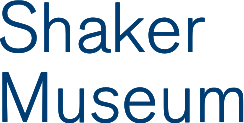
- Past Exhibitions
- Work With Us
- Mount Lebanon Historic Site
- Capital Campaign
- Press Releases
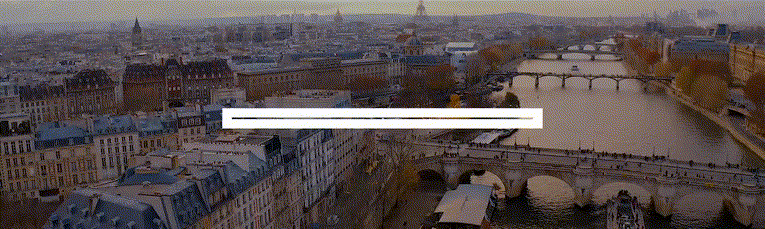
Shaker Museum
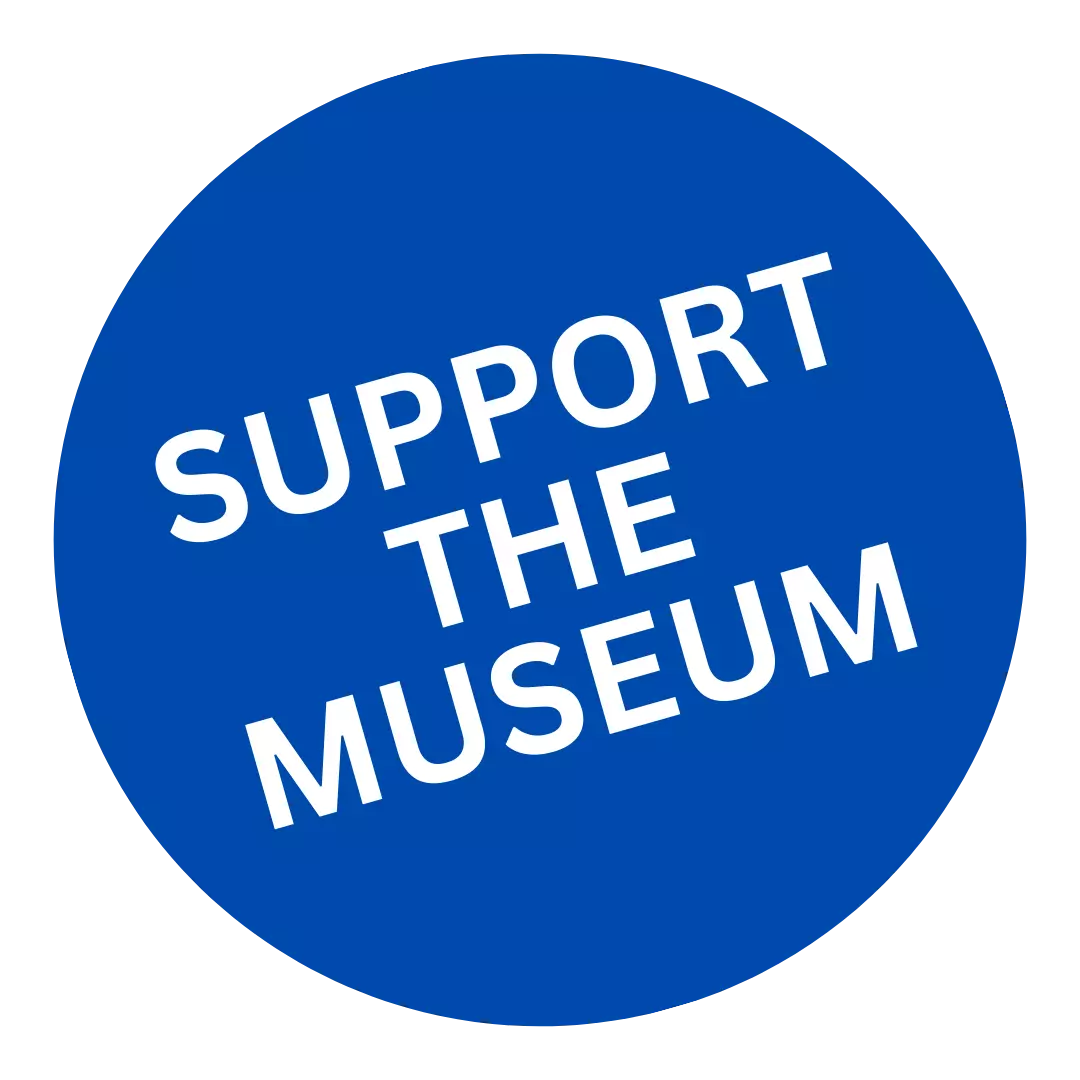
Trip Hammer on xhibition at the Shaker Museum, Old Chatham, NY, ca.1985, Shaker Museum | Mount Lebanon. Paul Rocheleau, photographer.
Nov 23, 2016
A four ton trip hammer.
- Church Family
- water power
In the winter of 1846 the First and Second Order of the Church Family determined to build a new blacksmith shop, one of stone with waterpower that would operate a lathe, drilling works, a grindstone, bellows for the forge, and a trip hammer. The shop was to be built 34 feet by 44 feet and […]
Forge, Center Family, Mount Lebanon, NY, 2016, Shaker Museum | Mount Lebanon. Staff photograph.
In the winter of 1846 the First and Second Order of the Church Family determined to build a new blacksmith shop, one of stone with waterpower that would operate a lathe, drilling works, a grindstone, bellows for the forge, and a trip hammer. The shop was to be built 34 feet by 44 feet and located in the corner of the Deming Lot at the northeast corner of the land bordered by the main road that ran through the village (now called Darrow Road) and the road that runs downhill to the Shaker gristmill (now called Ann Lee Lane on the east end and Cherry Lane on the west end). The shop still stands and is now a private residence. The 1845 Shakers’ census notes that there were three blacksmiths in what is now called the Center Family – Brothers Arba Noyes, James Vail, and George Long.
Construction was largely done by members of the Second Order with considerable help from hired Irish laborers who did much of the digging for the pit for the waterwheel and laid up most of the stonework. By mid-summer the wheel pit, the drain to carry away water from the wheel, and the masonry work were completed. In the early fall, the hired labor returned to build the dam to create the pond to supply water to power the shop. The dam is still standing and pond is on the east side of the road.
Interior of the Church Family Forge with the Trip Hammer in its Original Location, Center Family, Mount Lebanon, NY, 1940, Shaker Museum | Mount Lebanon. John S. Williams, Sr., photographer.
The decision to include a trip hammer in their new blacksmith’s shop was bold, but one that greatly increased the Shakers’ ability to fabricate and manufacture items out of iron. Trip hammers of many designs have been used for a couple of thousand years. The basic principle is that some kind of power is applied, in some manner, to raise a hammer larger than can be lifted by a man so that when it is dropped it will come down with more force than a man can exert alone. Trip hammers, in addition to forging iron, have been used for hulling and grinding grain, pounding rags for papermaking, and crushing iron ore to make it easier to extract the metal from the rock. In blacksmithing, trip hammers are often used to draw out flat sheets of metal from an iron bar and to shape a piece of square iron rod, for instance flattening the end of an iron bar to make a shovel and or making round ends on a square bar to make an axel for a wagon.
The Shakers documented their new trip hammer in their journals. In January 1846, Center Family Elder Amos Stewart experimented with a model for a windmill, hoping that he could use wind power “to tilt a triphammer.” This attempt, although it would have saved building a dam for the shop, apparently failed. The next month, Brother Hiram Rude, the family mechanic, went to Lee, Massachusetts to see a “gang of Triphammers.” The Shakers frequently went to visit businesses and factories to stay abreast of new technologies. Apparently in the next few weeks a design for the hammer was drawn up and casting patterns made for the metal parts. Elder Amos and Brother Peter went to Albany to see about castings for the gearing for the hammer. It was nine months later – after the new shop was finished and its forge fired up – that Elder Amos and Brother Braman Wicks, a carpenter from the Church Family, began working again on the gearing to drive the hammer. In July, a tree was cut for the frame to hold the hammer. Apparently by winter that year the Shakers were rethinking the design of the trip hammer. Elder Amos and Brother Hiram went to Cohose, New York, to look at another trip hammer and two days after that trip they had settled “upon the form for a Hammer & spoke for castings in Troy.” This final design was completed and the trip hammer seemed to be in use shortly after that.
While trip hammers were associated primarily with iron work, the Shakers appeared to have another idea for using it quite early on – maybe even before they began planning to built it: pounding black ash logs to break down the bond between the tree’s natural growth rings. When the growth rings are separated, they are easily peeled off in long strips and become the treasured materials from which baskets are woven. Most basket makers would do this work by pounding a log with a sledge hammer. For the Shakers, the ability to more efficiently produce basket weaving material meant that they could greatly increase their production of all kinds of baskets. In November of 1847, Elder Daniel Boler of the Church Family worked “at the blacksmith shop preparing trip hammer for pounding out basket stuff.” The Shakers were so dependent on having basket materials prepared by machine that in 1863, when apparently their own trip hammer was not available, they took ash logs to Bromley King’s forging shop in Waterford, New York, to get them pounded.
This trip hammer is among the largest and heaviest non-architectural objects made by the Shakers. It is over fifteen feet long, six and a half feet high, just over four feet wide, and is thought to weigh around four tons. The machine has two hammers – a large one at one end and a small one at the other end. It was powered by a waterwheel connected by a belt to the wooden drive pulley. Once the hammer got up to speed and the massive cast iron flywheel was rotating to preserve its inertia, one or both hammers could be engaged.
Watch a trip hammer demonstration from Thomas Ironworks, Seville, Ohio
Interior of the Blacksmith’s Shop Exhibition at the Shaker Museum, Old Chatham, NY, ca. 1955, Shaker Museum | Mount Lebanon. C. E. Simmons, photographer.
Shaker Museum | Mount Lebanon’s acquisition of the trip hammer has some tales and legends associated with it. In the 1940s John S. Williams, Sr., the museum’s founder, heard that the Shakers were breaking up the equipment in the blacksmith’s shop in preparation for selling the building. He appealed to have the work stopped until he could move the hammer and the forge and bellows to the museum. It was war-time in America and the scarcity of trucks made it difficult to find someone who could move such a heavy piece of equipment. Fortunately, Williams’s good friend Albert Callan, the owner of the Chatham Courier newspaper, had a new printing press being delivered around this time and once the delivery of the press was complete the truck headed to Mount Lebanon to move the trip hammer. Once loaded, they then had to find a route back to the Museum that did not involve crossing a bridge that could not bear the weight of the truck and hammer. Somehow it all worked out and the trip hammer has been at the Shaker Museum ever since.
