- The Staircraft Group
- Resource Centre

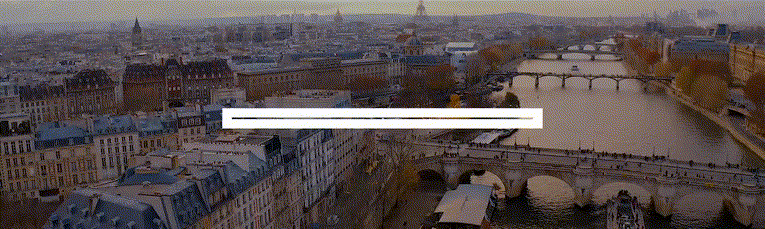
Fitting Stairs & Stair Parts
Unique Pre-Assembled Staircases from the world’s largest staircase manufacturer

Our products are created with you in mind - loaded with cost-saving innovations in addition to a faster installation. Continue reading to discover more about how to install our staircases.
Stair Installation Recommendations
Site fixing of stairs should be in accordance with Building Regulations, NHBC Standards and any referenced documents with particular attention to the BWF Installation Guide and the following:
All wall strings are to be fixed through the pre-drilled holes using appropriate fixings. Wall strings may need to be cut at each end vertically, to suit skirting height and/or cut to not project into a passageway causing a trip hazard. Refer to the above-mentioned BWF Fixing Guide for guidance and the string fitting guidance in our resource centre.
Tread and Winder
Treads should be fixed by gluing with PVA and driving home-supplied wedges.
Risers are to be fixed by gluing with PVA and driving home-supplied wedges. The lower edge of risers should be glued and fixed to treads using an appropriate fixing at centres not exceeding 230mm. The fixing should penetrate each tread by at least 23mm or 1.5 times the thickness of the risers, whichever is greater.
Newel-posts
Newel-posts are mortised to receive a string tenon and should be fixed using dowels and a suitable adhesive. Newel-posts must also be fixed square to the tread. DPC is to be fitted under newel-posts/stringer on the ground floor to avoid moisture intake.
Flight and Landing Nosings
Flight and Landing Nosings should be fixed to the wall string, newel-post and trimmer. Landing nosings should be fixed to the trimmer and not project more than 15mm from the finished face of the trimmer.
Corner Glue Blocks
Corner Glue Blocks are to be glued every 150mm.
All winder staircases are supplied with a factory-prepared, under-stair, soffit detail which also allows for the suitable dry lining to be fixed to the angled glue blocks, creating a stepped soffit detail. String trenchings are ‘stopped’ to provide a neat finish and this solution increases available headroom. This system is optional and allows for staircases to be finished via traditional methods.
The decorated finish of the product may determine the type of adhesive to be used. With a painted finish, Polyvinyl Acetate (PVA) will be suitable for joints. However, with a clear finish it may be necessary to use an alternative such as Cascamite. In all cases the adhesive supplier should be consulted for recommendations.
The material, packing distances, wall and well opening construction and load-bearing requirements are to be considered when deciding on an appropriate fixing. In all cases the fixing supplier should be consulted for recommendations, considering the materials to be fixed.
Before installing any staircase or staircase part, the following checks must be undertaken:
- The specification and standard of the product reflect the order
- The house type, handling, dwelling reference and floor level correspond accordingly
- The overall staircase finished floor to finished floor dimension must match the structural dimension to which the staircase is to be fitted
- All parts are present and correct to enable a full installation
- The overall width of the staircase provides for the required flight and balustrade clearances
- All intermediate landings are installed correctly
Final Checks Once Staircase Is Installed
Subsequent and final checks must conclude that:
- There is a minimum 2000mm headroom clearance
- The staircase is level
- All newel-posts are plumb
- All joints are correctly fitted and fixed
- All supports and blocks are glued and correctly fixed
- The wall strings are firmly fixed
- The staircase does not flex or squeak
Related Downloads
Please find useful related downloads below.

Privacy Overview
When Do the NHBC Standards Apply to Balconies?
The National House Building Council (NHBC) Standards play a pivotal role in ensuring that new homeowners receive a property that not only meets but often exceeds their expectations for quality and safety. These standards are intricately designed with a focus on reducing risk and enhancing the end-user experience in their new home.
Unlike a British Standard or a Euro Standard, which may form part of the mandatory path to demonstrating compliance with building regulations, NHBC Standards apply specifically when NHBC is selected to provide the warranty for the building. It’s important to note that these standards are not universally mandatory; they are particular to NHBC’s warranty service.
NHBC is recognised as one of the most reputable leaders in the field, setting a benchmark for excellence in warranty protection. Although other providers like Premier Guarantee are also common, especially for high-rise buildings, they typically do not operate a separate set of standards. This doesn’t diminish the influence of NHBC standards; on the contrary, in the absence of balcony specific guidance prior to the BS8579:2020, they were really the only independent source of guidance so often served as a reference point for balconies.
One area where the NHBC Standards have been particularly focused, for various products but especially balconies, is in preventing water ingress into buildings. This issue has been a significant aspect of warranty claims over the years. With the lack of specific guidance in British Standard BS8579:2020 and Part H (or Document H in Ireland) regarding balcony-related drainage, the NHBC standards have often been adopted as a reference point for best practice, regardless of the warranty provider.
Ultimately, NHBC Standards are applied to projects that they will warranty. However, when a warranty provider has not yet been chosen at the early stages of a project, it is considered good practice to ‘start with the end in mind.’ Given that NHBC’s balcony guidance is more stringent than BS8579:2020 and what is typically required by other warranty providers, it is prudent for developers to aim to meet or exceed these standards from the outset.
Doing so ensures that the project is prepared to meet the NHBC’s rigorous requirements should they be engaged as the warranty provider. Additionally, by adhering to these more onerous guidelines, developers are able to guarantee a higher standard of construction, thereby reducing risks associated with water ingress and enhancing the overall quality of the living experience for the end-user. This forward-thinking approach is not only beneficial for meeting NHBC standards but also serves as a mark of quality and diligence that is valued throughout the industry.
2024 Changes to the NHBC standard which particularly impact balcony design
In 2024, a significant update was rolled out, especially effecting thermal efficiency and sustainable design. However there are a number of ‘minor points’ of change which have been tweaked which will be impacting balcony design. Some have already been applied for a while on projects but some are a little more surprising.
The 2024 balcony related updates focus particularly on drainage, loosely based on BS8579:2020.
Changes to 7.1
7.1.4 Has been updated to add a clause to stop balcony drainage from dripping onto balustrades below. The statement This is additional to previous requirements which is loosely based on the BS8579:2020 interpretated in NHBC’s perspective. Not draining onto vertical surfaces below reflects BS8579:2020 however the difference lies in the requirement for not flowing onto barrier edges and fascia’s of balconies which is not referred to in the British Standard.
In real terms this means that any stacks of balconies will need to have a drip edge projecting beyond the balustrade. The clause says:
“The rainwater drainage system may be based on conventional piped drainage or an edge drained design. In all cases the downpipes, overflows and edge drainage outlets should be positioned in the construction to provide effective drainage that will not cause water to flow directly down onto the walls and fascia surfaces below or barrier edges of balconies installed in any stacked multi-storey arrangement”.
There is also a new requirement to:
“designed with a projecting profile that prevents rainwater from either tracking back into any soffit or running straight down onto vertical surfaces situated below”
This change doesn’t change anything for the way that Sapphire balconies are designed but in essence means balconies need to have some kind of drip edge at the lip where it is discharged. Again, there is reference to vertical surfaces which matches the BS8579:2020 diagram and guidance.
