Calculating Starting Wire Feed Speed, Voltage and Travel Speed
There might be affiliate links in this post. Buying through them can earn us a small commission at no cost to you. This covers our wages and keeps our resources free to use.
If your goal is to decrease the development time for new MIG welds, you can do it by calculating starting wire-feed speed, voltage, and travel speed. Pre-calculating is common among manufacturers welding with solid wire or flux-cored wire.
Most welding professionals know how calculating starting wire feed speed (WFS) based on their experience, while beginners usually follow the manufacturer’s recommended procedures.
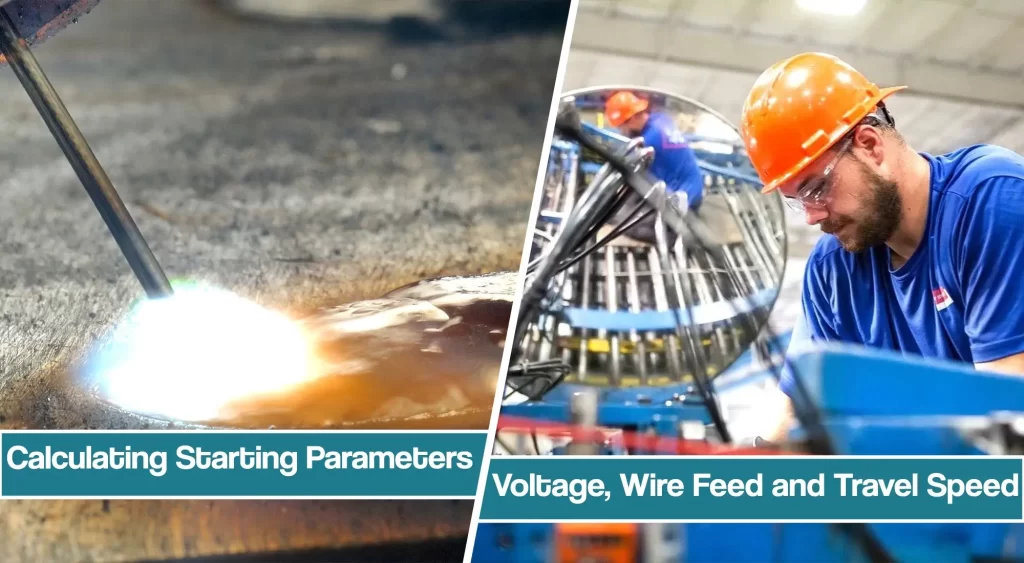
However, determining the travel speed for a particular size weld bead is an iterative, time-consuming process, meaning costs go up in manufacturing. Understanding a few concepts and doing some math with a few simple formulas can help you at least a good starting point for achieving the desired weld.
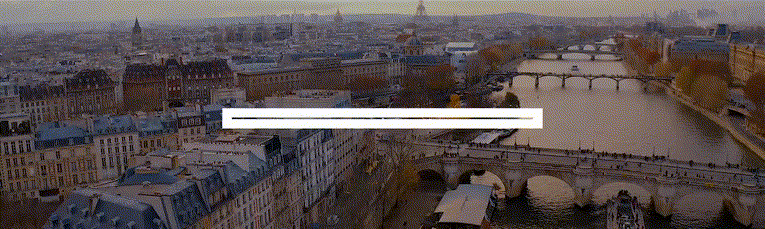
Understanding The Deposition Rate
Prior to any calculations, you should know that Deposition Rate is directly proportional to the speed of a particular wire diameter that emerges from a MIG welding gun. On the other hand, deposition rate has nothing to do with travel speed nor the voltage setting on the machine.
The deposition rate simply shows how many pounds of wire come from the welding gun in a particular time. That’s why it is typically measured in lb./hr.
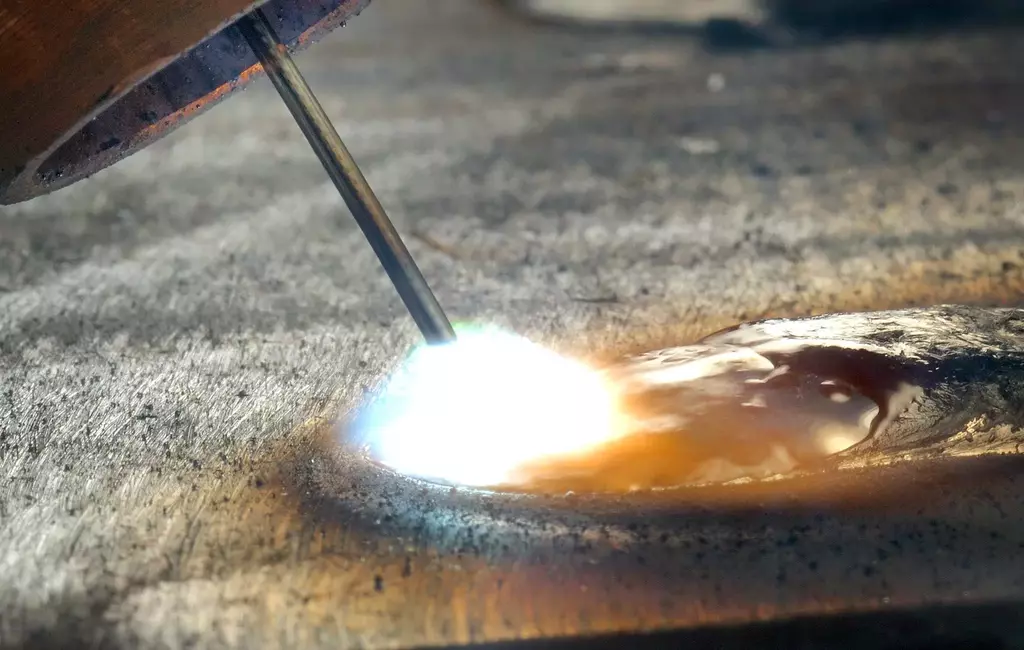
As a result, suppose wire-feed speed increases, and deposition rate increases. Therefore, if you maintain the wire-feed speed and choose a larger diameter wire, the deposition rate will also increase.
By understanding the fundamentals, calculating deposition rate is an effective exercise you can use to get to the critical welding parameters.
Let’s look at the formula and an example:
Deposition Rate Calculation
Deposition rate (lb./hr) = 13.1×( Wire diameter )2×( Wire-feed speed )×( Efficiency )
- Wire diameter in given in inches (in.)
- Wire-feed speed is calculated in inches per minute (IPM)
- Efficiency differs, and it is 1.0 for solid wire, 0.85 for cored wire
- Keep in mind that this calculation is for steel only
For example, if your project requires: Wire diameter = 0.030 in. (1.2 mm) solid wire, WFS = 350 IPM.
Deposition rate = 13.1×(0.030)2 ×(350)×(1.0) = 4.13 lb./hr
Calculating Travel Speed By Using Deposition Rate Results
By getting the deposition rate by using the calculation above, you can calculate the travel speed in inches per minute (IPM) for a particular weld. For example, let’s say you want to make a 3/8-in. steel fillet weld (assume 10% reinforcement or 0.4125 in. leg) using 0.030-in. solid wire at 350 IPM, the weight of weld metal per foot can be calculated by multiplying the density of steel (0.283 lb./in3) by the volume of weld metal per foot as follows:
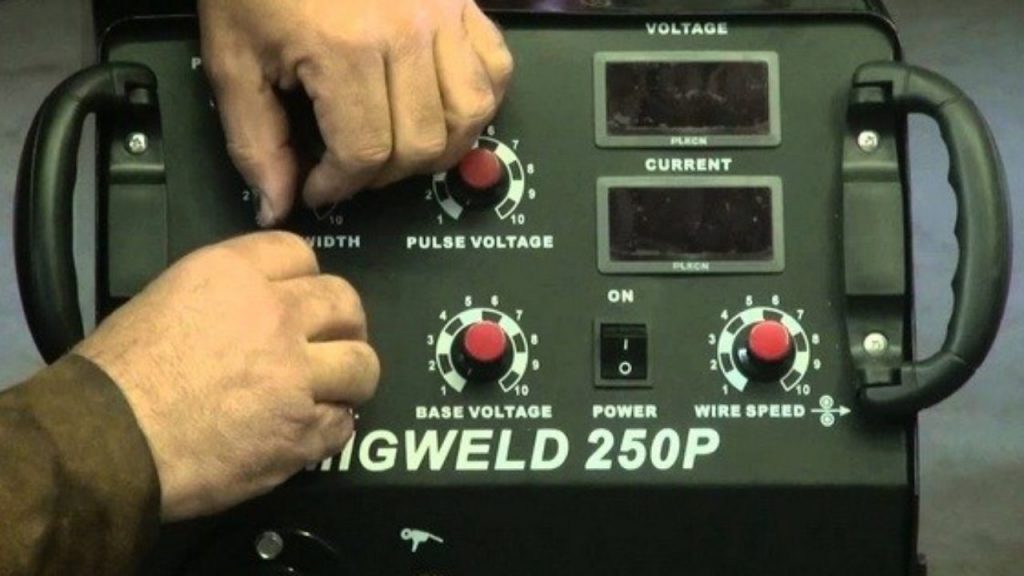
Calculating Weld Weight Per Foot
Vol. of weld metal/ft =1/2×b×h×12 in.=1/2×0.4125 in.×0.4125 in.×12 in.=1.02 in3.
Weight of weld metal/ft of 3/8 in. fillet weld=(0.283 lb./in3)×(1.02 in3)=0.2887 lb./ft.
Next, we will use weld weight per foot to calculate the travel speed
Calculating Travel Speed
Travel speed = ( deposition rate )×( # of passes )/5×( weight of weld metal per foot {lb./ft} ) = (4.13)×(1)/5 × (0.2887) = 0.23 IPM
Calculating Wire-feed Speed Using Deposition rate
Let’s assume a requirement to make fillet welds at a rate of 12 lb./hr using 0.030 in. welding wire. Then, we can calculate the WFS using the formulas below and the Weight of Weld Wire per foot in Table 1.
Wire-feed Speed Calculation
Wire-feed Speed = ( deposition rate )/5×( weight of wire per foot {lb./ft} ) = (12)/5×(0.0054) = 444.4 IPM
Of course, the travel speed for a one-pass, 3/8 in. fillet weld at a 12 lb./hr deposition rate would be 8.31 IPM, as calculated below.
Travel Speed = ( deposition rate )×( # of passes )/5×( weight of weld metal {lb./ft} ) = (12)×(1)/5×(0.2887) = 8.31 IPM
Using Simple Methods For Calculating Starting Wire Feed Speed, Voltage, and Travel Speed
The Bartonian Conversion Factor (Table 2) makes things a bit easier for fillet welds. The example below uses the conversion factor to calculate travel speed at 5.57 IPM for that same 3/8 in. fillet weld using a 0.045 in. solid wire.
Travel Speed = 7.96×0.7 = 5.57 IPM (.2887)
The weight of weld metal per foot can be calculated for any join type by summing the volume and multiplying by the density of the weld metal (eg. 0.283 lb./in3 for steel). However, the values shown in Table 3 through Table 6 eliminate the need to do the calculation. These values are taken from Table 12-1 in The Procedure Handbook of Arc Welding by the Lincoln Electric Co., showing the Weight of Weld Metal per Foot for several common joint types welded with steel.
The following sample calculations use Tables 3 through 6.
1/2-in. plate V groove weld with 90° included angle and 1/8 in. reinforcement using 0.052 in. solid wire, 90%Ar/10%CO2 shielding gas. The manufacturer recommends WFS at 325 IPM and 30 volts.
Deposition Rate (lb./hr) = 13.1×(0.052)2×(325)×(1.0) = 11.51 lb./hr
Travel Speed for fill and cap passes = (11.51)×(6)/5×(0.849 + 0.199) = 13.18 IPM
Second Example Sample Calculation
3/8 in. plate square butt weld into a backing, with a 3/16 in. gap and 1/8 in. reinforcement using 1/16 in. cored wire, 75%Ar/25%CO2 shielding gas. Our process runs great with WFS at 285 IPM and 26 volts.
Deposition rate (lb./hr) = 13.1×(1/16 in.)2 × (285)×(.85) = 12.39 lb./hr
Travel speed for fill and cap passes = (12.39)×(1)/5×(0.239 + 0.053) = 8.49 IPM
Third Example of Sample Calculation
What should my wire-feed speed be if I want to make a fat, 1/4 in. fillet weld at 20 IPM travel speed using 0.045 in. solid wire and 90%Ar/10%CO2 shielding gas?
Re-arranging the Travel Speed calculation above to solve for Deposition Rate, we get:\
Deposition rate = 5×Travel speed×(Weight of weld metal {lb./ft})/(# of passes)
Deposition rate = 5×20 IPM×(0.165)/1 = 16.5 lb./hr
Re-arranging the Deposition Rate calculation above to solve for Wire-feed Speed, we get:
Wire-feed speed = Deposition rate/13.1×(Wire diameter)2×(Efficiency) = 16.5/13.1 ×(.045 in.)2×(1) = 622 IPM
Final Thoughts
Using math and simple formulas can help you reduce your weld-development time and improve your pre-WPS documentation. These calculations are usually correct, but you might need some tweaking to achieve the desired weld. Nevertheless, having a good starting point for welding procedure development will decrease time and guesswork on the shop floor.
Leave a Comment Cancel reply
WeLDingpros.net
Mentioned On:

