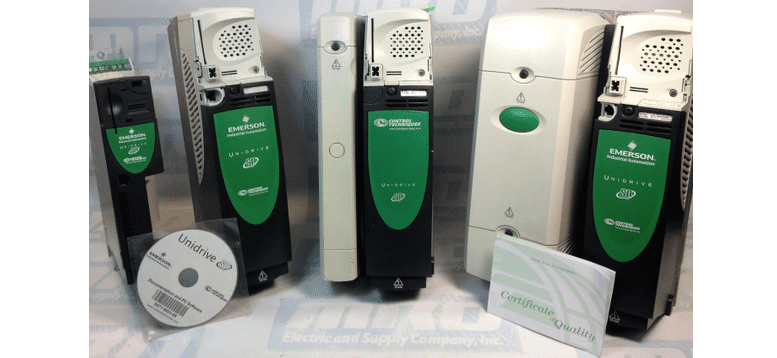
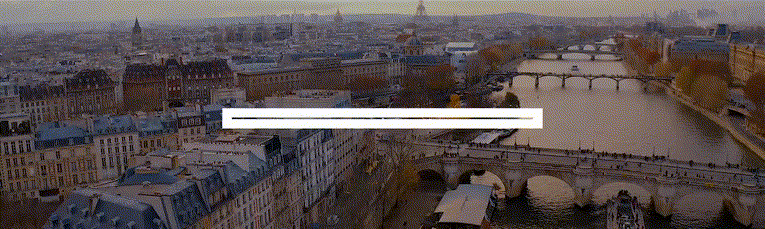
Emerson Industrial Automation: Unidrive SP Troubleshooting
Updated August 2019: Click here to view Unidrive fault codes .
DIGITAL INPUTS
The Unidrive SP can be enabled to run in several ways. The drive can use digital inputs, keypad, or a field buss networks to give the OK to run. The drive will display inh, rdy, or run depending on the given commands. The drive can be programmed to use positive or negative logic. The logic type is set up at #8.29 in the Control Techniques Unidrive SP. The Unidrive SP defaults to positive logic. When the drive is in positive logic you will need to inject +24VDC to activate the digital inputs. The +24VDC can be supplied by the drive or externally.
The Unidrive SP can be enabled to run in numerous ways.
When the drive is in the terminal mode the following sequence occurs under default conditions:
Unidrive SP:
Inh = drive disabled = connect pins 22-31 drive should go to rdy, rdy = drive enabled = connect pins 22-26 drive should go to run, run = drive is enabled and ready to run when a speed reference is applied.
Parameter #0.05 sets up the Reference Select. This will tell the drive where to search for run commands and speed references. You will only need to close the enable signal if it is set to pad. Then, the keypad can be used to control the drive and to set the speed reference. The speed reference will come in on an analog input if you choose a terminal code. The digital inputs will select the enable, run, and preset selections. The drive should operate as seen above if the digital inputs are activated correctly.
DRIVE SEQUENCER
When the drive is not running, there are several additional parameters in menu 6 that can assess the issue. The digital inputs may be configured wrong or inactive if the parameters are not going to a 1 with the corresponding commands. Check the following parameters:
#6.15 = 1 = Drive enabled
#6.43 = 1 = Control word disabled, Set to 1 for Field Buss Control
#6.29 = 1 = Hardware Enable (Pin 31 is activated)
#6.30 = 1 = Run Forward #6.31 = 1 = Jog
#6.32 = 1 = Run Reverse
#6.33 = 1 = Forward/Reverse
#6.34 = 1 = Run
#6.37 = 1 = Jog Reverse
#6.39 = 1 = Not Stop

The voltage on the corresponding digital inputs should be measured if the parameters in menu 6 aren’t changing state accordingly. The DC voltage should change between 0VDC and 24VDC when a command is given. Check the digital input configuration in menu 8 if menu 6 isn’t changing and the voltage is.
CONTROL WORD
To control the start/stop functions, the drive does not have to use the digital inputs. When #6.43 = 1 the control word is enabled. The drive will now accept a decimal value from 0 to 32767 at #6.42. This decimal value can be converted to a binary value.To see the function that will be carried out, you can reference the binary value to the chart below.
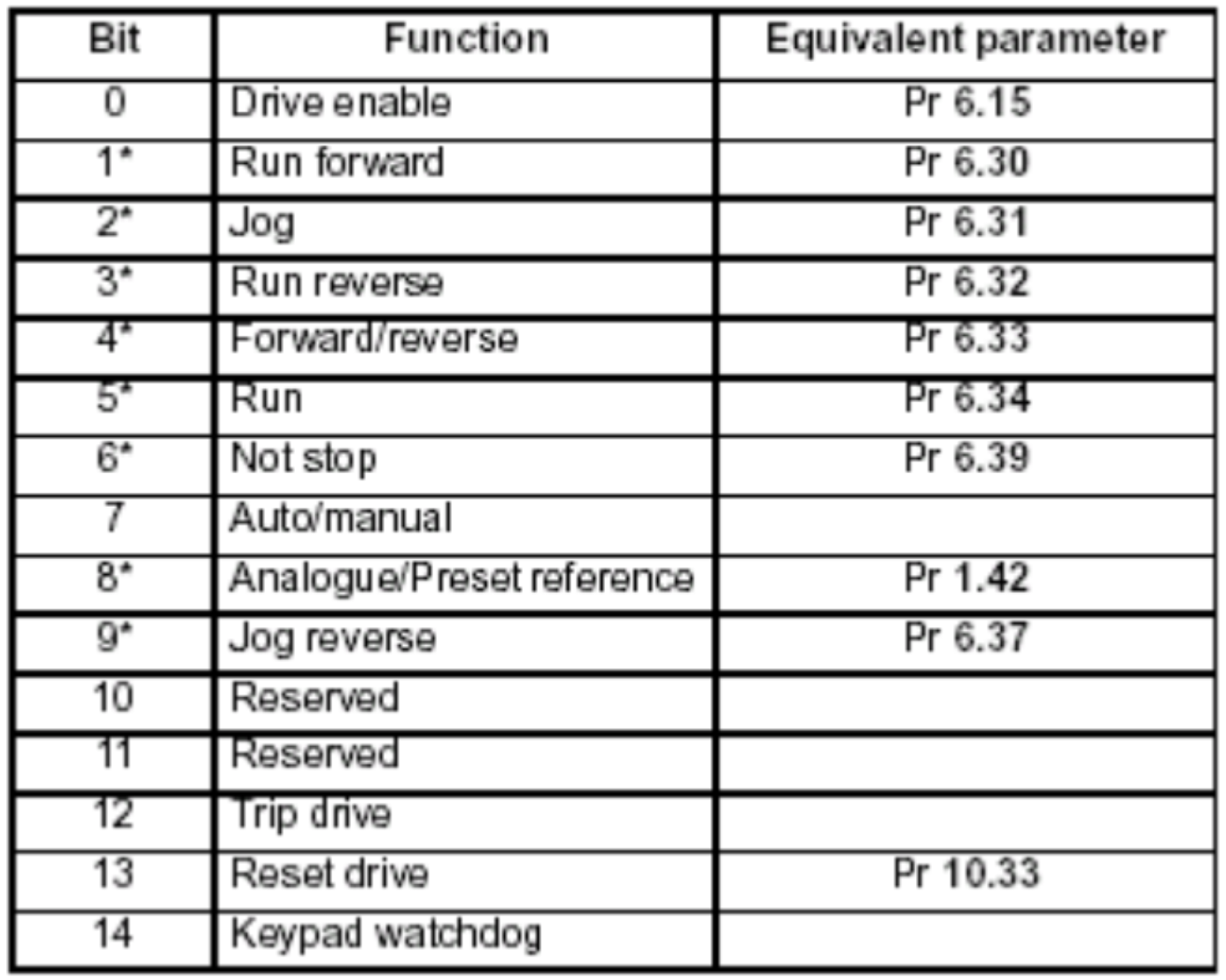
Speed Reference
The drive still may not run if the digital inputs and the drive sequencer are each working properly. There could be an issue with the speed reference to the drive if the display shows Run but the motor isn’t turning. The speed reference is able to be applied in several methods. An analog input can be used (current or voltage), preset speeds, and a field buss reference. The example is a 0-10VDC signal on analog input #1.
The final speed of the demand is parameter #3.01. The speed reference should be displayed here if the digital inputs and the drive sequencer are failing to operate properly. Check menu 1 and 2 to determine where it is stopping if the reference is not getting to this point.
If the drive is running in torque mode, the torque reference will come on parameter #4.08 under default conditions. #4.08 is able to be linked to an analog input or be written to via a filed buss network.
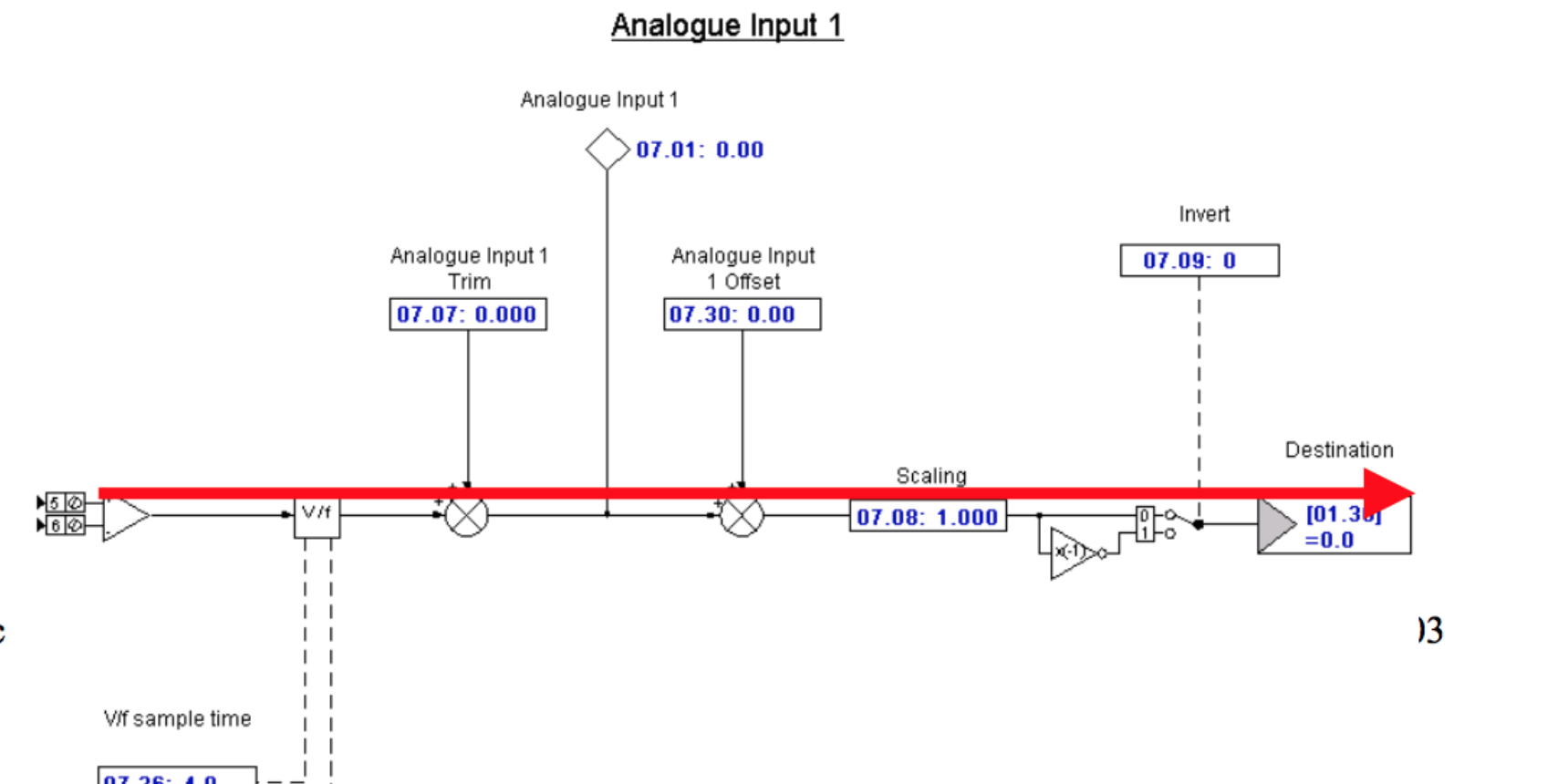
#7.01 should be inspected to determine if it changes with the change in reference at terminal 5 once the signal has been confirmed. #7.01 goes from +/- 0% – 100%. Check the destination of the speed reference at #7.10 if everything looks good. Follow it to the destination and confirm the speed reference value is arriving there and then through #3.01.
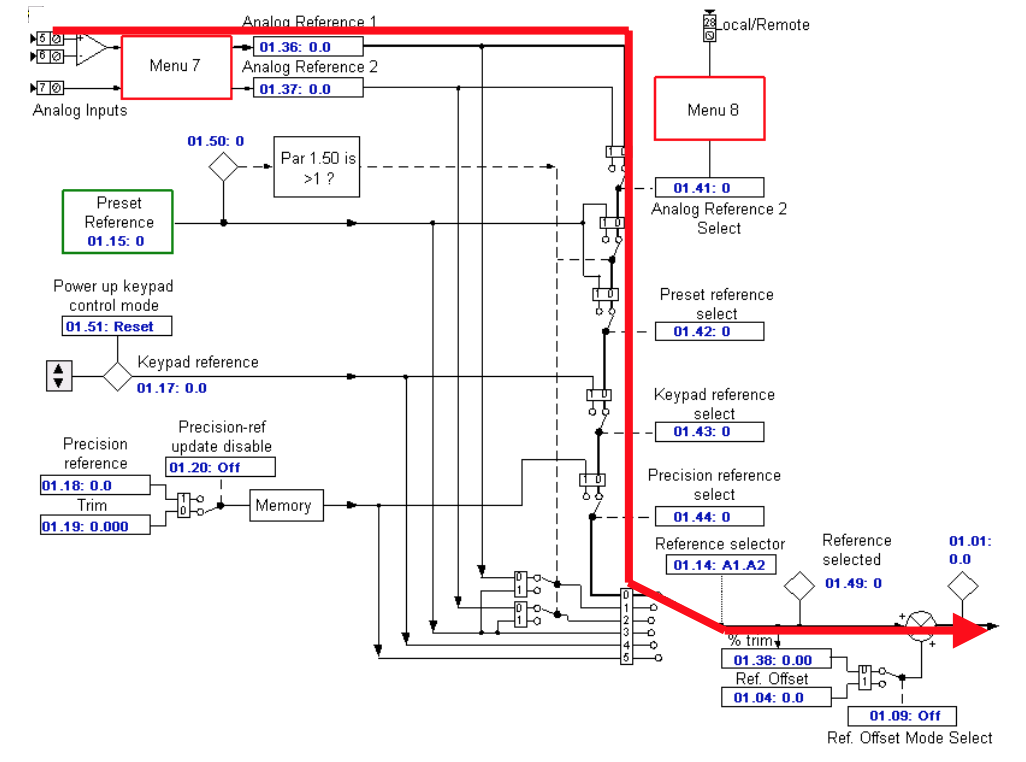
Contact the America’s Service Center if the drive will still not run after the Speed Reference, Digital Inputs and Drive Sequencer have all been confirmed.