Another new point relating to where the controlled drainage is being done using RWP (Rainwater Pipes). It would generally be considered standard practise and does not affect Sapphire Balconies design:
“designed with a downpipe shoe fitted where any downpipe outlet discharges above finished ground level, including above a drainage gulley.”
And also a standard not point balcony drainage to BS8579:2020. It has always been the case of what we would point people to for balcony guidance and again is best practise advise which doesn’t have an impact on what Sapphire do or the way we design.
Designs for drainage of balconies and terraces should follow BS 8579 guidance for the provision of discharge outlets with effective clearance, capacity and profile shape to throw rainwater clear of the edge and prevent residual dripping onto other parts of the building beneath.
Another couple of new clauses but ones we have seen multiple times on the more recent NHBC Warranty projects are now included on the new version of their standards. These points cover guidance around ground floor and entrances to buildings, generally following the common NHBC interpretation of BS8579:2020. Secondly, there is a point about water cascading down the building. Whilst our opinions differ considerably from this statement, based on the research and testing we have done which tends to suggests otherwise there is now the following wording:
“A design approach for free draining balconies can be accepted if rainwater will always be routed away from the building to drain via a suitably formed soffit drainage tray that directs water to run outwards over a continuous formed perimeter edge. But where this drainage design is installed for stacked balconies on multi-storey elevations – the rainwater will tend to cascade down from these edge drainage slots as water runs off each balcony.
Under typical wind driven rainstorm conditions the water runoff volumes from these balcony catchment surfaces will progressively increase in a downward direction until the full volume of water reaches ground level. this can adversely affect locations such as main entrances to apartment buildings as well as any access doorways and private gardens of individual homes situated at ground level. therefore, in addition to the free draining balcony design there is a requirement for design of ground level drainage to effectively prevent ponding or flooding of water. this drainage design is required along all building perimeter locations where thresholds, access locations and other places of regular use will exist.”.
There is new guidance specifically referencing free draining balconies. This is assumed to be what is called controlled edge draining in BS8579:2020. It here references a continuous formed perimeter edge. Again requiring a drip edge along the edge where drainage is being dispersed.
“A design approach for free draining balconies can be accepted if rainwater will always be routed away from the building to drain via a suitably formed soffit drainage tray that directs water to run outwards over a continuous formed perimeter edge.”
Guidance has been updated for 7.1.5 Flat roof, terrace and balcony structural design. Again this doesn’t effect the design of Sapphire balconies.
“Flat roofs, terraces and balconies shall support and transmit loads safely to the structure. The structure of the flat roof, terrace or balcony should:
Be produced by an engineer in accordance with technical requirement r5, and bs en 1991-1-1, bs en 1991-1-3, bs en 1991-1-4 and bs 8579: 2020 for balconies, be designed to address both short term and long-term deflection to provide an effective drainage strategy with no back falls or ponding. resist wind uplift by self-weight or by being anchored to the main structure – where required, holding down straps should be provided at maximum 2m centres at the perimeters, have adequate provision for the additional loads where a flat roof is to act as a terrace, roof garden, for support of permanent service equipment, and for additional loads during construction”..
There is however a reference to holding down straps which may see an increase in request relating to this.
Specific requirements for gaps around decking also remain in the standard and are split between edges and gaps between boards. Again not a change in intentions nor of our balcony design.
“As-built gaps of 10mm – 12mm should be provided between decking/paving units along perimeter upstands/thresholds. As-built gaps of 6mm – 8mm should be provided between individual units of decking or paving. Spacers and supports which raise the decking or paving should not obstruct the flow of rainwater to outlet(s).”
There is a new section referring to the use of metal balconies referring back to BS8579:2020. Again a welcome reference to a document we have been following for a long time.
“7.1.17 Metal balcony decking systems
Metal balcony framework structures and metal balcony decking systems should be designed and constructed as recommended in bs 8579 guidance for the design of balconies and terraces and their component parts.”.
There is also new guidance relating to glass use specifically mentioning glass compliant with Part B fire regulations but it does not mention limitations under Regulation 7. It seems to indicate that the use of monolithic glass in a guarding is permissible for balustrading.
“be toughened glass, laminated glass (subject to meeting fire regulations) or glass blocks (suitably reinforced) where glazed balustrading is used”
What were sapphire expecting to see which isn’t in the updated standards.
Previously the 30mm drip edge, referred to in BS 8579:2020, for where there is a vertical surface of the building (i.e. in scenarios where there is a warm space below a balcony or terrace) had been a frequent topic of conversation on projecting balconies. This has been the result of what we believe is a uncommon interpretation and application of one different application rather than the correct for the scenario show in the edge drained sketch in BS8579:2020. The only balcony and terrace related reference to 30mm drip edges in the 2024 standards is for where there are scenarios matching the BS8579:2020 sketch and guidance, for example parapet walls copings on top of inset balconies and similar scenarios. This matches the Sapphire interpretation of this guidance as these scenarios have a vertical surface of the building below and therefore needs a drip edge to avoid unsightly staining, water ingress etc.
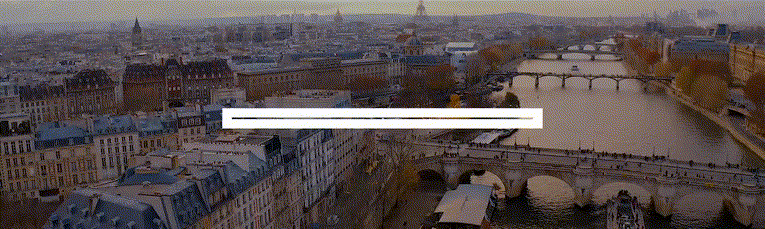
NHBC Future direction of travel
At the Building For Tomorrow, London Conference on 27/02/2024, the NHBC provided insights into the evolving landscape of construction standards, particularly for balcony design and high-rise buildings. This section summarises the key points from the speeches delivered at the conference, outlining the “direction of travel” for the NHBC standards.
NHBC Standard Direction of Travel: Chris Hall presentation
Chris Hall, the technical innovation manager at NHBC, shared that the process of updating the standards is ongoing and typically operates on an 18-month rolling update cycle. Coastal standards are revisited every three years to reflect the latest in environmental and technical requirements. He highlighted the focus in England on future homes and building standard consultations, with Wales adopting the 2022 version of Part F, L, and O. Scotland is pushing towards a ‘passive house like’ standard as a mandatory building regulation.
In 2024, a new chapter was added to the NHBC standards focusing on engineering fill. Five chapters received major updates, including those on external walls and pitched roof guidance, complemented by 70 new CAD drawings. Minor updates were made to other chapters, such as chapter 7.1, and the 2025 process will aim for consolidation of these changes.
Overview of the Implications of Building Safety Act for High-Risk Buildings: Steve Evans’ Speech
Steve Evans, the Head of Technical Operations at NHBC, provided an overview of how the Building Safety Regulator’s new regime, operated by the Health and Safety Executive (HSE), will function and its implications for NHBC. Following the post-Grenfell changes to the building control regime, as of 1 October, high-risk buildings (HRBs) can no longer be part of the NHBC Building Control Scope, with building control set to become a regulated profession under the BSR Rules from 6 April 2024.
For NHBC, this means:
- Continuation as warranty providers for buildings.