FOLLOW BLOG VIA EMAIL
- 518.794.9100
- [email protected]
Sign up for our newsletter
- Privacy Policy
- Terms of Service
- PO Box 328, Chatham, NY 12037
- Shaker Museum © 2023 All Rights Reserved.
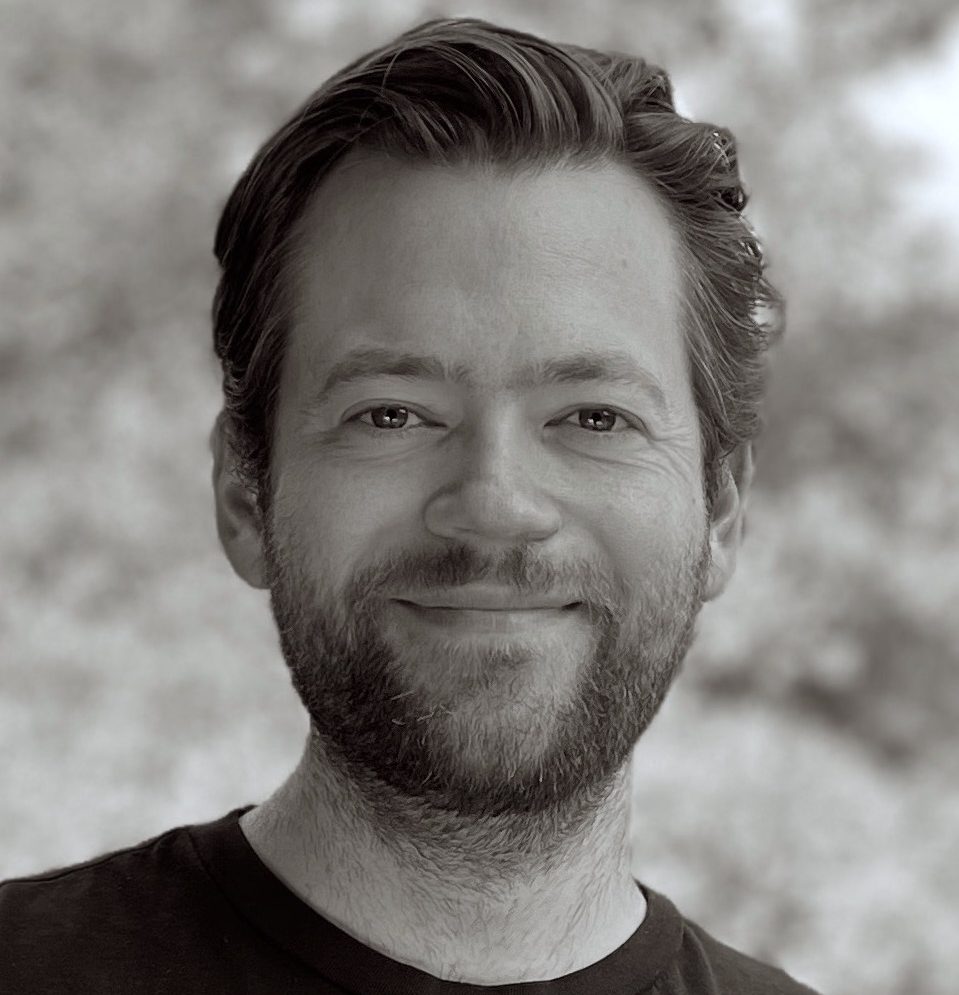
Shane Rothe
Curatorial Associate
Shane Rothe (they/them) joined Shaker Museum in July 2023, working with independent curator Maggie Taft on an exhibition for the new museum space in Chatham. Shane is an artist as well as a curator and continues to create in the mediums of painting, sculpture, writing, and performance. Shane holds a BFA from CalArts and an MA in art history and curatorial studies from the University of Chicago.
- The Fabricator
- Canadian Metalworking
- Our Publications
- E-Newsletter
- Digital Edition
- The Tube and Pipe Journal
- The Fabricator en Español
- Additive Manufacturing
- Aluminum Welding
- Arc Welding
- Assembly and Joining
- Automation and Robotics
- Bending and Forming
- Consumables
- Cutting and Weld Prep
- Electric Vehicles
- Hydroforming
- Laser Cutting
- Laser Welding
- Manufacturing Software
- Materials Handling
- Metals/Materials
- Oxyfuel Cutting
- Plasma Cutting
- Power Tools
- Punching and Other Holemaking
- Roll Forming
- Shop Management
- Testing and Measuring
- Tube and Pipe Fabrication
- Tube and Pipe Production
- Waterjet Cutting
Industry Directory
- Search the Directory (Showrooms)
- Buyers' Guides and Directories
- Product Showcases
- Classified Ads
- Register for the Directory
Our Affiliated Brands
- Fabricators and Manufacturers Association
- Nuts, Bolts & Thingamajigs Foundation
Account Login
- From The Fabricator
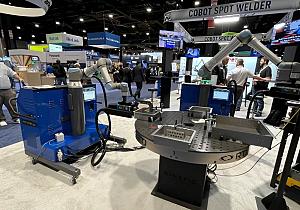
A visit to Automate 2024 reveals the future might be now
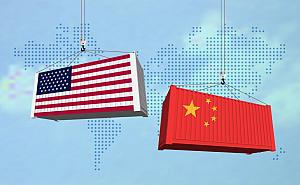
White House considers China tariff increases on materials
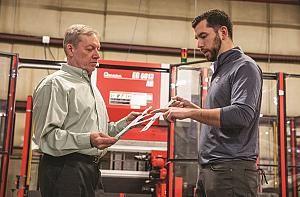
A deep dive into a bleeding-edge automation strategy in metal fabrication
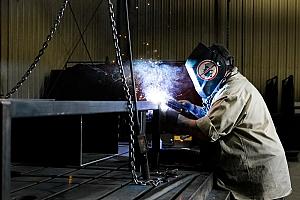
Young fabricators ready to step forward at family shop
- From The Welder
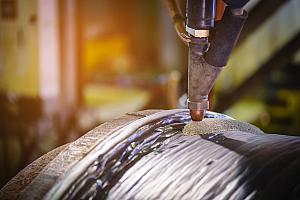
The role of flux in submerged arc welding performance
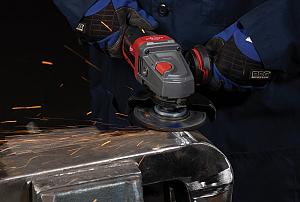
How welders can stay safe during grinding
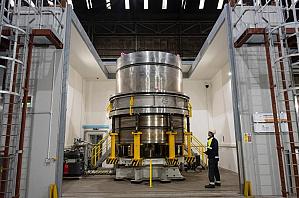
Sheffield Forgemasters makes global leap in welding technology
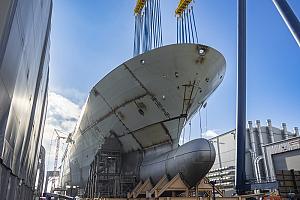
Launching a fleet revival at Seaspan shipyard
- From The Tube and Pipe Journal
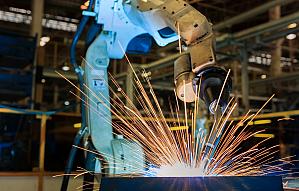
Making the move from hard automation to robotic welding
Fabricator achieves extraordinary with simple approach
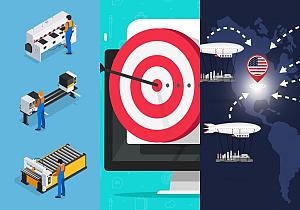
Three big issues fabricators must prioritize in 2024
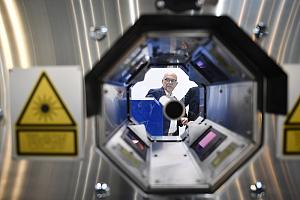
Tube 2024 to feature first-ever events
- From The Fabricator en Español
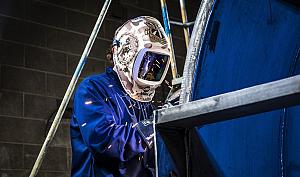
Seguridad en la soldadura desde el inicio
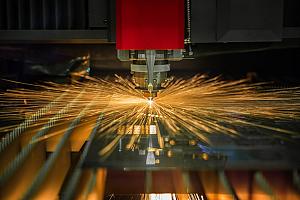
Anidado para la estabilidad del corte láser
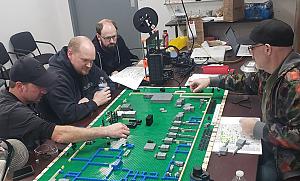
Prescripción para la reducción del desperdicio: arreglo esbelto de las instalaciones
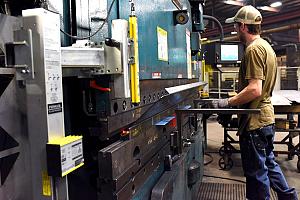
Los operadores de prensa dobladora inexpertos hacen indispensable el repensar la seguridad
Fabricators and their power hammers, here’s an overview of the brawny tool by the people who use it.
- By Jeffrey Dean
- June 2, 2016
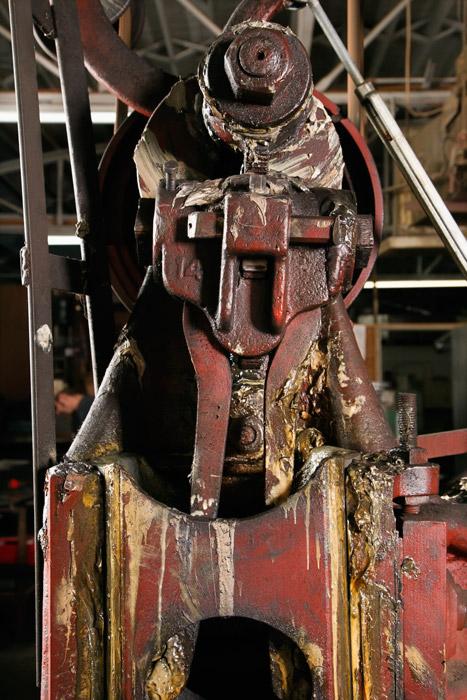
Figure 1 Power hammers are among the oldest metal fabricating tools known to man. They just happen to be smaller today than they were several hundred years ago.
There’s no mystery to the allure of a power hammer. It’s loud and powerful, while also emitting a whiff of implied danger.
Then there’s the power hammer’s practical side. It does the work of two stout men with 5-lb. sledges or 5-oz. planishing hammers. (Yes, they can be that delicate.) They hit hard and accurately. You can use one for a forge weld, or even as a quick-release vise for twists.
The idea of a power hammer goes back to antiquity. Records indicate that the Chinese employed them as early as 200 B.C. Power hammers were part of Europe’s industrial landscape as early as the 12th century. Of course, those were more correctly called trip hammers, and they worked like hefty blunt guillotines. A series of mechanical pulleys, gears, and cams hoisted the heavy hammer aloft, from where it was released. Gravity did the rest. Some of these hammers were immensely heavy. Typically, steam- or water-powered wheels provided the horsepower to raise the hammer back to its high position.
The flaw in this system was that the power of these early power hammers was directly related to their weight. In theory, at least, there was no limit to how heavy a hammer could be. The other part of the equation was that you still needed a way to lift it. So most trip hammers, except for a few wonder-of-the-world oddities, were kept to reasonable weights that wouldn’t exceed the capacity of the average steam engine, water wheel, or yoke of oxen or peasants.
The advent of the true power hammer solved the weight-lifting problem. It was an innovation that multiplied the hammer’s oomph by accelerating its downward motion. This meant that a power hammer could deliver the power of a trip hammer at a fraction of the size and weight. While no one man is credited with its invention, the power hammer began to find increased use across industrialized Europe around the end of the 18th century. By the mid-1800s, the power hammer totally eclipsed the trip hammer.
The earliest specimens were big boys, to be sure, used mainly for forging massive parts for locomotives and ships. However, the downsizing trend continued, and the first part of the 20th century saw power hammers (see Figure 1 ) that were small enough to fit into the average smithy or fabrication shop. Some were steam-powered, but electrical motors drove the majority of them.
Today’s power hammers fall into one of three categories: mechanical, utility, and self-contained. This might be a good time to mention that all power hammers are designated by relative hammer weight. That is, their relative size describes the weight of the actual striking surface plus everything behind it, including the ram, piston, levers, and gears that power and guide the hammer. The truth is, though, this is a frivolously arbitrary system. No two manufacturers make their hammers with the same hammer actuating system. So only two hammers with a shared factory birth could actually be compared to each other in terms of hammer weight. Still, the nomenclature works on a rough level for comparisons.
Mechanical Hammers: The Little Machines That Could
Mechanical power hammers are powered by an electric motor. They typically run smaller, with a narrower throat. This limits the type of work they can do because the smaller opening precludes the use of tools and dies. But for drawing metal down, they are demons.
These are the machines that first appeared in blacksmith shops at the dawn of the 20th century. If you see one today, chances are it’s a Little Giant. Some of the first ones ever built remain in service.
“Mechanical hammers were designed mainly to resharpen and re-edge agriculture tools,” said Ralph Sproul of Bear Hill Blacksmith in New Hampshire.