MRO Electric and Supply has new and refurbished Control Techniques Unidrives available now, and also offers repair pricing. For more information, please call 800-691-8511 or email [email protected] .
Updated on August 22, 2019 by Brian Hughes
Joe Kaminski
Joe Kaminski is an industrial automation specialist at MRO Electric. He has a background in industrial engineering and supply chain management. Joe has worked in the automation industry for over 10 years providing support to some of the largest companies in the world. For more info, visit www.mroelectric.com .
4 thoughts to “Emerson Industrial Automation: Unidrive SP Troubleshooting”
I have problem in 675KW pump motor drive SP size 9 with four SM module of 200KW,two +two drive connected in parallel operation,One side 1&2 and other side 3&4.1 is master with SM control module, My problem is that 3&4 drive U phase is taking zero current ,U&V phase are taking current,drive running with 30% load fine no issue from many months. But if i run 90 to 100 % load then i am facing problem of temp increase as total load of u phse is shared by 1&2 U phase.I have changed 3&2 module,SM module.but same poblem.Please guide .
I want to make enquiry if I can send a damaged emerson industrial automation SP 2402 to your company for repair.If yes, at what cost, time and process? Thank you
Our Unidrive SP displayed trip Oldc.p, the board is checked ok, the IGBTs checked ok. What can we do next
It would be nice if someone would publish a picture of the Emerson keypad with a description of the buttons/joystick functions, since Emerson didn’t bother to do so in their manuals. e.g. what does the M button do?
Leave a Reply Cancel reply
Your email address will not be published. Required fields are marked *
This site uses Akismet to reduce spam. Learn how your comment data is processed .
Helpful Links
- Control Techniques
- Schneider Electric
- (800) 691-8511
- (919) 367-6379
- [email protected]
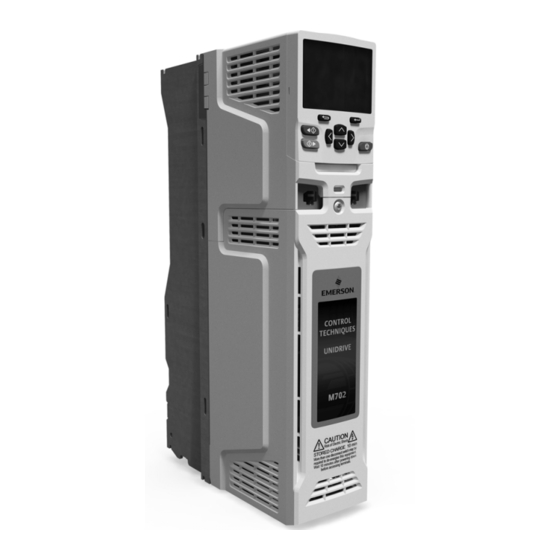
- Emerson Manuals
- Unidrive M702
- User manual
Emerson Unidrive M702 User Manual
- Getting started manual (72 pages)
- User manual (198 pages)
- Installation manual (120 pages)
- page of 285 Go / 285
Table of Contents
- Product View
- General Information
- How to Use this Guide
1 Safety Information
- Warnings, Cautions and Notes
- Electrical Safety - General Warning
- System Design and Safety of Personnel
- Environmental Limits
- Fire Protection
- Compliance with Regulations
- Mechanical Brake Control
- Electrical Installation
2 Product Information
- Model Number
- Introduction
- Typical Short Term Overload Limits
- Open Loop Mode
- RFC-A Mode/Rfc- S
- Compatible Position Feedback Devices
- Drive Features
- Options Available with the Drive
- Option Module Identification
- Keypad Identification
- Items Supplied with the Drive
- Additional Options
3 Mechanical Installation
- Environmental Protection
- Safety Information
- Planning the Installation
- Location and Identification of Terminal Covers
- Removing the Finger-Guard and DC Terminal Cover Break-Outs
- Removal of a Standard Option Module
- Installation and Removal of a Large Option Module
- Installation and Removal of the KI-Keypad
- Surface Mounting
- Mounting Brackets
- Recommended Spacing between the Drives
- Enclosure Sizing
- Calculating the Size of a Sealed Enclosure
- Calculating the Air-Flow in a Ventilated Enclosure
- Enclosure Design and Drive Ambient Temperature
- Heatsink Fan Operation
- Installing the Gasket
- Installation of High IP Insert
- Through Panel Mounting
- Heatsink Mounted Brake Resistor
- Internal Braking Resistor Installation
- External EMC Filter
- Location of the Power and Ground Terminals
- Terminal Sizes and Torque Settings
- Routine Maintenance of the Drive
- Plug-In Terminal Block Maximum Cable Sizes
- External EMC Filter Terminal Data
- Real Time Clock Battery Replacement
- Fan Removal Procedure
4 Electrical Installation
- AC and DC Connections
- Ground Connections
- AC Supply Requirements
- Supplies Requiring Line Reactors
- Input Inductor Calculation
- DC Bus Paralleling
- 24 VDC Supply
- Low Voltage Operation
- AC Input Current and Fuse Ratings (200 V)
- Input Current and Fuse Ratings (400 V)
- AC Input Current and Fuse Ratings (575 V)
- Input Current and Fuse Ratings (690 V)
- Cable Ratings
- Cable Types and Lengths
- High-Capacitance / Reduced Diameter Cables
- Motor Winding Voltage
- Multiple Motors
- Output Contactor
- Heatsink Mounted Braking Resistor
- Braking Resistor Overload Protection Parameter Settings
- Heatsink Mounted Braking Resistor Data
- External Braking Resistor
- Thermal Protection Circuit for the Braking Resistor
- EMC (Electromagnetic Compatibility)
- Braking Resistor Software Overload Protection
- Grounding Hardware
- Drive and EMC Filter Cross Reference
- Installation of Grounding Clamp
- Internal EMC Filter
- General Requirements for EMC
- Feedback Device Cable Shielding
- Supply and Ground Cable Clearance
- Grounding the Drive, Motor Cable Shield and Filter
- Sensitive Signal Circuit Clearance
- Grounding the Motor Cable Shield
- Variations in the EMC Wiring
- Interruptions to the Motor Cable
- Using a Motor Isolator / Disconnect-Switch
- Surge Immunity of Control Circuits
- Ethernet Fieldbus Communications
- Surge Suppression
- Control Connections
- Control Terminal Specification
- Position Feedback Connection Details
- Position Feedback Terminal Specifications
- Safe Torque off (STO)
- Sincos Encoder Resolution
- Keypad Operation
- Control Buttons
5 Getting Started
- Quick Access Mode
- Keypad Shortcuts
- Display Modes
- Menu Structure
- Mode Examples
- KI-Keypad Set-Up Menu
- Display Messages
- Alarm Indications
- Changing the Operating Mode
- Saving Parameters
- Restoring Parameter Defaults
- Parameter Access Level and Security
- Displaying Parameters with Non-Default Values Only
- Displaying Destination Parameters Only
- Communications
- User Security Level / Access Level
6 Basic Parameters
- Menu 0: Basic Parameters
- Parameter Descriptions
7 Running the Motor
- Quick Start Connections
- Minimum Connections to Get the Motor Running in any Operating Mode
- RFC - a Mode (with Position Feedback)
- RFC-A Mode (Sensorless Control)
- RFC-S Mode (with Position Feedback)
- P1 Position Interface
- Detailed Feedback Device Commissioning / Start-Up Information
- P2 Position Interface
- Software Mode - Incremental Signals
- Software Mode - Absolute SSI Data
8 Optimization
- Rated Speed/Number of Motor Pole
- Rated Power Factor
- Open Loop Control Mode
- Enable Slip Compensation
- Induction Motor with Position Feedback
- Motor Rated Current
- Rated Voltage/Frequency
- Motor Parameter Adaptive Control
- Current Loop Gains
- Speed Loop Gains
- Permanent Magnet Motor with Position Feedback
- Stationary Autotune/Rotating Autotune
- Inertia Measurement Test
- Maximum Motor Rated Current
- Current Limits
- Motor Thermal Protection
- Switching Frequency
- Encoder Feedback Limits
- Permanent Magnet Motor High Speed Operation
- Quasi-Square Wave (Open-Loop Only)
- Unidrive M702 User Guide Issue Number
9 NV Media Card Operation
- SMARTCARD Support
- Writing to the SMARTCARD
- Reading from the SMARTCARD
- Booting up from the SMARTCARD on Every Power up
- NV Media Card Parameters
- Data Block Header Information
- NV Media Card Trips
- Onboard PLC and Machine Control Studio
- Onboard PLC Parameters
- Onboard PLC Trips
11 Advanced Parameters
- Feature Look-Up Table
- Parameter Ranges and Variable Minimum/Maximums
- Menu 1: Frequency / Speed Reference
- Menu 2: Ramps
- Freeze System Logic
- P1 Position Feedback Interface Thermistor Input
- Encoder Simulation
- Menu 4 RFC-A Logic Diagram
- Menu 4 RFC-S Logic Diagram
- Menu 5 Open-Loop Logic Diagram
- Menu 5 RFC-A, RFC-S Logic Diagram
- Menu 6 Logic Diagram
- Menu 6 Low Voltage Operation
- Menu 7: Temperature Monitoring
- Menu 8: Digital I/O
- Menu 8 Logic Diagram
- Menu 9: Programmable Logic, Motorized Pot, Binary Sum and Timers
- Menu 9 Logic Diagram: Scope Function
- Menu 10: Status and Trips
- Menu 11: General Drive Set-Up
- Menu 12 Logic Diagram
- Open-Loop Brake Function
- Open-Loop Brake Sequence
- RFC-A Mode with Brake Controller Mode
- RFC-A Brake Sequence
- RFC-A Mode (Brake Controller (12.052) = 0) and RFC-S Mode
- Menu 13: Standard Motion Controller
- Menu 13 Logic Diagram
- Menu 14: User PID Controller
- Menu 14 Logic Diagram
- Menus 15, 16 and 17: Option Module Set-Up
- Location of Option Module Slots and Their Corresponding Menu Numbers
- Menu 18: Application Menu 1
- Menu 19: Application Menu 2
- Menu 20: Application Menu 3
- Menu 21: Second Motor Parameters
- Menu 22: Additional Menu 0 Set-Up
- Slot 4 Menu 0: Ethernet Status and Monitoring
- Slot 4 Menu 2: Ethernet Configuration
- Slot 4 Menu 9: Resources
- Slot 4 Menu 10: Easy Mode
- Slot 4 Menu 11: Synchronization
- Slot 4 Menu 15: Modbus
- Slot 4 Menu 20: Ethernet/Ip
- Menu 21 Ethernet/Ip in Mappings
- Menu 22 Ethernet/Ip out Mappings
- Menu 23 Ethernet/Ip Fault Values
12 Technical Data
- Maximum Permissible Continuous Output Current
- Power Dissipation
- Line Reactors
- Motor Requirements
- Temperature, Humidity and Cooling Method
- IP / UL Rating
- Corrosive Gasses
- Acoustic Noise
- Overall Dimensions
- Input Current, Fuse and Cable Size Ratings
- AC Input Current and Fuse Ratings
- Maximum Motor Cable Lengths
- Minimum Resistances and Power Ratings for Braking Resistor
- Braking Resistor Resistance and Power Rating
- Drive Power Terminal Data
- Electromagnetic Compatibility (EMC)
- Immunity Compliance
- Size 3 Emission Compliance
- EMC Filter Ratings
- Overall EMC Filter Dimensions
- EMC Filter Torque Settings
- Status Modes (Keypad and LED Status)
- Trip Indications
- Identifying a Trip / Trip Source
- Analog Input 1/2 Current Loss
- Analog Output Calibration Failed
- Customization Table for an Application Module Has Changed
- Position Feedback Direction Incorrect
- Drive Encoder U Commutation Signal Fail
- Autotune Test Stopped before Completion
- Braking Resistor Overload Timed out
- Advanced Motion Controller CAM Failure
- NV Media Card Write Fail
- Menu 0 Parameter Modification Cannot be Saved to NV Media Card
- NV Media Card File/Data Is Different to the One in the Drive
- NV Media Card Data Structure Error
- NV Media Card Has the Read Only Bit Set
- NV Media Card Full
- NV Media Card Data Not Found
- Trip Initiated from the Control Word (06.042)
- Current Feedback Offset Error
- Drive Parameters Are Being Changed
- Power Stage Recognition: Unrecognized Drive Size
- Default Parameters Have Been Loaded
- Drive Position Feedback Interface Power Supply Overload
- Drive Encoder (Feedback) Wire Break
- Phase Offset Incorrect While Running
- Feedback Device Comms Failure
- Checksum or CRC Error
- Encoder Has Indicated an Error
- Initialization Failed
- Position Feedback Interface Has Timed out
- RFC-S Mode Phasing Failure Due to Incorrect Phase Angle
- Encoder Could Not be Identified During Auto-Configuration
- Data Read from the Encoder Is out of Range During Auto-Configuration
- An External Trip Is Initiated
- Out of Range of Frequency Has Been Detected in Regen Mode
- Data Processing Error: CPU Address Error
- Data Processing Error: Illegal Slot Instruction
- Data Processing Error: CPU Interrupt Crash
- Data Processing Error: Free Store Overflow
- Data Processing Error: Main Program Stack Overflow
- Data Processing Error: Internal Flash Memory Has Failed
- Data Processing Error: CPU Register Bank Error
- Data Processing Error: RTOS Error
- Data Processing Error: ASIC Is Not Compatible with the Hardware
- Inductance Measurement out of Range or Motor Saturation Not Detected
- The Regen Inductor Has Overloaded
- Digital Output Overload
- Island Condition Detected in Regen Mode
- The Load on the Drive Has Fallen below the Low Load Detection Level
- Output Current Overload Timed out
- Electronic Nameplate Transfer Has Failed
- Control Stage over Temperature
- DC Bus over Temperature
- Inverter over Temperature Based on Thermal Model
- Power Stage over Temperature
- Rectifier over Temperature
- Instantaneous Output over Current Detected
- Braking IGBT over Current Detected
- Power Module over Current Detected from IGBT
- Snubber Over-Current Detected
- Option Module Does Not Acknowledge During Drive Mode Changeover
- Output Phase Loss Detected
- Motor Speed Has Exceeded the over Speed Threshold
- Supply Phase Loss
- DC Bus Voltage Has Exceeded the Peak Level for 15 Seconds
- Communication Has Been Lost
- Power System Configuration Data Error
- Power down Save Error
- Internal Power Supply Fault
- 24V Internal Power Supply Overload
- Reserved Trips
- Measured Resistance Has Exceeded the Parameter Range
- Ethernet Interface in Slot 4 Has Changed
- Ethernet Interface in Slot 4 Has Detected a Fault
- Ethernet Interface in Slot 4 Hardware Fault
- Ethernet Interface in Slot 4 Has Been Removed
- Application Menu Customization Conflict Error
- Option Module in Option Slot X Has Changed
- Option Module X Hardware Fault
- Option Module in Option Slot X Has Been Removed
- Option Module Watchdog Function Service Error
- Hardware Trip Has Occurred During Last Power down
- RAM Allocation Error
- Internal Thermistor Has Failed
- Brake Resistor over Temperature
- Motor Thermistor Short Circuit
- Motor Thermistor Over-Temperature
- Drive Has Tripped and the Cause of the Trip Is Undefined
- User 24 V Supply Is Not Present on Control Terminals (1,2)
- On Board User Program Error
- User Save Error / Not Completed
- Supply Voltage out of Range Detected in Regen Mode
- User Generated Trip
- Trip Generated by an Onboard User Program
- Serial Communications Look up Table
- Internal / Hardware Trips
- Trip Categories
- Status Indications
- Displaying the Trip History
- Behaviour of the Drive When Tripped
Advertisement
Quick Links
- 1 Trip Indications
- 2 Diagnostics
- Download this manual
Related Manuals for Emerson Unidrive M702

Summary of Contents for Emerson Unidrive M702
- Page 1 User Guide Unidrive M702 Model sizes 3 to 8 Universal Variable Speed AC drive for induction and permanent magnet motors Part Number: 0478-0002-03 Issue: 3 www.controltechniques.com...