- Managing HRB transitional provisions on projects still working to old regime.
- Implementing warranty pilot schemes for full compliance.
- Assisting the BSR on multi-disciplinary teams, ensuring teams demonstrate competency by 6/4/24.
Standards for High-Rise and Complex Buildings: Philip Smith’s speech
Philip Smith, a principal technical specialist at NHBC, discussed the need for a new standard for high-rise and complex buildings. The NHBC recognises the need to shift its focus from traditionally low-rise buildings to create specific and more focused guidance on the unique challenges posed by high-rise and complex building’s.
The NHBC has identified some particular areas where there is a gap between their standards and changing landscape in the high-rise sector includes legislation and regulation changes, the climate change and carbon-neutral agenda, future homes, and building standard consultations. There’s also an emphasis on Modern Methods of Construction (MMC) innovation, systemisation, and product certification changes highlighted by the OPSS. Particularly volumetric and panelised systems are increasingly common so that is an area of specific focus too.
Cladding and fire-related claims have significantly influenced the loss both in numbers and in value, prompting a new change control regime that impacts how changes are made and recorded throughout construction and the supply chain. NHBC standards are set to start aligning with the pace of change on MMC, particularly with volumetrics and panelised systems, as part of the PAS 8700 standard. NHBC continues to map out risks and changes in construction techniques, aiming to be simple, consistent, clear, and collaborative.
What Are the Practical Implications of NHBC Standards on Balconies?
The NHBC Standards, particularly those related to balconies, have practical implications that extend beyond compliance; they guide the design and construction processes to ensure the long-term integrity and usability of buildings. Here are three key points to consider:
A) Implementation of a Drip Edge
A drip edge is required at the front drainage edge of most balcony scenarios. This component is deemed crucial to fulfil the latest NHBC 2024 standards as it is aims at preventing water from dripping onto the guarding of the balcony below. It’s an essential consideration that serves to protect lower balconies in a stack or the building’s façade from water staining or nuisance. Sapphire has multiple ways of achieving this. The below images show how this can be done effectively and without the drainage having to run through small drainage slots which could be susceptible to becoming blocked or being too small outlets to deal with storm drainage.
B) Ground Floor Drainage Considerations
At the ground floor level, especially at main entrances needs more careful planning of the drainage is imperative to meet the newest guidelines. It’s essential to ensure that rainwater from balconies has been designed to minimise the nuisance of water discharged onto ground floor areas, especially the main access areas of buildings. This not only affects the aesthetic appeal but can also pose a safety hazard, especially in adverse weather conditions. Strategic placement of drainage solutions can help avoid creating slippery conditions or pooling of water in high-traffic areas. Design consideration needs to be made on how the balcony drains but equally how ground drainage is also done.
C) Sustainable Urban Drainage Systems (SUDS) Strategy
In line with sustainable building practices, it’s necessary to consider how your Sustainable Urban Drainage Systems (SUDS) will function, particularly in preventing ice formation on pathways below where balcony drainage may discharge. This is especially crucial in areas/locations prone to freezing temperatures, where improperly managed drainage can lead to hazardous ice patches. To meet the NHBC standards it should be a consideration of principle designers and landscape designers, etc as to how the design should ensure that water is channelled away safely and does not contribute to potential hazards or damage landscaping.
Conclusion and Recommendations
Adhering to the NHBC Standards for balconies puts increased focus on dealing with drainage appropriately. Therefore it necessitates thoughtful design and engineering solutions to manage rainwater effectively. The spirt and guidance in the standards aims to prevent immediate water related damage, whilst mitigating long-term risks and ensure safety and comfort for building occupants. For balconies, achieving the NHBC 2024 standards does require more than building regulation and compliance with BS and EN standards. It will cost more and will mean considering this early. We are happy to assist at an early stage with this to give project specific guidance.
For those seeking to deepen their understanding of this topic and to explore innovative drainage solutions and approaches, reach out to use to book a rainwater CPD presentation. Additionally, Sapphire’s Drainage Whitepaper offers an in-depth look at effective drainage strategies, providing valuable insights and guidance. Both resources can prove instrumental in achieving a design that is both compliant and conducive to a safe and sustainable living environment.
Do bear in mind that if you are designing to NHBC guidance early on because it is a change to a façade related component, under the new Building Safety Regulator regime, once it is submitted through Gateway 1, then it is going to need to be used. Our advice is; be prepared, or make the decision on warranty providers at an early stage. Your choice, just remember façade related changes will not be easy and neither will cost be an acceptable justification.
You may also find this video useful in understanding the BS8579:2020 statistics.
What are TEDI Ratings and How Do They Affect Balcony Design?
Insider magazine recognizes atw group for global growth, why would a prefabricated balcony benefit my development.
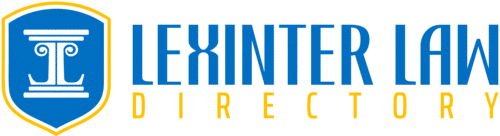
Understanding OSHA Regulations for Trip and Fall Hazards in the Workplace
Workplace safety isn’t just a good idea-it’s the law. In industries where the risk of trip and fall hazards is substantial, strict regulations exist to safeguard employees.
The fines for non-compliance can be hefty, but more importantly, adherence to these rules saves lives and prevents injuries. Below are the key OSHA-mandated practices your organization needs to have in place to prevent falls and protect your team.
Table of Contents
Uneven Surfaces
Spills and clutter, poor lighting, improper footwear, fines and penalties, worker’s compensation, productivity loss, routine hazard assessments, barrier installation, safety training, maintenance protocols, immediate response, medical referral, incident investigation, understanding your rights, filing a claim, maximum settlements, reputation and experience, local expertise, client testimonials, proactive prevention, follow this guide to adhere to osha regulations for trip and fall hazards in your workplace, identifying common hazards.
The first step to a safer workplace is to carefully find potential hazards. Below are some of the most frequently encountered dangers:
Hazards, like cracked sidewalks, uneven floors, and loose tiles, can easily cause trips. They can trip even the most cautious employees. Proactively identifying and promptly repairing these surfaces is crucial for preventing accidents.
Spills in the break room and unattended boxes in hallways are commonplace. But, they pose significant trip hazards.
These are among the most preventable risks that, surprisingly, occur frequently. Implementing strict cleanliness and storage policies can help mitigate these dangers.
Areas with inadequate lighting can hide hazards that are noticeable in well-lit conditions. Ensuring regular maintenance and conducting thorough lighting audits can help mitigate these risks.
Employees need the right footwear for their jobs. These might be non-slip shoes for wet areas or steel-toed boots for construction sites. Good footwear reduces falls.
The Cost of Negligence
Knowing the cost of workplace accidents can motivate people to follow safety rules and OSHA guidelines. Here are key considerations:
Violations of OSHA standards , especially those related to fall hazards, can lead to hefty fines and penalties. Adherence to these regulations is not only a matter of legal compliance but also a financial imperative to avoid such costs.
Injuries resulting from falls can lead to significant worker’s compensation claims. This creates financial strain on the company’s resources and negatively affecting the bottom line.
The direct costs of accidents are often accompanied by indirect costs such as:
- downtime for investigations
- recovery periods for injured employees
- decline in team morale
All these can adversely affect overall productivity.
Fall Safety Protocols
Following OSHA’s fall safety rules through practical steps can greatly improve workplace safety. Here are some strategies:
Regular walk-throughs and safety inspections are good proactive approaches. They help find and fix hazards before they cause accidents.