Figure 2 This original manufacturer’s warning plate on this power hammer reminds the operator of the power of the tool being used. Photo courtesy of Artisan Iron.
Indeed, that is precisely what Trenton Tye uses his 100-lb. Mayer hammer for. Tye, who owns Purgatory Ironworks in Morgan, Ga., is a well-known reforger of peanut blades. A peanut blade is the ground-level component of an agricultural implement for harvesting the nation’s multimillion-dollar crop of goobers.
Mayer hammers share DNA with the Little Giant, both having been developed by the eponymous Mayer brothers of Mankato, Minn.
Dave Court, who runs Bay Hill Forge in New Hampshire, has a 50-lb. Little Giant among his collection of power hammers.
“It was cast in 1910,” Court said. “I have its pedigree. It was shipped to Littleton, N.H., in 1911. I’ll put it against any hammer in America.”
While limited in throat space, Court’s Little Giant does have room for stroke adjustment.
“With the flywheel on it, you can get a single precise blow or [repetitive blows] like a machine gun. And it’s very accurate,” he said. A cone clutch, a hallmark of the Little Giant, makes the machine self-aligning.
The Little Giant was more than enough for the production work Court was turning out back when he was doing only hardware. But he readily conceded that his larger power hammers have capabilities that the mechanical hammers can’t touch.
“You can always do little work with a big hammer, but you can’t do big work with a little hammer,” he said.
Utility Power Hammers: Bring Your Own Air
Think of utility hammers as the stripped-down versions of air hammers. You supply your own compressor.
Elmer Roush of California runs three hammers, two of which are utility types, a Trip Air and a Big Blu. He powers them with three 5-HP, two-stage compressors. The three motors feed a manifold with a single pipe to feed the hammer in use. (Maybe it’s a California thing: most fabricators simply use one compressor.) It generally takes between 20 and 25 cubic feet per minute (CFM) to drive a power hammer of 120 lbs., for which a 5- or 8-HP compressor works nicely.
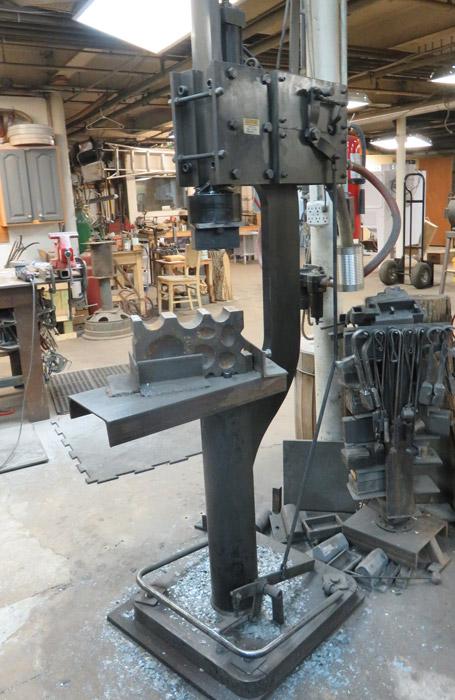
Figure 3 The utility hammer at the Ball & Chain Forge has enough daylight to accommodate an 8-inch swedge. Photo courtesy of the Ball & Chain Forge, Portland, Maine.
Ray Ciemny of Artisan Iron, Groton, Mass., uses a 10-HP Speedaire machine to run his 125-lb. Bull hammer (see Figure 2 ).
“You need big CFMs. That’s the key with these things. And you run all the valves and pipes open wide. You can’t choke anything down,” he said.
Ciemny bought the hammer when his 30-lb. Bradley mechanical hammer was limiting him for the production work he was getting into.
“I found the Bull hammer in North Carolina. It came with a factory plate that said, ‘Engage brain before operating this machine.’ The hammer was [made by] a quirky husband and wife inventor couple,” Ciemny said. That couple, Tom Troszak and Denise Mills, today makes a power hammer under the name Phoenix Hammers.
Ciemny bought his hammer more than 10 years ago.
“The throat is about 11 inches,” said Ciemny, “so you can use it with normal blacksmithing top tools.”
The ample throat is not the only thing Ciemny likes about the Bull hammer. The dies are held by just two bolts, making them fast and easy to change. And it’s a relatively compact machine, weighing just 650 lbs.
Bob Menard, who runs the Ball & Chain Forge in Portland, Maine, also avails himself of the Bull hammer’s compactness.
“I don’t have clearance for a big hammer, and [for its size] this one hits like a ton of bricks,” he said.
As is typical of most air hammers, Menard’s hammer (see Figure 3 ) has a wide open throat.
“It’s got 14 in. of daylight. I can fit 12- by 8-in. swage block on its 8-in. side in there,” he added. Menard runs the power hammer with a 7.5-HP compressor with an 80-gal. tank. It puts out about 18 CFM, according to Menard, who spends most of his time working on railings and gates.
Self-contained Power Hammers: Big Iron for Serious Ironwork
Those that don’t want to bother with acquiring a dedicated compressor have another option: self-contained power hammers.
A step up from the utility hammer, the self-contained hammer has its own built-in air compressor and tank. Like the utility hammers, these hammers have a lot of daylight between the workpiece and the business end of the ram. You can fit all manner of hand tools and dies in the typically 12- to 14-in. throat.
Self-contained hammers are hefty boys. They are usually in the upper size range of power hammers found in a fabrication shop. Of course, not all shops have hammers the size of Ralph Sproul’s.
Sproul, so the story goes, got a call from a friend in Minnesota, who had heard about an old Nazel in Everett, Mass., and wanted Sproul to take a look at it for him. But when Sproul locked eyes on the machine, he was smitten. The power hammer, which had been built in 1906 and done three-shift duty during two wars, was sitting in a maintenance shop in a state of advanced decrepitude.
When Sproul asked shop personnel to fire up the pile of junk and asked them for a piece of scrap steel, the guys cracked wise. But when he used that 12,000-lb. tool to transmogrify the steel into a delicate leaf pattern complete with stem, the shop personnel sobered right up. Sproul offered his friend $4,000 and promptly had the leviathan shipped to his shop in New Hampshire.
Sproul is not the only fan of self-contained hammers. While Tye does use a mechanical hammer for a lot of his work, his go-to hammer is a 110-lb. Sahinler self-contained hammer. Roush considers his 100-lb. Sahinler his primary hammer.
Bigger Is Smoother
Aside from the convenience of a built-in compressor, the greater mass of the self-contained hammer is an advantage. In short, the mass of the machine absorbs vibration. Less vibration means less maintenance. It also means more comfort for an operator by dampening the unpleasant sensation that’s transferred through the workpiece to the forearm.
You could liken the vibration to the recoils that a light and a heavy firearm generate. Court called it “white knuckle disease,” technically referred to as hand-arm vibration syndrome (HAVS). Research both here and in the U.K. has implicated power hammers as a suspect in the syndrome. In any case, heavier hammers that generate less vibration are certainly more comfortable for the operator. For example, after souring on a modern 205-lb. hammer with a total weight of only 6,000 lbs., the maintenance shop from which Sproul purchased his more than 100-year-old power hammer asked if it could buy the now fully operational 6-ton Nazel back from Sproul.
(Here’s a technical note about vibration: If you’re experiencing shock in your forearm and hand from a jumpy piece, you probably are not laying it on the die correctly. If it’s aligned perfectly in plane with the die, the workpiece shouldn’t be hopping around. Sometimes, switching to a radiused die will help.)
There’s no question that any power hammer saves wear and tear on a fabricator’s body. Court bought his first power hammer for precisely that reason. He was developing tendonitis in his forearm.
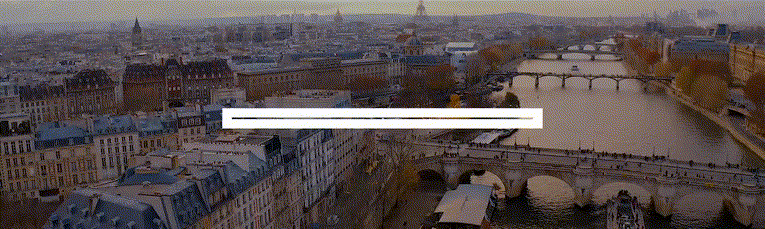
Finding the Right Hammer
So what should a fabricator look for in a first power hammer? For sheer simplicity and ease of use, a mechanical hammer is hard to beat. Its user-friendly operation makes it a snap for a beginner to gain skill and confidence.
“You can put a beginner on it,” Court said. “It’s easy to adjust and very forgiving.”
A utility hammer might cost twice as much as a mechanical hammer, but it also enables a fabricator to use hand tools and dies, opening up a world of fabricating possibilities. Of course, a shop needs to set up a compressor and that adds to the cost. Tools and dies come at an additional cost as well.
Self-contained hammers eliminate the need for a compressor, but a fabricator should be prepared to write a five-figure check for one. Again, the shop needs to make an additional investment for the smorgasbord of tools and dies to go with the self-contained hammer.
Self-contained hammers are definitely not for beginners. They are typically more daunting to operate. They also require a significant amount of floor space.
Tye offered this advice for fabricators looking for a power hammer: “There’s no secret sauce. Your tool should fit your work, not the other way around. A power hammer is a leap forward—a commitment.”
Artisan Iron, www.artisaniron.com
Ball & Chain Forge, www.ballandchainforge.com
Bay Hill Forge, 603-286-3097
Bear Hill Blacksmith, www.bearhillblacksmith.com
Elmer Roush Blacksmith, www.elmerroush.com
Purgatory Ironworks, www.purgatoryironworks.com
About the Author
Jeffrey dean.
Contributing Writer
Email Jeffrey Dean
See More by Jeffrey Dean
About the Publication
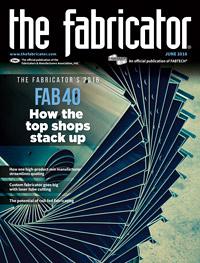
Read more from this issue
- View the Digital Edition
Subscribe to The Fabricator
Find The Fabricator on Facebook
Find The Fabricator on X
subscribe now
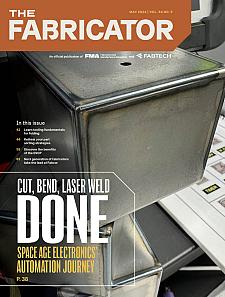
The Fabricator is North America's leading magazine for the metal forming and fabricating industry. The magazine delivers the news, technical articles, and case histories that enable fabricators to do their jobs more efficiently. The Fabricator has served the industry since 1970.
- Stay connected from anywhere
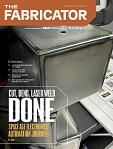
Easily access valuable industry resources now with full access to the digital edition of The Fabricator.
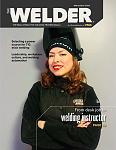
Easily access valuable industry resources now with full access to the digital edition of The Welder.
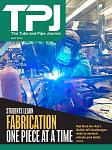
Easily access valuable industry resources now with full access to the digital edition of The Tube and Pipe Journal.
Easily access valuable industry resources now with full access to the digital edition of The Fabricator en Español.
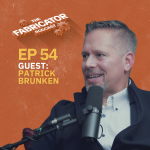
Patrick Brunken, VP of Addison Machine Engineering, joins The Fabricator Podcast to talk about the tube and pipe...
- Listen to the Podcast
- Trending Articles
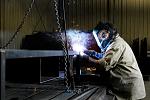
Material handling automation moves forward at MODEX
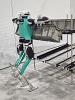
BZI opens Iron Depot store in Utah
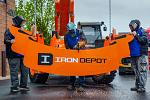
- Industry Events
Laser Welding Certificate Course
- May 7 - August 6, 2024
- Farmington Hills, IL
World-Class Roll Forming Workshop
- June 5 - 6, 2024
- Louisville, KY
Advanced Laser Application Workshop
- June 25 - 27, 2024
Precision Press Brake Certificate Course
- July 31 - August 1, 2024
Welcome back!
Forgot password?
Not yet registered? Sign up
- My Showrooms
- My Saved Guide Comparisons
- Change Password
- Change Personal Info
Trip hammer

