787 testing timeline
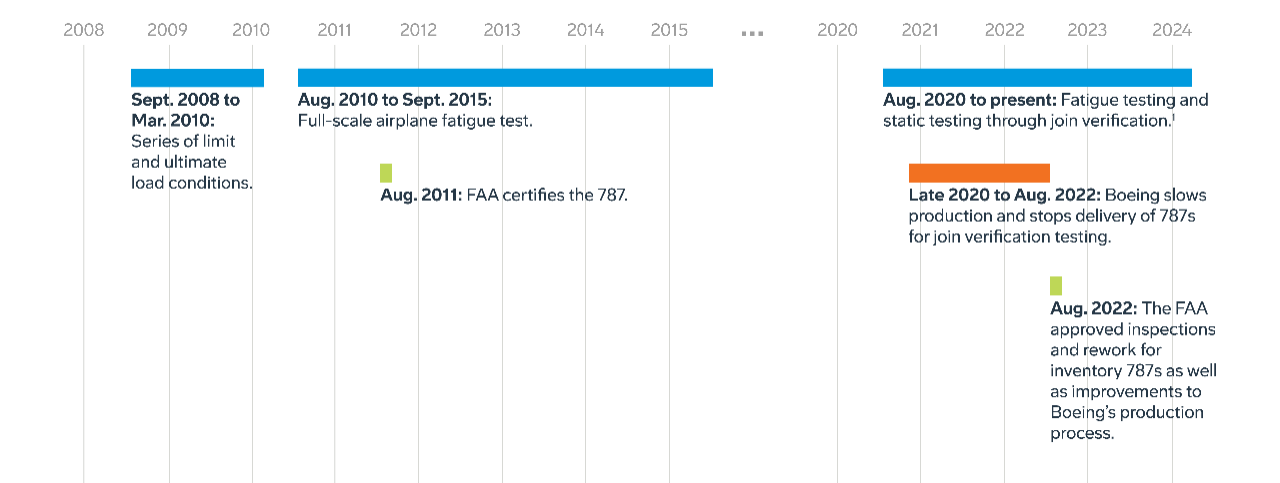
1 This included tests, strain gauge monitoring, and analysis of findings.
Flight cycle testing
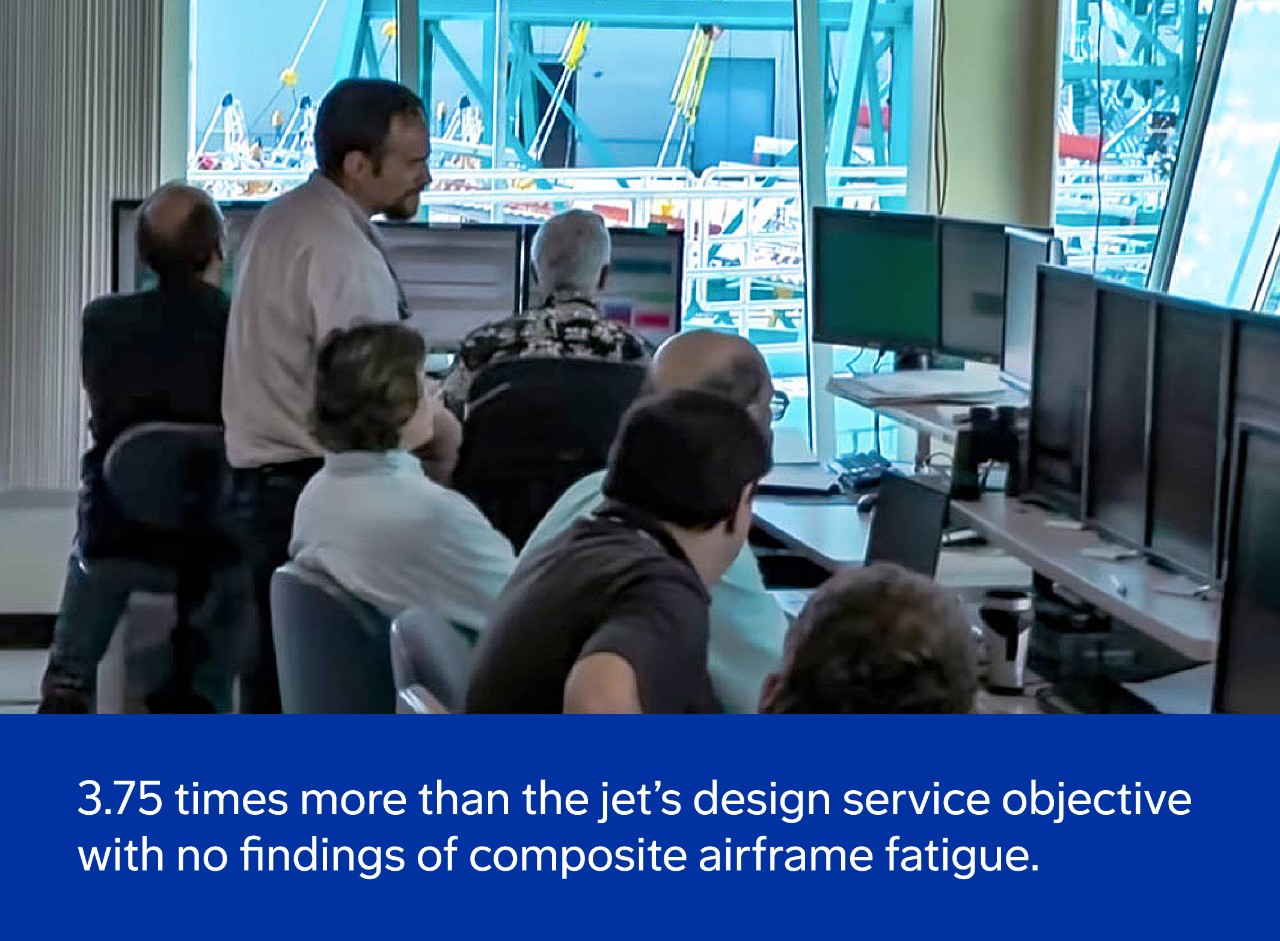
To confirm performance and life cycle of the composite 787 fuselage, Boeing tested a full-scale airplane and a forward fuselage section simulating up to 165,000 flight cycles, including pressurization , – about 3.75 times the jet’s design service objective– with no findings of composite airframe fatigue. The cycles of pressurization and depressurization are the contributors to fatigue on metal airplanes.