Installing safety measures can prevent falls and save lives. They include:
- safety nets
- skylight screens
These measures are installed proactively in areas identified as high-risk.
Offer comprehensive education to employees about the risks associated with their specific roles. They must understand the importance of adhering to safety protocols. This can dramatically reduce the likelihood of accidents.
Develop and maintain a consistent schedule for the repair and upkeep of workplace infrastructure. This is vital in ensuring a safe and hazard-free working environment.
What to Do After an Accident
Preventing falls is crucial, but it’s only one aspect of a comprehensive safety strategy. Equally important are the procedures followed after a fall. These are critical to ensuring employee well-being and meeting legal requirements.
It’s vital that all staff are well-versed in the immediate actions to take following a fall. These steps include:
- securing the area to prevent incidents
- providing first aid if qualified
- reporting the incident to the appropriate personnel
After an accident, providing clear and accessible processes to receive medical help is essential. This not only aids in their recovery but also supports any potential workers’ compensation claims .
Conducting a thorough investigation into the cause of a fall is crucial. It’s not just about fulfilling a legal requirement. It’s an opportunity to uncover and address underlying issues, preventing future incidents.
The Role of Legal Representation
The complexities of navigating the aftermath of a slip-and-fall incident can be overwhelming. This makes legal representation a valuable resource. Here’s why:
A qualified legal team can provide invaluable guidance on your rights after a slip and fall injury. Their expertise ensures that you’re aware of your entitlements and the obligations of your employer.
The process of filing a claim can be daunting, with many legal intricacies. Legal experts can simplify the process, allowing you to focus on your recovery while they handle the legalities.
If a settlement succeeds, legal help is crucial to ensure you get the full slip and fall settlement amounts you’re due. This includes medical expenses and lost wages.
Find a Personal Injury Attorney
Finding the right legal support after an injury is paramount. Here’s how to find a reputable attorney:
Seek out attorneys with a proven track record in personal injury law, especially those with experience in slip and fall cases. Their past successes can give you confidence in their ability to handle your case.
Choosing local attorneys can have significant advantages. They bring a deep understanding of state regulations and local legal nuances, which can be beneficial in navigating your case. For instance, if you work in Virginia, or specifically in Virginia Beach, then you should work with personal injury attorneys near Virginia Beach .
An attorney’s reputation can offer valuable insights into their dedication and effectiveness. Good reviews and referrals show their commitment. They aim for the best outcomes for their clients.
Viewing OSHA regulations as the minimum standard, not the goal, is key to creating a safer workplace. Proactive measures include regular safety meetings to discuss new measures and best practices.
Cultivating a safety-first culture transforms the workplace, with everyone committed to security. Encourage employees to voice concerns for a collaborative safety approach, making it a collective responsibility.
Following OSHA’s trip and fall rules avoids penalties. It also creates a secure, productive work environment for your team.
By understanding these rules and tailoring them to your organization’s needs, you show a commitment to safety. This commitment resonates with your team and stakeholders. Remember, a fall shouldn’t be the first sign you need to reinforce your safety measures-it should be the last.
For more insights and guidance on a range of other topics, we invite you to browse our blog.
Lost Your Password?
Reset Password
View prices for your travel dates
Reviews we perform checks on reviews. tripadvisor’s approach to reviews before posting, each tripadvisor review goes through an automated tracking system, which collects information, answering the following questions: how, what, where and when. if the system detects something that potentially contradicts our community guidelines , the review is not published. when the system detects a problem, a review may be automatically rejected, sent to the reviewer for validation, or manually reviewed by our team of content specialists, who work 24/7 to maintain the quality of the reviews on our site. our team checks each review posted on the site disputed by our community as not meeting our community guidelines . learn more about our review moderation..
- Excellent 18
- Very Good 9
- All languages ( 43 )
- Russian ( 37 )
- English ( 4 )
- German ( 1 )
- Italian ( 1 )

" DIR: West; bigger nice evening sun but louder due to main street DIR:East; Quiter, very bright in the morning if sun rises "
Own or manage this property? Claim your listing for free to respond to reviews, update your profile and much more.
APELSIN HOTEL - Reviews, Photos
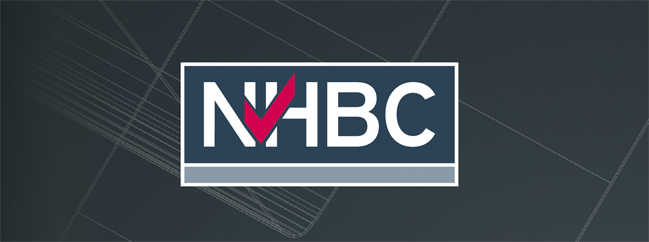
- Cookie Policy
- 1.1 Contact us
- 1.2 What’s changed
- 2.1 The Standards and Technical Requirements
- 2.2 3D Models
- 3.1.1 Compliance
- 3.1.2 Provision of information
- 3.1.3 Storage of materials
- 3.1.4 Site-mixed concrete
- 3.1.5 Ready-mixed concrete
- 3.1.6 Concrete specification
- 3.1.7 Admixtures
- 3.1.8 Special types of concrete
- 3.1.9 Design of reinforced concrete
- 3.1.10 Installation of reinforcement
- 3.1.11 Blinding concrete
- 3.1.12 Formwork
- 3.1.13 Before concreting
- 3.1.14 Casting
- 3.1.15 Curing
- 3.1.16 Testing
- 3.1.17 Glossary
- 3.2.1 Compliance
- 3.2.2 External conditions