A trip hammer , also known as a tilt hammer or helve hammer , is a massive powered hammer . Traditional uses of trip hammers include pounding, decorticating and polishing of grain in agriculture . In mining , trip hammers were used for crushing metal ores into small pieces, although a stamp mill was more usual for this. In finery forges they were used for drawing out blooms made from wrought iron into more workable bar iron . They were also used for fabricating various articles of wrought iron , latten (an early form of brass ), steel and other metals.
Early history
Bibliography, external links.
One or more trip hammers were set up in a forge , also known variously as a hammer mill , hammer forge or hammer works. The hammers were usually raised by a cam and then released to fall under the force of gravity . Historically, trip hammers were often powered hydraulically by a water wheel .
Trip hammers are known to have been used in Imperial China since the Western Han dynasty . They also existed in the contemporary Greco-Roman world , with more evidence of their use in medieval Europe during the 12th century. During the Industrial Revolution the trip hammer fell out of favor and was replaced with the power hammer . Often multiple hammers were powered via a set of line shafts , pulleys and belts from a centrally located power supply.

In ancient China, the trip hammer evolved out of the use of the mortar and pestle , which in turn gave rise to the treadle-operated tilt-hammer ( Chinese : 碓 Pinyin : dui ; Wade-Giles : tui ). [1] The latter was a simple device employing a lever and fulcrum (operated by pressure applied by the weight of one's foot to one end), which featured a series of catches or lugs on the main revolving shaft as well. [2] This device enabled the labor of pounding, often in the decorticating and polishing of grain, and avoided manual use of pounding with hand and arm.
Although Chinese historians assert that its origins may span as far back as the Zhou dynasty (1050 BC–221 BC), the British sinologist Joseph Needham regards the earliest texts to describe the device are the Jijiupian dictionary of 40 BC, Yang Xiong 's text known as the Fangyan of 15 BC, as well as the "best statement" the Xin Lun written by Huan Tan about 20 AD (during the usurpation of Wang Mang ). [3] The latter book states that the legendary mythological king known as Fu Xi was the one responsible for the pestle and mortar (which evolved into the tilt-hammer and then trip hammer device). Although the author speaks of the mythological Fu Xi, a passage of his writing gives hint that the waterwheel and trip-hammer were in widespread use by the 1st century AD in China (for water-powered Chinese metallurgy , see Du Shi ):
Fu Hsi invented the pestle and mortar, which is so useful, and later on it was cleverly improved in such a way that the whole weight of the body could be used for treading on the tilt-hammer (tui), thus increasing the efficiency ten times. Afterwards the power of animals—donkeys, mules, oxen, and horses—was applied by means of machinery, and water-power too used for pounding, so that the benefit was increased a hundredfold. [4]
However, this passage as well as other early references from the Han era may rather refer to a water lever, not a trip hammer. [5] [6] Later research, pointing to two contemporary Han era funeral wares depicting hydraulic hammers, proved that vertical waterwheels were used to power batteries of trip hammers during the Han dynasty. [7]
With his description, it is seen that the out-of-date Chinese term for pestle and mortar (dui, tui) would soon be replaced with the Chinese term for the water-powered trip-hammer ( Chinese : 水碓 ; pinyin : shuǐ duì ; Wade–Giles : shui tui . [2] The Han dynasty scholar and poet Ma Rong (79–166 AD) mentioned in one of his poems of hammers 'pounding in the water-echoing caves'. [4] As described in the Hou Han Shu , in 129 AD the official Yu Xu gave a report to Emperor Shun of Han that trip hammers were being exported from Han China to the Western Qiang people by way of canals through the Qilian Mountains . [4] In his Rou Xing Lun , the government official Kong Rong (153–208 AD) remarked that the invention of the trip hammer was an excellent example of a product created by intelligent men during his own age (comparing the relative achievements of the sages of old). [4] During the 3rd century AD, the high government official and engineer Du Yu established the use of combined trip hammer batteries (lian zhi dui), which employed several shafts that were arranged to work off one large waterwheel. [8] In Chinese texts of the 4th century, there are written accounts of men possessing and operating hundreds of trip hammer machines, such as the venerable mathematician Wang Rong (died 306 AD), Deng Yu (died 326 AD), and Shi Chong (died 300 AD), responsible for the operation of hundreds of trip hammers in over thirty governmental districts throughout China. [9] There are numerous references to trip hammers during the Tang dynasty (618–907 AD) and Song dynasty (960–1279), and there are Ming dynasty (1368–1644) references that report the use of trip hammers in papermills of Fujian Province. [10]
Although Chinese trip hammers in China were sometimes powered by the more efficient vertical-set waterwheel, the Chinese often employed the horizontal-set waterwheel in operating trip hammers, along with recumbent hammers. [11] The recumbent hammer was found in Chinese illustrations by 1313 AD, with the publishing of Wang Zhen 's Nong Shu book on ancient and contemporary (medieval) metallurgy in China. [12] There were also illustrations of trip hammers in an encyclopedia of 1637, written by Song Yingxing (1587–1666). [13]
The Chinese use of the cam remained confined to the horizontal type and was limited to a "small variety of machines" that included only rice hulling and much later mica-pounders, paper mills and saw mills, while fulling stocks, ore stamps or forge hammers were unknown. [6]
Greco-Roman world