Phases of flight testing
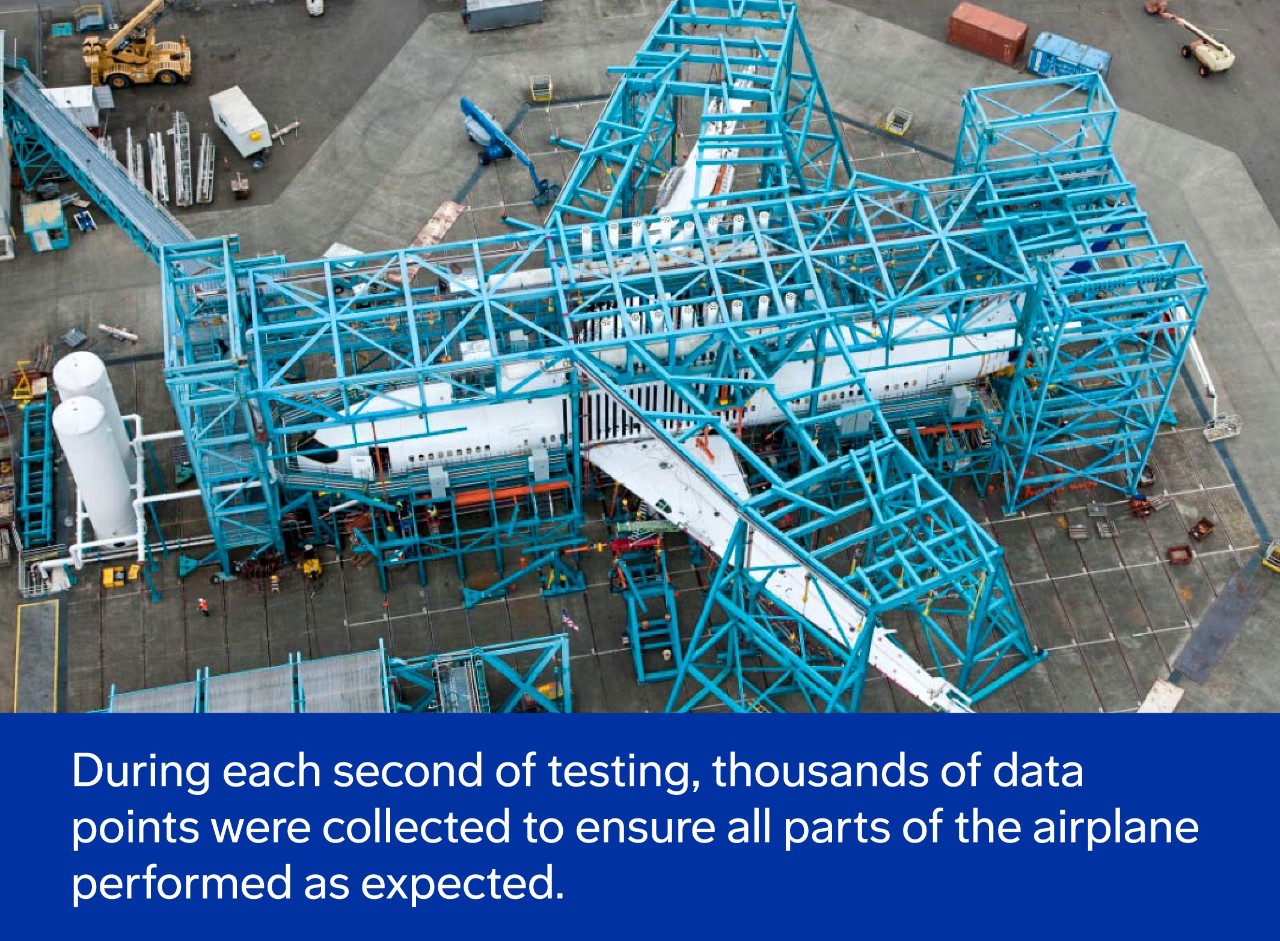
The multiyear 787 full-scale test program, from August 2010 to September 2015, was more robust than any conducted on a previous Boeing commercial airplane. Supported by a 1.2 million-pound (544,000-kilogram) test rig, the airplane’s wings, fuselage and tail were attached to load fittings. Hydraulic jacks then applied loads to the airplane, which pushed and pulled the wings and fuselage to simulate all phases of flight and evaluated the durability of the airplane in a variety of conditions over lifetimes of service. During each second of testing, thousands of data points were collected to ensure all parts of the airplane performed as expected.
Fostering transparency and openness
Safety and quality are core values at Boeing. We design and build all our airplanes to meet rigorous engineering specifications and FAA requirements, ensuring compliance with safety standards. We continuously propose improvements, supported by extensive data and testing, with oversight from the FAA for approval. Our culture fosters transparency, accountability and open communication, empowering employees to speak up through our confidential reporting channel, Speak Up. Reported concerns are thoroughly reviewed, and we take action while strictly prohibiting retaliation. We are committed to maintaining the highest levels of safety and quality through open dialogue and continuous improvement.
Media resources
Contact [email protected]
Photo and video resources 787 factory b-roll download
Media statements
Boeing statement on 787 claims.
“In 13 years of service, the global 787 fleet has safely transported more than 850 million passengers on more than 4.2 million flights. A 787 can safely operate for at least 30 years before needing expanded airframe maintenance routines. Extensive and rigorous testing of the fuselage and heavy maintenance checks of nearly 700 in-service airplanes to date have found zero evidence of airframe fatigue. Under FAA oversight, we have painstakingly inspected and reworked airplanes and improved production quality to meet exacting standards. We are fully confident in the safety and durability of the 787 Dreamliner.”
Boeing statement on 777 claims
“With three decades of innovation in design and production, the 777 fleet has safely flown more than 3.9 billion passengers around the world. We are fully confident in the safety of the 777, which remains the most successful widebody airplane family in aviation history.”