Welding Machines
TIG Welders
MIG Welders
SMAW Welders
Plasma Cutters
Flux Core Welders
Multi Process Welders
Welding Guides
Welding Symbols PDF
How to MIG Weld
TIG Welding (GTAW)
Welding Joints
Best Welding Schools
Welding Stainless
Welding Helmets
1/1/1/1 VS 1/1/1/2
Change The Battery
Underwater Welding Helmet
Welding Gloves
Lens Shade Guide
Disclaimer Weldingpros.net is a participant in the Amazon Services LLC Associates Program, an affiliate advertising program designed to provide a means for sites to earn advertising fees by advertising and linking to amazon.com.
Amazon, the Amazon logo, AmazonSupply, and the AmazonSupply logo are trademarks of Amazon.com, Inc. or its affiliates.
As a YesWelder affiliate, I earn commissions for qualifying purchases.
Copyright © 2021 Weldingpros.net


"The Business of Metal Manufacturing"
- Additive Manufacturing Systems
- Automation/Robotics
- CAD/CAM Software
- Coil Handling Equipment
- Cut-To-Length Lines
- Deburring Machines
- Heat Treating
- Ironworkers
- Laser Cutting Systems
- Oxyfuel Cutting Systems
- Plasma Cutting Systems
- Press Brakes, Panel Benders
- Punch Presses
- Sawing Systems
- Stamping Presses
- Tube & Pipe Fabrication
- Turret Presses
- Engine Driven Welders
- Filler Metals/Electrodes
- Inverter Welders
- MIG Welders
- Plasma Cutters
- Power Sources
- Resistance Welders
- TIG Welders
- Welding Gloves
- Welding Guns/Torches
- Welding Helmets
- Wire Feeders
- Drilling Machines
- Gear Cutting Machines
- Grinding Machines
- Honing Machines
- Horizontal Machining Centers
- Laser Cutting
- Machine Controls
- Milling Machines
- Multitasking Machines
- Ram EDM Machines
- Turning Centers
- Vertical Machining Centers
- Wire EDM Machines
- Cutting Tools
- Drilling Tools
- Fixturing Systems
- Abrasives, Belts, Brushes, Grinding Wheels
- Positioners
- Punches and Dies
- Threading Tools
- Vises and Vise Jaws
- Ballbar Systems
- Bore Gauges
- Calibration
- Coordinate Measuring Machines
- Dial Indicators
- Go/No Go Gauges
- Laser Scanners
- Non-Destructive Testing
- Other Gauges and Gauging Equipment
- Surface Roughness/Finish
- Compressed Air
- Computerized Maintenance Management Systems
- Indoor Air Quality
- Industrial Cleaning/Waste Removal
- Lubricants, Coolants, Metalworking Fluids
- Machine Tool Repair and Rebuilds
- Roof Systems
- Spindle Repair and Rebuilds
- Adjustable Guards
- Body Protection
- Eye and Face Protection
- Fixed Guards
- Foot and Leg Protection
- Hand and Arm Protection
- Head Protection
- Hearing Protection
- Interlocked Guards
- Moveable Barriers and Gates
- Presence Sensing Devices
- Pullbacks/Restraints
- Regulatory Compliance
- Safety Mats
- Safety Trip Controls
- Self-Adjusting Guards
- Two Hand Controls
- General Lifts
- Hand Lift Trucks
- Other Material Handling Equipment
- Racks and Storage Equipment
- White Papers
- Supplier Directory
Category Menu

Pre-Calculating Wire-Feed Speed, Travel Speed and Voltage
It is possible for manufacturers that are welding with solid wire or flux-cored wire to calculate the starting wire-feed speed and travel speed? These calculations will get you close, but some tweaking may have to be done to achieve your desired weld.
Posted: December 1, 2010

A shop would like to decrease the development time for new MIG welds. Is there a way to pre-calculate wire-feed speed, travel speed and voltage, to get them close before they strike the first weld?
Yes, it is possible to calculate starting wire-feed speed and travel speed. This is a very common question from manufacturers welding with solid wire or flux-cored wire. Most welding professionals know the wire-feed speed (WFS), where a process runs well based on their experience, or can quickly get WFS from the manufacturer’s recommended procedures.
However, determining how fast to travel for a particular size weld bead ends up being an iterative, time-consuming process. By understanding a few concepts and doing some math with a few simple formulas, we can determine at least a good starting point for a welding procedure that produces the desired weld.
DEPOSITION RATE It is essential to recall that Deposition Rate is directly proportional to the speed at which a particular wire diameter emerges from a welding gun during welding. Deposition rate has nothing to do with how fast the gun is traveling, nor the voltage setting on the machine. Deposition rate is simply a measure of how many pounds of wire come from the welding gun in a certain amount of time, typically measured in lb/hr.
If wire-feed speed increases, deposition rate increases. We also understand that if we maintain the wire-feed speed and change to a larger diameter wire, deposition rate will increase as well. Armed with this understanding, calculating deposition rate ends up being a very powerful exercise that gives you a number that can be used to calculate key welding parameters. Let’s look at the formula and an example:
Deposition Rate Calculation Deposition rate (lb/hr) = 13.1 × (Wire diameter) 2 × (Wire-feed speed) × (Efficiency) — Wire diameter in inches (in) — Wire-feed speed in inches per minute (ipm) — Efficiency (1.0 for solid wire, 0.85 for cored wire) — This calculation is for steel only — e.g. : Wire diameter = 0.045 in (1.2 mm) solid wire, WFS = 300 ipm
Deposition rate = 13.1 × (0.045) 2 × (300) × (1.0) = 7.96 lb/hr
Calculating Travel Speed With Deposition Rate Knowing the deposition rate, we can calculate the travel speed in inches per minute (ipm) for a particular weld. Let’s say we want to make a 3/8 in steel fillet weld (assume 10 percent reinforcement or 0.4125 in leg) using 0.045 in solid wire at 300 ipm, the weight of weld metal per foot can be calculated by multiplying the density of steel (0.283 lb/in 3 ) by the volume of weld metal per foot as follows:
Weld Weight Per Foot Calculation Volume of weld metal/ft = 1/2 × b × h × 12 in = 1/2 × 0.4125 in × 0.4125 in × 12 in = 1.02 in 3
Weight of weld metal/ft of 3/8 in fillet weld = (0.283 lb/in 3 ) × (1.02 in 3 ) = 0.2887 lb/ft
From the calculation below, we see that the travel speed for a one-pass, 3/8 in fillet weld would be 5.52 ipm, 11.03 ipm for a two-pass fillet weld, or 16.55 ipm for a three-pass weld.
Travel Speed Calculation Travel speed = (deposition rate) × (# of passes)/5 × (weight of weld metal per foot {lb/ft}) = Travel speed = {7.96 x 1} / {5 x 0.2887} = 5.52 ipm
CALCULATING WIRE-FEED SPEED WITH DEPOSITION RATE Let’s assume a requirement to make fillet welds at a rate of 12 lb/hr using 0.045 in welding wire. We can calculate the WFS using the formulas below and Weight of Weld Wire per foot in Table 1 .
Wire-Feed Speed Calculation Wire-feed Speed = (deposition rate)/5 × (weight of wire per foot {lb/ft}) = (12)/5 × (0.0054) = 444.4 ipm
Of course, the travel speed for a one-pass 3/8 in fillet weld at a 12 lb/hr deposition rate would be 8.31 ipm as calculated below: Travel Speed = (deposition rate) × (# of passes)/5 × (weight of weld metal {lb./ft}) = (12) × (1)/5 × (0.2887) = 8.31 ipm
MAKING IT EASIER The Bartonian Conversion Factor (see Table 2 ) makes things a bit easier for fillet welds. The example below uses the conversion factor to calculate travel speed at 5.57 ipm for that same 3/8 in fillet weld using a 0.045 in solid wire.
Travel Speed = 7.96 × 0.7 = 5.57 ipm (.2887)
Weight of weld metal per foot can be calculated for any joint type by calculating the volume and multiplying by the density of the weld metal (eg. 0.283 lb/in 3 for steel). However, the values shown in Table 3 through Table 6 eliminate the need to do the calculation. These values are taken from Table 12-1 in The Procedure Handbook of Arc Welding by the Lincoln Electric Co., and show the Weight of Weld Metal per Foot for several common joint types welded with steel. The following sample calculations use Tables 3 through 6 .
SAMPLE CALCULATION NO.1 1/2 in plate Vee groove weld with 90 deg included angle and 1/8 in reinforcement using 0.052 in solid wire, 90%Ar/10%CO 2 shielding gas. Manufacturer recommends WFS at 325 ipm and 30 volts.
Deposition Rate (lb/hr) = 13.1 × (0.052) 2 × (325) × (1.0) = 11.51 lb/hr
Travel Speed for fill and cap passes = (11.51) × (6)/5 × (0.849 + 0.199) = 13.18 ipm
SAMPLE CALCULATION NO.2 3/8 in plate square butt weld into a backing, with a 3/16 in gap and 1/8 in reinforcement using 1/16 in cored wire, 75%Ar/25%CO 2 shielding gas. Our process runs great with WFS at 285 ipm and 26 volts.
Deposition rate (lb./hr) = 13.1 × (1/16 in) 2 × (285) × (.85) = 12.39 lb/hr
Travel speed for fill and cap passes = (12.39) × (1)/5 × (0.239 + 0.053) = 8.49 ipm
SAMPLE CALCULATION NO.3 What should my wire-feed speed be if I want to make a fat, 1/4 in fillet weld at 20 ipm travel speed using 0.045 in solid wire and 90%Ar/10%CO 2 shielding gas?
Re-arranging the Travel Speed calculation above to solve for Deposition Rate we get: Deposition rate = 5 × Travel speed × (Weight of weld metal {lb/ft})/(# of passes) = 5 × 20 ipm × (0.165)/1 = 16.5 lb/hr
Re-arranging the Deposition Rate calculation above to solve for Wire-feed Speed we get: Wire-feed speed = Deposition rate/13.1 × (Wire diameter) 2 × (Efficiency) = 16.5/13.1 × (.045 in.) 2 × (1) = 622 ipm
SUMMARY Using math and these simple formulas can reduce your weld-development time, and improve your pre-WPS documentation. These calculations will get you close, but some tweaking may have to be done to achieve your desired weld. Having a good starting point for welding procedure development will decrease time and guesswork on the shop floor.
Subscribe to learn the latest in manufacturing.
Industry news.

BLM GROUP Appoints New Intermountain Regional Manager
Jeremy George is the new regional sales manager covering Utah, Arizona, Colorado and New Mexico.

Mitsubishi Electric Automation Provides Automated Machine Tending Solution that Triples Output for Customer
TL Aerotek was looking for an automated solution to keep up with accelerating demand. The solution, they hoped, would alleviate the need for manual, constant machine tending. They turned to LoadMate Plus.

SEYI and Dallas Industries Introduce a Full Press Line
These two leading suppliers of metal forming machinery have partnered to provide a full press line at the SEYI-America showroom in Tullahoma, Tenn.
Sign Up For e-Newsletter
Calendar & events, design-2-part show, international manufacturing technology show (imts), fabtech 2024.