- Page 2 Original Instructions For the purposes of compliance with the EU Machinery Directive 2006/42/EC General information The manufacturer accepts no liability for any consequences resulting from inappropriate, negligent or incorrect installation or adjustment of the optional operating parameters of the equipment or from mismatching the variable speed drive with the motor.
- Page 3 How to use this guide This user guide provides complete information for installing and operating the drive from start to finish. The information is in logical order, taking the reader from receiving the drive through to fine tuning the performance. NOTE There are specific safety warnings throughout this guide, located in the relevant sections.
Page 4: Table Of Contents
Page 5: table of contents.
- Page 6 Limitation of voltage fluctuations and flicker in EN 61000-3-3:2008 low-voltage supply systems for equipment with rated current <16 A EN 61000-3-2:2006 Applicable where input current <16 A. No limits apply for professional equipment where input power >1 kW. Unidrive M702 User Guide Issue Number: 3...
- Page 7 Validation Adjustable speed electrical power drive EN 61800-3:2004 systems. EMC requirements and specific test methods Safety of machinery. Functional safety of EN 62061:2005 safety related electrical, electronic and programmable electronic control systems Unidrive M702 User Guide Issue Number: 3...
Page 8: Safety Information
Page 9: electrical installation, page 10: product information, page 11: ratings.
- Page 12 42.0 63.0 84.0 18.5 30.0 06400470 63.0 30.0 40.0 69.3 47.0 70.5 94.0 22.0 30.0 07400660 86.9 Frame size 7 07400770 103.4 115.5 07401000 123.2 08401340 170.5 Frame size 8 08401570 202.4 235.5 Unidrive M702 User Guide Issue Number: 3...
- Page 13 690 V 690 V 07600190 18.5 25.3 28.5 07600240 18.5 07600290 39.6 43.5 Frame size 7 07600380 50.6 07600440 57.2 07600540 80.3 08600630 94.6 94.5 Frame size 8 08600860 118.8 Unidrive M702 User Guide Issue Number: 3...
Page 14: Operating Modes
Page 15: compatible position feedback devices, page 16: drive features, page 17: nameplate description.
- Page 18 Table 2-9 Keypad identification Type Keypad Name Further Details LCD keypad option KI-Keypad Keypad with a LCD display Keypad LCD keypad option KI-Keypad RTC Keypad with a LCD display and real time clock Unidrive M702 User Guide Issue Number: 3...
Page 19: Items Supplied With The Drive
Page 20: mechanical installation, page 21: terminal cover removal.
- Page 22 Motor terminal cover Motor terminal cover terminal cover AC / DC terminal cover AC / DC terminal cover Motor / Braking terminal cover Control terminal Control terminal Motor / Braking cover cover terminal cover Unidrive M702 User Guide Issue Number: 3...
- Page 23 On size 4 drives, the Control / AC / Motor terminal cover must be removed before removal of the DC / Braking terminal cover. When replacing the terminal covers, the screws should be tightened to a maximum torque of 1 N m (0.7 lb ft). Unidrive M702 User Guide Issue Number: 3...
- Page 24 On size 5 drives, the Control terminal cover must be removed before removal of the DC / Braking terminal cover right. When replacing the terminal covers, the screws should be tightened to a maximum torque of 1 N m (0.7 lb ft). Figure 3-7 Removing the size 6 terminal covers Unidrive M702 User Guide Issue Number: 3...
- Page 25 NV Media Card Onboard Advanced Technical UL listing Optimization Diagnostics information information installation installation started parameters the motor Operation parameters data information Figure 3-8 Removing the size 7 and 8 terminal covers (size 7 shown) Unidrive M702 User Guide Issue Number: 3...
- Page 26 Place finger-guard on a flat solid surface and hit relevant break-outs with hammer as shown (1). Continue until all required break-outs are removed (2). Remove any flash / sharp edges once the break-outs are removed. Unidrive M702 User Guide Issue Number: 3...
Page 27: Installing / Removing Option Modules And Keypads
- Page 28 Press down on the tab (2C), tilt the option module towards you and remove. NOTE The large option module can only be inserted into slot 3. Additional standard option modules can still be installed and used in slot 2 and slot 1. Unidrive M702 User Guide Issue Number: 3...
- Page 29 To remove, reverse the installation instructions. NOTE The keypad can be installed / removed while the drive is powered up and running a motor, providing that the drive is not operating in keypad mode. Unidrive M702 User Guide Issue Number: 3...
Page 30: Dimensions And Mounting Methods
- Page 31 106 mm (4.17 in) 143 mm (5.63 in) (0.32 in) Æ 7.0 mm (0.28 in) NOTE The outer holes in the mounting bracket are to be used for surface mounting. See Table 3-2 for further information. Unidrive M702 User Guide Issue Number: 3...
- Page 32 The outer holes in the mounting bracket are to be used for surface mounting. See Table 3-2 for further information. Figure 3-19 Surface mounting the size 7 drive 25 mm (0.98 in) 220 mm (8.66 in) 10 mm (0.39 in) 279 mm (11.0 in) 270 mm (10.63 in) Æ 9mm (0.35 in) Unidrive M702 User Guide Issue Number: 3...
- Page 33 400 mm (14.37 in) (14.13 in) (15.75 in) 109 mm (4.29 in) Radius 1.0 mm (0.04 in) 38 mm 38 mm 67 mm (1.50 in) (1.50 in) (2.64 in) 76 mm (2.99 in) Unidrive M702 User Guide Issue Number: 3...
- Page 34 106 mm (4.17 in) 143 mm (5.63 in) 26 mm 26 mm (1.02 in) (1.02 in) Æ5.0 mm (0.20 in) (x 4 holes) Æ7.0 mm (0.28 in) (x 4 holes) 136 mm (5.35 in) Unidrive M702 User Guide Issue Number: 3...
- Page 35 330 mm (12.99 in) 92 mm (3.62 in) 310 mm (12.20 in) 270 mm (10.63 in) 252 mm (9.92 in) 187 mm (7.36 in) 245 mm (9.65 in) 220 mm (8.66 in) Æ 9mm (0.35 in) Unidrive M702 User Guide Issue Number: 3...
- Page 36 (3.94 in) Æ9 mm (0.35 in) 310 mm (12.21 in) 259 mm (10.20 in) 190 mm (7.48 in) (4 holes) 285 mm (11.22 in) Æ5.3 mm (0.21 in) (6 holes) 27 mm (1.06 in) Unidrive M702 User Guide Issue Number: 3...
- Page 37 Hole size: 9 mm (0.35 in) Hole size: 9 mm (0.35 in) Hole size: 9 mm (0.35 in) Hole size: 5.3 mm (0.21 in) Hole size: 9 mm (0.35 in) Hole size: 9 mm (0.35 in) Unidrive M702 User Guide Issue Number: 3...
Page 38: Enclosure For Standard Drives
- Page 39 Ratio of Where: is the air pressure at sea level is the air pressure at the installation Typically use a factor of 1.2 to 1.3, to allow also for pressure-drops in dirty air-filters. Unidrive M702 User Guide Issue Number: 3...
Page 40: Enclosure Design And Drive Ambient Temperature
- Page 41 4. Close the hinged baffle as shown (1). To remove the high IP insert, reverse the above instructions. The guidelines in Table 3-5 should be followed. Through panel securing bracket Through panel securing bracket Unidrive M702 User Guide Issue Number: 3...
- Page 42 A current derating must be applied to the drive if the high IP insert is installed. Derating information is provided in section 12.1.1 Power and current ratings (Derating for switching frequency and temperature) on page 227. Failure to do so may result in nuisance tripping. Unidrive M702 User Guide Issue Number: 3...
Page 43: Heatsink Mounted Brake Resistor
- Page 44 2 N m (1.5 Ib ft). 7. Replace the terminal covers on the drive, tighten to a maximum torque of 1 N m (0.7 lb ft). Unidrive M702 User Guide Issue Number: 3...
Page 45: External Emc Filter
- Page 46 (17.09 in) (8.27 in) (0.26 in) (0.26 in) (11.81 in) 4200-3690 Table 3-12 Size 7 external EMC filter dimensions CT part number Table 3-13 Size 8 external EMC filter dimensions CT part number Unidrive M702 User Guide Issue Number: 3...
Page 47: Electrical Terminals
Page 48: routine maintenance.
- Page 49 (1), push and turn anti-clockwise until the battery cover is released. 2. Replace the battery (the battery type is: CR2032). 3. Reverse point 1 above to replace battery cover. NOTE Ensure the battery is disposed of correctly. Unidrive M702 User Guide Issue Number: 3...
- Page 50 C: Depress and hold the locking release on the fan cable lead as shown (2). D: With the locking release depressed (2), take hold of the fan supply cable and carefully pull to separate the connectors. Unidrive M702 User Guide Issue Number: 3...
- Page 51 The resistor is designed to fail safely under fault conditions. from the socket, a means of automatically isolating the plug from the drive must be used (e.g. a latching relay). See Figure 4-6 for further information on ground connections. Unidrive M702 User Guide Issue Number: 3...
- Page 52 If the heatsink mounted resistor is used, an overload protection device is not required. The resistor is designed to fail safely under fault conditions. See Figure 4-7 for further information on ground connections. Unidrive M702 User Guide Issue Number: 3...
- Page 53 +DC -DC AC Connections Motor Connections Optional EMC filter Optional line reactor Fuses Output connections Motor Optional ground Mains connection Supply Supply Ground Thermal Optional overload braking protection resistor device Motor Optional ground connection Unidrive M702 User Guide Issue Number: 3...
- Page 54 M5 studs located near the plug-in power connector. Refer to Figure 4-7 for additional ground connection. Figure 4-7 Size 5 ground connections 1. Ground connection studs 1. Ground connection studs. 2. Additional ground connection. Unidrive M702 User Guide Issue Number: 3...
Page 55: Ac Supply Requirements
Page 56: supplying the drive with dc, page 57: dc bus paralleling, page 58: low voltage operation.
- Page 59 Maximum current current Class Class 03200050 10.4 15.8 03200066 12.6 20.9 or J 03200080 03200106 04200137 or J 04200185 05200250 or J 06200330 or J 06200440 07200610 07200750 or J 07200830 08201160 08201320 Unidrive M702 User Guide Issue Number: 3...
- Page 60 Maximum Maximum Fuse rating Typical continuous overload UL / USA input input input Model current Nominal Maximum Nominal Maximum current current Class Class 07600190 07600240 07600290 or J 07600380 07600440 07600540 08600630 08600860 Unidrive M702 User Guide Issue Number: 3...
- Page 61 04200185 05200250 06200330 06200440 07200610 07200750 07200830 08201160 2 x 70 2 x 70 2 x 1 2 x 1 08201320 2 x 70 2 x 70 2 x 1 2 x 1 Unidrive M702 User Guide Issue Number: 3...
- Page 62 Table 4-12 Cable ratings (690 V) Cable size (IEC) Cable size (UL) Model Input Output Input Output Nominal Maximum Nominal Maximum Nominal Maximum Nominal Maximum 07600190 07600240 07600290 07600380 07600440 07600540 08600630 08600860 Unidrive M702 User Guide Issue Number: 3...
Page 63: Output Circuit And Motor Protection
- Page 64 The maximum motor cable lengths specified in Section 4.9.1 Cable types and lengths is shielded and contains four cores. Typical capacitance for this type of cable is 130 pF/m (i.e. from one core to all others and the shield connected together). Unidrive M702 User Guide Issue Number: 3...
Page 65: Braking
- Page 66 * To keep the temperature of the resistor below 70 °C (158 °F) in a 30 °C (86 °F) ambient, the average power rating is 50 W for size 3, 100 W for size 4 and 5. The above parameter settings ensure this is the case. Unidrive M702 User Guide Issue Number: 3...
- Page 67 The thermal protection circuit must disconnect the AC supply from the 07400660 41.6 75.2 drive if the resistor becomes overloaded due to a fault. Figure 4-18 07400770 50.6 shows a typical circuit arrangement. 07401000 96.6 60.1 08401340 08401570 Unidrive M702 User Guide Issue Number: 3...
Page 68: Ground Leakage
- Page 69 Loosen the ground connection nuts and slide the grounding clamp down onto the pillars in the direction shown. Once in place, the ground connection nuts should be tightened with a maximum torque of 2 N m (1.47 lb ft). Unidrive M702 User Guide Issue Number: 3...
- Page 70 Loosen the ground connection nuts and slide the grounding bracket in the direction shown. Once in place, the ground connection nuts should be tightened with a maximum torque of 2 N m (1.47 lb ft). Unidrive M702 User Guide Issue Number: 3...
- Page 71 Torx internal EMC filter removal screw (3) to electrically disconnect the internal EMC filter. Figure 4-26 Removal of the size 6 internal EMC filter To electrically disconnect the Internal EMC filter, remove the screw as highlighted above (1). Unidrive M702 User Guide Issue Number: 3...
- Page 72 It must not be connected directly to the power earth busbar. Optional ground connection Unidrive M702 User Guide Issue Number: 3...
- Page 73 2. Additional measures to prevent unwanted emission of radio pair Cable frequency noise. These are optional and only required where the cable installation is subject to specific requirements for radio frequency emission control. Twisted pair shield Unidrive M702 User Guide Issue Number: 3...
- Page 74 For longer motor cables, an external filter is required. Where a filter is required, follow the guidelines in Section 4.12.5 Compliance with generic emission standards . Unidrive M702 User Guide Issue Number: 3...
- Page 75 Figure 4-36 Grounding the motor cable shield ≥300 mm (12 in) Sensitive signal cable Avoid placing sensitive signal circuits in a zone 300 mm (12 in) in the area immediately surrounding the power module.Ensure good EMC grounding. Unidrive M702 User Guide Issue Number: 3...
- Page 76 The input/output ports for the control circuits are designed for general use within machines and small systems without any special precautions. These circuits meet the requirements of EN 61000-6-2:2005 (1 kV surge) provided the 0 V connection is not grounded. Unidrive M702 User Guide Issue Number: 3...
Page 77: Communications Connections
Page 78: control connections.
- Page 79 0 V to +24 V Sample / Update period 2 ms (output will only change at the update rate of the source parameter 0 V common Common connection for all external Function devices Unidrive M702 User Guide Issue Number: 3...