Boeing statement on 787 join verification
“From October 2020 to August 2022, as a result of employees identifying and sharing conformance items on the 787, we slowed production and stopped delivering nearly all 787s to take our time to get things right and ensure each met our exacting engineering specifications. We incorporated the join inspection and verification activity into our production system so that airplanes coming off of the production line meet these specifications. For the in-service fleet, comprehensive Boeing and FAA analysis determined there is no near-term safety of flight concern, and our engineers are completing exhaustive analysis to determine any long-term inspection and maintenance required, with oversight from the FAA. Based on the analysis and any future inspection, the 787 will maintain its strength, durability and service life.”
Boeing expects slower increase in 787 production rate and deliveries, memo says
- Medium Text
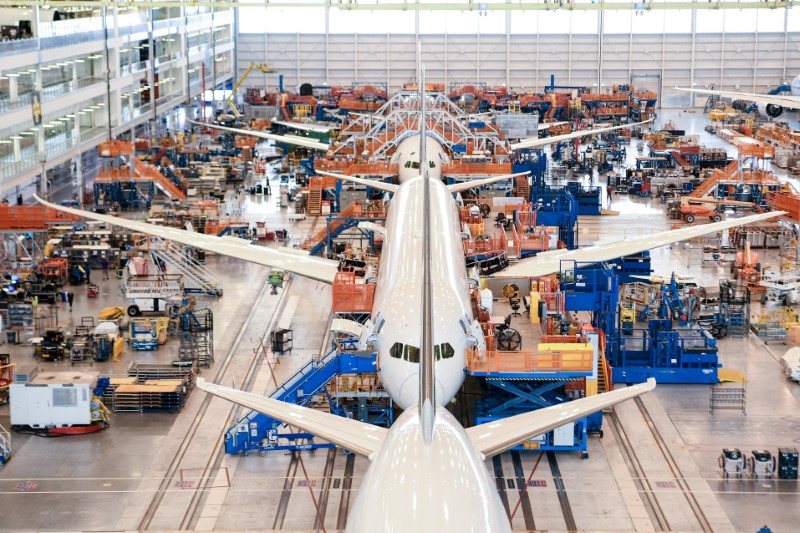
Sign up here.
Reporting By Allison Lampert in Montreal and David Shepardson in Washington; Editing by Jamie Freed and Lincoln Feast.
Our Standards: The Thomson Reuters Trust Principles. New Tab , opens new tab
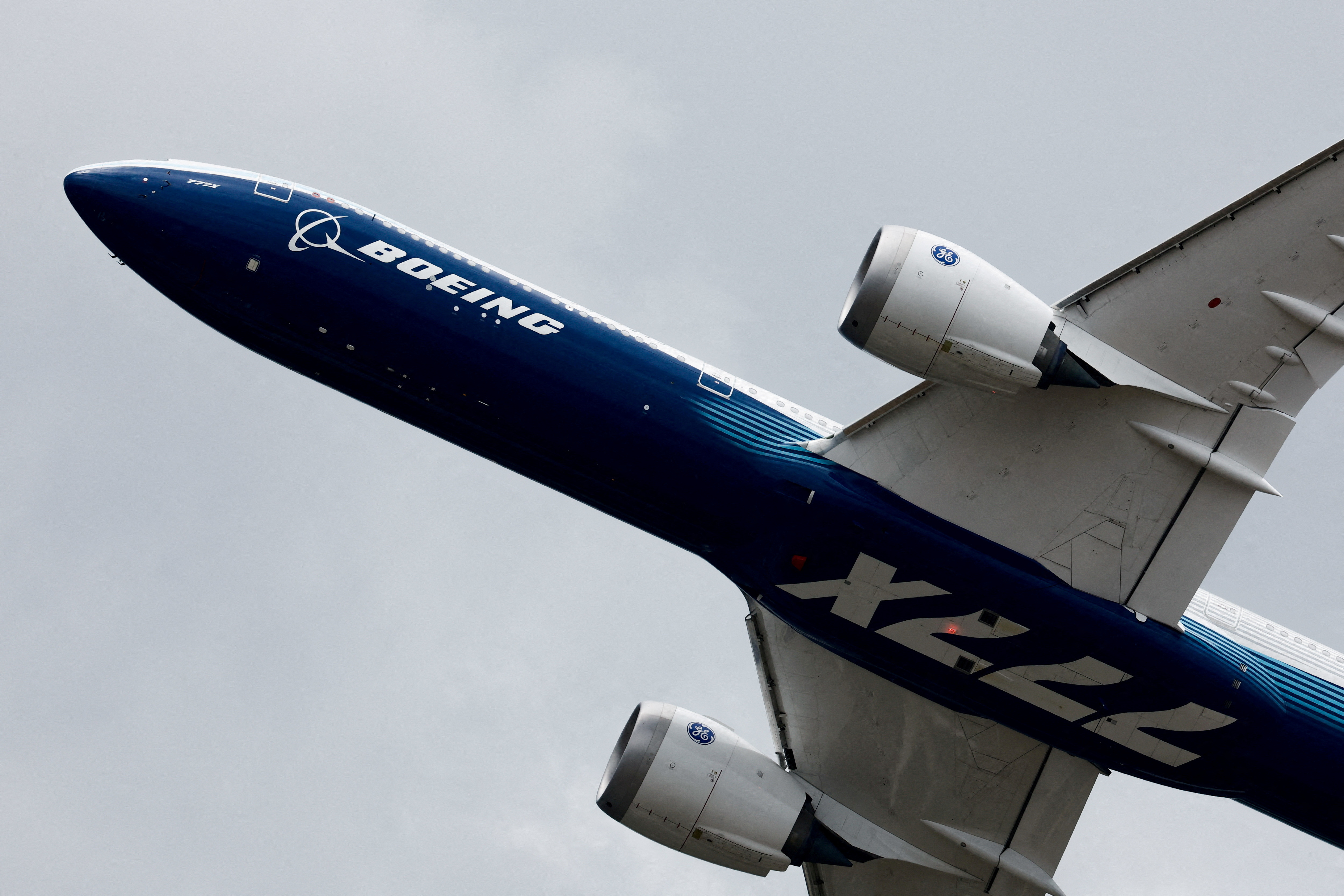
Business Chevron
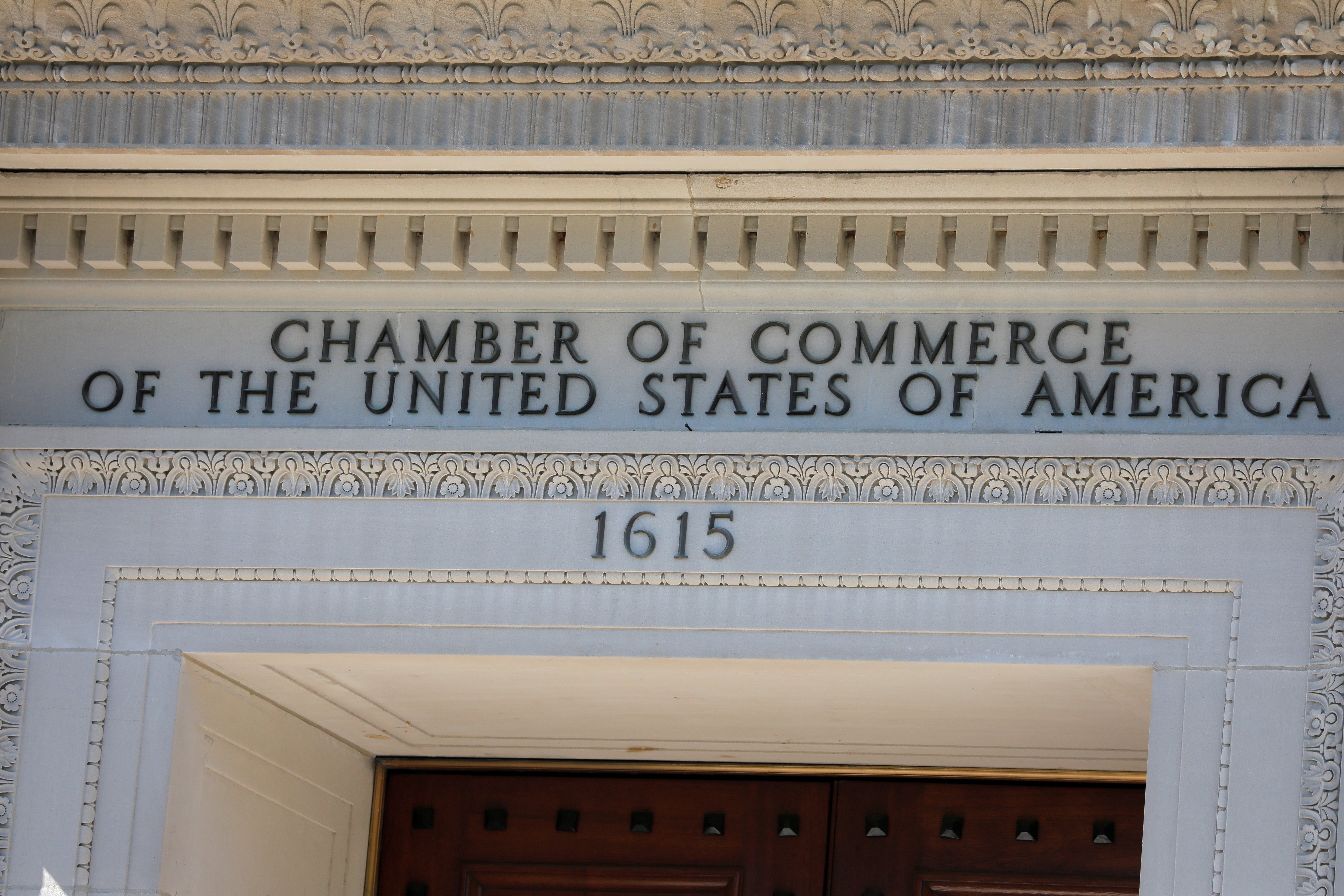
US ban on worker noncompete agreements faces lawsuit from major business group
The U.S. Chamber of Commerce, the country's largest business lobby, filed a lawsuit on Wednesday seeking to strike down a federal agency's near-total ban on employers requiring workers to sign agreements not to join rivals or launch competing businesses.
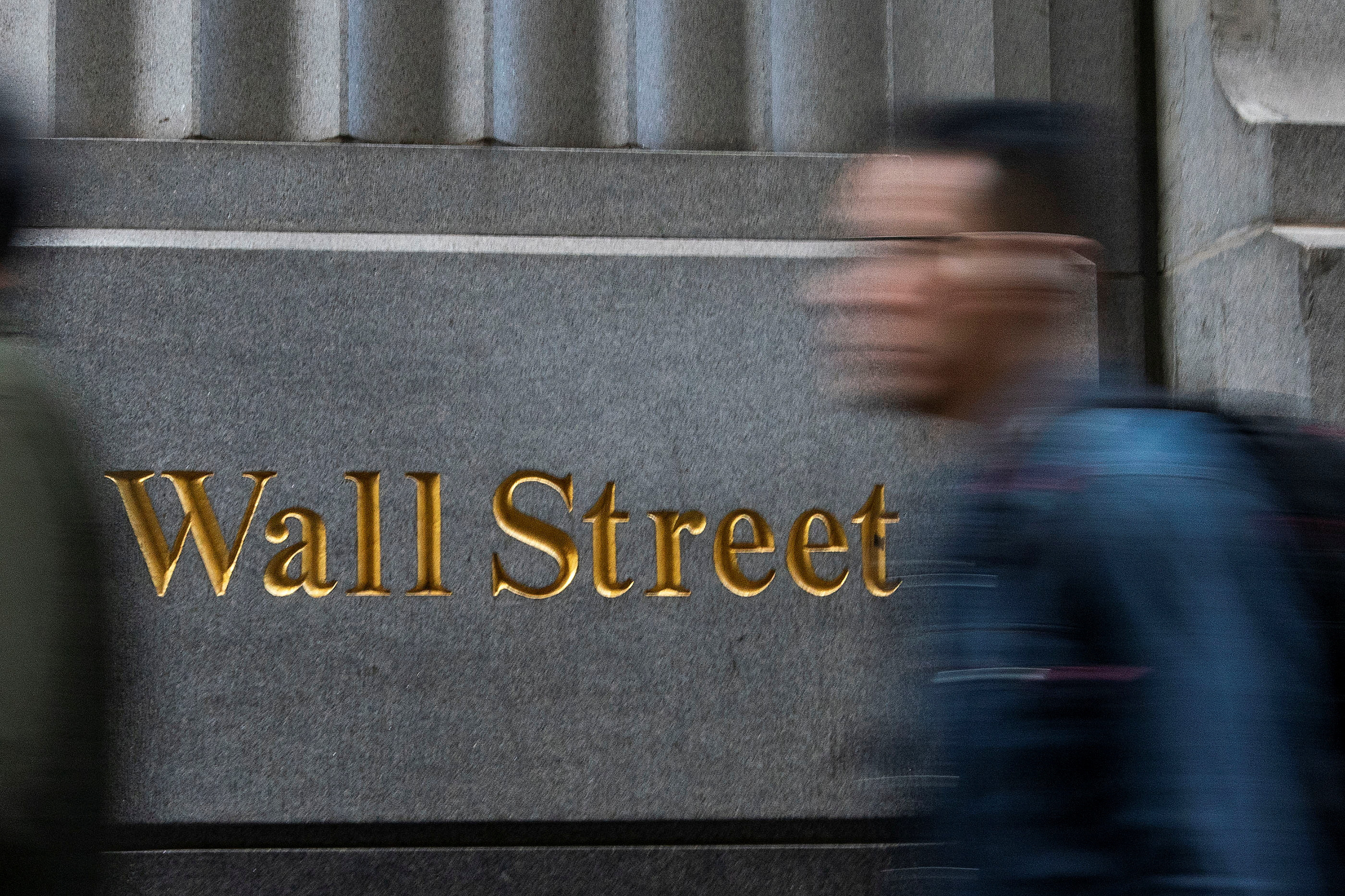
- Environment
In the wake of high-profile near misses, senators ask: Is Boeing doing enough?