- The Fabricator
- Canadian Metalworking
- Our Publications
- E-Newsletter
- Digital Edition
- The Tube and Pipe Journal
- The Fabricator en Español
- Additive Manufacturing
- Aluminum Welding
- Arc Welding
- Assembly and Joining
- Automation and Robotics
- Bending and Forming
- Consumables
- Cutting and Weld Prep
- Electric Vehicles
- Hydroforming
- Laser Cutting
- Laser Welding
- Manufacturing Software
- Materials Handling
- Metals/Materials
- Oxyfuel Cutting
- Plasma Cutting
- Power Tools
- Punching and Other Holemaking
- Roll Forming
- Shop Management
- Testing and Measuring
- Tube and Pipe Fabrication
- Tube and Pipe Production
- Waterjet Cutting
Industry Directory
- Search the Directory (Showrooms)
- Buyers' Guides and Directories
- Product Showcases
- Classified Ads
- Register for the Directory
Our Affiliated Brands
- Fabricators and Manufacturers Association
- Nuts, Bolts & Thingamajigs Foundation
Account Login
- From The Fabricator
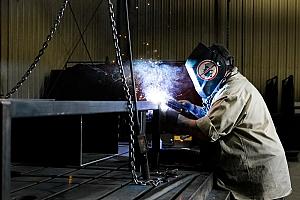
Young fabricators ready to step forward at family shop
How laser and TIG welding coexist in the modern job shop
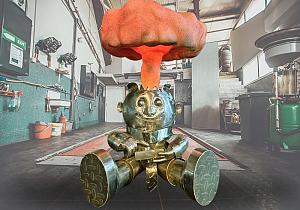
Fabricating favorite childhood memories
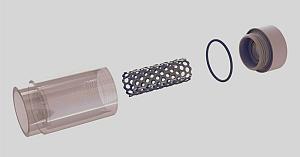
Tips for creating sheet metal tubes with perforations
- From The Welder
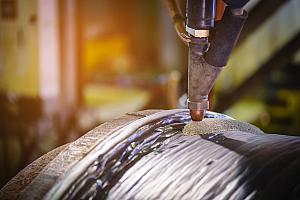
The role of flux in submerged arc welding performance
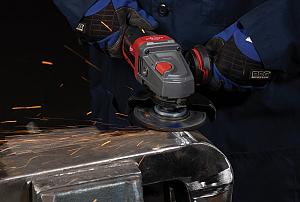
How welders can stay safe during grinding
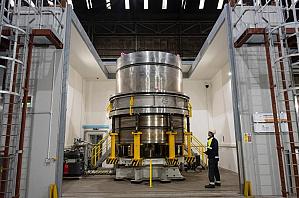
Sheffield Forgemasters makes global leap in welding technology
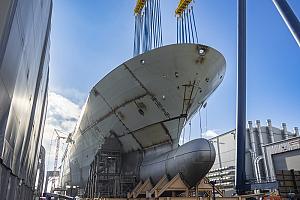
Launching a fleet revival at Seaspan shipyard
- From The Tube and Pipe Journal
Fabricator achieves extraordinary with simple approach
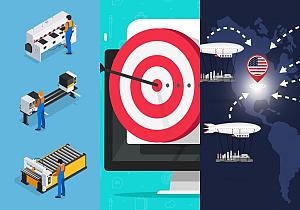
Three big issues fabricators must prioritize in 2024
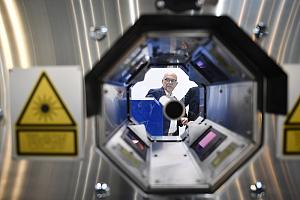
Tube 2024 to feature first-ever events
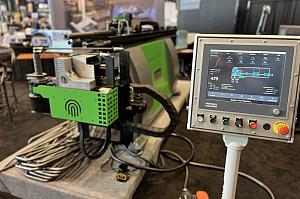
Decoding all the tube bender options
- From The Fabricator en Español
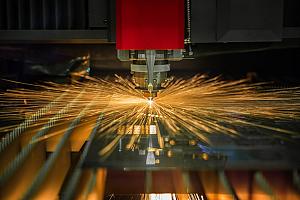
Anidado para la estabilidad del corte láser
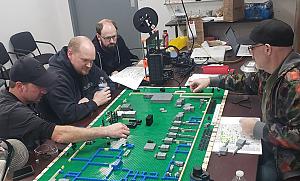
Prescripción para la reducción del desperdicio: arreglo esbelto de las instalaciones
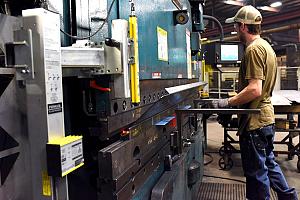
Los operadores de prensa dobladora inexpertos hacen indispensable el repensar la seguridad
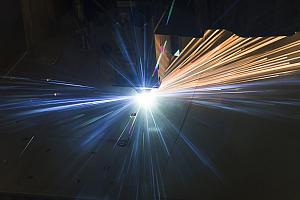
La mezcla de gas auxiliar impulsa la tecnología del láser de fibra
How amperage, wfs, voltage, travel speed, and shielding gas affect welding, why welders must consider all the variables.
- By Tre’ Heflin-King
- Updated December 7, 2023
- September 27, 2022
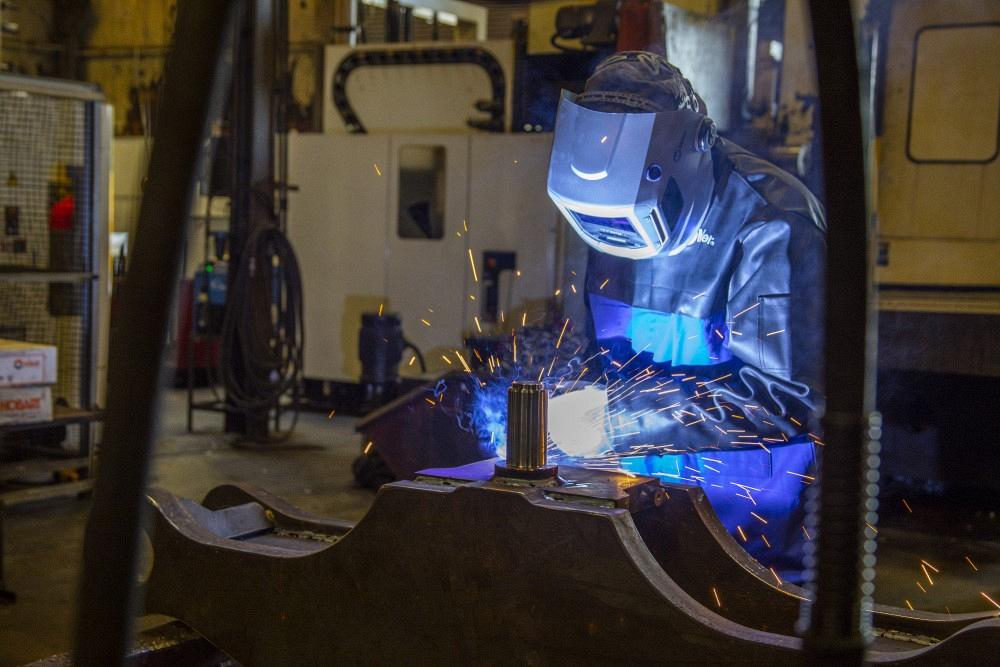
Properly maintaining welding variables is critical to establishing high weld quality in any operation.
Properly maintaining welding variables is critical to establishing high weld quality in any operation. Many companies put welding procedures in place that define the recommended parameters to help create consistency among welders and parts. Understanding what each welding variable in a procedure is and what it does can go a long way in helping welders meet productivity goals and reduce downtime and rework costs.
For constant voltage (CV) or CV welding with solid or tubular wires, welders must consider key welding variables and their functions and understand how they affect the process.
Welding Amperage
Welding amperage refers to the amount and speed of electricity flowing in a circuit, which affects the heat available to melt the welding wire and the base material. It is directly correlated to wire feed speed (WFS): the speed and volume of filler metal going into the weld. When WFS increases, so does the welding amperage; when it decreases, so does the amperage. This correlation, in turn, affects weld penetration. Higher amperage settings yield greater joint penetration while lower amperage settings provide less.
Welding amperage has an inverse relationship with contact-tip-to-work distance (CTWD), which is the distance from the end of the contact tip to the base material. Some also use the term to indicate the arc length in combination with the stick-out or how far the wire extends from the contact tip when it is flush with the nozzle. If an operator increases stick-out, welding amperage will decrease and vice versa. Changes to CTWD also affect weld penetration: the closer the contact tip is to the base material, the greater the penetration.
In addition, welding amperage affects melt-off rate—or how much wire is being used—along with weld bead appearance and heat input. Amperage that’s too high, particularly when welding with metal-cored wire, can result in a dull, flaky weld. Amperage also directly increases or decreases heat input and combined with travel speed has the largest effect on heat input. Heat input is calculated by the following:
(60 x Amps x Volts)/(1,000 x Travel Speed in IPM) = KJ/in.
Wire Feed Speed (WFS)
In addition to being directly correlated to amperage, the speed at which the electrode is advanced into the weld puddle also affects welding transfer modes. Higher WFS and voltage moves the process into a globular mode where large droplets of wire transfer across the arc to the weld pool. Increasing WFS (and therefore, amperage) and voltage allows for the use of a spray transfer mode. This mode sprays small droplets of wire to the weld pool and is known for being a smooth, easy-to-use process that improves productivity. That is especially true when paired with a metal-cored wire. The American Welding Society (AWS) “Welding Handbook, Volume 1” provides the approximate current needed to transition from a globular to a spray transfer mode.
Increasing WFS also provides higher deposition rates: the amount of filler metal added to a weld joint in a given period of time.
Lower WFS and voltage keeps the process in the range for short-circuit welding, in which the wire touches the base material and shorts from the contact that transfers the metal. This short can occur up to 200 times per second. Overall, it is a slower process with lower deposition rates.
Welding Voltage
Voltage refers to the electrical pressure that causes amperage to flow within the welding circuit. It is directly responsible for adjusting arc length. Higher welding voltage equals a longer arc; however, it also effectively decreases stick-out, resulting in higher amperages. That’s why it’s important for welders to maintain a constant stick-out when welding with a CV power source. Welding voltage also is directly correlated to heat input, so higher settings mean more heat. Increasing voltage also produces a wider arc cone.
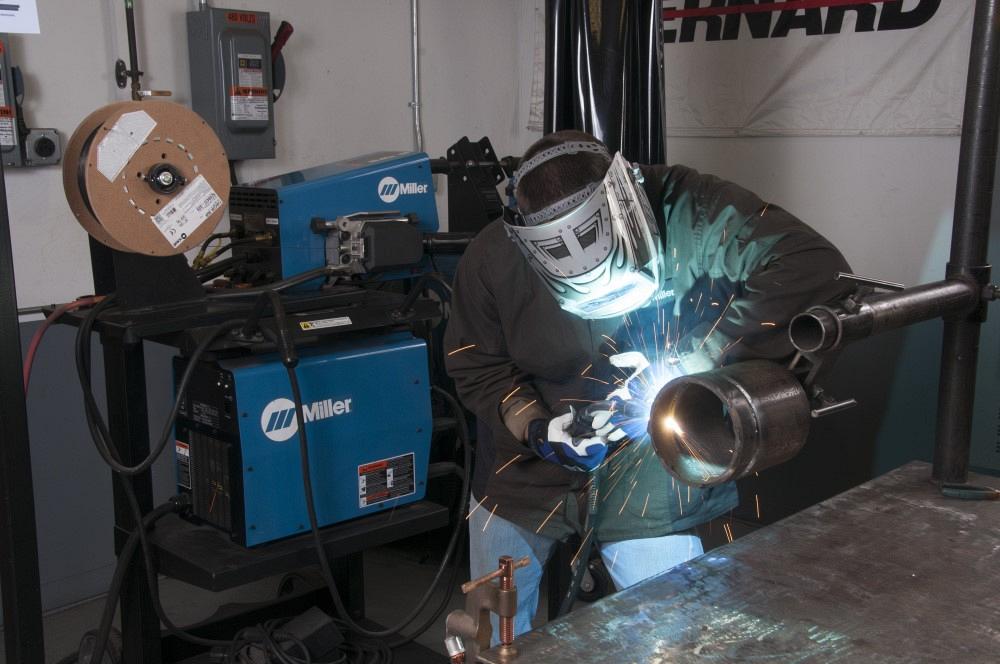
Welding variables relate to one another differently but ultimately work together to provide the desired weld performance.
Welding voltage affects the final weld in a variety of ways. If it is too high, the result will be a flatter bead and a concave weld profile. Voltage that is too high also can lead to undercut or a groove in the base material near the weld toe that isn’t filled with weld metal.
If welding voltage is too low, it can cause cold lap—a defect that occurs when the filler metal doesn’t fully fuse with the base material at the weld’s toes. Ropey or humped-up welds and excessive spatter can occur. For operators welding with long power cables, it’s important to know that voltage drops can occur at the point of welding despite the machine setting. For example, a power source may be set at 25 V but only be providing 23 V. This can also lead to cold lap.
Travel Speed
Travel speed simply refers to how fast the arc moves along the weld joint, measured in inches per minute (IPM). In semiautomatic operations, many welding operators feel comfortable with an average of 10 to 12 IPM, but more experienced operators may weld in the 18 to 20 IPM range. Travel speeds tend to be faster when welding with metal-cored wire due to its construction and internal composite powders.
Because changes in travel speed affect heat input, it’s important to take care when welding heat-sensitive materials, like aluminum. Welding faster will reduce heat input and prevent issues like burnthrough. Multipass welding on thick materials may require slower travel speeds to fill each pass and support good grain refinement.
Travel speeds that are too slow can lead to too much heat, a wide weld bead and poor penetration, while traveling too fast creates a narrow weld with insufficient weld toe tie-in. Maintaining a steady pace for the given weld joint is important.
Shielding Gas
Shielding gas, whether argon or carbon dioxide (CO 2 )—the most commonly used — has an impact on weld characteristics and welding performance. One hundred percent CO 2 shielding gas provides deep joint penetration on thicker material, but it does tend to have less arc stability and generate higher levels of spatter. Adding argon to CO 2 helps create aesthetically pleasing welds with less spatter. Shielding gas mixture with high levels of argon creates welds with higher tensile and yield strengths but lower ductility. High levels of CO 2 in the mixture improve ductility and crack resistance but decrease tensile and yield strengths.
Just as voltage and WFS affect welding transfer modes, so too does shielding gas.
For example, it’s possible to weld in short-circuit mode with solid and metal-cored wires using a blend of 75% argon and 25% CO 2 . Globular transfer welding with gas-shielded flux-cored wires requires 100% CO 2 , and at higher voltages, metal-cored wire can be paired with 80% argon and 20% CO 2 for welding thicker materials in the spray transfer mode.
Making It Work
Welding variables relate to one another differently but ultimately work together to provide the desired weld performance. For example, when welding on ½-in. thick mild steel, like A36, approximately 250 amps is a good target and provides sufficient root fusion in most cases. Using 90% argon/10% CO 2 gas mixture allows for welding in the spray transfer mode around 26 to 28 V and approximately 375 to 420 IPM WFS.
Maintaining proper variables helps to make the process cost-effective, keeps productivity goals in check, and produces sound welds.
About the Author
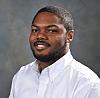
Tre’ Heflin-King
Applications Engineering Manager/CWI
Hobart Welding Products
See More by Tre’ Heflin-King
About the Publication
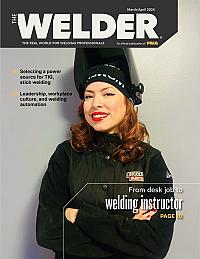
- View the Digital Edition
Subscribe to The Welder
subscribe now
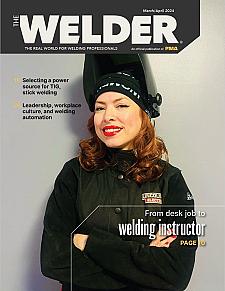
The Welder, formerly known as Practical Welding Today, is a showcase of the real people who make the products we use and work with every day. This magazine has served the welding community in North America well for more than 20 years.
- Stay connected from anywhere
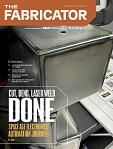
Easily access valuable industry resources now with full access to the digital edition of The Fabricator.
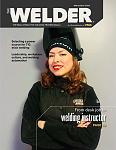
Easily access valuable industry resources now with full access to the digital edition of The Welder.
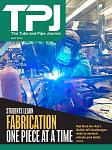
Easily access valuable industry resources now with full access to the digital edition of The Tube and Pipe Journal.
Easily access valuable industry resources now with full access to the digital edition of The Fabricator en Español.
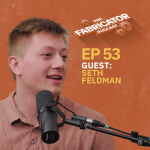
Seth Feldman of Iowa-based Wertzbaugher Services joins The Fabricator Podcast to offer his take as a Gen Zer...
- Listen to the Podcast
- Trending Articles
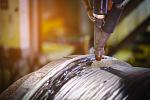
Aluminum MIG wires offer smooth feeding, reduced tangling
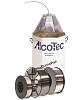
Connecticut students compete in Maritime Welding Competition
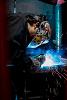
Three ESAB welding machines win Red Dot Awards for product design
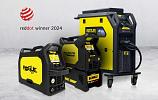
Power source added to cobot welding system for simplified automation
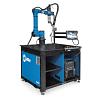
- Industry Events
Pipe and Tube Conference
- May 21 - 22, 2024
World-Class Roll Forming Workshop
- June 5 - 6, 2024
- Louisville, KY
Advanced Laser Application Workshop
- June 25 - 27, 2024
Precision Press Brake Certificate Course
- July 31 - August 1, 2024
Welcome back!
Forgot password?
Not yet registered? Sign up
- My Showrooms
- My Saved Guide Comparisons
- Change Password
- Change Personal Info