Page 80: Position Feedback Connections
- Page 81 BiSS communication only encoders (not currently BiSS (6) supported) Table 4-27 shows the possible combinations of position feedback device types connected to the P1 and P2 position interfaces and the availability of the encoder simulation output. Unidrive M702 User Guide Issue Number: 3...
- Page 82 Greyed cells are for P2 position feedback connections or simulated encoder outputs. NOTE Freeze and Freeze\ on terminals 5 and 6 are for Freeze input 1. Freeze2 and Freeze2\ on terminals 11 and 12 are for Freeze input 2. Unidrive M702 User Guide Issue Number: 3...
- Page 83 NOTE The termination resistors are always enabled on the P2 position interface. Wire break detection is not available when using AB, FD or FR position feedback device types on the P2 position interface. Unidrive M702 User Guide Issue Number: 3...
- Page 84 Input voltage 0.6 Vrms Common to All Common to All Absolute maximum applied voltage relative to 0V -9 V to 14 V Absolute maximum applied voltage relative to 0V -9 V to 14 V Unidrive M702 User Guide Issue Number: 3...
- Page 85 ±4 V common mode voltage range EnDat (8), SSI (10), BiSS (13) Not used Resolver (14) Not used Common to All Absolute maximum applied voltage relative to 0V -9 V to 14 V Unidrive M702 User Guide Issue Number: 3...
Page 86: Safe Torque Off (Sto)
- Page 87 The drive does not provide any facility to over-ride the SAFE TORQUE OFF function, for example for maintenance purposes. Because of the risk of human error, the installation must not provide any facility to over- ride the function. Unidrive M702 User Guide Issue Number: 3...
Page 88: Getting Started
- Page 89 0. • If the left and right keypad buttons are pressed together, the least significant digit (furthest right) will be selected on the keypad display for editing. Unidrive M702 User Guide Issue Number: 3...
Page 90: Menu Structure
Page 91: menu.
- Page 92 Enabled modules. During this period ‘Uploading From Options’ is displayed synchronized to the supply Under The drive is in the under voltage state Disabled Voltage either in low voltage or high voltage mode. Unidrive M702 User Guide Issue Number: 3...
Page 93: Changing The Operating Mode
Page 94: displaying parameters with non-default values only.
- Page 95 DHCP server and written to IP Address (4.02.006). NOTE When using manual / static IP address configuration, ensure Subnet Mask (4.02.007) and Default Gateway (4.02.008) should also be set manually. 4.02.006 IP Address 000.000.000.000 to 192.168.001.100 255.255.255.255 Unidrive M702 User Guide Issue Number: 3...
Page 96: Basic Parameters
- Page 97 Number parameter Bit parameter Text string Binary parameter Filtered No default value Not copied Protected parameter Rating dependent User save Power-down save Destination IP address Mac address Date Date parameter Time Time parameter Unidrive M702 User Guide Issue Number: 3...
- Page 98 Keypad Ref Keypad reference Enable Forward / 00.028 Reverse Key Precision reference Input Read-write (RW) 00.XXX terminals parameter Read-only (RO) Output 00.XXX parameter terminals The parameters are all shown in their default settings Unidrive M702 User Guide Issue Number: 3...
- Page 99 00.010 Power stage Maximum Switching 00.041 Frequency Drive Encoder 00.011 Output Frequency 00.027 Overspeed 00.026 RFC-A Threshold Current RFC-S Magnitude 00.013 00.012 Torque Producing Current 15 way sub-D Magnetising Current connector Resistor optional Unidrive M702 User Guide Issue Number: 3...
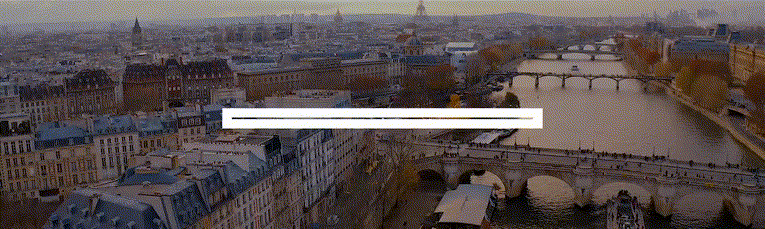
Page 100: Parameter Descriptions
- Page 101 ** These functions do not require a drive reset to become active. All other functions require a drive reset to initiate the function. To allow easy access to some commonly used functions, refer to the table overleaf. Equivalent values and strings are also provided in the table above. Unidrive M702 User Guide Issue Number: 3...
Page 102: Running The Motor
- Page 103 AC supply in the Open loop L1 L2 event of a fault. This is not required if the optional internal braking resistor is used RFC-A RFC-S Sensorless Sensorless RFC-A RFC-S Unidrive M702 User Guide Issue Number: 3...
- Page 104 AC supply in the Open loop L1 L2 event of a fault. This is not required if the optional internal braking resistor is used RFC-S RFC-A Sensorless Sensorless RFC-S RFC-A Unidrive M702 User Guide Issue Number: 3...
- Page 105 AC supply in the Open loop L1 L2 event of a fault. This is not required if the optional internal braking resistor is used RFC-S RFC-A Sensorless Sensorless RFC-S RFC-A Unidrive M702 User Guide Issue Number: 3...
- Page 106 This must be wired to interrupt the AC supply in the Open loop event of a fault. This is not required if the optional internal braking resistor is used RFC-A RFC-A Sensorless Sensorless RFC-S RFC-A Unidrive M702 User Guide Issue Number: 3...
Page 107: Quick Start Commissioning / Start-Up
- Page 108 Save parameters Select 'Save Parameters' in Pr mm.000 (alternatively enter a value of 1000 in Pr mm.000) and press red reset button or toggle the reset digital input. Drive is now ready to run Unidrive M702 User Guide Issue Number: 3...
- Page 109 Save parameters Select 'Save Parameters' in Pr MM.000 (alternatively enter a value of 1000 in Pr MM.000) and press red reset button or toggle the reset digital input. Drive is now ready to run Unidrive M702 User Guide Issue Number: 3...
- Page 110 The enable signal must be removed before the drive can be made to run at the required reference. The drive can be stopped at any time by removing the run signal or removing the drive enable. WARNING Unidrive M702 User Guide Issue Number: 3...
Page 111: Setting Up A Feedback Device
- Page 112 So for example, to enable the wire break error detection, set Pr 03.040 to 0001. * These settings should only be used in RFC-A mode. If used in RFC-S mode a phase offset test must be performed after every power up. Unidrive M702 User Guide Issue Number: 3...
- Page 113 A value of 1 ms to 2 ms may also be required in the Current Demand Filter (04.012) and it is also recommended that the speed loop gains are set to a low value to obtain stable operation. Unidrive M702 User Guide Issue Number: 3...
- Page 114 FD (2) for frequency and direction signals without commutation signals Device Type (03.138) FR (3) for forward and reverse signals without commutation signals Rotary Line Per Revolution (03.134) Set to the number of pulses per revolution of the encoder divided by 2 Unidrive M702 User Guide Issue Number: 3...
Page 115: Encoder Simulation Output Set-Up
- Page 116 Set to the required output pulse per revolution divided by 2. For example if 2000 pulses per revolution Revolution (03.092) is required, set this parameter to 1000. FD/Binary (1) for Frequency and Direction output signals Encoder Simulation Output Mode (03.098) FR/Binary (2) for Forward and Reverse output signals Unidrive M702 User Guide Issue Number: 3...
- Page 117 Set to the number bits in the whole position message. AB/Gray (0) for position data in Gray code format Encoder Simulation Output Mode (03.098) FD/Binary (1) or FR/Binary (2) for position data in binary format Unidrive M702 User Guide Issue Number: 3...
Page 118: Optimization
- Page 119 This mode is suitable for variable torque applications like fans and pumps where the load is proportional to the square of the speed of the motor shaft. This mode should not be used if a high starting torque is required. Unidrive M702 User Guide Issue Number: 3...
- Page 120 If too small a value is entered in Pr 00.045, the motor will run faster than the demanded frequency. The synchronous speeds for 50 Hz motors with different numbers of poles are as follows: 2 pole = 3000 rpm, 4 pole = 1500 rpm, 6pole =1000 rpm, 8 pole = 750 rpm Unidrive M702 User Guide Issue Number: 3...
- Page 121 The stator inductance can be measured by the drive by performing a rotating autotune (see Autotune (Pr 00.040), later in this table). Unidrive M702 User Guide Issue Number: 3...
- Page 122 In some applications where it is necessary for the reference frame used by the drive to dynamically follow the flux very closely (i.e. high speed Sensorless RFC-A induction motor applications) the integral gain may need to have a significantly higher value. Unidrive M702 User Guide Issue Number: 3...
- Page 123 4. Pr 03.017 = 3, Kp gains times 16 (03.017) If Speed Controller Set-up Method (03.017) = 3 the selected 5 Hz proportional gain used by the drive is multiplied by 16. Standard 25 Hz High 100 Hz Unidrive M702 User Guide Issue Number: 3...
- Page 124 Lq (05.069), Rated Load Offset (05.071) and Maximum Low Speed Sensorless Mode Current (05.072) are measured. To perform a Rotating autotune, set Pr 00.040 to 4, and provide the drive with both an enable signal ( and a run signal (on terminal 7 or 8). terminals 11 and 13) Unidrive M702 User Guide Issue Number: 3...
- Page 125 Increasing the differential term reduces the overshoot produced by under-damping, however, for most applications the proportional and integral gains alone are sufficient. Unidrive M702 User Guide Issue Number: 3...
- Page 126 4. Pr 03.017 = 3, Kp gains times 16 (03.017) If Speed Controller Set-up Method (03.017) = 3 the selected 5 Hz proportional gain used by the drive is multiplied by 16. Standard 25 Hz High 100 Hz Unidrive M702 User Guide Issue Number: 3...
Page 127: Maximum Motor Rated Current
Page 128: switching frequency, page 129: unidrive m702 user guide issue number, page 130: nv media card operation, page 131: transferring data, page 132: data block header information, page 133: nv media card trips, page 134: onboard plc, page 135: onboard plc parameters, page 136: advanced parameters.
- Page 137 Logic function 2 09.002 09.014 09.015 09.016 09.017 09.018 09.019 09.020 Low voltage supply 06.044 06.046 06.066 06.067 Marker pulse 03.032 03.031 Maximum speed 01.006 Menu 0 set-up 11.001 to 11.022 Menu 22 Unidrive M702 User Guide Issue Number: 3...
- Page 138 01.039 01.040 Voltage controller 05.031 Voltage mode 05.014 05.017 05.023 05.015 Voltage rating 11.033 05.009 05.005 Voltage supply 06.044 06.046 05.005 Warning 10.019 10.012 10.017 10.018 10.040 Zero speed indicator bit 03.005 10.003 Unidrive M702 User Guide Issue Number: 3...
- Page 139 VM_AMC_ROLL_OVER Range applied the position parameters in the advanced motion controller Units User units Range of [MIN] 0 or -2 Range of [MAX] 0 or -2 VM_AMC_ROLL_OVER[MAX] = 2 Definition VM_AMC_ROLL_OVER[MIN] = 2 Unidrive M702 User Guide Issue Number: 3...
- Page 140 VM_HIGH_DC_VOLTAGE[MAX] is the full scale DC link voltage feedback for the high DC link voltage measurement which can measure the voltage if it goes above the normal full scale value. This level is drive voltage rating dependent. Definition See Table 11-4 VM_HIGH_DC_VOLTAGE[MIN] = 0 Unidrive M702 User Guide Issue Number: 3...
- Page 141 Heavy duty), otherwise it is the lower of 0.9 x Pr 11.061 or 1.1 x Pr 11.060 (i.e. Normal duty). For VM_MOTOR2_CURRENT_LIMIT[MAX] use Pr 21.007 instead of Pr 05.007 and Pr 21.010 instead of Pr 05.010. Unidrive M702 User Guide Issue Number: 3...
- Page 142 VM_POWER[MAX] is rating dependent and is chosen to allow for the maximum power that can be output by the drive with maximum a.c. output voltage, at maximum controlled current and unity power factor. Definition VM_POWER[MAX] = √3 x VM_AC_VOLTAGE[MAX] x VM_DRIVE_CURRENT[MAX] / 1000 VM_POWER[MIN] = -VM_POWER[MAX] Unidrive M702 User Guide Issue Number: 3...
- Page 143 If Pr 01.008 = 1: VM_SPEED_FREQ_REF[MAX] = Pr 01.006 or |Pr 01.007|, whichever is larger. If the second motor map is selected (Pr 11.045 = 1) Pr 21.001 is used instead of Pr 01.006 and Pr 21.002 instead of Definition Pr 01.007. VM_SPEED_FREQ_REF[MIN] = -VM_SPEED_FREQ_REF[MAX]. Unidrive M702 User Guide Issue Number: 3...
- Page 144 Definition VM_SUPPLY_LOSS_LEVEL[MIN] is drive voltage rating dependent. See Table 11-4 VM_SWITCHING_FREQUENCY Range applied the switching frequency parameters Units Range of [MIN] Range of [MAX] VM_SWITCHING_FREQUENCY[MAX] = Power stage dependent Definition VM_SWITCHING_FREQUENCY[MIN] = 0 Unidrive M702 User Guide Issue Number: 3...
- Page 145 VM_USER_CURRENT_HIGH_RES[MIN] = -VM_USER_CURRENT_HIGH_RES[MAX] Table 11-4 Voltage ratings dependant values Voltage level (V) Variable min/max 200 V 400 V 575 V 690 V VM_DC_VOLTAGE_SET[MAX] 1150 VM_DC_VOLTAGE[MAX] 1190 VM_AC_VOLTAGE_SET[MAX] VM_AC_VOLTAGE[MAX] VM_STD_UNDER_VOLTS[MIN] VM_SUPPLY_LOSS_LEVEL[MIN] VM_HIGH_DC_VOLTAGE 1500 1500 1500 1500 Unidrive M702 User Guide Issue Number: 3...
Page 146: Menu 1: Frequency / Speed Reference
- Page 147 Skip freq./ Skip freq./ speed 1 speed 2 speed 3 Velocity feed-forward 01.005 01.030 01.032 01.034 [01.006] reference Skip freq./ Skip freq./ Skip freq./ reference speed band speed band speed band [01.006] [01.007] Unidrive M702 User Guide Issue Number: 3...
- Page 148 None (0), Forward (1), Reverse (2) None (0) RW Read / Write Read only Num Number parameter Bit parameter Text string Binary parameter Filtered No default value Not copied Protected parameter Rating dependent User save Power-down save Destination Unidrive M702 User Guide Issue Number: 3...
- Page 149 Safety Product Mechanical Electrical Getting Basic Running NV Media Card Onboard Advanced Technical UL listing Optimization Diagnostics information information installation installation started parameters the motor Operation parameters data information Unidrive M702 User Guide Issue Number: 3...
Page 150: Menu 2: Ramps
- Page 151 Open-loop Reference S-Ramp Enable 02.006 02.001 02.007 Maximum Rate Of Change 02.040 S-Ramp Percentage Motor And Load 03.018 S-Ramp Set-up Mode Inertia 02.041 02.038 d/dt Torque Per Amp 05.032 Inertia Compensation Torque Unidrive M702 User Guide Issue Number: 3...