A boeing engineer told lawmakers the company has been taking manufacturing shortcuts that led to “putting out defective airplanes,” part of a larger suite of allegations in the wake of a 737 max flight that saw its door plug blow out in midair. .
An engineer at Boeing said April 17 that the aircraft company, in rushing to produce as many planes as possible, is taking manufacturing shortcuts that could lead to jetliners breaking apart.
“They are putting out defective airplanes,” the engineer, Sam Salehpour, told members of a Senate subcommittee.
Mr. Salehpour was testifying about Boeing’s 787 Dreamliner, hundreds of which are in use by airlines, mostly on international routes. He spoke while another Senate committee held a separate hearing on the safety culture at Boeing.
The dual hearings were a sign of the intense pressure on Boeing since a door-plug panel blew off a 737 Max jetliner during an Alaska Airlines flight in January. The company is under multiple investigations, and the FBI has told passengers from the flight that they might be victims of a crime. Regulators limited Boeing’s rate of aircraft production, and even minor incidents involving its planes attract news coverage.
Mr. Salehpour alleged that workers at a Boeing factory used excessive force to jam together sections of fuselage on the Dreamliner. The extra force could compromise the carbon-composite material used for the plane’s frame, he said.
The engineer said he studied Boeing’s own data and concluded “that the company is taking manufacturing shortcuts on the 787 program that could significantly reduce the airplane’s safety and the life cycle.”
Mr. Salehpour said that when he raised concern about the matter, his boss asked whether he was “in or out” – part of the team, or not. “‘Are you going to just shut up?’ ... that’s how I interpreted it,” he said.
Boeing said retaliation is strictly prohibited. A spokesperson said the company encourages employees to speak up, and that since January it has seen more than a 500% increase in employee reports on a company portal.
The hearing of the investigations subcommittee marked the first time Mr. Salehpour has described his concern about the 787 and another plane, the Boeing 777, in public. Senators said they were shocked and appalled by the information. Democrats and Republicans alike expressed their dismay with the iconic American aircraft manufacturer.
The company says claims about the Dreamliner’s structural integrity are false. Two Boeing engineering executives said this week that in both design testing and inspections of planes – some of them 12 years old – there were no findings of fatigue or cracking in the composite panels. They suggested that the material, formed from carbon fibers and resin, is nearly impervious to fatigue, which is a constant worry with conventional aluminum fuselages.
The Boeing officials also dismissed another of Mr. Salehpour’s allegations: that he saw factory workers jumping on sections of fuselage on another one of Boeing’s largest passenger planes, the 777, to make them align.
Separately on April 17, the Senate Commerce Committee heard testimony from members of an expert panel that found serious flaws in Boeing’s safety culture.
One of the panel members, MIT aeronautics lecturer Javier de Luis, said employees hear Boeing leadership talk about safety, but workers feel pressure to push planes through the factory as fast as they can.
In talking to Boeing workers, Mr. de Luis said he heard “there was a very real fear of payback and retribution if you held your ground.”
The dual hearings added to criticism that has been heaped on Boeing since the door plug blew off an Alaska Airlines Boeing 737 Max as it flew over Oregon. Major safety failures have pushed Boeing into a crisis that has already resulted in a management shakeup, including the CEO’s decision to step down at the end of this year.
Sen. Ted Cruz, R-Texas, said the public is looking to Washington to ensure that boarding a plane is not getting more dangerous.
“Flying commercial remains the safest way to travel, but understandably, recent incidents have left the flying public worried. The perception is things are getting worse,” he said.
The Federal Aviation Administration, which regulates airlines and aircraft manufacturers, was also heavily criticized during the hearings on April 17.
The FAA was battered for the way it approved the 737 Max nearly a decade ago without fully understanding a key flight-control system. Two Max jets crashed in 2018 and 2019, killing 346 people. Critics continue to accuse the agency of being too cozy with Boeing.
“The FAA needs to be a regulator. They need to do their job. That’s the missing piece right now,” Joe Jacobsen, a former Boeing and FAA engineer, told the investigations subcommittee.
The FAA is now under a new administrator, Mike Whitaker, who has taken a tougher approach to Boeing. He limited Boeing’s production of 737 Max jets and gave the company until May 28 to produce a detailed plan for how it will fix manufacturing problems and resolve safety concerns.
Boeing is facing separate investigations by the FAA, the Justice Department, and the National Transportation Safety Board. The Justice Department could reopen a 2021 agreement in which Boeing avoided criminal prosecution on a charge of misleading regulators about the Max. In exchange, the company agreed to pay $2.5 billion – mostly to airline customers.