Stick welding basics: understanding arc length and travel speed
Stick welding, or Shielded Metal Arc Welding (SMAW), requires careful control of arc length and travel speed. Arc length should be about the same as electrode diameter. Short arcs provide deep penetration and less spatter. Travel speed affects weld quality; too fast may cause porosity, too slow can lead to excessive buildup.
Stick welding, also known as Shielded Metal Arc Welding (SMAW), is a popular welding method where an electric current forms an arc between the stick (or electrode) and the metals to be joined. The heat generated by the arc melts the metals, creating a joint when it cools down. As one of the oldest and most versatile welding processes, it’s widely used in various industries, from construction to automobile manufacturing.
Understanding the basics of stick welding, particularly the concepts of arc length and travel speed, is vital for any aspiring or professional welder. These elements significantly influence the quality of the weld, affecting its strength, appearance, and overall integrity.
In this blog post, we’ll delve into the specifics of stick welding, with a keen focus on arc length and travel speed. We’ll shed light on their importance, how to control them, and tips for optimizing your welding technique for the best results. Whether you’re a beginner or an experienced welder looking to brush up on your skills, this guide is for you. Let’s get started!
Before we jump into the nitty-gritty of arc length and travel speed, it’s essential to have a solid understanding of stick welding itself. So, let’s begin by demystifying what stick welding is, its significance, the fundamental components involved, and the different types of stick welding electrodes.
Table of Contents
Understanding Stick Welding
Before we dive into the specifics, let’s start by grounding our understanding in the basics of stick welding.
A. Definition of Stick Welding
Stick welding, also known as Shielded Metal Arc Welding (SMAW), is a manual arc welding process that uses a consumable electrode coated in flux to lay the weld. An electric current, either direct or alternating, is used to form an arc between the electrode and the metals being joined. This arc generates intense heat, which melts the electrode and the workpiece, creating a weld pool. When the weld pool cools and solidifies, it forms the joint.
B. Importance and Uses of Stick Welding
Stick welding is widely favored due to its simplicity, versatility, and cost-effectiveness. It can be used in a wide range of applications, from home DIY projects to heavy industrial fabrication and construction. It’s effective on various types of metals, including steel, stainless steel, and cast iron, making it a staple in sectors like shipbuilding, automotive repair, and pipe welding.
C. Basic Components and Setup of Stick Welding
The primary components of a stick welding setup include a power source, electrode holder, ground clamp, and welding electrodes. The power source provides the electric current necessary for the arc, while the electrode holder and ground clamp form the electrical circuit.
In terms of setup, the power source is connected to the electrode holder and the workpiece. The electrode is then inserted into the holder, and the ground clamp is attached to the workpiece. Once everything is set, you’re ready to strike the arc and begin welding.
D. Common Types of Stick Welding Electrodes
Stick welding electrodes come in various types, each designed for specific applications and materials. The American Welding Society (AWS) classifies these electrodes, with common types including E6010, E6011, E6013, E7018, and E7024.
For instance, E6010 electrodes are known for deep penetration and are typically used on dirty or rusty materials. On the other hand, E7018 electrodes offer strong welds with low hydrogen content, making them ideal for high-strength steels.
In our subsequent sections, we’ll see how understanding these basics plays a significant role when dealing with arc length and travel speed. These two elements are vital in manipulating the weld’s quality and overall outcome, ensuring we achieve a strong and durable weld joint.
With a firm understanding of stick welding and its key components, we are now well-equipped to delve deeper into one of the critical parameters that greatly affect the quality of your weld: the arc length. In the following sections, we’ll define what arc length in stick welding is, explore its importance, and discuss the factors that influence it.
Mastering the Arc Length
Navigating the world of stick welding necessitates a thorough understanding and mastery of arc length. Let’s dive into what this means.
A. Definition of Arc Length in Stick Welding
In stick welding, the arc length refers to the distance between the tip of the electrode and the base metal, or the workpiece. It’s usually equivalent to the diameter of the metal core of the electrode. For instance, if you’re using a 1/8 inch electrode, the ideal arc length would be approximately 1/8 inch.
B. Importance of Correct Arc Length in Welding
Maintaining the correct arc length is vital for producing a high-quality weld. If the arc length is too short, it could cause the electrode to stick to the workpiece, leading to a rough and irregular weld bead. On the other hand, if the arc length is too long, it might result in excessive spatter, a wider and shallower weld bead, and could even lead to undercutting. Thus, mastering the right arc length is crucial for a neat, strong, and durable weld.
C. Factors that Influence Arc Length
Several factors can influence the arc length in stick welding. These include the type of electrode being used, the welding current, and the welder’s technique.
- Electrode Type: Different types of electrodes require different arc lengths. For instance, a rutile electrode typically needs a longer arc length, while a basic electrode requires a shorter arc.
- Welding Current: The welding current also affects the arc length. A higher current tends to shorten the arc length, while a lower current lengthens it.
- Welder’s Technique: The welder’s skill and technique significantly impact the arc length. A skilled welder can maintain a consistent arc length, leading to a better-quality weld.
In the next section, we’ll discuss how to control the arc length effectively and explore the potential problems and solutions related to it. By mastering arc length, we can significantly improve our welding outcomes, resulting in stronger and more reliable welds.
D. Techniques to Control Arc Length
Maintaining a consistent arc length is crucial for creating a quality weld, and there are several techniques that can help you achieve this:
- Proper Stance and Positioning: Ensuring a comfortable and stable stance can help you control your movements better, leading to a more consistent arc length.
- Use of Guides: Using a guide or a rest for your hand can help stabilize your movement and maintain the electrode at a consistent distance from the workpiece.
- Practice: Like any skill, practice is key. Regularly practicing your welding with different types of electrodes and on various materials can help you get a feel for maintaining the appropriate arc length.
- Watch the Puddle, Not the Arc: Instead of focusing on the arc, observe the weld puddle. The size and shape of the weld puddle can give you a good indication of whether your arc length is correct.
E. Potential Problems and Solutions Related to Arc Length
While welding, you may encounter some issues related to arc length. Here are a couple of common problems and their solutions:
- Sticking Electrodes: If your electrode frequently sticks to the workpiece, your arc length might be too short. Try to increase it slightly.
- Excessive Spatter or Undercut: If you’re experiencing excessive spatter or undercut, your arc length might be too long. Reducing the arc length can help to alleviate these issues.
Remember, controlling the arc length effectively can take some time and practice. Don’t be discouraged if you don’t get it right immediately. With time and persistence, you’ll soon be able to maintain a consistent arc length, enhancing the quality of your welds significantly.
In the next section, we’ll move on to another crucial aspect of stick welding – the travel speed. Just like the arc length, mastering the travel speed is vital for creating strong and high-quality welds.
Now that we have explored the arc length and its significance in the stick welding process, it’s time to turn our attention to another critical variable: the travel speed. Understanding and mastering travel speed can significantly improve your welding results. In this section, we’ll define travel speed in welding, discuss its role in weld quality, and offer some tips on how to control it effectively.
Understanding Travel Speed in Stick Welding
Travel speed plays a vital role in the stick welding process, and its mastery is just as important as controlling the arc length. Let’s delve deeper into this subject.
A. Definition of Travel Speed in Welding
In welding, travel speed refers to the rate at which the welding arc moves along the joint being welded. It is typically measured in inches per minute (IPM) or millimeters per minute (mm/min). In stick welding, the travel speed can significantly influence the shape and quality of the weld bead.
B. Role of Travel Speed in Determining Weld Quality
Travel speed plays a crucial role in determining the shape, penetration, and overall quality of the weld.
- Shape: A slower travel speed can lead to a wider, more convex weld bead, while a faster travel speed tends to produce a narrower, more concave bead.
- Penetration: Similarly, slower travel speeds result in deeper penetration, while faster speeds lead to shallow penetration.
- Defects: Incorrect travel speed can also cause various welding defects. For instance, a travel speed that’s too fast may lead to lack of fusion or undercut, while a speed that’s too slow can result in excessive penetration or burn-through.
C. How to Control Travel Speed for Optimal Results
Maintaining an optimal travel speed is a matter of skill and experience. Here are a few tips to help you master it:
- Consistent Movement: Try to maintain a steady and consistent movement along the joint. This can be facilitated by a comfortable stance and using your arm and hand in a way that allows smooth, controlled movement.
- Watch the Puddle: Keep an eye on the weld puddle. It should maintain a consistent size and shape if your travel speed is correct.
- Practice: Just like with arc length, practice is crucial. The more you weld, the better feel you’ll get for the right travel speed.
Mastering travel speed is critical for achieving high-quality welds. In the following section, we’ll discuss the relationship between travel speed, arc length, and bead shape, and highlight common travel speed mistakes and how to avoid them.
D. The Relationship Between Travel Speed, Arc Length, and Bead Shape
Travel speed, arc length, and bead shape are all interrelated in the welding process.
- Travel Speed and Bead Shape: As mentioned earlier, a slower travel speed leads to a wider, more convex bead and deeper penetration, while a faster speed results in a narrower, more concave bead with shallower penetration.
- Arc Length and Bead Shape: A shorter arc length tends to produce a narrower bead with deeper penetration, while a longer arc length results in a wider bead with less penetration.
- Interaction Between Travel Speed and Arc Length: The interplay between travel speed and arc length is also crucial. For instance, a short arc length combined with a slow travel speed can lead to a high degree of penetration but might also create a large, convex bead. Conversely, a long arc length paired with a high travel speed could result in a shallow, wide bead.
Understanding these relationships can help you adjust your technique to achieve the desired bead shape and penetration, enhancing the overall quality of your weld.
E. Common Travel Speed Mistakes and How to Avoid Them
Mistakes in travel speed are common, especially among beginners. Here are some of the most common ones and tips on how to avoid them:
- Traveling Too Fast: This is one of the most common mistakes. It leads to shallow penetration and potential for lack of fusion. To avoid this, practice maintaining a consistent speed and watch the weld puddle to ensure it’s not getting too small or moving too quickly.
- Traveling Too Slow: This can cause excessive penetration or even burn-through, especially on thinner materials. It can also result in a large, convex weld bead. If you notice the weld puddle getting too large or the weld bead becoming excessively convex, you might need to increase your travel speed.
- Inconsistent Travel Speed: Inconsistency in travel speed can lead to an irregular bead appearance and inconsistent penetration. Try to maintain a steady pace and use a guide or rest your hand, if needed, to help control your movement.
Remember, mastering travel speed, like any other welding skill, comes with practice. Don’t be discouraged by mistakes – instead, use them as learning opportunities to improve your technique.
In the next section, we’ll provide some tips for improving your stick welding techniques overall, focusing on maintaining appropriate arc length and travel speed. With a bit of patience and a lot of practice, you’ll see your welding skills improve significantly.
Having delved into the critical aspects of arc length and travel speed in stick welding, it’s now time to provide some practical tips to help improve your stick welding techniques overall. In this section, we’ll cover some best practices for maintaining appropriate arc length and travel speed, offer advice for troubleshooting common stick welding problems, discuss important safety measures, and stress the importance of practice in mastering this skilled craft.
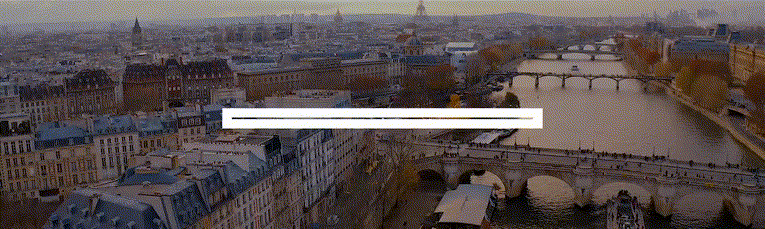
Tips for Improving Stick Welding Techniques
Mastering stick welding is a continuous journey, and even experienced welders continue to learn and refine their techniques. Here are some tips to aid you on your journey.
A. Best Practices for Maintaining Appropriate Arc Length and Travel Speed
- Maintain a Steady Hand: Keeping your hand steady can help maintain a consistent arc length and travel speed. You can also use a guide or rest to stabilize your hand.
- Watch the Weld Puddle: The weld puddle provides essential visual feedback. If it’s too large or too small, you may need to adjust your arc length or travel speed.
- Use the Right Electrode: Different electrodes require different arc lengths and travel speeds. Make sure you understand the specifications of your chosen electrode.
- Adjust for Different Positions: Welding in different positions (flat, horizontal, vertical, overhead) may require adjustments to both arc length and travel speed.
B. Advice for Troubleshooting Common Stick Welding Problems
- Sticking Electrodes: If your electrode is sticking, your arc length may be too short. Try increasing it slightly.
- Excessive Spatter or Undercut: These issues could indicate your arc length is too long or your travel speed is too fast. Try reducing either or both.
- Poor Penetration or Fusion: These could be signs of a travel speed that’s too fast. Slow down and watch the weld puddle for feedback.
C. Safety Measures to Take While Stick Welding
Safety is paramount when welding. Here are some important measures to take:
- Wear Appropriate PPE: This includes a welding helmet, gloves, and flame-resistant jacket.
- Ensure Good Ventilation: Welding can produce harmful fumes, so ensure you’re working in a well-ventilated area or use a fume extraction system.
- Avoid Electric Shock: Always wear dry gloves, and don’t touch the electrode or metal parts of the electrode holder with skin or wet clothing.
D. Importance of Practice in Mastering Stick Welding
There’s no substitute for practice when it comes to improving your stick welding skills. The more you practice, the better you’ll become at controlling arc length and travel speed, and the higher the quality of your welds will be. Don’t be afraid to make mistakes – they’re just learning opportunities in disguise.
In conclusion, mastering stick welding is a journey of continuous learning and practice. Understanding and controlling arc length and travel speed are critical steps on this journey. So, don your helmet, fire up your welder, and get practicing!
To further illustrate the importance of proper arc length and travel speed in stick welding, let’s dive into a real-world case study. This will give us a chance to see these principles in action, understand how experienced welders manage these variables, and draw valuable lessons that we can apply in our own welding projects.
Case Study: Real-world Application of Proper Arc Length and Travel Speed
Case studies can offer invaluable insights, especially in a practical field like welding. By examining the techniques used by experienced welders, we can learn and improve our skills.
A. Explanation of the Chosen Case Study
In this case study, we’ll look at a large-scale industrial project – the construction of a high-pressure steam boiler. Stick welding was extensively used in this project, particularly in welding the boiler’s thick steel plates. The welds had to be of the highest quality, as the boiler would operate under high pressure, and any weld failure could have serious consequences.
B. Breakdown of How the Welder Managed Arc Length and Travel Speed
The welder in our case study was highly experienced and had developed an innate understanding of managing arc length and travel speed.
- Managing Arc Length: The welder maintained a short arc length – roughly equal to the diameter of the electrode. This helped ensure deep penetration and reduced the risk of undercutting or porosity.
- Controlling Travel Speed: The welder used a steady, moderate travel speed. This allowed the weld to cool sufficiently, reducing the risk of burn-through and ensuring adequate fusion. The welder also watched the weld puddle closely, adjusting his travel speed as necessary to maintain a consistent bead profile.
C. Lessons Learned from the Case Study
This case study provides a number of valuable lessons:
- Importance of Experience: The welder’s experience played a key role in managing arc length and travel speed effectively. This highlights the importance of practice and hands-on experience in mastering these skills.
- Attention to Detail: The welder’s close attention to the weld puddle and his willingness to adjust his technique as necessary were crucial in achieving high-quality welds.
- Safety and Quality: The high-stakes nature of the project underscored the importance of welding quality and safety. Proper management of arc length and travel speed were key to ensuring the integrity and safety of the final product.
By studying real-world applications of stick welding techniques, we can gain insights and learn valuable lessons that can help us improve our own welding skills. Remember, every welding project offers a learning opportunity, so keep practicing, stay curious, and continue refining your skills.
Stick welding is an essential skill in various industries, from construction to manufacturing. Mastering this craft involves understanding and controlling several key variables, with arc length and travel speed being among the most crucial. These factors directly influence the quality of your welds, affecting penetration, bead shape, and the likelihood of defects.
Through this post, we’ve explored these concepts in depth, offering practical advice and tips to improve your stick welding techniques. We’ve also examined a real-world case study that underscores the importance of these principles in achieving high-quality, safe, and reliable welds.
However, as with any practical skill, the knowledge is only half the battle. The real mastery comes from hands-on practice, continual learning, and the willingness to make and learn from your mistakes. So don’t be afraid to get out there, start welding, and begin your journey towards becoming a proficient stick welder.
Remember, every welder was once a beginner. With patience, diligence, and the right approach, you too can master the art of stick welding. We hope that this guide serves as a valuable resource on your welding journey, helping you to understand and perfect the critical aspects of arc length and travel speed in stick welding. Happy welding!
Leave a Comment Cancel reply
Save my name, email, and website in this browser for the next time I comment.
How to Calculate Travel Speed in Mig Welding: A Comprehensive Guide
How to calculate travel speed in mig welding.
To calculate travel speed in MIG welding, you need to use the Travel Speed calculator.