The main components for water-powered trip hammers – water wheels , cams , and hammers – were already known in Hellenistic times . [15] Early cams are in evidence in water-powered automata from the third century BC. [16] [17] One Greek automaton in particular, a flute player whose mechanism was described by the Banu Musa but can be "reasonably" attributed to Apollonius of Perge , functions on the principle of water-powered trip hammers. [18]
The Roman scholar Pliny ( Natural History XVIII, 23.97) indicates that water-driven pestles had become fairly widespread in Italy by the first century AD:
The greater part of Italy uses an unshod pestle and also wheels which water turns as it flows past, and a trip-hammer [ mola ]".
While some scholars have viewed this passage to mean a watermill, [19] later scholarship argued that mola must refer to water-powered trip hammers which were used for the pounding and hulling of grain . [20] [16] Their mechanical character is also suggested by an earlier reference of Lucius Pomponius (fl. 100–85 BC) to a fuller's mill , a type of mill that has been operated at all times with falling stocks. [21] [22] However, it has been pointed out that the translation of Pomponius' fragmentary text could be faulty, and relies on translating mola , which is often thought to mean either a mill or millstone, to instead refer to a water powered trip hammer. [23] Grain-pounders with pestles, as well as ordinary watermills , are attested as late as the middle of the 5th century AD in a monastery founded by Romanus of Condat in the remote Jura region , indicating that the knowledge of trip hammers continued into the early Middle Ages . [16]
At the Italian site of Saepinum excavators have recently unearthed a late antique water mill that may have employed trip hammers for tanning , the earliest evidence of its kind in a classical context. [24] [25]
The widest application of trip hammers seems to have occurred in Roman mining, where ore from deep veins was first crushed into small pieces for further processing. [26] Here, the regularity and spacing of large indentations on stone anvils indicate the use of cam-operated ore stamps, much like the devices of later medieval mining. [26] [14] Such mechanically deformed anvils have been found at numerous Roman silver and gold mining sites in Western Europe , including at Dolaucothi ( Wales ), and on the Iberian peninsula , [26] [14] [27] [28] where the datable examples are from the 1st and 2nd century AD. [29] At Dolaucothi, these trip-hammers were hydraulic-driven and possibly also at other Roman mining sites, where the large-scale use of the hushing and ground sluicing technique meant that large amounts of water were directly available for powering the machines. [26] [30] However, none of the Spanish and Portuguese anvils can be convincingly associated with mill sites, though most mines had water sources and leat systems which could easily be harnessed. [14] Likewise, the dating of the Pumsaint stone to the Roman era did not address that the stone could have been moved, and relies on a series of interlinked probabilities which would jeopardize the conclusion of a Roman dating should any of them unravel. [14]
Medieval Europe

Water-powered and mechanised trip hammers reappeared in medieval Europe by the 12th century. Their use was described in medieval written sources of Styria (in modern-day Austria), written in 1135 and another in 1175 AD. [31] Medieval French sources of the years 1116 and 1249 both record the use of mechanised trip hammers used in the forging of wrought iron . [31] Medieval European trip hammers by the 15th century were most often in the shape of the vertical pestle stamp-mill, although they employed more frequent use of the vertical waterwheel than earlier Chinese versions (which often used the horizontal waterwheel). [10] The well-known Renaissance artist and inventor Leonardo da Vinci often sketched trip hammers for use in forges and even file-cutting machinery, those of the vertical pestle stamp-mill type. [12] The oldest depicted European illustration of a forge-hammer is perhaps the A Description of the Northern Peoples of Olaus Magnus , dated to 1565 AD. [12] In this woodcut image, there is the scene of three martinets and a waterwheel working wood and leather bellows of the Osmund Bloomery furnace. [12] The recumbent hammer was first depicted in European artwork in an illustration by Sandrart and Zonca (dated 1621 AD). [12]
A trip hammer has the head mounted at the end of a recumbent helve , hence the alternative name of helve hammer. The choice of which type was used in a particular context may have depended on the strain that its operation imposed on the helve. This was normally of wood, mounted in a cast-iron ring (called the hurst) where it pivoted. However, in the 19th century the heaviest helves were sometimes a single casting, incorporating the hurst.

The tilt hammer or tail helve hammer has a pivot at the centre of the helve on which it is mounted, and is lifted by pushing the opposite end to the head downwards. In practice, the head on such hammers seems to have been limited to one hundredweight (about 50 kg), but a very rapid stroke rate was possible. This made it suitable for drawing iron down to small sizes suitable for the cutlery trades. There were therefore many such forges known as 'tilts' around Sheffield . They were also used in brass battery works for making brass (or copper) pots and pans. In battery works (at least) it was possible for one power source to operate several hammers. In Germany, tilt hammers of up to 300 kg were used in hammer mills to forge iron. Surviving, working hammers, powered by water wheels, may be seen, for example, at the Frohnauer Hammer in the Ore Mountains .
The belly helve hammer was the kind normally found in a finery forge , used for making pig iron into forgeable bar iron. This was lifted by cams striking the helve between the pivot and the head. The head usually weighed quarter of a ton. This was probably the case because the strain on a wooden helve would have been too great if the head were heavier.
The nose helve hammer seems to have been unusual until the late 18th or early 19th century. This was lifted beyond the head. Surviving nose helves [32] and those in pictures [33] appear to be of cast iron.
The steam-powered drop hammer replaced the trip hammer (at least for the largest forgings). James Nasmyth invented it in 1839 and patented in 1842. However, by then forging had become less important for the iron industry, following the improvements to the rolling mill that went along with the adoption of puddling from the end of the 18th century. Nevertheless, hammers continued to be needed for shingling .
- Abbeydale Industrial Hamlet
- Dorfchemnitz Iron Hammer Mill
- Finch Foundry
- Freibergsdorf Hammer Mill
- Frohnauer Hammer Mill
Related Research Articles
A crankshaft is a mechanical component used in a piston engine to convert the reciprocating motion into rotational motion. The crankshaft is a rotating shaft containing one or more crankpins, that are driven by the pistons via the connecting rods.

A watermill or water mill is a mill that uses hydropower. It is a structure that uses a water wheel or water turbine to drive a mechanical process such as milling (grinding), rolling, or hammering. Such processes are needed in the production of many material goods, including flour, lumber, paper, textiles, and many metal products. These watermills may comprise gristmills, sawmills, paper mills, textile mills, hammermills, trip hammering mills, rolling mills, wire drawing mills.