All the attention is taking a chunk from Boeing stock, which has tumbled in price by nearly one-third since the Alaska Airlines panel blowout. Shares of the Arlington, Virginia, company have lost 32% – more than $47 billion in market value.
Sen. Richard Blumenthal, the Connecticut Democrat who chairs the investigations subcommittee, and the panel’s senior Republican, Sen. Ron Johnson of Wisconsin, have asked Boeing and the FAA for troves of documents going back six years. Mr. Blumenthal said his subcommittee plans to hold more hearings on Boeing and hopes to hear from CEO David Calhoun.
In interviews and messages to employees, Mr. Calhoun has said many times that Boeing is taking steps to improve its manufacturing quality and safety culture. He called the Alaska Airlines accident a “watershed moment” from which a better Boeing will emerge.
There is plenty of skepticism about comments like that.
“We need to look at what Boeing does, not just what it says it’s doing,” said Sen. Tammy Duckworth, D-Ill.
This story was reported by The Associated Press.
Full HTML version of this story which may include photos, graphics, and related links.
Boeing posts a $355M loss as the plane maker tries to dig out from under its latest crisis

Remove the ads from your TribLIVE reading experience but still support the journalists who create the content with TribLIVE Ad-Free.
Get Ad-Free >
TribLIVE's Daily and Weekly email newsletters deliver the news you want and information you need, right to your inbox.
News Spotlight
- How to Choose the Right Roofing Material for Your Home Bella Construction & Development Inc Partner News
- NFL draft has been on tour for a decade and the next stop is Detroit, giving it a shot in spotlight TribLive
- Missouri hires Memphis athletic director Laird Veatch for the same role with the Tigers AP
- Are Ceramic Coatings Good For Your Car's Paint? Elusive Auto Shine Partner News
- Spanish judge freezes a bank account of Piqué's company amid probe into Saudi deal to host Super Cup AP
- PGA Tour has a team event in New Orleans. LIV Golf returns Down Under AP
- 5 Key Life Skills Your Child Can Gain from Martial Arts Training Norwin Ninjas Partner News
- Capturing Spirituality on Screen: 3 Paths to Engagement and Preservation Through Video Agape Lane Ministry Partner News
- Trib Total Media named best newspaper in Pa. by Society of Professional Journalists TribLive
- Spring Hiking near Foggy Mountain Lodge Foggy Mountain Lodge Partner News
'Flora' statue unveiled as Pittsburgh’s 1st to depict woman of color
Video of Boeing's Dreamliner buzzing Hilton Head's iconic No. 18 at 2024 RBC Heritage
Apr. 20—The humongous Dreamliner made its appearance right on cue at RBC's Heritage Presented by Boeing on Saturday afternoon.
At 224 feet long with a wing span of 197 feet and a passenger capacity of 320, Boeing's 787-9 is the largest airplane in the fleet of WestJet, a Calgary-based airliner. The gigantic passenger airplane is assembled in North Charleston.
This is the 13th year Boeing has been a sponsor of the PGA Tour tournament, and the flyover has become a tournament tradition and a highlight for players and fans.
This story was originally published April 20, 2024, 5:17 PM.
(c)2024 The Island Packet (Hilton Head, S.C.) Distributed by Tribune Content Agency, LLC.
Simple Flying
Boeing still lost less than q1 last year despite 737 max issues and airline compensation.
While it has reduced its losses, the operating cash flow and lower revenues are a cause for concern for Boeing.
- Even if Boeing reduced its net losses, its operating cash outflow increased significantly.
- The manufacturer said that the results reflected the temporarily 737 MAX 9 grounding and subsequent customer compensations.
- David Calhoun, the outgoing chief executive of Boeing, emphasized safety and quality above everything else.
While Boeing has managed to reduce its losses Year-on-Year (YoY) during the first quarter of the year, the aircraft manufacturer’s revenues and operating cash flows were a sore sight for investors. Still, in a publicly available letter to employees, David Calhoun, the president and chief executive officer (CEO) of Boeing, emphasized that its focus remains on sweeping actions the manufacturer is taking after the Alaska Airlines flight AS1282 incident that happened in January 2024.
Diminishing revenues and burning through cash
While its net loss (under generally accepted accounting principles (GAAP) and core operating loss (non-GAAP) improved YoY, with Boeing posting a $355 million and $388 million loss, respectively, the manufacturer’s revenues have gone down. While in Q1 2023, it earned $17.9 billion in revenue, its Q1 2024 income dwindled to $16.5 billion.
Meanwhile, its negative operating cash flow (GAAP) worsened significantly, with operating cash outflow in Q1 2023 being $318 million. In Q1 2024, the operating cash outflow grew to $3.3 billion. According to Calhoun, the results reflected the fact that Boeing slowed down the production of the 737 to improve quality in its manufacturing processes.
“We will take the time necessary to strengthen our quality and safety management systems and this work will position us for a stronger and more stable future.”
As such, its free cash flow (FCF) was -$3.9 billion in Q1 2024, compared to -$786 million a year prior. “Operating cash flow was ($3.4) billion in the quarter reflecting lower commercial deliveries, as well as unfavorable timing of receipts and expenditures,” the company said, adding that the results reflect lower 737 deliveries and compensations for the 737 MAX 9 groundings.
Boeing Will Pause Renton Manufacturing For 24 Hours Tomorrow
36% fewer deliveries.
Speaking about its Boeing Commercial Airplanes (BCA) division, the company detailed that it delivered 36% fewer aircraft during the quarter, which resulted in BCA’s revenues shrinking from $6.7 billion to $4.6 billion (-31%) YoY. As a result, the subsidiary’s operating margin worsened to -24.6%.
“During the quarter, the 737 program slowed production below 38 per month to incorporate improvements to its quality management system and reduce traveled work within its factory and supply chain. In addition, Commercial Airplanes is implementing a comprehensive action plan to address feedback from the FAA audit of 737 production.”
In terms of other aircraft programs, Boeing delivered zero 777F freighters, while handing over one one P-8 Poseidon (based on the 737-800), one 767F, 11 787-9, two 787-10, and two KC-46s. In total, including the 737 MAX, the aircraft manufacturer’s customers received 83 aircraft, compared to 130 in Q1 2023.