This calculator uses the time taken to complete the weld, the weld length, welding amps, and volts to determine the travel speed.
It utilizes two formulas to calculate the heat input.
It is important to calculate the travel speed accurately to ensure proper feed speed in MIG welding.
Improper feed speed can result in weak weld joints or burn holes in the metal.
MIG welding machines automatically feed wire through the torch head to the weld site, and the wire acts as the electrode to create the weld bead and filler material.
The MIG wire must be fed at the appropriate speed to ensure a proper joint is created.
Did You Know?
1. The speed of travel in MIG welding is typically measured in inches per minute (IPM) or centimeters per minute (CPM). However, did you know that the optimal travel speed can vary depending on the material being welded? For example, when welding aluminum, the travel speed should be slower compared to welding steel or stainless steel.
2. One factor that can affect travel speed in MIG welding is the welding position. It is generally easier and faster to weld in the flat or horizontal positions compared to vertical or overhead positions. So, if you’re looking to increase your travel speed, try to weld in a favorable position whenever possible.
3. Travel speed can have a significant impact on the quality of the weld. Welding too slowly can result in excessive heat input, leading to distortion, burn-through, or lack of fusion. Conversely, welding too fast can result in insufficient heat input, causing poor penetration and weak welds. Therefore, finding the right balance and maintaining a consistent travel speed is crucial for achieving high-quality welds.
4. The type and size of the welding wire you use can also influence the travel speed in MIG welding. Thicker wires typically require higher travel speeds, while thinner wires require slower travel speeds. Additionally, selecting the proper wire feed speed and voltage settings for your specific wire diameter can help optimize travel speed and overall welding performance.
5. It’s important to note that travel speed is not the sole determinant of productivity in MIG welding. Other factors, such as proper joint preparation, suitable shielding gas, and appropriate welding techniques, also play a significant role. Keeping these aspects in mind and adjusting the travel speed accordingly can help you achieve efficient and high-quality MIG welds.
Introduction To Travel Speed Calculator In Mig Welding
MIG welding , also known as Gas Metal Arc Welding (GMAW) , is a versatile welding process widely used in various industries. The travel speed calculator is an essential tool that aids in determining the optimal travel speed for MIG welding.
By finding the right travel speed , welders can ensure the creation of strong and durable weld joints. The calculator requires specific inputs, including:
- The time taken to complete the weld
- The length of the weld
- Welding amps
With this information, the calculator employs two formulas to calculate the heat input , which is a crucial factor in determining the travel speed.
Required Inputs For Travel Speed Calculation
To effectively utilize the travel speed calculator, the following key inputs must be provided:
- Time taken to complete the weld : This refers to the duration it takes to finish the welding process.
- Length of the weld : It is the distance that needs to be covered during welding.
- Welding amps and volts : These represent the electrical parameters set on the welding machine. These values directly impact the heat input and consequently determine the travel speed.
Accurate measurements and data are crucial for the calculator to provide reliable results.
The Importance Of Heat Input Calculation In Mig Welding
The heat input calculation in MIG welding is crucial for ensuring the quality and integrity of the weld joint. It refers to the total amount of heat energy transferred to the weld, and is a critical parameter in determining the proper travel speed needed to achieve a sound weld .
Accurate heat input calculation is vital to ensure that the weld metal is adequately melted and fused together. Incorrect calculations can result in incomplete fusion or overheating , leading to weak weld joints and potential failure under stress.
The travel speed calculator utilizes the heat input calculation to determine the optimal travel speed , which greatly contributes to the overall success and durability of the welded joint.
– Importance of heat input in MIG welding:
- Determines quality and integrity of weld joint
- Critical for achieving a sound weld
- Ensures adequate melt and fusion of weld metal
– Consequences of incorrect heat input calculation:
- Incomplete fusion or overheating
- Weak weld joints
- Potential failure under stress
– Utilization of travel speed calculator:
- Determines optimal travel speed
- Enhances overall success and durability of weld joint
“The heat input calculation in MIG welding is of utmost importance as it directly affects the quality and integrity of the weld joint.”
Effects Of Improper Feed Speed In Mig Welding
Proper feed speed is crucial in MIG welding as improper feeding can have detrimental effects on the resulting weld joint. Inadequate wire feed speed , either too slow or too fast , can lead to various issues such as weak weld joints or burn holes in the metal.
Insufficient wire feed speed can result in a lack of proper fusion between the weld metal and the base metal. This can lead to weak weld joints that are prone to failure under stress . On the other hand, excessive wire feed speed can create excessive heat , causing burn holes in the metal.
It is essential to ensure that the wire feed speed is at an appropriate level to guarantee the creation of a sound and durable weld joint . The travel speed calculator aids in determining the suitable wire feed speed by considering the specific parameters and requirements of the welding process.
Understanding The Role Of Mig Wire In Creating Weld Joints
In MIG welding , the wire acts as the electrode , creating the weld bead and serving as the filler material to join metal pieces. The MIG wire plays a critical role in the welding process, as it determines the composition and strength of the weld joint.
The MIG wire must be carefully selected based on the materials being welded and the desired mechanical properties. Different types of MIG wires, such as solid wires and flux-cored wires , have various applications and advantages. Solid wires are commonly used for welding mild steel , while flux-cored wires are suitable for welding in outdoor or windy conditions .
Understanding the role of the MIG wire allows welders to select the appropriate wire for the job at hand, ensuring optimal performance and strong weld joints .
- MIG welding uses the wire as the electrode, weld bead, and filler material.
- The composition and strength of the weld joint depend on the MIG wire selected.
- Different types of MIG wires, such as solid and flux-cored wires, have specific applications.
- Solid wires are suitable for welding mild steel, while flux-cored wires are ideal for outdoor or windy conditions.
“The MIG wire determines the composition and strength of the weld joint.”
Significance Of Proper Wire Feed Speed In Mig Welding
Proper wire feed speed is crucial in MIG welding as it directly impacts the quality and strength of the weld joint. The wire must be fed at the correct speed to ensure the creation of a proper joint.
If the wire feed speed is too slow , there may be insufficient filler material to adequately fill the weld joint, resulting in weak or incomplete fusion . Conversely, if the wire feed speed is too fast , excessive heat may be produced, potentially leading to burn-through or distortion .
By utilizing the travel speed calculator , welders can determine the appropriate wire feed speed needed for a particular welding project. This ensures the creation of strong, durable, and high-quality weld joints that meet industry standards and requirements .
In conclusion , the travel speed calculator plays a vital role in MIG welding by helping calculate the optimal travel speed . Accurate inputs and calculations aid in determining the appropriate heat input , which directly influences the quality and strength of the weld joint. By understanding the significance of proper wire feed speed and selecting the appropriate MIG wire , welders can ensure the creation of sound and durable weld joints .
Frequently Asked Questions
How do you calculate mig welding speed.
To calculate MIG welding speed, you need to multiply the required amperage of the weld by the burn rate associated with the wire’s diameter. For instance, if the required amperage is 125 amps and the wire’s burn rate is 2 inches, the feed speed can be calculated as 250 inches per minute. This formula helps determine the appropriate feed speed for achieving the desired welding result.
What is the formula for travel speed in welding?
The formula for travel speed in welding can be determined by dividing the length traveled (l) by the time taken (t) to travel that length. In this case, with a length (l) of 150 mm and a time (t) of 68 s, the travel speed can be calculated as 150 mm / 68 s = ~2.2 mm/s or 132 mm/min. Therefore, the formula for travel speed in welding is l / t.
What is the formula for travel speed?
The formula for calculating travel speed is derived from the relationship between distance travelled and the time taken. By dividing the distance by the time, we can determine the average speed at which an object has traveled. This relationship is represented in the formula: speed = distance ÷ time. By applying this formula, we can quantify and understand the speed at which objects move in relation to the distance covered and the time it took.
How do you calculate MIG welding parameters?
To calculate MIG welding parameters, it is crucial to understand the relation between material thickness and required output amperage. As a rule of thumb, for every .001 inch of material thickness, 1 amp of output is needed. For instance, a .125 inch thickness warrants 125 amps for optimum welding performance. Thus, determining the appropriate wire size becomes pivotal and should be chosen accordingly to match the designated amperage for a successful MIG welding operation.
Related Articles
What is welding electrode specification and its importance, how to protect welding mask from damage: top tips, can welding burn your face understanding the hazards, precautions, and prevention measures, how to install glasspack without welding: a stepbystep guide, adblock detected.
- Flow Limiter
- Cable Cover
- Current Specials
- Weld Quality
With a fixed wire feed speed the amperage decreased from 200 amps with a 3/8 inch stickout to a low of 154 amps when the stickout was increased to 7/8 inches. The resistance heating of the wire (the 2nd Amp 2 term in the equation) is a very efficient heating process. Therefore the current needed to finish melting the wire as it enters the arc, becomes less as the wire is hotter with longer stickout.
However there is a reduction in weld penetration when varying stickout in a normal range from 3/8 to 3/4 inches is 24%! If extended to 7/8 inches penetration decreases 29%.
Therefore it is very important to keep the torch stickout constant. Also the shorter the distance from tip to work for a fixed wire feed speed the greater the penetration since current also increases. When welding in the short circuiting mode it is often desirable to use a long contact tip which protrudes from the shielding gas cup. This helps assure adequate penetration is maintained by keeping current higher. It also helps visibility so the welder can stay on the leading edge of the weld puddle.
The picture right is from our recently published book and is one of several examples presented of the effects of MIG welding parameter changes on weld performance. See Book Details on Current Speicals Offers Page
Weld Penetration Definition
For the purposes of this exercise, weld penetration is a measure of how deep the weld penetrates in a bead-on-plate deposit. Have a different wire than the 0.035 inch solid wire used in this example? No problem. In fact not only changes in wire type and size but also shielding gas and torch angle will alter the actual value. You can generate your own constant K for what you are doing by making a bead-on-plate deposit, cutting a cross section and etching it.
Caution About the Use of This Approach
The above equations are designed to work within a practical range for normal MIG welding. There are much more elaborate equations that take into account the variable resistively of material with temperature, other arc effects etc. However within a range of normal operation the above approach will work adequately. As mentioned, you may need to develop your own coefficients. Make a weld, measure the depth of penetration and work backwards! That is what Clarence Jackson did with thousands of data points!
Reference (1): AWS Welding Handbook, Volume 1, 9 th Addition; pp 79
Reference (2): “The Science of Arc Welding” by C. E. Jackson. 1960 Welding Journal 39(4) pp 129-s thru 230-s
========== =========== ==========
"Advanced Automotive Welding"
Author: Jerry Uttrachi
(President of WA Technology)
Great book for welding students to also learn some welding math and science.
CLICK for Book Details
Review by Editors of Hemmings Motor News; August 2012
"Advanced Automotive Welding" by Jerry Uttrachi
Welding is a hot topic in the hobby these days. For less than $500 a do-it-yourselfer can purchase a good quality welder and start laying beads or zapping in spot welds.
This kind of accessibility to a once specialized skill is excellent for the hobby, and we encourage everyone with an interest to learn to weld. Just as important as buying the gear, however, is getting versed in the many different processes, techniques and materials used in all types of welding. A class at a local welding school or a community college is a good place to start, as is the purchase of a book like Advanced Automotive Welding, part of Car Tech’s SA Design series.
Despite the “Advanced” in the title, the book is a good resource for beginning and intermediate welders. The author, Jerry Uttrachi, is a former American Welding Society President, with 40 years of welding experience, as well as a car enthusiast, and he writes in a clear, mostly jargon free style.
The book covers all welding processes, as well as cutting processes, and includes insight into some car related welding projects. Advanced Automotive welding is a good addition to any budding or experienced metal worker’s shelf.
========== =========== ==========
Gas Pressure/Volume Calculations
In 1662 Robert Boyle defined the basic relationship between gas Pressure and Volume. He stated the relationship in mathematic terms as:
P 1 / P 2 = V 1 / V 2 (Where P, pressure, is measured as absolute pressure =
gauge pressure + 14.7 psi at sea level)
For example, in a MIG gas delivery hose if the initial absolute pressure is doubled the gas volume must be double. That was until 140 years later when around 1800 both Charles and Dalton independently added temperature to the relationship! They defined the following relationship:
V 1 / V 2 = T 1 / T 2 (Where T, Temperature is measured as absolute Temperature in degrees Rankin = Degrees Fahrenheit gauge + 460)
Applying this equation we'll see in general we need not worry about temperature effecting volume in normal ranges:
i.e. V 1 / V 2 = T 1 / T 2
If T 1= 75 F than T1 Rankin = 75+460=535 R
Assume T2 = T1 + 20% =90 deg F; then T2 Rankin = 90+460=550 R
V1/V2 due to 20 % Temp Difference =
V 1 / V 2 = T 1 / T 2 = 535/550=0.97
O r at a constant pressure, an increase in Temperature of 20% measured in degrees Fahrenheit yields only 3% increase in volume. For most welding purposes and over the range of production temperatures there is not enough change in Volume with gas Temperature to consider it significant.
The general Gas Laws can be written as:
(P 1 X V 1) / T 1 = (P 2 x V 2 ) / T 2
It can also be written as P x V = (nR) T
where the constants nR can defined based on the gas. We'll let you find details about the nR by searching the Internet since for our purposes ratio comparisons are all we need.
MIG WELDING EXAMPLE
The pressure needed in the gas delivery hose from gas source to welder/feeder to flow 30 CFH is 3 psi.
A regulator/flowmeter is used that utilizes an 80 psi regulator.
Therefore when welding stops gas continues to flow through the needle valve flow control until the pressure in the gas delivery hose equals 80 psi.
Then the volume of excess gas in the gas delivery hose compared to the volume when welding will be:
V stopped / V welding = P stopped / P welding =
( 80 psi +15) / ( 3 psi + 15) = 5.3 times the physical hose volume
Hose Expansion Causes More Excess Volume: Tests of a standard 1/4 inch diameter gas delivery hose showed it had a 13% increased volume due to the hose expanding with 80 psi pressure. Therefore 87% of the excess gas stored in the hose is due to the increased Pressure and 13% of the excess due to Hose Expansion. SEE MORE DETAILS .
Excess Gas Blasts Out of the MIG Torch When Welding Starts: The high velocity creates turbulence in the shielding gas stream which takes several seconds to stabilize to a desirable smooth Laminar flow. The turbulence pulls in air causing excess spatter and internal weld porosity. For a typical 5/8 inch diameter MIG nozzle more than 50 CFH flow rate causes this turbulent flow. For a smaller 1/2 inch diameter nozzle flow rates should not exceed about 40 CFH.
Was This Welding Math Information Useful? What Other Math Would You Like To See?
CLICK ICON to Download PDF DOWNLOAD
Brad Weaver, Science Teacher
Belmont Career and Technical Education Center Sent This Email Requesting:
"..permission to use the wonderful materials you have produced on welding math and physics with the students here at our career and technical education center. As the science teacher at the center, I am always looking for ways to instruct key science and math concepts and skills in the context of the technical programs. When the lesson materials come from their field of study, it is more meaningful to the students for the direct application of science and math. In searching for materials on instruction regarding the use of the ruler, I came across your website, and shared it with our welding instructor, Mr. Greg Hutchison." We would like to incorporate your materials into our lessons."
We Thanked Brad and Gave Permission
Mrs. Vicki S. Morrow, a Mathematics Teacher Asked:
“Would it be possible for me to print out and share your welding math information with a specific student? He attends my school part-time and a trade school the remainder of the time. I thought I could make math more relatable to him because he is studying welding and is very interested in the subject. I really appreciate the information available on your site."
After providing permission she emailed and said:
"Thank you so much. Your site is perfect for what I need for my student."
See YouTube Video Discussion of Our
Patented Shielding Gas Saver System
Also shows some Bernoulli gas equations
CLICK HERE OR PIC OF OUR STREET ROD
See "Welding; Go Green" Video
CLICK Here or Picture Left
Shows Calculation of How Industrial MIG Welders Waste 8 TONS/YEAR of CO 2 (or Argon) Shielding Gas
See YouTube Video Discussion of
" Welding Race Cars " with Video Clips of
Richard Petty Discussing Importance of Welding
CLICK HERE OR PIC OF NASCAR CHASSIS
Calculate Weld Metal Volume for Any Weld Joint.
Also Calculate Amount of Rod or Wire Needed to Fill the Weld. Joint. Click Here or ICON.
New Info-"Friction Stir Welding"
Improve MIG Weld Starts and Have Shielding Gas Cylinder Last 2 to 3 Times Longer! Click Here.
Ideal for Welding Schools CLICK FOR DETAILS
A small shop fabricator in Georgia with a Miller TM 175 amp welder purchased a 50 foot Gas Saver System so he could use a larger cylinder and mount it on the wall of his shop. He wrote:
"The system works great. Thanks for the professional
service and a great product." CHECK OUT HIS SHOP
Purchase Training
Purchase Wire Feeding Aids
Purchase Replaceable Orifice Flow Control System
Save over $1000 per year per welder and improve weld starts with Payback measured in weeks!! * US Patent # 6,610,957; "Welding Shielding Gas Saver Device" August 26, 2003; Canadian Patent # 2,455,644.
The "Flow Rate Limiter" device is covered by 2008 US patent # 7,462,709. Other site material may be covered under Patents # 7,015,412 ; # 7,019,248 or # 8,104,094
Questions send e-mail [email protected] o r see contact us.
Copyright 1999-2017 WA Technology TM ; GSS TM ; All rights reserved.