- 3.2.3 Materials
- 3.2.4 Concreting
- 3.2.5 Masonry
- 3.2.6 Rendering, plastering and screeding
- 3.2.7 Admixtures
- 3.2.8 Painting
- 3.3.1 Compliance
- 3.3.2 Durability
- 3.3.3 Sitework
- 3.3.4 Protection and storage
- 3.3.5 Treatment of cut surfaces
- 3.3.6 Compatibility with metal
- 3.3.7 Further information
- 4.1.1 Compliance
- 4.1.2 Initial Assessment – desk study (all sites)
- 4.1.3 Initial Assessment – walkover survey (all sites)
- 4.1.4 Initial Assessment – results
- 4.1.5 Basic Investigation (sites where hazards are not identified or suspected)
- 4.1.6 Detailed Investigation (sites where hazards are identified or suspected)
- 4.1.7 Managing the risks (sites where hazards are found)
- 4.1.8 Unforeseen hazards
- 4.1.9 Documentation and verification
- 4.1.10 Guidance for investigations
- 4.1.11 Further information
- 4.2.1 Compliance
- 4.2.2 Provision of information
- 4.2.3 Building near trees
- 4.2.4 The effects of trees on shrinkable soils
- 4.2.5 Foundations in all soil types
- 4.2.6 Excavation of foundations
- 4.2.7 Foundations in shrinkable soils
- 4.2.8 Design and construction of foundations in shrinkable soils
- 4.2.9 Foundation depths for specific conditions in shrinkable soils
- 4.2.10 Heave precautions
- 4.2.11 New drainage
- 4.2.12 Foundation depth charts
- 4.2.13 Foundation depth tables
- 4.2.14 Example
- 4.2.15 Further information
- 4.3.1 Compliance
- 4.3.2 Provision of information
- 4.3.3 Ground conditions
- 4.3.4 Hazardous ground
- 4.3.5 Setting out
- 4.3.6 Services and drainage
- 4.3.7 Safe transmission of loads
- 4.3.8 Sloping ground and stepped foundations
- 4.3.9 Excavations
- 4.3.10 Reinforcement
- 4.3.11 Concrete
- 4.3.12 Movement joints
- 4.3.13 Construction joints
- 4.4.1 Compliance
- 4.4.2 Provision of information
- 4.4.3 Site conditions
- 4.4.4 Hazardous ground
- 4.4.5 Services and drainage
- 4.4.6 Safe transmission of loads
- 4.4.7 Construction
- 4.4.8 Engineer checks
- 4.4.9 Compressible materials
- 4.4.10 Reinforcement
- 4.4.11 Concrete
- 4.4.12 Movement joints
- 4.4.13 Resistance to moisture
- 4.5.1 Compliance
- 4.5.2 Hazardous sites and ground hazards
- 4.5.3 Desk study and site investigation
- 4.5.4 Confirmation of suitability for treatment
- 4.5.5 Suitability of ground conditions
- 4.5.6 Compatibility of the ground, design and treatment
- 4.5.7 Acceptable methods
- 4.5.8 Materials for use as fill
- 4.5.9 Granular material
- 4.5.10 Sitework
- 4.5.11 Adjacent excavations
- 4.5.12 Verification of completed treatment
- 5.1.1 Compliance
- 5.1.2 Provision of information
- 5.1.3 Transfer of loads
- 5.1.4 Ground conditions
- 5.1.5 Services and drainage
- 5.1.6 Ground below fill
- 5.1.7 Fill below floors
- 5.1.8 Infill up to 600mm deep
- 5.1.9 Materials used for fill
- 5.1.10 Harmful or toxic materials
- 5.1.11 Regulatory solutions
- 5.1.12 Walls below the DPC
- 5.1.13 Durability
- 5.1.14 Mortar
- 5.1.15 Wall ties
- 5.1.16 Blinding
- 5.1.17 Ground floor slab and concrete
- 5.1.18 Laying the ground-bearing floor slab
- 5.1.19 Damp proof course
- 5.1.20 Damp proofing concrete floors
- 5.1.21 Thermal insulation
- 5.1.22 Installation of insulation
- 5.1.23 Further information
- 5.2.1 Compliance
- 5.2.2 Provision of information
- 5.2.3 Contaminants
- 5.2.4 Proprietary systems
- 5.2.5 Transfer of loads: concrete floors
- 5.2.6 Reinforced concrete
- 5.2.7 Construction of suspended concrete ground floors
- 5.2.8 Transfer of loads: timber floors
- 5.2.9 Thermal insulation and cold bridging
- 5.2.10 Damp-proofing and ventilation
- 5.2.11 Floor finishes
- 5.2.12 Floor decking
- 5.3.1 Compliance
- 5.3.2 Provision of information
- 5.3.3 Preliminary work
- 5.3.4 Foul and surface water disposal
- 5.3.5 Drainage system performance
- 5.3.6 Ground water drainage
- 5.3.7 Design to avoid damage and blockages
- 5.3.8 Durability
- 5.3.9 Septic tanks and cesspools
- 5.3.10 Septic tank outputs
- 5.3.11 Surface water soakaways
- 5.3.12 Component requirements
- 5.3.13 Excavation
- 5.3.14 Protection of pipework
- 5.3.15 Laying pipework
- 5.3.16 Protection of work
- 5.3.17 Testing
- 5.4.1 Compliance
- 5.4.2 Provision of information
- 5.4.3 Waterproofing
- 5.4.4 Ground conditions
- 5.4.5 Structural stability
- 5.4.6 Design considerations
- 5.4.7 Waterproofing systems
- 5.4.8 Handling, storage and protection
- 6.1.1 Compliance
- 6.1.2 Provision of information
- 6.1.3 Structural design
- 6.1.4 Fire resistance
- 6.1.5 Acoustic resistance
- 6.1.6 Exposure
- 6.1.7 Thermal insulation
- 6.1.8 Concrete blocks
- 6.1.9 Bricks
- 6.1.10 Stone masonry
- 6.1.11 Construction of masonry walls
- 6.1.12 Lintels
- 6.1.13 Materials suitable for mortar
- 6.1.14 Mortar
- 6.1.15 Render
- 6.1.16 Cladding
- 6.1.17 DPCs and cavity trays
- 6.1.18 Wall ties and bed joint reinforcements
- 6.1.19 Handling materials
- 6.1.20 Protection of the works during construction
- 6.2.1 Compliance
- 6.2.2 Provision of information
- 6.2.3 Design checking and certification
- 6.2.4 Load-bearing walls
- 6.2.5 Fixing the frame
- 6.2.6 Nails and staples
- 6.2.7 Sheathing
- 6.2.8 Differential movement
- 6.2.9 Fire resistance
- 6.2.10 Protection from moisture
- 6.2.11 Timber preservation
- 6.2.12 Vapour control layers
- 6.2.13 Breather membranes
- 6.2.14 Wall ties and fixings
- 6.2.15 Insulation
- 6.3.1 Compliance
- 6.3.2 Provision of information
- 6.3.3 Supporting load-bearing internal walls
- 6.3.4 Masonry walls
- 6.3.5 Load-bearing timber walls
- 6.3.6 Fire resistance
- 6.3.7 Sound insulation
- 6.3.8 Partitions: internal non load-bearing
- 6.3.9 Construction of timber partitions
- 6.3.10 Construction of steel framed partitions
- 6.3.11 Construction of proprietary systems
- 6.3.12 Plasterboard
- 6.3.13 Damp-proof courses
- 6.3.14 Components
- 6.4.1 Compliance
- 6.4.2 Provision of information
- 6.4.3 Upper floor design
- 6.4.4 Fire spread
- 6.4.5 Sound insulation
- 6.4.6 In-situ concrete floors and concreting