Boeing Reports 36% Decline In Quarterly Aircraft Deliveries
Emphasizing safety and quality.
Calhoun addressed the company's employees in a letter published on the same day as its financial results, saying that tis focus remains on the “sweeping actions we are taking following the Alaska Airlines Flight 1282 accident," which happened in January 2024.
“Importantly, the foundation of our work is listening to our people. Since Jan. 5, more than 70,000 of you have participated in Quality Stand Downs across more than a dozen Boeing sites. From those, we’ve received more than 30,000 ideas on how we can improve. And this year, we’ve seen more than a 500% increase in employee Speak Up submissions compared to 2023.”
While Calhoun admitted that in the near term, Boeing is currently in a challenging financial situation, he once again asserted that safety and quality must and will come above everything else. According to the manufacturer’s chief executive, there is a lot more work to be done, but the company was fully confident in its future.
“You are why I’m so confident in our future. Together we will ensure that Boeing is the company the world needs, and the one that we are all proud to work for every day.”
Calhoun, including several other Boeing executives, announced that he will be leaving the company at the end of the year on March 25. Stan Deal, the now-retired CEO of BCA, retired with immediate effect, while Larry Kellner, the chair of the board, informed Calhoun that he would not be seeking reelection for his position.
Boeing CEO Resigns Amidst 737 MAX Crisis Top Management Shakeup

Boeing posts quarterly loss as it slows 737 factory

Boeing burned through nearly $4 billion in the most recent quarter as fallout from the Alaska Airlines midair accident exacted a financial toll.
The jet maker reported a $355 million loss as revenue fell 8% from a year ago in quarterly results that were slightly better than expectations. Under pressure from airlines and regulators to clean up its operations, the company has slowed its factories and stopped providing most financial targets earlier this year.
“Near term, yes, we are in a tough moment," outgoing Chief Executive Dave Calhoun said in a message to employees. “Lower deliveries can be difficult for our customers and for our financials."
Boeing is building fewer of its 737 MAX jets as the company weeds out quality problems at the Renton, Wash., factory that makes the planes. The company faces added inspections and heightened regulatory scrutiny following the Jan. 5 near tragedy. It delivered 83 commercial airplanes in the March quarter, a 36% drop from a year ago.
The production slowdown of the bestselling planes means the company’s operations are burning cash. Boeing warned investors last month that it would take a hit of between $4 billion and $4.5 billion for the year’s first quarter, larger than it previously forecast. The company ended March with $7.5 billion of cash and investments, less than half what it had at the start of the year.
Meantime, Boeing faces a separate problem with its 787 Dreamliner. A shortage of some key parts means the company can’t increase production of the wide-body jets as quickly as it hoped.
For the March quarter, the company reported an adjusted loss of $1.13 per share on revenue of $16.6 billion. On that basis, analysts had predicted an adjusted loss of $1.63 per share on revenue of $16.2 billion.
The results come a month after Boeing announced Calhoun will exit at the end of the year as part of an executive shake-up. The head of Boeing’s commercial-aircraft business, Stanley Deal, stepped down and its board chair, Larry Kellner, won’t stand for re-election.
Calhoun, in his employee letter, said the company is seeing results from efforts to improve quality.
“We are using this period, as difficult as it is, to deliberately slow the system, stabilize the supply chain, fortify our factory operations and position Boeing to deliver with the predictability and quality our customers demand for the long term," he said.
On Tuesday, jet fuselage supplier Spirit AeroSystems said Boeing would give it $425 million in advance payments to cover costs tied to Boeing’s quality-improvement efforts.
Spirit’s factory in Wichita, Kan., made the fuselage involved in the Alaska Airlines door-plug blowout in January.
Spirit now must make its own quality improvements, while dealing with inventory buildup as well as a new mandate from Boeing that jet fuselages must be defect-free before being shipped to Renton.
Write to Sharon Terlep at [email protected]
MINT SPECIALS
Wait for it….
Log in to our website to save your bookmarks. It'll just take a moment.
You are just one step away from creating your watchlist!
Oops! Looks like you have exceeded the limit to bookmark the image. Remove some to bookmark this image.
Your session has expired, please login again.
Congratulations!
You are now subscribed to our newsletters. In case you can’t find any email from our side, please check the spam folder.

Subscribe to continue
This is a subscriber only feature Subscribe Now to get daily updates on WhatsApp

- Bahasa Indonesia
- Slovenščina
- Science & Tech
- Russian Kitchen
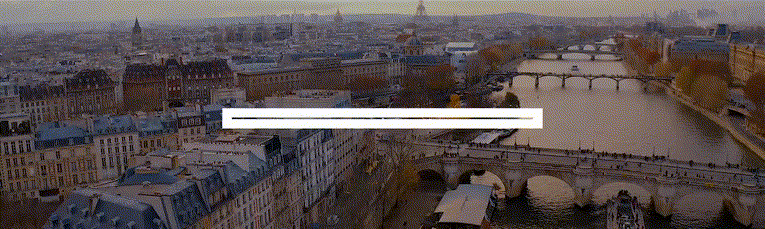
IMAGES
VIDEO
COMMENTS
Step inside the world's largest factory for a behind-the-scenes look at the Boeing Everett Factory and 777 assembly line. Each tour is an 80-minute guided experience with a front row view of current airplane production, the Everett site's history, and the central role it plays in the future of commercial aviation. Tours are available Thursday ...
Let's Tour Together. Step inside the world's largest factory for a behind-the-scenes look at the Boeing Everett Factory and 777 assembly line. Each tour is an 80-minute guided experience with a front row view of current airplane production, the Everett site's history and the central role it plays in the future of commercial aviation.
Boeing said in 2020 that it would consolidate 787 production in Charleston instead of splitting it between South Carolina and Washington, a move which was completed the following year. TPG had a chance to tour the factory last December ahead of an event marking United Airlines' new order for up to 200 airplanes.