- Page 152 0.000 RW Num RW Read / Write Read only Num Number parameter Bit parameter Text string Binary parameter Filtered No default value Not copied Protected parameter Rating dependent User save Power-down save Destination Unidrive M702 User Guide Issue Number: 3...
Page 153: Menu 3: Frequency Slaving, Speed Feedback And Speed Control
- Page 154 P2 Speed Feedback Motor Control Feedback 03.026 Select* d/dt 03.079 03.080 Position Feedback Sensorless 03.076 Initialized* Mode Filter Sensorless Position NOTE *Automatic change over if the relevant ‘bit’ of Position Feedback Initialized (03.076) is 0. Unidrive M702 User Guide Issue Number: 3...
- Page 155 Absolute At Speed 03.007 Select At Speed Above Set Speed Upper Limit Input Read-write (RW) mm.ppp terminals parameter Read-only (RO) Output mm.ppp parameter terminals The parameters are all shown in their default settings Unidrive M702 User Guide Issue Number: 3...
- Page 156 Reference P1 Reference ??.??? Scaling 03.043 P1 Maximum Reference 03.045 03.044 ??.??? Input Read-write (RW) mm.ppp terminals parameter Read-only (RO) Output mm.ppp parameter terminals The parameters are all shown in their default settings Unidrive M702 User Guide Issue Number: 3...
- Page 157 Reference P2 Reference ??.??? Scaling 03.143 P2 Maximum Reference 03.145 03.144 ??.??? Input Read-write (RW) mm.ppp terminals parameter Read-only (RO) Output mm.ppp parameter terminals The parameters are all shown in their default settings Unidrive M702 User Guide Issue Number: 3...
- Page 158 Digital input 4 Freeze Line Digital input 5 P1 Marker Input Read-write (RW) mm.ppp terminals parameter P2 Marker x(-1) Read-only (RO) mm.ppp Output parameter terminals Disabled The parameters are all shown in their default settings Unidrive M702 User Guide Issue Number: 3...
- Page 159 03.097 SSI Comms Bits Encoder Simulation Output Mode Encoder simulation out 03.098 Input Read-write (RW) mm.ppp terminals parameter Read-only (RO) Output mm.ppp parameter terminals The parameters are all shown in their default settings Unidrive M702 User Guide Issue Number: 3...
- Page 160 5V (0), 8V (1), 15V (2) 100K (0), 200K (1), 300K (2), 400K (3), 500K (4), 03.037 300K (2) Baud P1 Comms Baud Rate 1M (5), 1.5M (6), 2M (7), 4M (8) Baud Unidrive M702 User Guide Issue Number: 3...
- Page 161 Off (0) or On (1) Encoder Simulation Output Lines Per 03.092 1024 4096 1 to 16384 Revolution 03.093 65536 Encoder Simulation Numerator 1 to 65536 03.094 65536 Encoder Simulation Denominator 1 to 65536 Unidrive M702 User Guide Issue Number: 3...
- Page 162 P2 Feedback Reverse Off (0) or On (1) 03.157 P2 Normalization Turns 0 to 16 03.158 P2 Normalized Position -2147483648 to 2147483647 ND NC 03.159 P2 Normalized Marker Position --2147483648 to 2147483647 ND NC Unidrive M702 User Guide Issue Number: 3...
- Page 163 BiSS (6), EnDat Alt (7), SSI Alt (8), BiSS Alt (9) RW Read / Write Read only Num Number parameter Bit parameter Text string Binary parameter Filtered No default value Not copied Protected parameter Rating dependent User save Power-down save Destination Unidrive M702 User Guide Issue Number: 3...
Page 164: Menu 4: Torque And Current Control
- Page 165 Current Limit Braking Energy Motor Motor Current Read-only (RO) Load Indicator Active Overload Overload Overload Alarm Output mm.ppp parameter Indicator Indicator Accumulator Indicator terminals The parameters are all shown in their default settings Unidrive M702 User Guide Issue Number: 3...
- Page 166 Current Limit Braking Energy Motor Motor Current Read-only (RO) Load Active Overload Indicator Overload Overload Alarm Output mm.ppp parameter terminals Indicator Indicator Accumulator Indicator The parameters are all shown in their default settings Unidrive M702 User Guide Issue Number: 3...
- Page 167 0 to 100 % RW Read / Write Read only Num Number parameter Bit parameter Text string Binary parameter Filtered No default value Not copied Protected parameter Rating dependent User save Power-down save Destination Unidrive M702 User Guide Issue Number: 3...
Page 168: Menu 5: Motor Control
- Page 169 Safety Product Mechanical Electrical Getting Basic Running NV Media Card Onboard Advanced Technical UL listing Optimization Diagnostics information information installation installation started parameters the motor Operation parameters data information Unidrive M702 User Guide Issue Number: 3...
- Page 170 Low frequency Voltage Boost 05.015 High Dynamic Performance Enable 05.026 Voltage Controller Gain 05.031 Input Read-write (RW) mm.ppp terminals parameter Read-only (RO) Output mm.ppp parameter terminals The parameters are all shown in their default settings Unidrive M702 User Guide Issue Number: 3...
- Page 171 Output Flux Optimization 05.013 Select Power Motor Parameter 05.003 Power Calculation (V x 1) 05.016 Adaptive Control RFC-S Enable High Current 05.022 Speed Mode Torque Magnitude Producing Current 04.002 04.001 04.017 Magnetising Current Unidrive M702 User Guide Issue Number: 3...
- Page 172 -50 to 300 °C 0 °C 05.046 Stator Temperature -50 to 300 °C 05.047 Stator Temperature Coefficient 0.00000 to 0.10000 °C 0.00390 °C 05.048 Stator Base Temperature -50 to 300 °C 0 °C Unidrive M702 User Guide Issue Number: 3...
- Page 173 Torque ripple compensation phase 9 0.0 to 359 ° 0.0 ° 05.109 Torque ripple compensation magnitude 10 0.0 to 100 % 0.00 % 05.110 Torque ripple compensation phase 10 0.0 to 359 ° 0.0 ° Unidrive M702 User Guide Issue Number: 3...
Page 174: Menu 6: Sequencer And Clock
- Page 175 Rate Enable 06.071 06.070 User Supply Select 06.072 Under Voltage System Contactor Closed Input Read-write (RW) mm.ppp terminals parameter Read-only (RO) Output mm.ppp parameter terminals The parameters are all shown in their default settings Unidrive M702 User Guide Issue Number: 3...
- Page 176 0 to 100 % 06.053 Sleep / Wake Threshold ±VM_SPEED_FREQ_REF_UNIPOLAR 06.054 Sleep Time 0.0 to 250.0 s 10.0 s 06.055 Wake Time 0.0 to 250.0 s 10.0 s 06.056 Sleep Required Off (0) or On (1) Unidrive M702 User Guide Issue Number: 3...
- Page 177 Off (0) Threshold Select RW Read / Write Read only Num Number parameter Bit parameter Text string Binary parameter Filtered No default value Not copied Protected parameter Rating dependent User save Power-down save Destination Unidrive M702 User Guide Issue Number: 3...
Page 178: Menu 7: Temperature Monitoring
- Page 179 Safety Product Mechanical Electrical Getting Basic Running NV Media Card Onboard Advanced Technical UL listing Optimization Diagnostics information information installation installation started parameters the motor Operation parameters data information Unidrive M702 User Guide Issue Number: 3...
Page 180: Menu 8: Digital I/O
- Page 181 An Option Module with External Trip Generator Combine with I/O input (Menu 6) 06.029 safety functions can External Trip Mode open these switches Hardware Enable T13 STO Input 2 08.040 STO input 2 state Unidrive M702 User Guide Issue Number: 3...
- Page 182 08.052 08.062 unprotected bit parameter ??.??? Auxiliary Button 00.000 ??.??? x(-1) Toggle Input Read-write (RW) mm.ppp terminals parameter Read-only (RO) Output mm.ppp parameter terminals The parameters are all shown in their default settings Unidrive M702 User Guide Issue Number: 3...
- Page 183 0000000000000000 to 1111111111111111 0000000000000000 RW Read / Write Read only Num Number parameter Bit parameter Text string Binary parameter Filtered No default value Not copied Protected parameter Rating dependent User save Power-down save Destination Unidrive M702 User Guide Issue Number: 3...
Page 184: Menu 9: Programmable Logic Motorized Pot, Binary Sum And Timers
- Page 185 Function disabled if set to a non valid destination 09.031 Binary-Sum Input Logic Fours(MSB) Read-write (RW) mm.ppp terminals parameter Read-only (RO) mm.ppp Output parameter terminals The parameters are all shown in their default settings Unidrive M702 User Guide Issue Number: 3...
- Page 186 Timer disabled if set Timer 2 Repeat 09.049 to a non valid destination Function Input Read-write (RW) mm.ppp terminals parameter Read-only (RO) mm.ppp Output parameter terminals The parameters are all shown in their default settings Unidrive M702 User Guide Issue Number: 3...
- Page 187 Scope Trigger 09.059 Scope Trigger Source x(-1) 09.060 Scope Trigger Threshold 09.061 Input Read-write (RW) mm.ppp terminals parameter Read-only (RO) mm.ppp Output parameter terminals The parameters are all shown in their default settings Unidrive M702 User Guide Issue Number: 3...
- Page 188 Scope Trace 2 Source 0.000 to 59.999 0.000 09.057 Scope Trace 3 Source 0.000 to 59.999 0.000 09.058 Scope Trace 4 Source 0.000 to 59.999 0.000 09.059 Scope Trigger Off (0) or On (1) Off (0) Unidrive M702 User Guide Issue Number: 3...
- Page 189 Disabled (0), Active (1), Stopped (2), Failed (3) Disabled (0) RW Read / Write Read only Num Number parameter Bit parameter Text string Binary parameter Filtered No default value Not copied Protected parameter Rating dependent User save Power-down save Destination Unidrive M702 User Guide Issue Number: 3...
Page 190: Menu 10: Status And Trips
- Page 191 Drive size Pr 10.030 Pr 10.031 Pr 10.061 75 Ω Size 3 50 W 3.3 s Size 4 and 5 100 W 2.0 s 38 Ω All other ratings and frame sizes 0.000 0.00 Unidrive M702 User Guide Issue Number: 3...
Page 192: Menu 11: General Drive Set-Up
- Page 193 (2147483647) ND NC RW Read / Write Read only Num Number parameter Bit parameter Text string Binary parameter Filtered No default value Not copied Protected parameter Rating dependent User save Power-down save Destination Unidrive M702 User Guide Issue Number: 3...
Page 194: Menu 12: Threshold Detectors, Variable Selectors And Brake Control Function
- Page 195 ??.??? Source 2 Scaling 12.034 ??.??? Input Read-write (RW) Variable Selector 2 mm.ppp 12.029 terminals parameter Source 2 Read-only (RO) mm.ppp Output parameter terminals The parameters are all shown in their default settings Unidrive M702 User Guide Issue Number: 3...
- Page 196 Brake Control: Brake Apply Through reset Zero Threshold If the reset input is 1, the output is 0. If the reset input is 0, the output latches at 1 if the input is 1. Unidrive M702 User Guide Issue Number: 3...
- Page 197 5. Wait for zero frequency 01.011 Reference On 6. 1s delay as phase 2 of stopping sequence (Pr 06.001 =1,2 or 3) 12.040 Brake Control: Brake Release 02.003 Ramp Hold Pr 12.046 Pr 12.047 Unidrive M702 User Guide Issue Number: 3...
- Page 198 Brake Control Read-only (RO) Output mm.ppp Brake Apply parameter terminals Speed 12.045 The parameters are all shown in their default settings x(-1) 01.011 Reference Brake Control Brake Apply Zero Threshold 12.051 Unidrive M702 User Guide Issue Number: 3...
- Page 199 4. Wait for brake apply speed delay 5. Brake apply delay 01.011 Reference On 12.040 Brake Control: Brake Release 02.003 Ramp Hold 13.010 Position Control Mode 06.008 Hold Zero Speed Pr 12.047 Pr 12.046 Pr 12.048 Unidrive M702 User Guide Issue Number: 3...
- Page 200 If the reset input is 1, the output is 0. If the reset input is 0, the output latches at 1 if the input is 1. The parameters are all shown in their default settings Unidrive M702 User Guide Issue Number: 3...
- Page 201 Off (0) or On (1) Off (0) RW Read / Write Read only Num Number parameter Bit parameter Text string Binary parameter Filtered No default value Not copied Protected parameter Rating dependent User save Power-down save Destination Unidrive M702 User Guide Issue Number: 3...
Page 202: Menu 13: Standard Motion Controller
- Page 203 3. The absolute mode parameter (Pr 13.011) is changed. The position controller is disabled transiently to reset the error integrator. 4. One of the position sources is invalid. 5. The position feedback initialized parameter (Pr 03.048) is zero. Unidrive M702 User Guide Issue Number: 3...
- Page 204 4 ms (0), 250 us (1), Not Selected (2) RW Read / Write Read only Num Number parameter Bit parameter Text string Binary parameter Filtered No default value Not copied Protected parameter Rating dependent User save Power-down save Destination Unidrive M702 User Guide Issue Number: 3...
- Page 205 Safety Product Mechanical Electrical Getting Basic Running NV Media Card Onboard Advanced Technical UL listing Optimization Diagnostics information information installation installation started parameters the motor Operation parameters data information Unidrive M702 User Guide Issue Number: 3...
Page 206: Menu 14: User Pid Controller
- Page 207 ??.??? Scaling PID Integral Gain 14.001 14.015 14.012 ??.??? PID Derivative Gain Input Read-write (RW) mm.ppp terminals parameter Read-only (RO) Output mm.ppp parameter terminals The parameters are all shown in their default settings Unidrive M702 User Guide Issue Number: 3...
- Page 208 PID2 Digital Reference ±100.00 % 0.00 % 14.056 PID2 Digital Feedback ±100.00 % 0.00 % 14.057 PID2 Enable Source 2 0.000 to 59.999 0.000 14.058 PID1 Feedback Output Scaling 0.000 to 4.000 1.000 Unidrive M702 User Guide Issue Number: 3...
- Page 209 Off (0) or On (1) Off (0) RW Read / Write Read only Num Number parameter Bit parameter Text string Binary parameter Filtered No default value Not copied Protected parameter Rating dependent User save Power-down save Destination Unidrive M702 User Guide Issue Number: 3...
Page 210: Menus 15, 16 And 17: Option Module Set-Up
Page 211: menu 18: application menu 1, page 212: menu 19: application menu 2, page 213: menu 20: application menu 3, page 214: menu 21: second motor parameters.
- Page 215 0.0 to 359 ° 0.0 ° RW Read / Write Read only Num Number parameter Bit parameter Text string Binary parameter Filtered No default value Not copied Protected parameter Rating dependent User save Power-down save Destination Unidrive M702 User Guide Issue Number: 3...
Page 216: Menu 22: Additional Menu 0 Set-Up
Page 217: menu 24: ethernet status and monitoring.
- Page 218 Text string Binary parameter Filtered No default value Not copied Protected parameter Rating dependent User save Power-down save Destination IP address Mac address Date Date parameter Time Time parameter Slot,menu,parameter Character parameter Version number Unidrive M702 User Guide Issue Number: 3...