- 6.4.7 Precast concrete
- 6.4.8 Timber joist spans
- 6.4.9 Timber joists
- 6.4.10 Construction of timber floors
- 6.4.11 Joists supported by intermediate walls
- 6.4.12 Joists connected to steel
- 6.4.13 Joists into hangers
- 6.4.14 Timber joist and restraint strap
- 6.4.15 Strutting
- 6.4.16 Joists and openings
- 6.4.17 Multiple joists
- 6.4.18 Notching and drilling
- 6.4.19 Floor decking
- 6.4.20 Floating floors or floors between homes
- 6.5.1 Compliance
- 6.5.2 Design guidance
- 6.5.3 Steel grade and coatings
- 6.5.4 Installation and support
- 6.5.5 Padstones
- 6.5.6 Connections
- 6.5.7 Examples
- 6.6.1 Compliance
- 6.6.2 Provision of information
- 6.6.3 Fire precautions
- 6.6.4 Lighting
- 6.6.5 Glazing
- 6.6.6 Structural design
- 6.6.7 Headroom and width
- 6.6.8 Design of steps
- 6.6.9 Landings
- 6.6.10 Guarding
- 6.6.11 Handrails
- 6.6.12 Staircases made from timber and wood-based products
- 6.6.13 Concrete staircases
- 6.6.14 Steel staircases
- 6.6.15 Proprietary staircase units
- 6.6.16 Protection
- 6.7.1 Compliance
- 6.7.2 Provision of information
- 6.7.3 In-service performance
- 6.7.4 Timber doors and windows
- 6.7.5 Non-timber windows and doors
- 6.7.6 Installation
- 6.7.7 Glazing
- 6.7.8 Security
- 6.7.9 Ironmongery
- 6.7.10 Material storage and protection
- 6.7.11 Completed work
- 6.8.1 Compliance
- 6.8.2 Provision of information
- 6.8.3 Solid fuel – fireplaces and hearths
- 6.8.4 Solid fuel – combustion air
- 6.8.5 Solid fuel – flue pipes
- 6.8.6 Solid fuel – chimneys
- 6.8.7 Solid fuel – outlets and terminals
- 6.8.8 Gas – fireplaces and hearths
- 6.8.9 Gas – combustion air
- 6.8.10 Gas – flue pipes
- 6.8.11 Gas – chimneys
- 6.8.12 Gas – outlets and terminals
- 6.8.13 Oil – fireplaces and hearths
- 6.8.14 Oil – combustion air
- 6.8.15 Oil – flue pipes
- 6.8.16 Oil – chimneys
- 6.8.17 Oil – outlets and terminals
- 6.8.18 All – fireplaces and hearths
- 6.8.19 All – fireplace surrounds
- 6.8.20 All – flue pipes
- 6.8.21 All – flue liners
- 6.8.22 All – flues
- 6.8.23 All – chimneys
- 6.8.24 Masonry
- 6.8.25 Mortar
- 6.8.27 Flashings
- 6.8.28 Terminals
- 6.8.29 Flue testing
- 6.8.30 Further information
- 6.9.1 Compliance
- 6.9.2 Provision of information
- 6.9.3 Certification
- 6.9.4 Loads
- 6.9.5 Support and fixings
- 6.9.6 Durability
- 6.9.7 Interfaces
- 6.9.8 Insulation
- 6.9.9 Damp proofing and vapour control
- 6.9.10 Installation and tolerances
- 6.9.11 Electrical continuity and earth bonding
- 6.9.12 Maintenance
- 6.9.13 Glazing, gaskets and sealants
- 6.9.14 Cavity barriers and firestops
- 6.9.15 Ventilation screens
- 6.9.16 Handling and storage
- 6.9.17 Curtain walling
- 6.9.18 Rainscreen cladding
- 6.9.19 Insulated render and brick slip cladding
- 6.10.1 Compliance
- 6.10.2 Provision of information
- 6.10.3 Structural certification
- 6.10.4 Structural design of load-bearing floors and walls
- 6.10.5 Structural design of infill walls
- 6.10.6 Roofs
- 6.10.7 Steel and fixings
- 6.10.8 Detailing of steel joists
- 6.10.9 Restraint
- 6.10.10 Construction of load-bearing walls and external infill walls
- 6.10.11 Interfaces with staircases
- 6.10.12 Fixing floor decking and ceilings
- 6.10.13 Other design issues
- 6.10.14 Behaviour in relation to fire
- 6.10.15 Acoustic performance
- 6.10.16 Moisture control
- 6.10.17 Insulation
- 6.10.18 Vapour control layers
- 6.10.19 Breather membranes
- 6.10.20 Cladding, lining and sheathing boards
- 6.10.21 Wall ties
- 6.10.22 Services
- 6.10.23 Further information
- 6.11.1 Compliance
- 6.11.2 Provision of information
- 6.11.3 Weather conditions
- 6.11.4 Backgrounds
- 6.11.5 Accommodation of movement
- 6.11.6 Mixes
- 6.11.7 Detailing
- 6.11.8 Render onto board backgrounds
- 6.11.9 Finishes
- 7.1.1 Compliance
- 7.1.2 Provision of information
- 7.1.3 Flat roof, terrace and balcony general design
- 7.1.4 Drainage
- 7.1.5 Flat roof, terrace and balcony structural design
- 7.1.6 Timber structure and deck
- 7.1.7 Concrete decks
- 7.1.8 Profiled self-supporting metal decks
- 7.1.9 Profiled self-supporting metal roofing
- 7.1.10 Thermal insulation and vapour control
- 7.1.11 Waterproofing layer and surface treatments
- 7.1.12 Green and biodiverse (brown roofs) – including roof gardens
- 7.1.13 Blue roofs
- 7.1.14 Raised Podium
- 7.1.15 Detailing of flat roofs
- 7.1.16 Accessible thresholds and upstands
- 7.1.17 Parapets and guarding to terraces and balconies
- 7.2.1 Compliance
- 7.2.2 Provision of information
- 7.2.3 Design of pitched roofs
- 7.2.4 Protection of trusses
- 7.2.5 Durability
- 7.2.6 Wall plates
- 7.2.7 Joints and connections
- 7.2.8 Restraint
- 7.2.9 Bracing for trussed rafter roofs
- 7.2.10 Strutting for attic trusses and cut roofs that form a floor
- 7.2.11 Support for equipment
- 7.2.12 Access
- 7.2.13 Dormer construction
- 7.2.14 Underlay and sarking
- 7.2.15 Ventilation, vapour control and insulation
- 7.2.16 Firestopping and cavity barriers
- 7.2.17 Battens
- 7.2.18 Roof coverings
- 7.2.19 Fixing tiles and slates
- 7.2.20 Weathering details
- 7.2.21 Valleys and hidden gutters
- 7.2.22 Drainage
- 7.2.23 Fascias and trim
- 7.2.24 Spandrel panels in cold roofs
- 8.1.1 Compliance
- 8.1.2 Provision of information
- 8.1.3 Water services and supply
- 8.1.4 Cold water storage
- 8.1.5 Hot water service
- 8.1.6 Soil and waste systems
- 8.1.7 Electrical services and installations
- 8.1.8 Gas service installations
- 8.1.9 Meter Boxes
- 8.1.10 Space heating systems
- 8.1.11 Installation
- 8.1.12 Extract ducts
- 8.1.13 Testing and commissioning
- 8.2.1 Compliance
- 8.2.2 Provision of information
- 8.2.3 Clean Air Act
- 8.2.4 System design
- 8.2.5 Access
- 8.2.6 Handling, storage and protection
- 8.2.7 Sequence of work
- 8.2.8 Location
- 8.2.9 Building integration
- 8.2.10 Fixing
- 8.2.11 Electrical installation requirements
- 8.2.12 Pipes, insulation and protection from cold
- 8.2.13 Ground collectors