A water wheel is a machine for converting the energy of flowing or falling water into useful forms of power, often in a watermill. A water wheel consists of a wheel, with a number of blades or buckets arranged on the outside rim forming the driving car. Water wheels were still in commercial use well into the 20th century but they are no longer in common use today. Uses included milling flour in gristmills, grinding wood into pulp for papermaking, hammering wrought iron, machining, ore crushing and pounding fibre for use in the manufacture of cloth.
The chain pump is type of a water pump in which several circular discs are positioned on an endless chain. One part of the chain dips into the water, and the chain runs through a tube, slightly bigger than the diameter of the discs. As the chain is drawn up the tube, water becomes trapped between the discs and is lifted to and discharged at the top. Chain pumps were used for centuries in the ancient Middle East, Europe, and China.
The River Eden is a tributary of the River Medway in south east England. It rises at the foot of the North Downs escarpment near Titsey in Surrey and runs initially southwards through Oxted before turning eastwards to enter Kent. After flowing through Edenbridge and passing Hever Castle, the Eden meets the Medway at Penshurst.

The Wealden iron industry was located in the Weald of south-eastern England. It was formerly an important industry, producing a large proportion of the bar iron made in England in the 16th century and most British cannon until about 1770. Ironmaking in the Weald used ironstone from various clay beds, and was fuelled by charcoal made from trees in the heavily wooded landscape. The industry in the Weald declined when ironmaking began to be fuelled by coke made from coal, which does not occur accessibly in the area.

A hammer mill is a mill whose purpose is to shred or crush aggregate material into smaller pieces by the repeated blows of small hammers. These machines have numerous industrial applications, including:
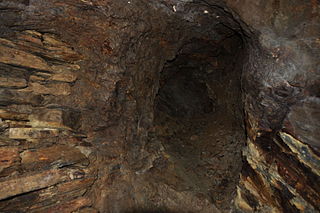
The Dolaucothi Gold Mines , also known as the Ogofau Gold Mine , are ancient Roman surface and underground mines located in the valley of the River Cothi, near Pumsaint, Carmarthenshire, Wales. The gold mines are located within the Dolaucothi Estate, which is owned by the National Trust.

Pumsaint is a village in Carmarthenshire, Wales, halfway between Llanwrda and Lampeter on the A482 in the valley of the Afon Cothi. It forms part of the extensive estate of Dolaucothi, which is owned by the National Trust.

A hammer mill , hammer forge or hammer works was a workshop in the pre-industrial era that was typically used to manufacture semi-finished, wrought iron products or, sometimes, finished agricultural or mining tools, or military weapons. The feature that gave its name to these workshops was the water-driven trip hammer, or set of hammers, used in the process. The shaft, or 'helve', of the hammer was pivoted in the middle and the hammer head was lifted by the action of cams set on a rotating camshaft that periodically depressed the end of the shaft. As it rose and fell, the head of the hammer described an arc. The face of the hammer was made of iron for durability.
Zhang Sixun was a Chinese astronomer and mechanical engineer from Bazhong, Sichuan during the early Song dynasty. He is credited with creating an armillary sphere for his astronomical clock tower that employed the use of liquid mercury. The liquid mercury filled scoops of the waterwheel would rotate and thus provide the effect of an escapement mechanism in clockworks and allow the astronomical armillary sphere to rotate as needed.

A finery forge is a forge used to produce wrought iron from pig iron by decarburization in a process called "fining" which involved liquifying cast iron in a fining hearth and removing carbon from the molten cast iron through oxidation. Finery forges were used as early as the 3rd century BC in China. The finery forge process was replaced by the puddling process and the roller mill, both developed by Henry Cort in 1783–4, but not becoming widespread until after 1800.

A stamp mill is a type of mill machine that crushes material by pounding rather than grinding, either for further processing or for extraction of metallic ores. Breaking material down is a type of unit operation.

Wang Zhen was a Chinese agronomist, inventor, mechanical engineer, politician, and writer of the Yuan dynasty (1271–1368). He was one of the early innovators of the wooden movable type printing technology. His illustrated agricultural treatise was also one of the most advanced of its day, covering a wide range of equipment and technologies available in the late 13th and early 14th century.

Mining was one of the most prosperous activities in Roman Britain. Britain was rich in resources such as copper, gold, iron, lead, salt, silver, and tin, materials in high demand in the Roman Empire. Sufficient supply of metals was needed to fulfil the demand for coinage and luxury artefacts by the elite. The Romans started panning and puddling for gold. The abundance of mineral resources in the British Isles was probably one of the reasons for the Roman conquest of Britain. They were able to use advanced technology to find, develop and extract valuable minerals on a scale unequaled until the Middle ages.

Du Shi was a Chinese hydrologist, inventor, mechanical engineer, metallurgist, and politician of the Eastern Han dynasty. Du Shi is credited with being the first to apply hydraulic power to operate bellows in metallurgy. His invention was used to operate piston-bellows of the blast furnace and then cupola furnace in order to forge cast iron, which had been known in China since the 6th century BC. He worked as a censorial officer and administrator of several places during the reign of Emperor Guangwu of Han. He also led a brief military campaign in which he eliminated a small bandit army under Yang Yi.