- Page 219 Text string Binary parameter Filtered No default value Not copied Protected parameter Rating dependent User save Power-down save Destination IP address Mac address Date Date parameter Time Time parameter Slot,menu,parameter Character parameter Version number Unidrive M702 User Guide Issue Number: 3...
- Page 220 Too many links (-2), Out of memory (-1), OK (0) 4.10.050 Rx2 Link Profile 0 to 0 4.10.051 Rx2 Link Number 0 to 255 4.10.052 Rx2 Destination Parameter 0 to 4.99.999 0.00.000 4.10.053 Rx2 Parameter Count 0 to 32 Unidrive M702 User Guide Issue Number: 3...
- Page 221 Text string Binary parameter Filtered No default value Not copied Protected parameter Rating dependent User save Power-down save Destination IP address Mac address Date Date parameter Time Time parameter Slot,menu,parameter Character parameter Version number Unidrive M702 User Guide Issue Number: 3...
- Page 222 Text string Binary parameter Filtered No default value Not copied Protected parameter Rating dependent User save Power-down save Destination IP address Mac address Date Date parameter Time Time parameter Slot,menu,parameter Character parameter Version number Unidrive M702 User Guide Issue Number: 3...
- Page 223 Text string Binary parameter Filtered No default value Not copied Protected parameter Rating dependent User save Power-down save Destination IP address Mac address Date Date parameter Time Time parameter Slot,menu,parameter Character parameter Version number Unidrive M702 User Guide Issue Number: 3...
- Page 224 7-SCI (2) 10-Trap PM BL (4) Read / Write Read only Number parameter Bit parameter Text string Binary parameter Filtered No default value Not copied Protected parameter Rating dependent User save Power-down save Destination Unidrive M702 User Guide Issue Number: 3...
- Page 225 Output Mapping Parameter 20 0.00.000 to 4.99.999 0.00.000 Read / Write Read only Number parameter Bit parameter Text string Binary parameter Filtered No default value Not copied Protected parameter Rating dependent User save Power-down save Destination Unidrive M702 User Guide Issue Number: 3...
- Page 226 Output Fault Value 20 -2147483648 to 2147483647 Read / Write Read only Number parameter Bit parameter Text string Binary parameter Filtered No default value Not copied Protected parameter Rating dependent User save Power-down save Destination Unidrive M702 User Guide Issue Number: 3...
Page 227: Technical Data
- Page 228 23.8 20.0 15.6 06500350 30.0 40.0 43.0 39.6 31.3 26.2 20.5 22.0 30.0 35.0 34.0 29.8 23.8 20.0 15.6 07500440 07500550 08500630 08500860 690 V 07600190 07600240 07600290 07600380 07600440 07600540 08600630 08600860 Unidrive M702 User Guide Issue Number: 3...
- Page 229 04400172 05400270 17.1 15.6 14.4 12.6 11.4 17.2 15.6 14.5 12.6 11.3 05400300 19.8 19.5 18.9 17.6 16.4 13.9 11.7 19.8 19.5 18.9 17.7 16.2 13.8 11.7 575 V 05500030 05500040 05500069 10.0 Unidrive M702 User Guide Issue Number: 3...
- Page 230 06500230 27.0 23.5 18.3 23.0 21.6 19.0 14.1 06500290 34.0 28.2 23.5 18.3 29.0 27.3 21.8 19.0 14.1 06500350 43.0 41.7 36.1 28.2 23.7 18.3 35.0 31.2 27.3 21.8 19.0 14.1 07500440 07500550 Unidrive M702 User Guide Issue Number: 3...
- Page 231 Heavy Duty Maximum permissible continuous output current (A) Maximum permissible continuous output current (A) Model for the following switching frequencies for the following switching frequencies 690 V 07600190 07600240 07600290 07600380 07600440 07600540 Unidrive M702 User Guide Issue Number: 3...
- Page 232 03200066 03200080 03200106 04200137 04200185 06200330 06200440 400 V 03400025 0.75 03400031 03400045 03400062 03400078 03400100 04400150 04400172 06400350 18.5 06400420 18.5 06400470 575 V 06500100 06500150 06500190 06500230 18.5 06500290 18.5 06500350 Unidrive M702 User Guide Issue Number: 3...
- Page 233 200 V 03200050 03200066 03200080 03200106 04200137 04200185 05200250 400 V 03400025 03400031 03400045 03400062 03400078 03400100 04400150 04400172 05400270 05400300 575 V 05500030 05500040 05500069 Unidrive M702 User Guide Issue Number: 3...
- Page 234 Maximum supply imbalance: 2 % negative phase sequence (equivalent to 3 % voltage imbalance between phases). Frequency range: 45 to 66 Hz For UL compliance only, the maximum supply symmetrical fault current must be limited to 100 kA Unidrive M702 User Guide Issue Number: 3...
- Page 235 The DC bus capacitors have a storage period of 10 years. The low voltage capacitors on the control supplies typically have a storage period of 2 years and are thus the limiting factor. Unidrive M702 User Guide Issue Number: 3...
- Page 236 100 ppm (0.01 %) of the reference, when a preset speed is used. If an analog input is used the absolute accuracy is further limited by the absolute accuracy of the analog input. Unidrive M702 User Guide Issue Number: 3...
- Page 237 The values of maximum input current are stated for a supply with a 2 % negative phase-sequence imbalance and rated at the maximum supply fault current given in Table 12-13. Table 12-13 Supply fault current used to calculate maximum input currents Model Symmetrical fault level (kA) Unidrive M702 User Guide Issue Number: 3...
- Page 238 Maximum current current Class Class 03400025 03400031 03400045 or J 03400062 03400078 03400100 04400150 or J 04400172 05400270 or J 05400300 06400350 06400420 or DFJ 06400470 07400660 07400770 or J 07401000 08401340 08401570 Unidrive M702 User Guide Issue Number: 3...
- Page 239 Maximum Maximum Fuse rating Typical continuous overload UL / USA input input input Model current Nominal Maximum Nominal Maximum current current Class Class 07600190 07600240 07600290 or J 07600380 07600440 07600540 08600630 08600860 Unidrive M702 User Guide Issue Number: 3...
- Page 240 2 x 50 2 x 1 2 x 1 2 x 70 2 x 70 2 x 1/0 2 x 1/0 08401570 2 x 70 2 x 70 2 x 1/0 2 x 1/0 Unidrive M702 User Guide Issue Number: 3...
- Page 241 185 m 125 m 07200750 250 m (820 ft) (607 ft) (410 ft) (295 ft) 07200830 08201160 90 m 185 m 125 m 250 m (820 ft) (607 ft) (410 ft) (295 ft) 08201320 Unidrive M702 User Guide Issue Number: 3...
- Page 242 125 m 90 m (820 ft) (607 ft) (410 ft) (295 ft) 07600380 07600440 07600540 08600630 250 m 185 m 125 m 90 m (820 ft) (607 ft) (410 ft) (295 ft) 08600860 Unidrive M702 User Guide Issue Number: 3...
- Page 243 6 way AC power connector 6 mm (10 AWG) 3 way AC power connector 8 mm (8 AWG) 3 way motor connector 2 way low voltage power 1.5 mm (16 AWG) 24 V supply connector Unidrive M702 User Guide Issue Number: 3...
- Page 244 Note that category 4 is more restrictive than E2R, since the rated current of the PDS must exceed 400 A or the supply voltage exceed 1000 V, for 10 - 20 the complete PDS. Using external filter: 0 – 20 20 - 100 Unidrive M702 User Guide Issue Number: 3...
Page 245: Optional External Emc Filters
- Page 246 Table 12-40 Optional external EMC Filter terminal data Power connections Ground connections CT part Max cable size Max torque Max torque number Ground stud size Ib ft Ib ft 4200-3230 0.59 4200-3480 4200-2300 4200-4800 1.70 4200-3690 Unidrive M702 User Guide Issue Number: 3...
Page 247: Diagnostics
Page 248: identifying a trip / trip source, page 249: trips, sub-trip numbers.
- Page 250 If an external thermal protection device is being used and the braking resistor software overload protection is not required, set Pr 10.030, Pr 10.031 or Pr 10.061 to 0 to disable the trip. Unidrive M702 User Guide Issue Number: 3...
- Page 251 Ensure the destination drive supports the drive operating mode in the parameter file. • Clear the value in Pr mm.000 and reset the drive • Ensure destination drive operating mode is the same as the source parameter file Unidrive M702 User Guide Issue Number: 3...
- Page 252 Recommended actions: • Clear the read only flag by setting Pr mm.000 to 9777 and reset the drive. This will clear the read-only flag for all data blocks in the NV Media Card Unidrive M702 User Guide Issue Number: 3...
- Page 253 The Drive Size trip indicates that the control PCB has not recognized the drive size of the power circuit to which it is connected. Recommended action: • Ensure the drive is programmed to the latest firmware version • Hardware fault - return drive to supplier Unidrive M702 User Guide Issue Number: 3...
- Page 254 If wire break detection on the drive encoder input is not required, set Pr 03.040 = XXX0 to disable the Encoder 2 trip • Check cable continuity • Check wiring of feedback signals is correct • Check encoder power supply is set correctly (Pr 03.036) • Replace encoder Unidrive M702 User Guide Issue Number: 3...
- Page 255 Drive position feedback interface 1 Drive position feedback interface 2 Recommended actions: • For SSI encoders, check the wiring and encoder power supply setting (Pr 03.036) • Replace the encoder / contact the supplier of the encoder Unidrive M702 User Guide Issue Number: 3...
- Page 256 The Encoder 12 trip indicates that the drive is communicating with the encoder but the encoder type is not recognized. Sub-trip Reason Drive position feedback interface 1 Drive position feedback interface 2 Recommended actions: • Enter the encoder setup parameters manually • Check to see the encoder supports auto-configuration Unidrive M702 User Guide Issue Number: 3...
- Page 257 The HF03 trip indicates that an illegal instruction has occurred. This trip indicates that the control PCB on the drive has failed. Recommended actions: • Hardware fault – Contact the supplier of the drive Unidrive M702 User Guide Issue Number: 3...
- Page 258 The HF13 trip indicates that the drive firmware is not compatible with the hardware. This trip indicates that the control PCB on the drive has failed. Recommended actions: • Re-program the drive with the latest version of the drive firmware for Unidrive M702 • Hardware fault – Contact the supplier of the drive Unidrive M702 User Guide...
- Page 259 The HF20 trip indicates that the ASIC version is not compatible with the drive firmware. The ASIC version can be identified from the sub-trip number. Recommended actions: • Hardware fault - Contact the supplier of the drive Unidrive M702 User Guide Issue Number: 3...
- Page 260 Synchronization to the power supply has been lost The Line Sync trip indicates that the inverter has lost the synchronization with the AC supply in Regen mode. Recommended actions: • Check the supply / supply connections to the regen drive Unidrive M702 User Guide Issue Number: 3...
- Page 261 • Check enclosure / drive fans are still functioning correctly • Check enclosure ventilation paths • Check enclosure door filters • Increase ventilation • Reduce the drive switching frequency • Check ambient temperature Unidrive M702 User Guide Issue Number: 3...
- Page 262 Decrease acceleration / deceleration rates • Reduce motor load • Check the derating tables and confirm the drive is correctly sized for the application. • Use a drive with larger current / power rating Unidrive M702 User Guide Issue Number: 3...
- Page 263 The OI dc trip indicates that the short circuit protection for the drive output stage has been activated. Recommended actions: • Disconnect the motor cable at the drive end and check the motor and cable insulation with an insulation tester • Replace the drive Unidrive M702 User Guide Issue Number: 3...
- Page 264 Recommended actions: • Reduce the Speed Controller Proportional Gain (03.010) to reduce the speed overshoot (RFC-A, RFC-S modes only) • If an SSI encoder is being used set Pr 03.047 to 1 Unidrive M702 User Guide Issue Number: 3...
- Page 265 Check the DC bus ripple level with an isolated oscilloscope • Check the output current stability • Reduce the duty cycle • Reduce the motor load • Disable the phase loss detection, set Pr 06.047 to 2. Unidrive M702 User Guide Issue Number: 3...
- Page 266 Recommended actions: • Remove any option modules and perform a reset • Remove encoder connection and perform a reset • Hardware fault within the drive – return the drive to the supplier Unidrive M702 User Guide Issue Number: 3...
- Page 267 To confirm that the parameter changes detected is acceptable, reset the trip and perform a parameter save to ensure that the trip doesn't occur the next time the drive is powered up. • If the trip persists - Contact the supplier of the drive. Unidrive M702 User Guide Issue Number: 3...
- Page 268 Identify the reason for the trip from the trip string or from sub-trip number and resolve the error. • Reset the trip, If the trip persists, Hardware fault - Contact the supplier of the drive. Unidrive M702 User Guide Issue Number: 3...
- Page 269 The SlotX Error trip indicates that the option module in option slot X on the drive has detected an error. The reason for the error can be identified by the sub-trip number. Recommended actions: • See relevant Option Module User Guide for details of the trip Unidrive M702 User Guide Issue Number: 3...
- Page 270 The Stored HF trip indicates that a hardware trip (HF01 –HF17) has occurred and the drive has been power cycled. The sub-trip number identifies the HF trip i.e. stored HF.17. Recommended actions: • Enter 1299 in Pr mm.000 and press reset to clear the trip Unidrive M702 User Guide Issue Number: 3...
- Page 271 Analog Input 3 Mode (07.015) = 7 and the resistance of the thermistor connected to analog input 3 is less than 50 Ω. Recommended actions: • Check thermistor continuity • Replace motor / motor thermistor Unidrive M702 User Guide Issue Number: 3...
- Page 272 1 and no user 24 V supply is present on control terminals 1 and 2. Recommended actions: • Ensure the user 24 V supply is present on control terminals 1 (0 V) and 2 (24 V) Unidrive M702 User Guide Issue Number: 3...
- Page 273 As 30 installed in slot 4 not present Image is not compatible with the control board Initiated from within the image code Image is not compatible with the control board As 80 serial number Unidrive M702 User Guide Issue Number: 3...
- Page 274 Set Maximum Voltage (03.027) to zero to disable the trip. Watchdog Control word watchdog has timed out The Watchdog trip indicates that the control word has been enabled and has timed out Recommended actions: Unidrive M702 User Guide Issue Number: 3...
- Page 275 Encoder 4 Slot4 Not installed Low Load Encoder 5 Slot4 Different Line Sync Encoder 6 Reset Logs 40 -89 User Trip 40 - 89 Encoder 7 Power Comms Encoder 8 User 24V Encoder 9 Unidrive M702 User Guide Issue Number: 3...
Page 276: Internal / Hardware Trips
Page 277: alarm indications, page 278: behaviour of the drive when tripped.
- Page 279 • Metal conduit entry plate • KI-Keypad Advanced • Type 12 sealing kit • SI-PROFIBUS • SD card kit • SI-DeviceNet • UL Type 1 kit • SI-CANopen • SI-Applications Plus • SI-Register Unidrive M702 User Guide Issue Number: 3...