- 8.2.14 Fuel storage
- 8.2.15 Safe discharge
- 8.2.16 Testing and commissioning
- 8.2.17 Handover requirements
- 8.2.18 Further information
- 8.3.1 Compliance
- 8.3.2 Provision of information
- 8.3.3 Building integration
- 8.3.4 Noise
- 8.3.5 Design considerations
- 8.3.6 Access and operation
- 8.3.7 Ductwork
- 8.3.8 Fixing and jointing of ductwork
- 8.3.9 Commissioning and balancing
- 8.3.10 Handover requirements
- 9.1.1 Compliance
- 9.1.2 External walls
- 9.1.3 Internal walls and ceilings
- 9.1.4 Doors and windows
- 9.1.5 Floors
- 9.1.6 Glazing
- 9.1.7 Ceramic, concrete, terrazzo and similar tile finishes
- 9.1.8 Fitted furniture
- 9.1.9 Joint sealants
- 9.1.10 Paint finishes
- 9.1.11 Sanitary ware
- 9.1.12 Other surfaces and components
- 9.1.13 Pitched roof coverings
- 9.1.14 Garages
- 9.1.15 External works
- 9.2.1 Compliance
- 9.2.2 Provision of information
- 9.2.3 Plastering
- 9.2.4 Dry lining
- 9.2.5 Ceramic wall tiling
- 9.3.1 Compliance
- 9.3.2 Provision of information
- 9.3.3 Insulation
- 9.3.4 Screed
- 9.3.5 Ceramic, concrete, terrazzo and similar tile finishes
- 9.3.6 Wood finishes
- 9.3.7 Flexible sheet and tile finishes
- 9.3.8 Asphalt finishes
- 9.3.9 Staircase finishes
- 9.4.1 Compliance
- 9.4.2 Provision of information
- 9.4.3 General provisions – cupboards and fitments
- 9.4.4 Finishings and internal trim
- 9.4.5 Joinery
- 9.4.6 Airing cupboards, cupboards, worktops and fitments
- 9.4.7 Ironmongery, prefabricated items and other materials
- 9.4.8 Protection and handover
- 9.5.1 Compliance
- 9.5.2 Provision of information
- 9.5.3 Storage
- 9.5.4 Conditions for painting and decorating
- 9.5.5 Timber
- 9.5.6 Steel
- 9.5.7 Walls
- 9.5.8 Wallpapering
- 9.5.9 Other surfaces
- 9.5.10 Completed painting and decorating
- 10.1.1 Compliance
- 10.1.2 Provision of information
- 10.1.3 Garage foundations
- 10.1.4 Garage floors
- 10.1.5 Garage walls
- 10.1.6 Resistance to fire spread
- 10.1.7 Security
- 10.1.8 Doors and windows
- 10.1.9 Garage roofs
- 10.1.10 Permanent prefabricated garages and carports
- 10.1.11 Services
- 10.2.1 Compliance
- 10.2.2 Provision of information
- 10.2.3 Stability
- 10.2.4 Freestanding walls and retaining structures
- 10.2.5 Guarding and steps
- 10.2.6 Drives, paths and landscaping
- 10.2.7 Materials
- 10.2.8 Garden areas within 3m of the home
- 10.2.9 Garden areas
- 10.2.10 Timber decking
- 10.2.11 Landscaping
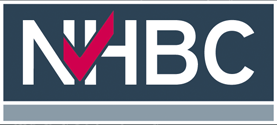
Foundations
4.2 building near trees, this chapter gives guidance on meeting the technical requirements when building near trees, hedgerows and shrubs, particularly in shrinkable soils., introduction.
The combination of shrinkable soils and trees, hedgerows or shrubs represents a hazard to structures that requires special consideration. Trees, hedgerows and shrubs take moisture from the ground and, in cohesive soils such as clay, this can cause significant volume changes resulting in ground movement. This has the potential to affect foundations and damage the supported structure. In order to minimise this risk, foundations should be designed to accommodate the movement or be taken to a depth where the likelihood of damaging movement is low.
This chapter gives guidance for common foundation types to deal with the hazard and includes suitable foundation depths which have been established from field data, research, NHBC data and practical experience. The depths are not those at which root activity, desiccation and ground movement are non-existent, but they are intended to provide an acceptable level of risk. However, if significant quantities of roots are unexpectedly encountered in the base of the trench, the excavation may need to be deepened.
The interaction between trees, soil and buildings is dependent on many factors and is inherently complex. The relationship becomes less predictable as factors combine to produce extreme conditions. These are signified by the need for deeper foundations. Depths greater than 2.5m indicate that conditions exist where prescriptive guidance is less reliable.
The services of a specialist arboriculturalist may be helpful for the identification of the type and condition of trees that may affect building work. This includes trees both on and adjacent to the site.
Consideration has been given to the potential effects of climate change in the guidance provided.
The following situations are beyond the scope of the guidance in this chapter and will require a site-specific assessment by an engineer (see Technical Requirement R5):
- foundations deeper than 2.5m within the influence of trees
- ground with a slope of greater than 1 in 7 (approximately 8°) and man-made slopes such as embankments and cuttings
- underpinning.
NHBC Mobile App – Foundation Depth Calculator
NHBC Risk Guide - Heave precautions
Technical Extra 10 - Foundation Depth Calculator App
Technical Extra 18 - Foundation defects under the spotlight
Technical Guidance - Strip/trench fill foundations - slip membrane
NHBC Standards 2023 Complete
NHBC Standards 2023 Chapter 4
Share this page via email
Na Ulitse Yalagina 13B Apartments
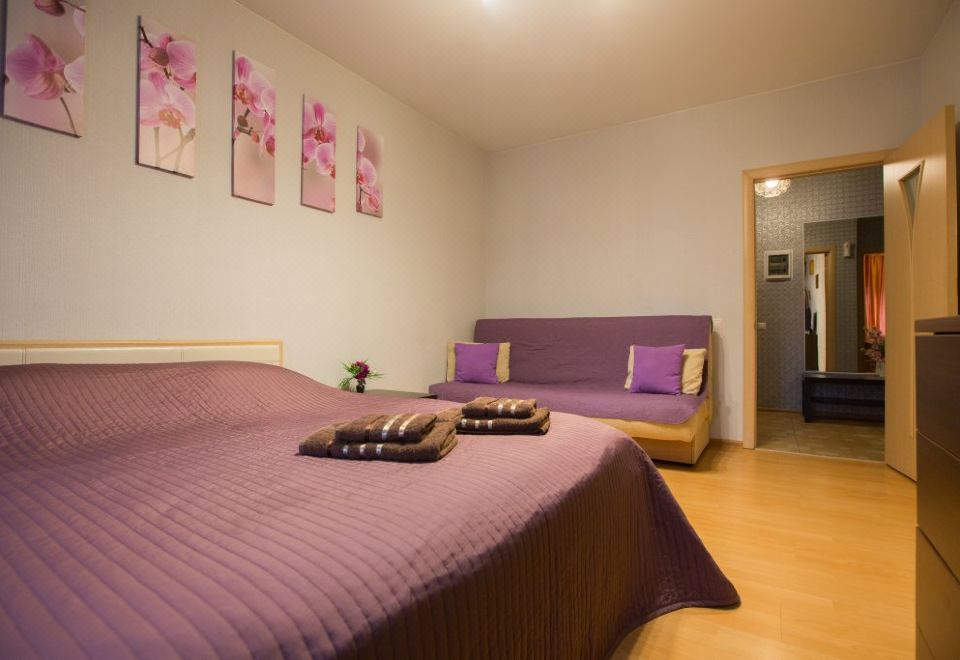
Property Policies
Frequently asked questions, how much does it cost to stay at na ulitse yalagina 13b apartments, what are the check-in and check-out times at na ulitse yalagina 13b apartments, does na ulitse yalagina 13b apartments provide airport transfer services, what amenities and services does na ulitse yalagina 13b apartments have, does na ulitse yalagina 13b apartments have a swimming pool, does na ulitse yalagina 13b apartments have fitness amenities, does na ulitse yalagina 13b apartments provide wi-fi, does na ulitse yalagina 13b apartments have non-smoking rooms, does na ulitse yalagina 13b apartments have a restaurant, is parking available at na ulitse yalagina 13b apartments, popular hotels, popular attractions, explore more.