A field mill , also known as a camp mill , was a premodern vehicle which acted as a mobile mill used for grinding grains, which had the very practical use of feeding a moving army.
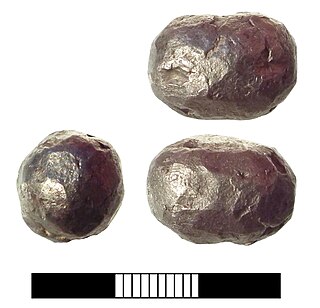
Metals and metal working had been known to the people of modern Italy since the Bronze Age. By 53 BC, Rome had expanded to control an immense expanse of the Mediterranean. This included Italy and its islands, Spain, Macedonia, Africa, Asia Minor, Syria and Greece; by the end of the Emperor Trajan's reign, the Roman Empire had grown further to encompass parts of Britain, Egypt, all of modern Germany west of the Rhine, Dacia, Noricum, Judea, Armenia, Illyria, and Thrace. As the empire grew, so did its need for metals.
The Tiangong Kaiwu (天工開物), or The Exploitation of the Works of Nature was a Chinese encyclopedia compiled by Song Yingxing. It was published in May 1637 with funding provided by Song's patron Tu Shaokui. The Tiangong Kaiwu is an encyclopedia covering a wide range of technical issues, including the use of various gunpowder weapons. Copies of the book were very scarce in China during the Qing dynasty (1644–1911), but original copies of the book were preserved in Japan.
- ↑ Needham, Volume 4, Part 2, 183.
- 1 2 Needham, Volume 4, Part 2, 390.
- ↑ Needham, Volume 4, Part 2, 184.
- 1 2 3 4 Needham, Volume 4, Part 2, 392.
- ↑ Terry Reynolds: Stronger Than a Hundred Men. A History of the Vertical Water Wheel , The Johns Hopkins University Press, 1983, pp. 26-30
- 1 2 Lewis 1997 , p. 118
- ↑ Xiaolei 2019 , p. 115
- ↑ Needham, Volume 4, Part 2, 393.
- ↑ Needham, Volume 4, Part 2, 392-393.
- 1 2 Needham, Volume 4, Part 2, 394.
- ↑ Needham, Volume 4, Part 2, 391–392.
- 1 2 3 4 5 Needham, Volume 4, Part 2, 395.
- ↑ Song, 91–93.
- 1 2 3 4 5 Barry C. Burnham: "Roman Mining at Dolaucothi: The Implications of the 1991-3 Excavations near the Carreg Pumsaint", Britannia , Vol. 28 (1997), pp. 325-336 (333-335)
- ↑ Wilson 2002 , p. 22
- 1 2 3 Wilson 2002 , p. 16
- ↑ Lewis 1997 , pp. 84–88
- ↑ Lewis 1997 , pp. 86–88
- ↑ Terry Reynolds: Stronger Than a Hundred Men. A History of the Vertical Water Wheel , The Johns Hopkins University Press, 1983, p. 355, fn. 51
- ↑ Lewis 1997 , pp. 101–105
- ↑ Lewis 1997 , pp. 94f.
- ↑ Wilson 2002 , p. 16, fn. 93
- ↑ Flohr 2013 , p. 102
- ↑ Brun & Leguilloux 2014 , pp. 160–170, particularly 162
- ↑ Wilson 2020 , p. 171
- 1 2 3 4 Wilson 2002 , pp. 21f.
- ↑ J. Wahl: "Tres Minas: Vorbericht über die archäologischen Ausgrabungen im Bereich des römischen Goldbergwerks 1986/87", in H. Steuer and U. Zimmerman (eds): "Montanarchäologie in Europa", 1993, p.123-152 (141; Fig.19)
- ↑ Sánchez-Palencia Ramos, Francisco-Javier (1984/1985): "Los «Morteros» de Fresnedo ( Allande) y Cecos (Ibias) y los lavaderos de oro romanos en el noroeste de la Península Ibérica , "Zephyrus", Vol. 37/38, pp. 349–359 (356f.)
- ↑ Wilson 2002 , p. 21, fn. 110
- ↑ Lewis 1997 , pp. 106–1010
- 1 2 Needham, Volume 4, Part 2, 379.
- ↑ For example at Abbeydale Industrial Hamlet [ dubious – discuss ]
- ↑ For example in the metalwork gallery in Birmingham Museum & Art Gallery
- Sim, David and Ridge, Isable: "Iron for the Eagles" (2002)
- Burnham, Barry C.: "Dolaucothi-Pumsaint: Survey and Excavations at a Roman Gold-mining Complex" (2004)
- Lewis, M. J. T. (1997), Millstone and Hammer. The Origins of Water Power , The University of Hull Press, ISBN 0-85958-657-X
- Needham, Joseph; Wang, Ling. (1986) [1965]. Science and Civilization in China: Volume 4, Physics and Physical Technology, Part 2, Mechanical Engineering . Taipei: Caves Books Ltd (reprint edition of Cambridge & New York: Cambridge University Press). ISBN 0-521-05803-1 .
- Wilson, Andrew (2002), "Machines, Power and the Ancient Economy", The Journal of Roman Studies , vol. 92, pp. 1–32
- Wilson, Andrew (2020), "Roman Water-Power. Chronological Trends and Geographical Spread", in Erdkamp, Paul; Verboven, Koenraad; Zuiderhoek, Arjan (eds.), Capital, Investment, and Innovation in the Roman World , Oxford University Press, pp. 147–194, ISBN 978-0-19-884184-5
- Song, Yingxing, translated with preface by E-Tu Zen Sun and Shiou-Chuan Sun: T'ien-Kung K'ai-Wu: Chinese Technology in the Seventeenth Century . (University Park: Pennsylvania State University Press 1966).
- Xiaolei, Shi (2019), "The Hydraulic Tilt Hammer in Ancient China", in Baichun, Zhang; Marco, Ceccarelli (eds.), Explorations in the History and Heritage of Machines and Mechanisms , Springer Nature Switzerland AG, pp. 113–122, ISBN 978-3-030-03537-2
- Flohr, Miko (2013), The World of the Fullo: Work, Economy and Society in Roman Italy , Oxford University Press, p. 102, ISBN 978-0199659357
- "Diagram of a forge trip hammer" . ExplorePAHistory.com . WITF; Pennsylvania Historical and Museum Commission . Retrieved 22 January 2013 .
- Fabrication
- Tools and terminology
Pete's Power Hammer Page See my Power Hammer FAQ at the bottom of the page
Last revised: october 19, 2023, hammers at my house.
My small collection of power hammers contains nine units at present. Eight of them are in an out building that I loosely call my "Museum". Five of the eight are Little Giants. One is a 50# Mayer Bros., one is a 25# Mayer Bros. (made after 2 of them moved to Wisconsin) and one is a 25# hammer made by Novelty Iron works, Dubuque, Ia. In Little Giant 25#'ers, I have one "old style " (wrap around guide), one "transition hammer", one "new style" and one "Easy" hammer. Lastly, I have one old style 50# hammer in my shop and one in my "Museum". This collection is a handy place for local people to come to compare various sizes of vertical hammers and modifications that the product line had seen over the years. Some need work and some are ready to go. We held a Fred Caylor/Harlan (Sid) Suedemeier Power hammer rebuilding workshop out here in 1992 and again in 1996 and the collection got quite a going over at that time. 24 people and their families came for the first 2 1/2 day workshop and about 18 workers came the second time. Sid Suedmeier, former owner of Little Giant, holds one of these workshops each year, usually in his shop in Nebraska City, NE. You can phone him at 402-873-6603.
In June of 2013, Sid turned the business over to Roger Rice, also from Nebraska City. Here's the announcement: Little Giant is changing ownership, effective immediately. In order to perpetuate the line of replacement parts, repair services and information, Little Giant will now be in the extremely capable hands of our machinist, Roger Rice. He will be assisted by our friend David Sloan, who has a great understanding of the mechanical operation of Little Giants. We will be assisting Roger and Dave during the initial transition, and Sid will continue teaching the annual Little Giant rebuilding class. The same telephone number (402-873-6603) will move to the new location at: Midwest Machine, 6414 King Road, Nebraska City, Nebraska 68410. New Email Address (Updated 7/18/2019): [email protected] It has been a great 22 years, and we are profoundly grateful to have been a part of the blacksmithing community. We have often said we have the best customers in the world, and we do mean it. It has been an honor to not only help keep these venerable machines in operation, but to have made so many good friends in the process. With sincere appreciation, Sid Suedmeier and Keri Hincker (End of Announcement) P.S. An additional email says that Sid's health is good.
The foregoing description of my power hammers is not an offer to sell, but I have been thinking about it lately. I collect them. Lots of people ask me why. I point out that when I was a little kid, I used to collect popsicle sticks and now I am big.
Vertical Hammers
What Style of Hammer IS That??????? > Click HERE to find out how to differentiate the styles of Litttle Giant/Mayer Brothers Hammers from one another. I use examples of 25# and 50# hammers to show each style.
Horizontal (Helve) Hammer, the RAREST of all the Mayer Bros. Hammers! Click HERE to see my Easy Hammer (Before and After) and to find out how I went about rebuilding it.
My Power Hammer FAQ Section
How do I locate a Power Hammer to Buy? Read this article: How do I get started in blacksmithing? It mostly suggests that you go where the blacksmiths are to find the equipment you want. And, since power hammers are pretty heavy and therefore expensive to ship, you will have the best chance to minimize that part of the cost.
What kind of Foundation Do I Need for My 25# or 50# Powerhammer?
What size Motor and Pulley do I Need for My 25# or 50# Powerhammer?
Why does my 25# Powerhammer Bog down?
What's this old trip hammer worth?
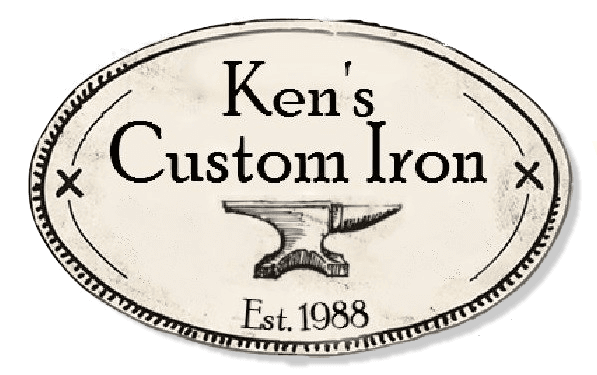
MZ75 Power Hammer
Brute 30 ton press.
Power and versatility meet in the all-new BRUTE 30-Ton Press. Click "Learn More" below to see it in action and read its specs!
Links:
Online Store
Frequently Asked Questions
Blacksmithing for Veterans Event
Central Minnesota Blacksmiths Group

PLEASE refer to the updated price sheet for the best-estimated pricing and email or call to confirm prices - THANK YOU
Little Giant
First manufactured in 1895, the Little Giant Company sold more than 18,000 power hammers during 99 years of production. Shipped to every state in the U.S. and more than 30 other countries, the Little Giant Power Hammer was the best selling of all brands of mechanical hammers.
In 1991, our company was offered the opportunity to purchase what remained of Little Giant: blueprints, foundry patterns, and invaluable handwritten sales records. From this, we have established a parts line, repair services and a clearinghouse for information on these machines.
Still in use across the nation, the Little Giant Power Hammer remains a vital part of a reborn art form - the transformation of metal.
The parts we supply for the LG Power Hammer are those that are most needed to repair and maintain! Parts listed under each category are normally in stock and ready to ship. Also we have the standard one piece dies and a 2 piece interchangable system that is popular. Part numbers not listed are not available. We also manufacture parts for other brands.
Repair Services
We have 26 years of experience repairing LG parts, and over 40 years repairing mechanical parts. We can repair many of the steel parts, including non-LG parts, depending on condition, please call to discuss. Anything shipped to us needs to be in a sturdy, wooden crate and insured. Parts such as the pulley have never been recast and if they are lost or damaged in shipment will be very hard to find used!
Search results for: 'products hammers forging hammers'
Items 1 - 18 of 524
- You're currently reading page 1
Related search terms

Starting at $18.00

Starting at $45.00

Starting at $15.00

Starting at $30.00

As low as $185.00

As low as $235.00

Starting at $35.00

Starting at $50.00

Starting at $240.00

As low as $70.00

Call For Shipping Quote, (828) 667-8868 Or 665-1988 Cathy Kayne Kayne and Son Custom Hardware, Inc.
- #6 (1/8") 2 items
- #7 (9/64") 2 items
- #8 (5/32") 5 items
- 5/8" 2 items
- 3/4" 2 items
- 1-1/2" 2 items
- Remove This Item
- Create account

Anyang ST Blacksmith Power Hammers
Anyang ST Blacksmith Power HammerThe Anyang ST Power Hammer: Self-contained, Powerful, and Easy to Maintain The Anyang ST Power Hammer stands out as a self-contained hammer that eliminates the need for an additional air supply compressor. With its solid casting frame and integrated air channel, it offers a more robust construction. The longer ram design prevents the top die from retracting into the cylinder, ensuring enhanced control and power. Experience low noise operation and ease of maintenance, empowering users to achieve optimal results. Choose the Anyang ST Power Hammer for superior performance and reliability in your metalworking projects.

Anyang ST 25 kg Pneumatic Power Hammer
Regular price $9,550.00

Anyang ST 75 kg Pneumatic Power Hammer
Regular price $17,350.00

Anyang ST 55 kg Pneumatic Power Hammer
Regular price $14,449.00

Anyang ST 40 kg Pneumatic Power Hammer
Regular price $11,650.00

Anyang ST 15 kg Pneumatic Power Hammer
Regular price $7,350.00
- choosing a selection results in a full page refresh
- Opens in a new window.
- Opens external website in a new window.

- TRIPP'S END -
Blacksmith shop, new england's premier maker of hand-forged outdoor cooking equipment.