- Page 280 Keypad and display - Installing / removing ....... 28 Digital Input 2 ................79 Keypad operation ..............88 Dimensions (overall) .............236 Display ..................88 Display messages ..............92 Line reactors ..............56 Drive enable ................80 Drive features ................15 Unidrive M702 User Guide www.controltechniques.com Issue Number: 3...
- Page 281 Operating mode (changing) ........... 93 Surge suppression for digital and unipolar inputs and outputs 77 Operating modes ..............14 Switching frequency ............. 128 Optimization ................118 Option Module ...............210 Options ..................17 Output contactor ..............65 Output frequency ..............236 Unidrive M702 User Guide Issue Number: 3...
- Page 282 Through-panel mounting the drive ..........33 Torque settings .............. 48 Trip ..................247 Trip History ................277 Trip Indications ..............247 UL Listing Information ............279 User Security ................94 Ventilation ................38 Vibration ................236 Voltage mode ............... 119 Warnings ...................8 Weights .................237 Unidrive M702 User Guide www.controltechniques.com Issue Number: 3...
- Page 284 0478-0002-03...
Rename the bookmark
Delete bookmark, delete from my manuals, upload manual.

- Motion Made Easy®
- Packaged Pump Solutions
- Elevator Solutions
- Servo Drives
- Servo Motors
- Integration Products
- Functional Safety
- Options and Accessories
- Application Solutions
Service and Support
- Customer Portal
- Industrial Distributor Login
- Technical Support
- Technical Documentation
- Application Support
- Replacement and Spare Parts
- Field Service
- Warranty Repairs & RMAs
- 5 Year Warranty Registration
- Extended Warranties
- Upgrade Assistance
- Terms and Conditions
- Where to Buy
- Artificial Lift
- Food and Beverage
- Cranes and Hoists
- Entertainment
- Forestry and Wood Working
- Lift and Elevators
- Material Handling
- Mining Cement and Aggregate
- Packaging Machinery
- OEM Machine Manufacturing
- Port and Freight Terminal Machinery
- Renewable Energy Research and Development
- Rubber and Plastics
- Test Stands
- Water and Wastewater
- Wire and Cable
News and Media
- In The News
- Drive Obsessed for 50 Years
- Drive Basics - FAQs
- Join the Team
- System Integrators
- Subscribe to Newsletter
- Environment
- Case Studies
- Engineering Guides
- Manuals and Software
- Application Notes
- Motor DDF Files
- Technical Notes
- Mobile Applications
- Software Registration
- About Nidec Corp
- English - Global
- English - USA
- German - Germany
- German - Switzerland
- Français
- Italian - Italy
- Spanish - Spain
- Turkish - Turkey
- Polish - Poland
- Czech - Czech Republic
- Share This Page:
- Troubleshooting Guides
- Warranty, Repairs & RMA Requests
- Extended Product Warranty
- Replacement and spare parts
- Site Power Audits
There are a number of Troubleshooting Guides that have been created by the Nidec Industrial Automation USA Technical Support team. These Troubleshooting Guides are intended for use by Qualified Electronic Technicians versed in Motor Drives and Industrial Power devices . The procedures outlined in these guides expect that the Technician understands the hazards of working with High Voltage 3 phase power devices and has basic troubleshooting skills and a working knowledge of troubleshooting equipment.
By clicking on the button below you confirm that you have read, understand and acknowledge the hazards and warning statements posted above. Only then will you have access to the Troubleshooting Guides.
- Request Information
- Motion Made Easy®
- Warranty Repairs & RMAs
- Terms of Use
- Privacy Notice
- Cookie Policy
13 diagnostics, 1 errors and error codes – Emerson P/N 400361-00 User Manual
- Original mode

Diagnostics www.emersonct.com 117
13 Diagnostics
There are many different tools available to the user to help diagnose problems or errors in the Unidrive SP and SM-EZMotion module. The most common tools used are the Error Codes, Analog Outputs, and PowerTools Pro utilities such as the Watch Window, Fault View, Status Bar, and Online View Tabs. Any or all of these can be used to figure out why an application may not be running properly.
The following section gives detailed information about each of the tools listed above.
13.1 Errors and Error Codes
The Unidrive SP and SM-EZMotion module fault handling system is made of a series of Trips, Trip Codes, Errors, and Error Codes. Following is a definition of each.
A Trip is an action that happens in the Unidrive SP that causes the drive bridge to be inhibited therefore stopping all motion. When the drive inhibits, the drive does not have control of the motor/load.
An Error is an action that happens in the SM-EZMotion module or Unidrive SP that may or may not cause the
Unidrive SP to Trip. Most of the Errors that occur in the SM-EZMotion module will cause a Trip on the drive.
Following is a description of the Errors Handling System used by the SM-EZMotion module
When the SM-EZMotion module has an error (i.e. Program - Divide By Zero Error), it sends a signal to the Unidrive SP that the error occurred. The SP then recognizes the error in the module by causing the drive to trip. The specific trip that will be displayed on the SP depends on the slot number that the SM-EZMotion module is located in. The drive trip will be a Sl#.Er trip where # indicates the slot # that module error occurred in.
The Unidrive SP Trip Log will be updated with the Sl#.Er trip. To find out what the specific error in the module was, the user needs to query parameter MM.50 where MM is 15, 16, or 17 depending on the slot # of the module. Parameter MM.50 stores the error code for the specific error that occurred.
Following is a list of the Errors that can occur in the SM-EZMotion module along with Error Codes, reset methods, and potential causes for each fault.
Possible Reason
Possible Solution
SP Parameter Access Error -
Parameter Doesn't Exist
The SP Menu Parameter that you are trying to read from or write to does not exist.
Please double check the parameter number
Parameter is Read Only
The SP Menu Parameter that you are trying to write to is a Read Only parameter
Avoid writing to Read Only parameters. Use Drive Menu Watch view in PowerTools Pro, or Unidrive SP User Guide to verify parameter accessibility
Parameter is Write Only
The SP Menu Parameter that you are trying to read from is Write Only
Avoid reading from Write Only parameters. Use Drive Menu Watch view in PowerTools Pro, or Unidrive SP User Guide to verify parameter accessibility
SP Parameter Access Error - Written
Value Out of Range
The value you are trying to write to the SP Menu Parameter is out of range.
Modify value that you are trying to write so that it is within valid range of the parameter. Use the Unidrive SP User Guide to verify the range of the parameter and try again
SP Database Setup Error
Module Overheat Error
SM-EZMotion module temperature has exceeded 83 degrees Farenheit
Select lower switching frequency in PowerTools Pro configuration, or reduce motion performance (i.e. lower accel/ decel, lengthen dwells). If problem persists, please contact factory
Invalid Configuration Error
NVM Invalid Error
Power Up Test Failure Error
SM-EZMotion module Power Up Test failed
Cycle power to the system. If problem persists, please contact factory
- Canon - AE-1
- Fitbit - Flex
- Nikon - D5000
- Nikon - D40
- Nikon - D3100
- Nikon - D90
- Nikon - D7000
- Nikon - D80
- Nikon - D3000
- HP - Officejet Pro 8600
- Canon - EOS 60D
- HP - 12C Financial calculator

Opening Times
Commander sk diagnostic status error and trip codes.
Understanding trip codes is an important part of keeping your equipment running smoothly. Below are some of the more common codes you may come across:
* The Enable/Reset terminal will not reset an O.Ld1 trip. Use the Stop/Reset key
**These trips cannot be reset for 10 seconds after they occur
If you have an AC / DC drive module breakdown or stability issue our engineers are able to analyse the whole machine to identify where the control issues lie. Our extensive experience in retrofit and new projects means we have the knowledge to look deep into the control system where we commonly find the peripheral devices are faulty rather than the drive module.
Telephone support
Where appropriate we are often able to offer technical support by phone, we will need the following information from you:
- Your official Purchase order (this must be received prior to any support).
- Details of the Drive.
- Error Codes.
- We may also need copies of drawings and software to aid diagnosis.
Telephone support rates are £100.00 per hour, with a minimum charge of 1 hour.
Our team of engineers are also able to offer on site service and breakdown support throughout the UK to get you up and running again quickly, please enquire for details.

If you have a faulty drive but don't require on site support, Drives and Automation are able to repair them. Trained engineers will strip down your drive, assess what is required and we will then send you a repair quotation. If you are happy to proceed they will repair the drive, clean it and load test it before returning it to you. Fast turnarounds are usually no problem!
Get your faulty Commander SK repaired
The Commander SK is now a superceded product and is in it's maintenance period. Volume production of these products has now ceased, but manufacturer contractual obligations regarding warranty, service and repairs will continue. The maintenance period is expected to last up to ten years subject to raw material and component availability and will end in 2027 when no further manufacturer support will be available. Drives and Automation are able to supply refurbished units for certain models, simply contact us with details of your existing Commander SK and we will see if we can offer you a replacement.
Call us now on 0845 3704660 to enquire about a refurbished Commander SK
In 2013, the Unidrive SP and Commander SK were replaced by a new range of industrial AC drives called Unidrive M. Unidrive M’s design is based on the success and popularity of Unidrive SP and Commander SK, and incorporates market-leading technologies. If you are wanting to upgrade your obsolete Commander SK to an M Series Drive, use our quick reference guide to choose the right replacement Drive for your application:
Upgrade to Unidrive M from Commander SK
- Commander SK Trip and Status Diagnostic Codes
- Unidrive SP Error and Trip codes
- Unidrive M200 – Diagnostic Status Trip and Error Codes
- Unidrive M700 – Diagnostic Status Trip and Error Codes
- What is a soft starter?
Got a problem with your Commander SK Drive?
Call us now on 0845 3704660 to book an on site support visit from one of our trained engineers.
(Standard Service Rates apply).
404 Not found
404 Not found
Introduction
Trip 2 a non-emergency medical transportation solution dedicated to optimizing patient care and service. Getting patients to their appointments quickly and safely is our highest priority. The Trip 2 software integrates over 30 years of field experience with the latest in cutting edge technology. Finding faster, efficient solutions for transportation dispatching, distribution and management. Trip 2 maximized client experiences and provider satisfaction.
Trip2 Web App Documentation
404 Not found
404 Not found
Emerson 0471-0128-02 9.4 Drive trip display codes, 9.5 SM-EtherCAT module temperature, 9.6 SM-EtherCAT serial number
Ohio man, 81, fatally shoots Uber driver, 61, after scammers target both of them, officials say
An 81-year-old Ohio man has been charged in the fatal shooting of an Uber driver he believed was working with a scammer, according to officials who said the victim was sent to the home by the same scammer.
William Brock told investigators he shot Loletha Hall, 61, outside his home March 25 because he thought she was working with a man who called him pretending to be an officer at the local court, Lt. Kristopher Shultz of the Clark County Sheriff's Office said.
"Mr. Brock received some scam call by a person purporting to be someone from our courts who informed him a family member was incarcerated and that he had a bond of a significant amount of money," Shultz said. "The calls turned from 'I'm an officer in the court' to 'We have this subject hostage, this is a ransom demand.'"
The person who called Brock, or an accomplice, requested an Uber ride to his South Charleston home to pick up the money, Shultz said.
"Ms. Hall did not have any idea," he added.
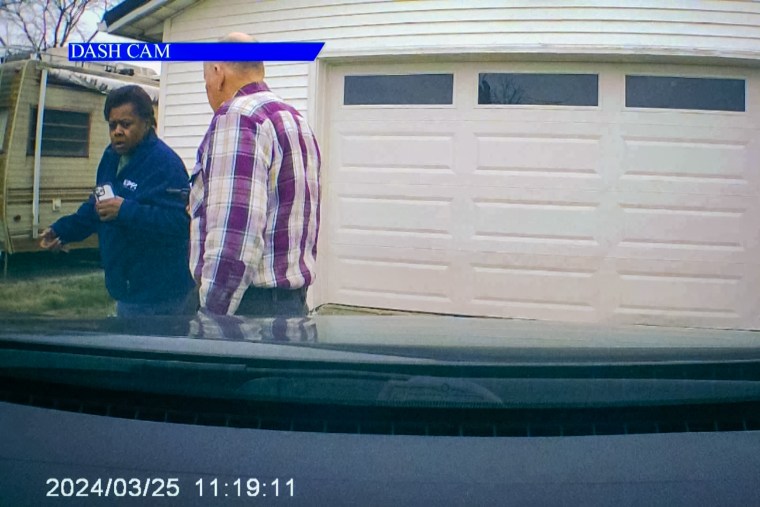
When Hall arrived at the home and approached the front door, Brock confronted her with a gun and asked her who she was working for, Shultz said. He took her cellphone and prevented her from getting in her vehicle and driving away.
“When she tried to get away, he shot her once, then there was more exchange between them," Shultz said. "Mr. Brock was at some point injured to his head, and he shot Ms. Hall a second time. There was more conversation, and then he shot her a third time. Only after he shot her a third time did he then make contact with authorities to report the incident."
Hall did not threaten Brock, have a weapon or assault him, according to the sheriff's office and a complaint filed in Clark County Municipal Court. She was taken to a hospital where she died from her injuries, according to the complaint.
In a statement, Uber said the company had spoken with Hall's family.
"This is a horrific tragedy and our hearts continue to be with Loletha’s loved ones as they grieve," an Uber spokesperson said. "We have been in contact with law enforcement and remain committed to supporting their investigation."
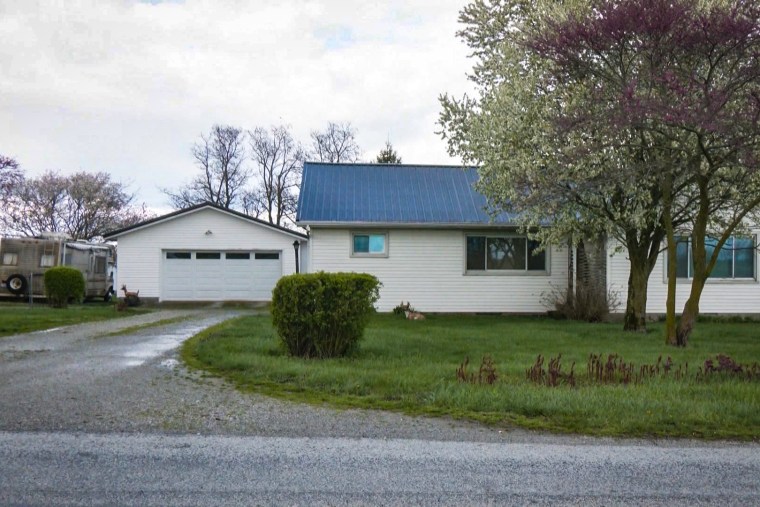
The Uber spokesperson said the account of the person who ordered a car to Brock's house has been banned. Officials have not identified the person who requested the Uber and have not said whether they have made any additional arrests in connection with the case.
In a grand jury presentation Monday, Brock was indicted on three counts of murder, one count of felonious assault and one count of kidnapping, Shultz said. He will be arraigned on those charges later this week.
It was not immediately clear whether he has an attorney.
Brock was originally arraigned on a murder charge in the Municipal Court of Clark County on Wednesday and posted a $200,000 bond. If convicted of that charge, he could be sentenced to 15 years to life in prison or a $15,000 fine.