The factory in Everett has produced some of the most iconic widebody aircraft, including the 747, 767, 777, and the 787 Dreamliner. Boeing provides a behind-the-scenes tour of its factory and the assembly line. The tour includes the Boeing Gallery, Sky Deck, and the Boeing Store. According to Boeing,
Get an inside look at the Boeing South Carolina facility where the energy-efficient 787 Dreamliner is built. Watch as many diverse teams come together to create an airplane that lives up to Boeing's principles of safety, quality, and integrity. After watching the virtual tour, download the DreamLearners activity, to learn what it's like to ...
The tour provides a glimpse into the fascinating world of aviation, with a behind-the-scenes look at the assembly line of iconic Boeing aircraft, which included the 747, 767, 777, and 787 Dreamliner. Christi Medlyn, Boeing Future of Flight general manager, shared the excitement surrounding the reopening with Business Traveler USA.
Our Story. Boeing South Carolina is the the home of the 787 Dreamliner, where the full cycle of 787 Dreamliner production happens - from freezer to flight. Our teammates fabricate, assemble and deliver the 787-8, 787-9, and 787-10 to customers all over the world. In addition to the Dreamliner assembly, Boeing South Carolina is home to Boeing ...
Aviation enthusiasts get an exclusive Boeing factory tour where some of the world's biggest, most advanced airliners are made, including 747, 777 and 787.
Want to know how aerospace innovations get off the ground? Get an inside look at the Boeing South Carolina facility where the energy-efficient 787 Dreamliner...
The Boeing factory tour, part of the company's Future of Flight experience in Mukilteo, Washington, will soon be back. Newsletter ... such as the Boeing 777, 787 Dreamliner, 767, and the 747 ...
It has played a pivotal role in the production of iconic Boeing aircraft, including the 747, 767, 777, and 787 Dreamliner. Factory Tour tickets are available for purchase online today at BoeingFutureofFlight.com, in-person at Boeing Future of Flight and through the Call Center 1-800-464-1476. Advance ticket purchase is highly recommended as ...
Step inside the world's largest building by volume where the Dreamliner gets its wings: Boeing's Everett factory in Washington state, USA. Roughly 50km north of Seattle, that single building churns out 10 Boeing 787s every month - over 230 to date - and also houses the assembly lines of the Boeing 747-8, 767 and 777. Join Australian Business Traveller as we peek behind the scenes ...
Step inside the world's largest factory for a behind-the-scenes look at the Boeing Everett Factory and 777 assembly line. Each tour is an 80-minute guided experience with a front-row view of current airplane production, the Everett site's history and the central role it plays in the future of commercial aviation. Annual Passholders — please ...
Korean Air shows off new Boeing Dreamliner in South Carolina. Boeing's North Charleston factory is capable of producing all three variants of the Dreamliner - the 787-8, 787-9 and 787-10 ...
The Dreamliner's quiet revolution. I've been warned. "The cool factor in here is pretty awesome," says Kim Westenskow, Boeing's 787 factory superintendent, Position 4, as she escorts me ...
Overview. Boeing's Everett Site is heralded as having the largest manufacturing building in the world, producing the 747, 767, 777, and the 787 airplanes. Thousands of aerospace employees in Everett support aircraft fabrication and production, product development, aviation safety and security and airplane certifications.
Welcome to the Boeing Everett Factory Tour !We are inside the biggest Building in the World by volume ! Here, Boeing is assembling the famous Boeing 747, but...
Boeing's famous factory in Everett, Washington is reopening its tours after being shut down since 2020 due to the COVID-19 pandemic. ... Since its groundbreaking in 1966, the factory has produced the 747, 767, 777, and the 787 Dreamliner. The factory is also recognized as the largest building in the world by volume. It takes up 98.3 acres and ...
By David Parker Brown. The Boeing 787 Dreamliner line inside the Boeing Factory. Here are 787s for Air India, JAL and China Southern. During the Boeing 747-8 Intercontinental event, invited guests were allowed into factory to not only take a look at the Boeing 747-8I and 747-8F, but also the Boeing 777 Worldliner and Boeing 787 Dreamliner.
Reporting from Boeing's factory in North Charleston, S.C. April 15, 2024. Boeing sought on Monday to reassure the public of the safety of its 787 Dreamliner plane days before a whistle-blower is ...
The cycles of pressurization and depressurization are the contributors to fatigue on metal airplanes. In service, a 787 currently flies about 600 flight cycles per year on average and will operate safely for many decades before retirement. Supported by a 1.2 million-pound (544,000-kilogram) test rig, the airplane's wings, fuselage and tail ...
At a media tour of its 787 Dreamliner manufacturing plant in South Carolina held Monday, two top Boeing engineers defended the structural integrity of the 787, saying the wide-body jet was stress ...
Boeing expects a slower increase in the production rate and deliveries of its 787 widebody jets as the U.S. planemaker wrestles with supplier shortages "on a few key parts," an executive on the ...
The 787 Dreamliner, piloted by Boeing captains Ricardo Traven and Tommy Schueler, will fly over the 18th fairway at the RBC Heritage PGA Tour golf tournament at 4 p.m. Details of annual Dreamliner ...
Mr. Salehpour was testifying about Boeing's 787 Dreamliner, hundreds of which are in use by airlines, mostly on international routes. ... that he saw factory workers jumping on sections of ...
The most recent, a quality engineer, told Congress last week that Boeing is taking manufacturing shortcuts that could eventually cause 787 Dreamliners to break apart. Boeing pushed back ...
At 224 feet long with a wing span of 197 feet and a passenger capacity of 320, Boeing's 787-9 is the largest airplane in the fleet of WestJet, a Calgary-based airliner. The gigantic passenger ...
In terms of other aircraft programs, Boeing delivered zero 777F freighters, while handing over one one P-8 Poseidon (based on the 737-800), one 767F, 11 787-9, two 787-10, and two KC-46s. In total, including the 737 MAX, the aircraft manufacturer's customers received 83 aircraft, compared to 130 in Q1 2023.
Boeing posts quarterly loss as it slows 737 factory. Sharon Terlep , The Wall Street Journal 2 min read 24 Apr 2024, 07:17 PM IST. Boeing faces a separate problem with its 787 Dreamliner. A ...
Bratsk is a city in the Irkutsk region which is on the Angara River near the vast Bratsk Reservoir. The population is not so big in comparison to other Russian towns at the 260,000 mark. The ...