My love of history began as a child growing up on the family farm. Our family roots run deep. My father's family has lived in York County Maine for at least eight generations. My mother's family tree traces straight back to England and they lived on the same farm in western York County Maine for seven generations. I now live on the farm that my father and grandfather owned before me. Growing up we had large vegetable gardens, grew our own meat and cut firewood down back on the woodlot. It seems as though my brother and I grew up with hammers in our hands. From building forts in the top of the old barn, to building fence, to helping Dad nail a new roof on the house, we had our share of smashed thumbs and broken handles. We hung our own handles sitting on a shave horse using an old draw shave and my grandfather's combo spoke shave.
In 1979 I found the book "Edge of the Anvil" by Jack Andrews in a local bookstore. The book is an introduction to blacksmithing and the binding has long since broken down from being read over and over. From that point on I gained a greater appreciation of the tools we used every day on the farm. My tool and book collection began to grow but in the days before Google I was unable to locate a blacksmith to train with.
After graduating from the University of Maine College of Forestry, I was working for a local paper mill as a landowner assistance forester and was asked to meet with a landowner in Brownfield Maine. After touring the woodlot and receiving a particularly grueling grilling about tree diseases and the breeding habits of white pine trees, Ed Grove revealed that he had been a graduate of the University of Maine College of Forestry some thirty five years earlier. Ed had a background in blacksmithing and after working for several years in the wood industry he went full time into farrier work and blacksmithing. We hitched up well together and in 1991 I trained with Ed. That spring I built my own shop and since then I have operated a custom blacksmithing business and a forestry consulting/logging business at the same time.
My business focus now is producing hand forged outdoor cooking equipment. From carbon steel frying pans to marshmallow forks, I love to discover the forging processes required to recreate these items. Prior to the industrial revolution the blacksmith was integral to everyday life. From the housewife's spatula and spoon, to the woodsman's axe, to the stone cutter's feathers and wedges, everyone needed the blacksmith to make and repair tools.
Keep forging, Joel F. Tripp

OUR BESTSELLERS
Appalachian Trail Cook Kit
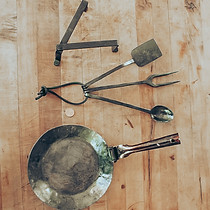
Maine Woodsman Frying Pan 9" Folding Handle
Medieval Hammer

Have fun. We only get one chance at this ride so have a good time
JOEL F. TRIPP, OWNER

Thanks for submitting!
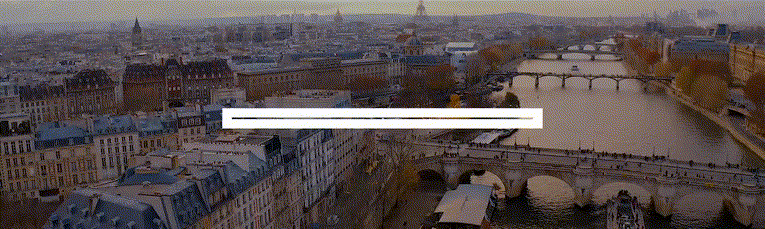
IMAGES
VIDEO
COMMENTS
A 1960s trip hammer placed at Trattenbach village, Lower Austria The same trip hammer in operation, shaping a folding knife at the strike area. A trip hammer, also known as a tilt hammer or helve hammer, is a massive powered hammer.Traditional uses of trip hammers include pounding, decorticating and polishing of grain in agriculture.In mining, trip hammers were used for crushing metal ores ...
Blacksmithing craft education and metalworking are what this page is all about. I cover blacksmithing how-to articles, blacksmith tools and other blacksmithed items I have made using hand hammer, treadle hammer and trip hammer. Blacksmithing at French Creek Valley Forge Last Updated: March 23, 2024.
Trip hammers revisited. In 2016 the Museum published a blog post about a trip hammer built by the Church Family Shakers in 1847 to be used in their new blacksmiths' workshop. The new trip hammer was an industrial size machine with the capability to shape hot metal of any size the Shaker might need forged. Trip hammers of […]
A four ton trip hammer. In the winter of 1846 the First and Second Order of the Church Family determined to build a new blacksmith shop, one of stone with waterpower that would operate a lathe, drilling works, a grindstone, bellows for the forge, and a trip hammer. The shop was to be built 34 feet by 44 feet and […]
SOLD. Photos from Ted Mays, Tool Collection Tour 25 Pound Little Giant Trip Hammer. A classic of small blacksmith and blademiths shops. Ready to plug and play. These little hammers weigh less than 1,000 pounds (450 kg) and can be hauled in a small pickup truck. Maker: Mayer Bros. Mankato, MN. MOTOR: Leland Faraday 1.5HP 115/120 VAC, 1725 RPM.
The idea of a power hammer goes back to antiquity. Records indicate that the Chinese employed them as early as 200 B.C. Power hammers were part of Europe's industrial landscape as early as the 12th century. Of course, those were more correctly called trip hammers, and they worked like hefty blunt guillotines.
Investing in a different kind of precious metal..! I got this hammer from a fellow blacksmith in Midland, Texas and can't wait to use it!My Website: https://...
1871 CE — Powered trip hammer patented by Wilhelm Schneider; ... Hammers — Blacksmiths wield a range of hammers to pound hot metal into shape. Hammers have specially shaped peen and face ends ...
A trip hammer, also known as a tilt hammer or helve hammer, is a massive powered hammer. Traditional uses of trip hammers include pounding, decorticating and polishing of grain in agriculture. In mining, trip hammers were used for crushing metal ores into small pieces, although a stamp mill was more usual for this. In finery forges they were used for drawing out blooms made from wrought iron ...
A 1960s trip hammer placed at Trattenbach village, Lower Austria The same trip hammer in operation, shaping a folding knife at the strike area. A trip hammer, also known as a tilt hammer or helve hammer, is a massive powered hammer.Traditional uses of trip hammers include pounding, decorticating and polishing of grain in agriculture.In mining, trip hammers were used for crushing metal ores ...
A power hammer A blacksmith working with a 50-kilogram (110 lb) power hammer. Power hammers are mechanical forging hammers that use an electrical power source or steam to raise the hammer preparatory to striking, and accelerate it onto the work being hammered. They are also called open die power forging hammers.They have been used by blacksmiths, bladesmiths, metalworkers, and manufacturers ...
The same telephone number (402-873-6603) will move to the new location at: Midwest Machine, 6414 King Road, Nebraska City, Nebraska 68410. New Email Address (Updated 7/18/2019): [email protected]. It has been a great 22 years, and we are profoundly grateful to have been a part of the blacksmithing community.
The KZ100 and MZ75 Power Hammers operate just like a steam hammer. We use a mechanical linkage and a directional valve along with compressed air to operate and control the hammer. ... Ken walks you through his process of the models preceding the MZ75 and how we've grown to selling our 100th hammer.] . . . . . #blacksmith #blacksmithtongs # ...
Photos from Ted Mays, Tool Collection Tour 50 Pound Star Foundry Trip Hammer. Maker: Star Foundry, Albert Lea, Minn USA. MOTOR: GE Repulsion Induction 1HP 110/220 VAC, 1170 RPM. SIZE: 26 x 16 x 66 inches tall. #574583. Works (See photos) NOTE: Leg under motor is to support the hammer while not bolted down. May be removed when installed.
Little Giant. First manufactured in 1895, the Little Giant Company sold more than 18,000 power hammers during 99 years of production. Shipped to every state in the U.S. and more than 30 other countries, the Little Giant Power Hammer was the best selling of all brands of mechanical hammers. In 1991, our company was offered the opportunity to ...
The footbridge was built around 1890 by the blacksmith Bongiovanni Gio Battista and his son in order to shorten the route to Cuneo and last but not least, to attract customers heading to the other two forges, located on the other side of the Maira. ... Gianpiero Cavallo, and Davide Colletti. 2023. "The Water-Powered Trip Hammer and Forge La ...
Little Giant 50 Lb blacksmith Power Trip Hammer low use original. Opens in a new window or tab. super nice low use original. Pre-Owned. $7,500.00. fireguy715 (552) 100%. 0 bids · Time left 2d 9h left (Sun, 06:15 PM) Free local pickup. ANTIQUE CHAMPION TOOL CO. ANVIL LOGO BLACKSMITH 2 LB. FARRIER ROUNDING HAMMER.
Blacksmith 50 Pound Power Trip Hammer As Found . $4,250.00. Local Pickup. or Best Offer. 46 watching. Vintage Large Heavy 18 Inch Long Blacksmith Metal Power Hammer Tongs. $24.95. or Best Offer. $9.99 shipping. Blacksmithing - PoWeR HaMMer Work - Steam Hammers - 1906 - new reprint . $8.98.
Many blacksmiths use a cheap steel forging hammer and cutting plate on the anvil when punching and chiseling. Read More. Items 1 - 18 of 19. Show per page. Sort By. Larson Diagonal Peen Hammer - Left Hand - 2.5 lb. Write your review. $195.00. Add to Cart.
Anyang ST Blacksmith Power HammerThe Anyang ST Power Hammer: Self-contained, Powerful, and Easy to Maintain The Anyang ST Power Hammer stands out as a self-contained hammer that eliminates the need for an additional air supply compressor. With its solid casting frame and integrated air channel, it offers a more robust construction.
Blacksmith's, Anvils, Blowers, Cones, Chisels, Hardies, Hammers, Swage Blocks, Punches . . For Power Hammers, Ironworkers, Presses, Rolls and Cranes see Machinery : RULES TERMS ... FOR SALE 50lb Little Giant Trip hammer: 5000 : 1937 50lb little giant trip hammer, only made this model for 5 years. due to the die positioning this is the hammer ...
How to use, buy, build, repair and maintain forging machinery for the blacksmith shop. Listed January 27, 2017 Sold Feb 3. Josh Greenwood forging a billet under his "Little Red Hammer" (A 500 pound Chambersburg Utility hammer) while Bruce Wallce watches. 1957 color poster of Bêché 2000 Kg air hammer sent to us by Antti Sakari Salminen of Finland.
Prior to the industrial revolution the blacksmith was integral to everyday life. From the housewife's spatula and spoon, to the woodsman's axe, to the stone cutter's feathers and wedges, everyone needed the blacksmith to make and repair tools. Keep forging, Joel F. Tripp.