What is Wire Feed Speed in Welding? Common wire feed speed errors to avoid
In the world of welding, there are several important factors to consider, and one of them is wire feed speed. If you’re new to welding, you may be wondering what exactly wire feed speed is, and how it affects the quality of your welds. Simply put, wire feed speed refers to the rate at which the welding wire is fed into the welding arc. It plays a significant role in determining the heat input and penetration of the weld.

Image by everlastgenerators
Wire feed speed is a crucial parameter in the welding process, as it directly affects the quality and strength of the weld. The wire feed speed is typically measured in inches per minute (IPM) or meters per minute (MPM), and it determines how quickly the electrode wire is consumed during welding.
When the wire feed speed is too high, the welding wire can create excessive spatter, which is the small molten metal droplets that are ejected during the welding process. This can result in poor fusion and a weaker weld. On the other hand, if the wire feed speed is too low, the weld may lack penetration, leading to a weak joint.
Achieving the right wire feed speed is essential for producing quality welds. It requires finding the perfect balance between the wire feed speed, welding current, and voltage settings to ensure optimal heat input and penetration.
Importance of wire feed speed in welding
Wire feed speed plays a crucial role in the welding process, as it directly affects the quality and strength of the weld. When the wire feed speed is set correctly, it ensures proper fusion between the base metal and the welding wire, resulting in a strong bond. Additionally, the wire feed speed determines the size and shape of the weld bead, which can impact the overall appearance of the weld.
A proper wire feed speed setting also helps control the heat input, which is crucial for preventing distortion, warping, and excessive heat-affected zones. By adjusting the wire feed speed, welders can achieve the desired penetration depth and control the amount of filler material deposited.
Furthermore, wire feed speed affects the efficiency and productivity of the welding process. By finding the optimal wire feed speed, welders can minimize downtime spent on rework, reduce material waste, and increase overall productivity.
Factors that affect wire feed speed
Several factors can influence the ideal wire feed speed for a specific welding application. Understanding these factors is crucial for achieving the best results in your welding projects.
Welding process: Different welding processes, such as MIG (Metal Inert Gas) welding, TIG (Tungsten Inert Gas) welding, and Flux-Cored Arc Welding (FCAW), have different wire feed speed requirements. It’s important to consider the specific welding process being used to determine the appropriate wire feed speed.
Material type and thickness: The type and thickness of the base metal being welded also affect the wire feed speed. Thicker materials typically require a higher wire feed speed to ensure proper penetration, while thinner materials may require a slower wire feed speed to prevent burn-through.
Electrode diameter: The diameter of the welding wire electrode can impact the wire feed speed. Thicker electrodes may require a higher feed speed, while thinner electrodes may require a lower feed speed.
Welding position: The position in which the weld is being performed can also influence the wire feed speed. Welding in a vertical or overhead position may require a slower wire feed speed to prevent excessive spatter and ensure proper fusion.
Welding current and voltage: The welding current and voltage settings are closely related to the wire feed speed. Adjusting these parameters can help fine-tune the wire feed speed to achieve the desired weld quality.
By considering these factors, welders can determine the appropriate wire feed speed for their specific welding application.
Determining the appropriate wire feed speed for different welding processes
Each welding process has its own recommended wire feed speed range, which serves as a starting point for finding the optimal setting. Here are the general guidelines for determining the appropriate wire feed speed for different welding processes:
MIG welding: For MIG welding, start with a wire feed speed of around 250-300 IPM (inches per minute) and adjust as needed based on the specific welding application. Thicker materials may require a higher wire feed speed, while thinner materials may require a lower feed speed.
TIG welding: TIG welding typically requires a lower wire feed speed compared to MIG welding. Start with a wire feed speed of around 50-100 IPM and make adjustments based on the material thickness and desired weld penetration.
Flux-Cored Arc Welding (FCAW): FCAW utilizes a tubular wire filled with flux, which affects the wire feed speed requirements. Start with a wire feed speed of around 150-200 IPM and adjust accordingly based on the specific welding application.
Remember that these are general guidelines, and it’s important to consult the welding equipment manufacturer’s recommendations and conduct test welds to fine-tune the wire feed speed for optimal results.
Tips for adjusting wire feed speed
Finding the correct wire feed speed can be a trial-and-error process, but here are some tips to help you make the necessary adjustments:
Start with the manufacturer’s recommendations: Consult the welding machine’s manual or the wire manufacturer’s guidelines to determine the recommended wire feed speed range for your specific welding application.
Conduct test welds: Perform test welds on scrap materials to evaluate the weld quality and make adjustments to the wire feed speed as necessary. Pay attention to the appearance of the weld bead, penetration depth, and overall fusion.
Observe spatter: Excessive spatter is often an indicator of a wire feed speed that is too high. If you notice excessive spatter, try reducing the wire feed speed gradually until the spatter is minimized while maintaining good fusion.
Evaluate penetration: Insufficient penetration may indicate a wire feed speed that is too low. If the weld lacks penetration, increase the wire feed speed gradually until the desired penetration is achieved.
Consider travel speed: The travel speed of the welding torch can also impact the wire feed speed. A slower travel speed may require a lower wire feed speed, while a faster travel speed may require a higher wire feed speed.
By following these tips and closely monitoring the weld quality, you can make the necessary adjustments to find the optimal wire feed speed for your welding projects.
Common wire feed speed errors to avoid
While adjusting the wire feed speed, it’s important to be aware of common errors that can negatively impact the weld quality. Here are some mistakes to avoid:
Inconsistent wire feed speed: Maintaining a consistent wire feed speed throughout the welding process is crucial for achieving uniform welds. Inconsistent wire feed speed can result in an uneven weld bead and poor fusion.
Over-reliance on default settings: While manufacturers provide recommended wire feed speed ranges, it’s important to remember that these are starting points. Different welding applications may require adjustments to the default settings to achieve optimal results.
Neglecting other welding parameters: Wire feed speed is just one of the parameters that affect the quality of the weld. Neglecting other parameters, such as welding current, voltage, and shielding gas flow rate, can result in subpar welds.
Ignoring the sound of the arc: The sound of the welding arc can provide valuable feedback on the quality of the weld. A steady, crackling sound indicates good fusion and indicates that the wire feed speed is set correctly.
By avoiding these common errors, you can improve the quality and consistency of your welds.
Tools and equipment to measure wire feed speed
Accurately measuring the wire feed speed is essential for fine-tuning your welding process. Here are some tools and equipment commonly used to measure wire feed speed:
Wire feed speed meters: These devices are specifically designed to measure the wire feed speed. They can be attached to the welding torch or wire feeder to provide real-time wire feed speed readings.
Marking the welding wire: Marking the welding wire at a specific point and measuring the time it takes for the marked point to pass through the wire feeder can provide an estimation of the wire feed speed.
Counting revolutions: Counting the number of revolutions the wire feeder motor makes in a given time period can provide an approximate wire feed speed measurement.
It’s important to consult the welding equipment manufacturer’s recommendations and guidelines for accurate wire feed speed measurement.
Troubleshooting wire feed speed issues
Sometimes, welders may encounter issues with the wire feed speed that can affect the weld quality. Here are some common wire feed speed issues and possible solutions:
Excessive spatter: Excessive spatter can be caused by a wire feed speed that is too high. Try reducing the wire feed speed gradually until the spatter is minimized while maintaining good fusion.
Lack of fusion and penetration: If the weld lacks fusion and penetration, the wire feed speed may be too low. Increase the wire feed speed gradually until the desired fusion and penetration are achieved.
Inconsistent weld bead: Inconsistent wire feed speed can result in an uneven weld bead. Ensure that the wire feed speed remains consistent throughout the welding process.
Wire feed motor issues: If the wire feed motor is not functioning properly, it can affect the wire feed speed. Regular maintenance and inspection of the wire feed motor can help prevent issues.
If troubleshooting the wire feed speed issues becomes challenging, it’s recommended to consult a welding professional or seek assistance from the welding equipment manufacturer.
Conclusion: the role of wire feed speed in achieving quality welds
Wire feed speed is a critical parameter in the welding process that directly impacts the quality, strength, and appearance of the weld. Finding the right wire feed speed requires considering various factors such as welding process, material type and thickness, electrode diameter, welding position, and welding current and voltage settings.
By understanding the importance of wire feed speed and making the necessary adjustments, welders can achieve strong, consistent welds with optimal penetration and fusion. Remember to conduct test welds, observe spatter and penetration, and make gradual adjustments to find the perfect wire feed speed for your specific welding application.
Accurate measurement of wire feed speed using specialized tools and equipment, along with troubleshooting common wire feed speed issues, will further enhance the welding process and ensure quality welds.
So, whether you’re a beginner looking to learn more about welding or an experienced welder looking to fine-tune your skills, mastering wire feed speed is essential for successful welding projects.
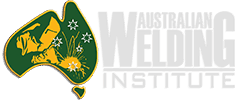
Travel Speed Calculator
Heat input calculator.
To use the Travel Speed calculator, insert the the time taken to complete the weld and the weld length into boxes of formula 1
Next, input your recorded welding Amps and Volts into formula 2 and it will calculate the Heat Input
- 1.TRAVEL SPEED CALCULATOR [Input the time taken & the length of weld]
- Weld time * sec
- Weld length * mm
- Calculated Travel Speed mm/min
- 2.HEAT INPUT CALCULATOR [Input Amps, Volts]
- KiloJoules kJ/mm
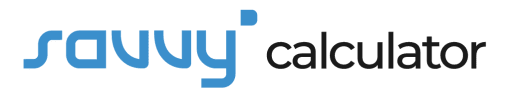
Inches Per Minute Calculator
Introduction.
In various fields such as machining, woodworking, and 3D printing, knowing the rate at which an object moves in inches per minute (IPM) is crucial for precision and efficiency. Whether you’re cutting materials, carving intricate designs, or extruding filament, the Inches Per Minute Calculator is a handy tool that simplifies the process of determining the speed at which your equipment should operate.
The Inches Per Minute Calculator employs a straightforward formula to calculate speed:
Speed (IPM) = Distance (inches) / Time (minutes)
This formula allows you to convert the distance your equipment or tool moves into inches per minute, providing you with valuable information for optimizing your work processes.
How to Use?
Using the Inches Per Minute Calculator is a breeze:
- Input Information: Gather the necessary data, including the distance the object will travel (in inches) and the time it takes (in minutes) to complete the journey.
- Enter Values: Input the distance and time values into the calculator.
- Calculate: The calculator will instantly provide you with the speed in inches per minute.
- Apply the Result: Use the calculated IPM value to configure your equipment or tool at the appropriate speed for your specific task.
Suppose you are working with a CNC machine, and your cutting tool is moving a distance of 12 inches in 0.5 minutes. Using the Inches Per Minute Calculator:
Speed (IPM) = 12 inches / 0.5 minutes = 24 IPM
In this scenario, you would set your CNC machine to operate at a speed of 24 inches per minute to ensure precise and efficient cutting.
- Why is knowing IPM important? Understanding IPM is essential for achieving accuracy and efficiency in various industrial and crafting processes, as it allows you to control the speed of your equipment or tools effectively.
- What are some common applications for the Inches Per Minute Calculator? This calculator is used in a wide range of industries, including manufacturing, woodworking, metalworking, 3D printing, and more, where precise control of speed is critical.
- Can I use this calculator for metric units as well? While this calculator focuses on inches and minutes, you can easily convert metric units (e.g., millimeters per second) by converting your measurements before using the calculator.
- Are there any safety considerations when using this calculator? Always prioritize safety when adjusting equipment speeds. Consult equipment manuals and safety guidelines to ensure that you operate machinery within safe parameters.
Conclusion:
The Inches Per Minute Calculator is a valuable tool that simplifies the process of determining speed in various industries and applications. Whether you’re managing large-scale manufacturing operations or pursuing intricate crafting projects, having a precise understanding of speed in inches per minute is essential. By utilizing this calculator, you can optimize your processes, enhance precision, and ultimately achieve superior results in your work. Don’t let speed become a stumbling block—let the Inches Per Minute Calculator be your guide to success in your projects, big and small.
Leave a Comment Cancel reply
Save my name, email, and website in this browser for the next time I comment.
- Privacy Policy
- Terms and Conditions
- Disclosure And Amazon Disclaimer
- Affiliate Disclosure
Welding of Welders All about welding, its types, equipment and safety rules
Estimating weld cost, how to determine weld size, strategies for creating a highly productive welding workplace, 6g welding position.
- Pulse TIG Welding
- Excessive Weld Reinforcement
- Welding Cracks and How to Prevent Them
- Hobart Handler 210 MVP MIG Welder Review
- YesWelder MIG-250A PRO 220V Spool Gun Aluminum MIG Welder
- Can you Weld Rusty Metal?
Welding Speed and Travel Angle
admin February 29, 2024 Basics Leave a comment 611 Views
- Stumbleupon
Table of Contents
Introduction
Welding, the process of joining materials, plays a vital role in various industries such as construction, automotive, and aerospace. Within the realm of welding, two crucial factors significantly impact the quality and integrity of welds: welding speed and travel angle.
Explanation of Welding Speed and Travel Angle
Welding speed refers to the rate at which the welding torch or electrode travels along the joint being welded. It is typically measured in inches per minute (IPM) or centimeters per minute (CPM), and it directly influences the heat input and the formation of the weld bead.
Travel angle, on the other hand, refers to the angle formed between the electrode or welding torch and the workpiece’s surface. It determines the direction and distribution of heat during the welding process, affecting penetration and weld bead shape.