Breaking news reporter
404 Not found
Azerbaijan - Government Gulfstream Aerospace G650, G650ER 4K-A188

Photographer's remark (26.6.2019, 13:08 CET)
Create link | Add to Photo Album

Terms and Conditions | About | FAQ | Photo Use | Privacy Policy | Online 1249 (31 members) © 2006-2024 Airplane-Pictures.net | E-mail us: [email protected] All photos are copyright © to their respective photographers and may not be used without permission.
404 Not found
Na Ulitse Yalagina 13B Apartments
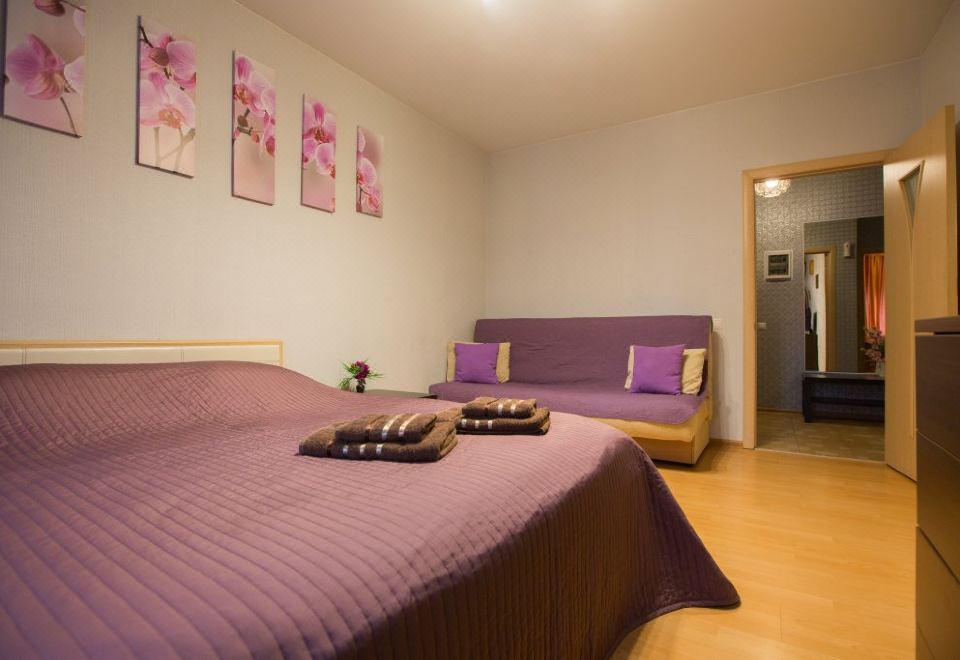
Property Policies
Frequently asked questions, how much does it cost to stay at na ulitse yalagina 13b apartments, what are the check-in and check-out times at na ulitse yalagina 13b apartments, does na ulitse yalagina 13b apartments provide airport transfer services, what amenities and services does na ulitse yalagina 13b apartments have, does na ulitse yalagina 13b apartments have a swimming pool, does na ulitse yalagina 13b apartments have fitness amenities, does na ulitse yalagina 13b apartments provide wi-fi, does na ulitse yalagina 13b apartments have non-smoking rooms, does na ulitse yalagina 13b apartments have a restaurant, is parking available at na ulitse yalagina 13b apartments, popular hotels, popular attractions, explore more.
Park City snowboarder accused of trying to sneak onto Texas flight home at SLC airport faces federal charges
The man used a photo of another passenger’s boarding pass to board the plane, prosecutors say..
(Rick Egan | The Salt Lake Tribune) Delta Air Lines planes at Salt Lake City International Airport, on Friday, Dec. 23, 2022.
A Texas man who authorities say took a picture of another person’s boarding pass and tried to sneak onto a Salt Lake City airport flight home after a snowboarding trip to Park City is now charged with national security crimes.
A federal grand jury this month indicted 26-year-old Wicliff Yves Fleurizard, of Leander, Texas, on charges of stowing away on an aircraft and access device fraud, according to the U.S. Attorney’s Office for the District of Utah.
Fleurizard was arrested March 17 after he successfully boarded a Delta Air Lines flight bound for Austin, Texas, using a cellphone photo of another passenger’s boarding pass. Once on the plane, he opened an emergency equipment storage door, charging documents say.
A flight attendant who saw Fleurizard open the storage door then directed him to the plane’s front lavatory, which Fleurizard stayed inside of for the remainder of boarding.
When he exited the lavatory, he then made his way to the plane’s back lavatory. By the time he exited that restroom, a flight attendant noticed all the plane’s seats were occupied and confronted Fleurizard.
The plane had started to taxi away from its gate when Fleurizard claimed another passenger was in his seat. When flight attendants verified that was not true, and were unable to locate a valid ticket or booking reservation for him, the plane returned to the gate and Fleurizard was arrested.
Authorities reviewed surveillance video of the boarding area, which showed Fleurizard surreptitiously taking photos of several passengers’ phones and paper boarding passes before boarding the plane.
Fleurizard told police he was “only trying to get home” after a snowboarding trip to Park City, according to charging documents. A friend had given him a Southwest Airlines companion pass, he said, which allowed him to get through airport security.
But he was then unable to board any Southwest flights because they were full, he told police, prompting him to try and fly home on the Delta plane.
Fleurizard’s initial court appearance will be scheduled for “a later date,” federal prosecutors said.

Donate to the newsroom now. The Salt Lake Tribune, Inc. is a 501(c)(3) public charity and contributions are tax deductible
RELATED STORIES
High-stress flying environment mixed with pandemic causes explosion of unruly passengers at salt lake airport, even with few travelers, 3 firearms found at salt lake airport checkpoints this week, salt lake airport tsa intercepts seven guns in seven days. six of them were loaded., boost your utah home’s value with these 4 strategic upgrades, why this lds lawyer recognizes passover by driving six hours to buy liquor he will never drink, opinion: we can’t get back what is lost. preserving utah’s historic places is investing in our future., how salt lake city plans to heal its ‘single-largest transportation issue’, gordon monson: do you believe in miracles i do, and here’s why., with one slc skyscraper stuck, developer turns to converting an office tower into apartments, featured local savings.
Electrostal History and Art Museum
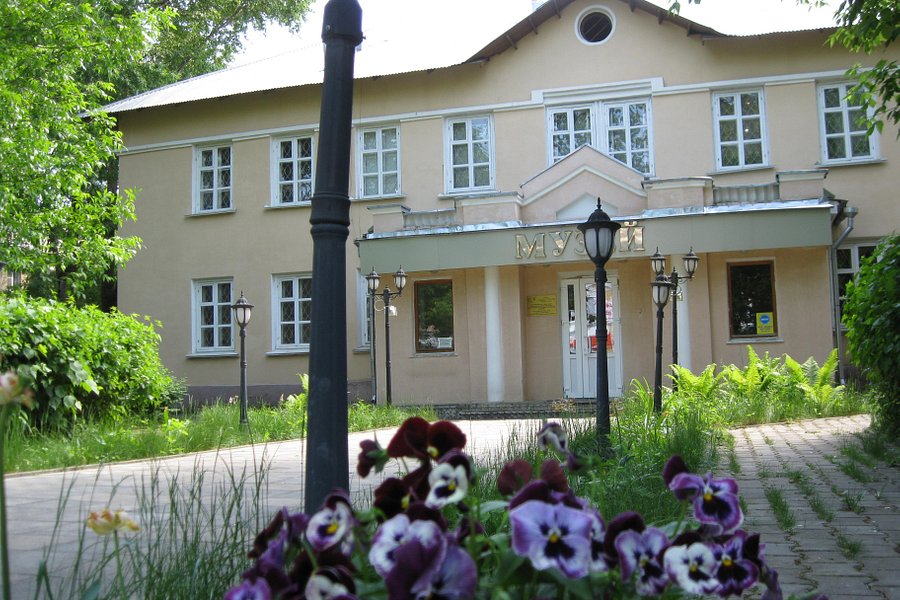
Most Recent: Reviews ordered by most recent publish date in descending order.
Detailed Reviews: Reviews ordered by recency and descriptiveness of user-identified themes such as wait time, length of visit, general tips, and location information.
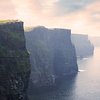
Electrostal History and Art Museum - All You Need to Know BEFORE You Go (2024)
- (0.19 mi) Elektrostal Hotel
- (1.21 mi) Yakor Hotel
- (1.27 mi) Mini Hotel Banifatsiy
- (1.18 mi) Elemash
- (1.36 mi) Hotel Djaz
- (0.07 mi) Prima Bolshogo
- (0.13 mi) Makecoffee
- (0.25 mi) Amsterdam Moments
- (0.25 mi) Pechka
- (0.26 mi) Mazhor
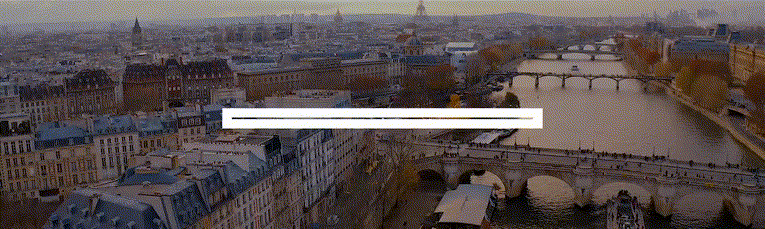
IMAGES
VIDEO
COMMENTS
Under voltage trip and restart levels are as follows: Drive voltage rating UU trip level UU restart level. 200 175 215. 400 330 425. 575 435 590. 690 435 590. 2. OU. DC link over voltage.
Understanding trip codes is an important part of keeping your equipment running smoothly. Below are some of the more common codes you may come across when using your Control Techniques Unidrive M200 series drive: Trip Code. Condition. Possible Cause. C.Acc. NV Media Card Write fail. Unable to access the NV Media Card.
Motor thermistor trip. Excessive motor temperature. O.Ld1*. User +24v or digital output overload. Excessive load or short circuit on +24v output. cL1. Analogue input 1 current mode, current loss. Input current less than 3mA when 4-20 or 20-4mA modes selected. SCL.
The logic type is set up at #8.29 in the Control Techniques Unidrive SP. The Unidrive SP defaults to positive logic. When the drive is in positive logic you will need to inject +24VDC to activate the digital inputs. The +24VDC can be supplied by the drive or externally. The Unidrive SP can be enabled to run in numerous ways.
28 mA* AC at 400 V 50 Hz 30 µA DC with a 600 V DC bus (10 MΩ) Size 4: 9.5 mA* AC at 400 V 50 Hz 36 µA DC with a 600 V DC bus (10 MΩ) Unidrive M702 User Guide Issue Number: 3... Page 69 Loosen the ground connection nuts and slide the grounding clamp down onto the pillars in the direction shown.
These Troubleshooting Guides are intended for use by Qualified Electronic Technicians versed in Motor Drives and Industrial Power devices. The procedures outlined in these guides expect that the Technician understands the hazards of working with High Voltage 3 phase power devices and has basic troubleshooting skills and a working knowledge of ...
1.2 Electrical safety - general warning. The voltages used in the drive can cause severe electrical shock and/or burns, and could be lethal. Extreme care is necessary at all times when working with or adjacent to the drive. Specific warnings are given at the relevant places in this User Guide.
A Trip is an action that happens in the Unidrive SP that causes the drive bridge to be inhibited therefore stopping all motion. When the drive inhibits, the drive does not have control of the motor/load.
Emerson Commander SK Trip and Status Diagnostic Codes - Free download as PDF File (.pdf), Text File (.txt) or read online for free. Commander SK Trip and Status Diagnostic Codes
Internal Drive EEPROM trip: Possible loss of parameter values: PH: Input phase imbalance or input phase loss: One of the input phases has become disconnected from the drive (applies to 200/400v three phase drives only, not dual rated drives. rS: Failure to measure motors stator resistance:
Trip Trip Trip Code Sizes 1-4 Trips Size 5
UU. UTILITIES link under voltage. Lower voltage trip and restart floors are the follows: Drive voltage performance UU journey plane UU restart level. 200 175 215. 400 330 425. 575 435 590. 690 435 590. 2.
All drives are going to trip at some point conversely other. Next time your Unidrive is throw an flaws code, the follows information may help. ... SL2.HF: Option component the slot 2: Ironware fault: 206: SL2.tO: Option module in single 2: watchdog timeout: 207: SL2.Er: Option module in slot 2: oversight: 208: SL2.nF: Option model in slot 2 ...
Introduction. Trip 2 a non-emergency medical transportation solution dedicated to optimizing patient care and service. Getting patients to their appointments quickly and safely is our highest priority. The Trip 2 software integrates over 30 years of field experience with the latest in cutting edge technology. Finding faster, efficient solutions ...
in. Motor thermistor trip. Excessive motor temperature. O.Ld1*. User +24v or digital performance overload. Excessive load or short circuit on +24v output. cL1. Analogue in 1 current mode, current loss. Input current less than 3mA when 4-20 instead 20-4mA modes selected.
Stop your equipping running smoothly by using the following guided to diagnose anywhere trip codes. The tracking are some of the common fault you might meetup: Emerson Commander SK Fault & Trip Codes by Controls Techniques. Trip Codes: Set: ... What is a SL2.er fault upon a Unidrive SP? Your there anywhere way to clear it? Reply. pritesh says ...
Emerson 0471-0128-02 9.4 Drive trip display codes, 9.5 SM-EtherCAT module temperature, 9.6 SM-EtherCAT serial number 1 59 70 70 Download 70 pages, 3.59 Mb
By Mirna Alsharif. An 81-year-old Ohio man has been charged in the fatal shooting of an Uber driver he believed was working with a scammer, according to officials who said the victim was sent to ...
Emerson Commander SK Fault & Trip Codes by Control Technologies. Trip Code: Condition: Possible Why: UU: ... please help own on Emerson Unidrive M200. i drive views ER 01.5C faults. What fault is ER01.5C ? Reply. Tom Gawlik says: December 27, 2021 at 3:29 pm ... What will a SL2.er fault on a Unidrive SP? Lives there random way to clear it ...
Azerbaijan - Government Gulfstream Aerospace G650, G650ER 4K-A188. Request photo usage. Chris2002 Dominik Kauer Image ID: 1208106 Views: 684
Apelsin Hotel, Elektrostal: See 43 traveler reviews, 19 candid photos, and great deals for Apelsin Hotel, ranked #1 of 4 hotels in Elektrostal and rated 4 of 5 at Tripadvisor.
Emerson Unidrive SP2403. I/P 380-460 Volt , 50-60Hz. 3Ph, 26.6 Amp S# 8127689002 How can myself impede the present set setup. Process instructions please explain.
LocationIf you want to feel like you're at home no matter where you are, choose this — apartment «Na Ulitse Yalagina 13A Apartments» is located in Elektrostal. This apartment is located in 3 km from the city center. You can take a walk and explore the neighbourhood area of the apartment — ZIL Culture Center, Saint Basil's Cathedral and ...
Comment. A Texas man who authorities say took a picture of another person's boarding pass and tried to sneak onto a Salt Lake City airport flight home after a snowboarding trip to Park City is ...
Art MuseumsHistory Museums. Write a review. Full view. All photos (22) Suggest edits to improve what we show. Improve this listing. The area. Nikolaeva ul., d. 30A, Elektrostal 144003 Russia. Reach out directly.