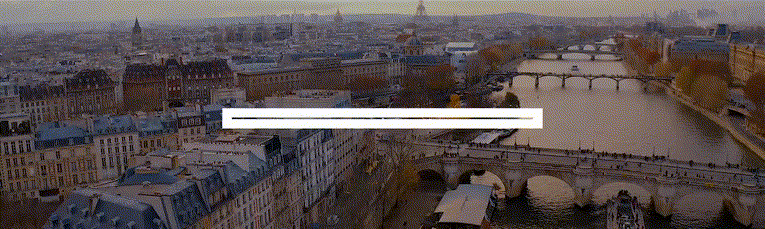
IMAGES
VIDEO
COMMENTS
n Unequal risers can create a trip hazard. n Approved Document K (England & Wales), Scottish Building Standards Technical Handbook Domestic Section 4.3 and Building Regulations (Northern Ireland) Technical Handbook H, require all risers to be equal. ... NHBC, NHBC House, Davy Avenue, Knowlhill, Milton Keynes, Bucks MK5 8FP. Tel: 0344 633 1000
NATIONAL STANDARDS FOR THE PHYSICAL INSPECTION OF REAL ESTATE U.S. DEPARTMENT OF HOUSING AND URBAN DEVELOPMENT Page 2 of 9 DEFICIENCY 1 - UNIT: TRIP HAZARD ON WALKING SURFACE. DEFICIENCY CRITERIA: There is an abrupt change in vertical elevation or horizontal separation on any walking surface along the normal path of travel, consisting of the following criteria:
Nosings with a raised edge, designed to accommodate floor finishes such as carpet or vinyl flooring, can create a trip hazard until the flooring is inserted and are therefore not acceptable without the flooring. ... NHBC, NHBC House, Davy Avenue, Knowlhill, Milton Keynes, Bucks MK5 8FP. Tel: 0344 633 1000 ...
10.2.6 Drives, paths and landscaping. Appropriate access (including private roads, shared private drives, private drives, car parking and paths) shall be provided to and around the home. Issues to be taken into account include: general construction considerations. drainage. construction details. minimum sub-base thickness. house paths and patios.
nstep profiles should be designed to avoid tripping hazards (for example, no contrasting nosings). Thhe objoTctoi eojvofiastacr oqo o tuessacr For further advice, please contact an NHBC surveyor on 0844 633 1000 and ask for 'Building Control'. Entrance to curtilage or point of alighting from vehicle Access level 20 1 Diagram 2 - Plot gradient
For technical advice and support, call 01908 747384 or visit www.nhbc.co.uk NHBC STANDARDS Pitched roofs - is standard bracing acceptable? REQUIREMENTS (CONTINUED) House builders are generally constructing buildings with a roof span of between 6 and 10 metres, and therefore, unless the duo roof pitch is 30° or greater,
4.1.5 Basic Investigation (sites where hazards are not identified or suspected) 4.1.6 Detailed Investigation (sites where hazards are identified or suspected) 4.1.7 Managing the risks (sites where hazards are found) 4.1.8 Unforeseen hazards; 4.1.9 Documentation and verification; 4.1.10 Guidance for investigations; 4.1.11 Further information
The NHBC Standards contain the Technical Requirements, performance standards and guidance for the design and construction of homes acceptable to NHBC. The home is defined in NHBC Rules for builders and developers registered with NHBC. The Standards come into effect for every NHBC registered home whose foundations are begun on or after 1 January ...
Site fixing of stairs should be in accordance with Building Regulations, NHBC Standards and any referenced documents with particular attention to the BWF Installation Guide and the following: ... to suit skirting height and/or cut to not project into a passageway causing a trip hazard. Refer to the above-mentioned BWF Fixing Guide for guidance ...
NHBC, NHBC House, Davy Avenue, Knowlhill, Milton Keynes, Bucks MK5 8FP. Tel: 0344 633 1000 NHBC is authorised by the Prudential Regulation Authority and regulated by the Financial Conduct Authority and the Prudential Regulation Authority. Created Date:
(sites where hazards are not identified or suspected) 05 4.1.6 Detailed Investigation (sites where hazards are identified or suspected) 05 4.1.7 Managing the risks (sites where hazards are found) 06 4.1.8 Unforeseen hazards 07 4.1.9 Documentation and verification 07 4.1.10 Guidance for investigations 07 4.1.11 Further information 08
NATIONAL STANDARDS FOR THE PHYSICAL INSPECTION OF REAL ESTATE U.S. DEPARTMENT OF HOUSING AND URBAN DEVELOPMENT Page 2 of 4 DEFICIENCY 1 - UNIT: TRIP HAZARD ON WALKING SURFACE. DEFICIENCY CRITERIA: There is an abrupt change in vertical elevation or horizontal separation on any walking surface along the normal path of travel, consisting of the following criteria:
That means preventing slips, trips, and falls is an ongoing process that relies heavily on employees being able to recognize related hazards. What Are OSHA's Trip Hazard Regulations? OSHA's primary standard for slip, trip, and fall hazards is the General Industry Walking-Working Surface standard (29 CFR 1910 Subpart D, which includes §1910.21-30).
A drip edge is required at the front drainage edge of most balcony scenarios. This component is deemed crucial to fulfil the latest NHBC 2024 standards as it is aims at preventing water from dripping onto the guarding of the balcony below. It's an essential consideration that serves to protect lower balconies in a stack or the building's ...
NATIONAL STANDARDS FOR THE PHYSICAL INSPECTION OF REAL ESTATE U.S. DEPARTMENT OF HOUSING AND URBAN DEVELOPMENT Page 2 of 5 DEFICIENCY 1 - UNIT: TRIP HAZARD ON WALKING SURFACE DEFICIENCY CRITERIA: There is an abrupt change in vertical elevation or horizontal separation on any walking surface along the normal path of travel, consisting of the following criteria:
In industries where the risk of trip and fall hazards is substantial, strict regulations exist to safeguard employees. The fines for non-compliance can be hefty, but more importantly, adherence to these rules saves lives and prevents injuries. Below are the key OSHA-mandated practices your organization needs to have in place to prevent falls ...
4.1.5 Basic Investigation (sites where hazards are not identified or suspected) 4.1.6 Detailed Investigation (sites where hazards are identified or suspected) 4.1.7 Managing the risks (sites where hazards are found) 4.1.8 Unforeseen hazards; 4.1.9 Documentation and verification; 4.1.10 Guidance for investigations; 4.1.11 Further information
In 1938, it was granted town status. [citation needed]Administrative and municipal status. Within the framework of administrative divisions, it is incorporated as Elektrostal City Under Oblast Jurisdiction—an administrative unit with the status equal to that of the districts. As a municipal division, Elektrostal City Under Oblast Jurisdiction is incorporated as Elektrostal Urban Okrug.
Apelsin Hotel. 43 reviews. #1 of 4 hotels in Elektrostal. Noginskoye hwy, 36B, Elektrostal 144008 Russia. Write a review. Check availability. View all photos ( 19)
Explore Elektrostal' with Trip.com's comprehensive travel guide. Discover the city's top attractions, best local dishes, essential travel tips, and hidden gems. Get insights from real travelers' reviews and make the most of your visit.
The following situations are beyond the scope of the guidance in this chapter and will require a site-specific assessment by an engineer (see Technical Requirement R5): foundations deeper than 2.5m within the influence of trees. ground with a slope of greater than 1 in 7 (approximately 8°) and man-made slopes such as embankments and cuttings.
Na Ulitse Yalagina 13B Apartments. Region, Elektrostal, ulitsa Yalagina, 13Б, Elektrostal', Moscow region, Russia. LocationIf you want to feel like you're at home no matter where you are, choose this — apartment «Na Ulitse Yalagina 13A Apartments» is located in Elektrostal. This apartment is located in 3 km from the city center.