Importance of Managing Welding Speed and Travel Angle in Welding Processes
Managing welding speed and travel angle is paramount in achieving high-quality welds and ensuring the structural integrity of the welded components.
Quality Assurance: Proper management of welding speed and travel angle ensures consistent weld quality by controlling factors such as penetration depth, fusion, and bead appearance. This is crucial for meeting industry standards and specifications, reducing the likelihood of weld defects, and ensuring the structural integrity of the welded joints.
Productivity Enhancement: Effective management of welding speed can enhance productivity by optimizing the time required to complete welds while maintaining quality standards. It enables welders to work efficiently without compromising on weld integrity, thereby increasing overall throughput and reducing production costs.
Welder Safety: Maintaining appropriate welding speed and travel angle reduces the risk of overheating the workpiece, minimizing the potential for material distortion and weld defects. This not only improves weld quality but also enhances welder safety by reducing exposure to hazardous conditions and minimizing the need for rework or repair.
Cost Reduction: By managing welding speed and travel angle effectively, welders can minimize material waste, rework, and downtime associated with weld defects. This results in cost savings for businesses, as they can allocate resources more efficiently and avoid additional expenses related to scrap materials or post-weld repairs.
Understanding Welding Speed
Definition of welding speed.
Welding speed, a critical parameter in welding processes, refers to the rate at which the welding torch, electrode, or welding head moves along the joint being welded. It is typically measured in inches per minute (IPM) or centimeters per minute (CPM) and directly affects the heat input and the formation of the weld bead.
Factors Influencing Welding Speed
- Material Type and Thickness: The type and thickness of the materials being welded significantly influence welding speed. Thicker materials generally require slower welding speeds to ensure proper fusion and penetration, while thinner materials may permit higher welding speeds. Additionally, different materials have varying thermal conductivity and melting points, which can affect the optimal welding speed.
- Welding Process: Different welding processes, such as Shielded Metal Arc Welding (SMAW), Gas Metal Arc Welding (GMAW/MIG), Gas Tungsten Arc Welding (GTAW/TIG), and Flux-Cored Arc Welding (FCAW), have distinct characteristics and optimal welding speeds. Each process may require specific parameters to achieve the desired weld quality and efficiency.
- Welding Position: Welding position, whether it’s flat, horizontal, vertical, or overhead, affects the welding speed. Welding in positions other than the flat position may require adjustments to the welding speed to maintain proper penetration and weld bead shape.
- Joint Design: The design of the joint, including its geometry and accessibility, influences welding speed. Complex joint configurations or hard-to-reach areas may necessitate slower welding speeds to ensure adequate fusion and penetration. Proper joint preparation and fit-up are crucial for optimizing welding speed.
- Skill Level of the Welder: The skill and experience of the welder play a significant role in determining the appropriate welding speed. Experienced welders can often work at higher speeds while maintaining quality, whereas less experienced welders may need to proceed more cautiously to avoid weld defects.
Effects of Improper Welding Speed
- Incomplete Fusion: Insufficient welding speed can result in incomplete fusion between the base metals and the filler material, leading to weak or defective welds. Incomplete fusion compromises the structural integrity of the weld joint, increasing the risk of failure under load or stress.
- Excessive Spatter: High welding speeds combined with improper parameters can lead to excessive spatter, which is the ejection of molten metal droplets during welding. Spatter not only affects the appearance of the weld but also indicates poor weld quality and can cause contamination of the workpiece and surrounding area.
- Distortion of the Workpiece: Improper welding speed, particularly when welding thicker materials, can result in excessive heat input and thermal distortion of the workpiece. This distortion may lead to dimensional inaccuracies, warping, or misalignment of components, affecting the overall fit and function of the welded assembly.
Importance of Travel Angle
Definition of travel angle.
The travel angle in welding refers to the angle formed between the electrode or welding torch and the workpiece’s surface during the welding process. It determines the direction and distribution of heat applied to the weld pool, influencing penetration depth, weld bead shape, and overall weld quality.
Role of Travel Angle in Welding
The travel angle plays a crucial role in controlling the welding process and achieving desired weld characteristics:
- Penetration Control: The travel angle affects the depth of penetration into the base metal. By adjusting the travel angle, welders can control the amount of heat directed into the joint, thereby regulating penetration depth.
- Weld Bead Shape: Proper manipulation of the travel angle helps in shaping the weld bead. It allows welders to achieve a desired bead profile, ensuring uniformity and strength throughout the weld.
- Heat Distribution: The travel angle influences the distribution of heat across the weld pool. By maintaining the appropriate travel angle, welders can ensure even heat distribution, minimizing the risk of defects such as lack of fusion or excessive heat-affected zones.
Optimal Travel Angles for Different Welding Processes
- SMAW typically requires a slightly forward travel angle, ranging from 5 to 15 degrees in the direction of welding. This angle promotes adequate penetration and helps control the shape of the weld bead.
- For GMAW or MIG welding, a slightly backward travel angle of around 5 to 15 degrees is commonly recommended. This angle allows for better gas coverage and shielding of the weld pool, resulting in improved weld quality.
- In GTAW or TIG welding, maintaining a perpendicular travel angle (0 degrees) or a slightly forward angle is often preferred. This positioning ensures precise control over the heat input and weld pool, leading to high-quality, defect-free welds.
- FCAW typically requires a forward travel angle similar to SMAW, ranging from 5 to 15 degrees. This angle helps in achieving proper penetration and controlling the shape of the weld bead, especially when using flux-cored electrodes.
Effects of Incorrect Travel Angle
- Inadequate Penetration: Incorrect travel angles can result in insufficient penetration into the base metal, leading to weak welds with reduced mechanical strength and integrity. This can compromise the structural performance of the welded joint, increasing the risk of failure under load or stress.
- Excessive Heat Input: Improper travel angles may cause excessive heat input into the weld zone, resulting in overheating, distortion, or even burn-through of the base metal. This can lead to weld defects such as excessive spatter, porosity, and metallurgical changes, negatively impacting weld quality and performance.
- Weld Defects like Undercutting: Incorrect travel angles can contribute to weld defects such as undercutting, where the weld metal fails to adequately fill the groove or joint, leaving a depression along the weld toe. Undercutting weakens the weld joint and increases susceptibility to cracking and failure.
Techniques for Managing Welding Speed and Travel Angle
Proper training and skill development.
Proper training and skill development are fundamental for welders to effectively manage welding speed and travel angle. Training programs should cover theoretical knowledge and practical skills related to welding processes, including understanding the influence of speed and angle on weld quality, as well as techniques for adjusting them according to specific welding tasks.
Utilization of Welding Procedure Specifications (WPS)
Welding Procedure Specifications (WPS) provide guidelines for welders regarding the parameters, techniques, and procedures required to produce acceptable welds. By adhering to WPS, welders can ensure consistency in welding speed and travel angle settings, leading to predictable and reliable weld quality.
Monitoring and Adjusting Welding Parameters
Continuous monitoring and adjustment of welding parameters during the welding process are essential for maintaining optimal welding speed and travel angle. Welders should regularly assess factors such as arc voltage, wire feed rate, travel speed, and torch angle, making adjustments as needed to achieve the desired weld characteristics.
Pre-welding Preparation and Planning
Thorough pre-welding preparation and planning contribute to effective management of welding speed and travel angle. This includes proper joint preparation, fit-up, and cleaning to ensure optimal welding conditions. Additionally, planning the sequence of welding operations and considering factors such as material type, thickness, and joint geometry help in determining the appropriate speed and angle settings for each weld.
Use of Welding Aids and Accessories
- Jigs and Fixtures: Jigs and fixtures provide support and alignment for the workpieces, ensuring consistency in joint configuration and positioning. By using appropriate jigs and fixtures, welders can maintain consistent welding speed and travel angle, resulting in uniform weld quality across multiple welds.
- Positioners: Welding positioners allow for rotation or manipulation of the workpiece during welding, enabling welders to access different welding positions and angles with ease. By using positioners, welders can optimize their body position and torch angle, enhancing control over welding speed and travel angle.
- Travel Speed Guides: Travel speed guides, such as wheel or track systems, help welders maintain a consistent travel speed along the joint. By following the guidance provided by these devices, welders can ensure uniformity in welding speed and minimize deviations that could affect weld quality.
Real-time Feedback and Adjustment During Welding Process
Real-time feedback mechanisms, such as visual inspection, weld monitoring systems, and welding process monitoring software, enable welders to assess weld quality and performance during the welding process. By monitoring weld appearance, penetration, and other parameters, welders can make immediate adjustments to welding speed and travel angle to correct any deviations and maintain weld integrity.
Case Studies and Examples
Demonstrations of correct welding speed and travel angle settings.
In this section, we will present real-life demonstrations showcasing correct welding speed and travel angle settings across different welding processes and joint configurations. These demonstrations will highlight the importance of precise parameter control in achieving high-quality welds.
Analysis of Common Mistakes and Their Consequences
We will examine common mistakes related to welding speed and travel angle settings, such as excessive speed, incorrect torch angles, and inconsistent travel speeds. Through visual examples and analysis, we will discuss the detrimental effects of these mistakes on weld quality, including inadequate penetration, incomplete fusion, and distortion.
Comparison of Welds with Proper and Improper Speed/Angle Management
By comparing welds produced with proper speed and angle management to those with improper settings, we will illustrate the significant differences in weld quality and performance. This comparison will emphasize the importance of meticulous parameter control in achieving welds that meet industry standards and specifications.
How does welding speed affect the quality of welds?
Welding speed influences the heat input and cooling rate, which can affect the microstructure and mechanical properties of the weld. Too high a speed may result in insufficient fusion, while too low a speed can cause excessive heat input and distortion.
What is the ideal travel angle for different welding processes?
The ideal travel angle varies depending on factors such as the welding process, material thickness, and joint configuration. Generally, a travel angle of around 5 to 15 degrees from perpendicular to the workpiece surface is recommended for most welding processes.
Can improper speed and angle lead to defects in the weld?
Yes, improper welding speed and travel angle can result in various defects, including lack of fusion, undercutting, and incomplete penetration. It’s crucial to control these parameters carefully to ensure proper weld quality.
How can beginners improve their control over welding speed and travel angle?
Beginners can improve their control over welding speed and travel angle through regular practice, experimentation, and seeking guidance from experienced welders. Starting with simple projects and gradually increasing complexity can help develop proficiency.
What are the most common safety hazards associated with welding?
The most common safety hazards associated with welding include exposure to fumes and gases, UV radiation, electrical shock, and fire hazards. It’s essential to follow proper safety protocols and wear appropriate protective gear to mitigate these risks.
In conclusion, effective management of welding speed and travel angle is essential for achieving high-quality welds and ensuring the reliability of welded structures. By emphasizing training, adherence to procedures, and continuous improvement, welders and welding supervisors can optimize their welding processes and adapt to emerging trends and technologies in the field.
Tags Advanced Welding Technologies Data Analytics in Welding Digitalization in Welding Future Trends in Welding Robotics in welding Travel Angle Weld quality welding automation welding efficiency welding optimization welding parameters Welding Procedure Specifications Welding Processes Welding Skill Development Welding speed Welding standards Welding Supervision welding techniques welding training
About admin
Related Articles

6 hours ago

17 hours ago

Mastering the 6G Welding Position: Challenges, Techniques, and Advantages Welding is a critical skill in …
Leave a Reply Cancel reply
Your email address will not be published. Required fields are marked *
Save my name, email, and website in this browser for the next time I comment.

- Shop All Welding Machines
- TIG Welders
- MIG Welders
- Plasma Cutters
- Multi-Process Welders
- Shop All Welding Gas
- 100% Argon Tank
- 75% Argon 25% CO2 Tank
- Shop All Welding Accessories
- Foot Pedals
- Guides & Regulators
- Machine Covers
- Torches & Guns
- Protective Gear
- MIG Welding
- TIG Welding
- Plasma Cutting
- Multi-Process Welding
- Welding Coupons
- Shop All Consumables
- CUT60 Ipt60 & Ipt40
- Cut50d & Ct520d SG-55
- Cut50dp & Ct520dp AG-60
- Tungsten Electrodes
- Collet Body 17/18/26 or 9/20
- Kits, Cups, Electrodes, Gas Lens, Collets
- Fixture Table
Understanding Voltage & Amperage in Welding
Gas metal arc welding (GMAW) is a welding process that happens when an electrical arc is established between a base material and a continuously fed wire electrode. The molten weld pool is protected from the atmosphere by a shielding gas that flows around the wire filler metal in the weld pool and the weld pool itself. The heat from the electrical arc melts the base metal and the wire filler metal being fed into the weld pool.
While many variables can influence a weld's quality, including the type and thickness of the base material, the four primary factors affecting it are welding current, welding voltage, contact-to-work distance, and travel speed.
Of all the welding factors, voltage and amperage cause the most confusion, especially in the novice welder. And since they are considered among the primary aspects that impact a GMAW weld, we will take a more detailed look at them.
What is amperage in welding?
The welding current is the variable that mainly controls the amount of weld metal deposited during the welding process. Amperage measures the strength of the electrical current, with its primary effect on welding being the melt-off rate of the electrode and the depth of penetration into the base material.
Wire feed speed (WFS), another of the welding variables, controls amperage and the amount of weld penetration. WFS and current are directly related: as one increases, so does the other and vice versa. If the WFS is set too high, it can lead to burn-through. That's because as the welding current increases, the weld penetrates deeper into the base material.
Take a look at Table 1: Welding Current Data to see how this works in practice. As you can see, the WFS was incrementally increased from Weld 1 through Weld 5, which, in turn, increased the welding current. Keep in mind that the welding operator sets the WFS--not the current level--on a GMAW-CV power supply. The primary way of adjusting the current is by changing the WFS.
You can see from the table that as the wire feed speed increased, so did the amperage. The results are evident in Figure 1: Cross-Sectional View of Welds 1 through 5.
Table 1 shows the welding data from the following welds

Figure 1: Cross-Sectional View of Welds 1-5 (Table and Image Courtesy of EWI.org )
Notice the increase in weld penetration from Weld 1 to Weld 5. With the voltage and travel speed variables held constant, the increase in WFS and current indicates a substantially deeper weld moving from the 1st to the 5th. Also, note the fingerlike penetration in Welds 3-5 caused by the metal transfer mode in the welding arc changing to "spray metal" transfer mode. The metal transfer mode typically transitions from globular to spray mode transfer above 190 amps of welding current for specific metal and shielding gas combinations.
What is welding voltage?
If amperage measures the volume of electrons flowing through an electrical current, voltage measures the pressure that allows them to flow. In other words, it's the carrying force of the electrical current. So, what effect does this electrical "pressure" (voltage) have on the weld? Welding voltage controls the arc length: the distance between the weld pool and the wire filler metal at the point of melting within the arc. As the voltage increases, the weld bead will flatten out, and its width-to-depth ratio will increase. Check out the weld data in Table 2:
Table 2 shows the welding voltage data from the following welds

Figure 2: Cross-Sectional View of Welds 7-11 (Table and Image Courtesy of EWI.org )
While the travel speed, wire feed speed, and amperage remained constant, the voltage varied. Clearly, the voltage has little impact on penetration. You can see the effects of voltage on the weld's surface, helping it lay flat and wash in at the edges. Too much voltage can produce a weld that is flat, concave or undercut. Too little voltage could yield a shoddy weld bead, or it can contribute to a lack of fusion.
Figure 2 shows this widening of the weld beads from 7 to 11 as the voltage is increased. You can see the penetration remained constant for Welds 7-9 since the current was unchanged. Welds 10 and 11 showed the same increase in fingerlike penetrations as in Welds 3-5, as well as an increase in welding current. As the arc length increases in proportion to the rise in voltage, the electrode extension, the distance from the contact tip to the point where the welding wire is melting in the arc, consequently decreases.
Welding amps per thickness of common types of metal
Anyone wishing to achieve optimal welding results should know how to set the proper amps according to the type and thickness of each metal. Refer to the chart below for welding amps per thickness for carbon steel and stainless steel.
Carbon Steel With 75 Percent Argon/25 Percent CO2 Shielding Gas
Stainless steel with 90 percent helium/7.5 percent argon/2.5 percent co2.
Remember the rule of thumb: Material thickness determines amperage, and each .001 inch of material thickness requires approximately 1 amp of output. (1/4" thickness, or .25" = 250 amps)
Do you have questions on amperage and voltage?
Talk to the experts at PrimeWeld. Our technical specialists and support representatives have the answers. When you contact us , you will be talking to a real professional welder. They have many years of hands-on experience with our products, and they are always available to help you come up with solutions for practically any welding project.
While you're at it, look over our impressive lineup of machines and accessories. Our welding machines are engineered to demanding standards of accuracy, convenience, and endurance. And we stand by what we sell!
Thanks for reading.
Leave a comment 0 comments, be the first.
Please note comments must be approved before they are published.
0 Items in your cart
Subtotal $0
Tax and shipping will be calculated at checkout.
Your shopping cart is empty.

GMAW Travel Speed & Deposition Rate Calculator
How to use this calculator.
The below GMAW / MIG welding calculator is designed to help welding professionals quickly and accurately estimate weld travel speeds and deposition rates. Simply select the desired fillet weld size, material type, welding wire diameter, transfer method, and wire feed speed being used. Once you click the calculate button, the required travel speed will be displayed in inches per minute. The deposition rate will also be displayed below the travel speed in lbs. per hour. The tool can be used to quickly setup automated or semi-automated GMAW / MIG welding equipment.
Inches Per Minute (IPM) Calculator
Online cutting speed calculator to calculate Inches Per Minute (IPM) from RPM, IPR values. IPM can be calculated by multiplying both RPM, IPR value.
Inches Per Minute Calculation
IPM = RPM * IPR
Related Calculators
Science calculators.

Powered by mwForum 2.29.2 © 1999-2013 Markus Wichitill
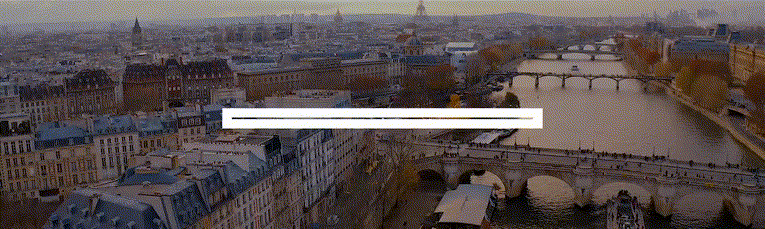
COMMENTS
By getting the deposition rate by using the calculation above, you can calculate the travel speed in inches per minute (IPM) for a particular weld. For example, let's say you want to make a 3/8-in. steel fillet weld (assume 10% reinforcement or 0.4125 in. leg) using .030-in. solid wire at 350 IPM, the weight of weld metal per foot can be ...
Weld travel speed, for manual GTAW, is generally measured in inches per minute (IPM) and can range from 4 to 6 IPM (100 to 150 mm/min). However, with similar configurations, it is possible to achieve much higher weld travel speeds of up to 25 to 35 IPM with a single-wire application. The wire feed speed is a key factor in welding that can ...
Travel Speed = 7.96 × 0.7 = 5.57 ipm (.2887) Weight of weld metal per foot can be calculated for any joint type by calculating the volume and multiplying by the density of the weld metal (eg. 0.283 lb/in 3 for steel). However, the values shown in Table 3 through Table 6 eliminate the need to do the calculation.
CHECK OUT MY WEBSITE AND BENEFIT FROM THE PRACTICE CWI EXAMS AND MORE!!!!! https://www.weldingandstuff.netOne Attempt Part A CWI Fundamentals 150 Random Prac...
Travel Speed. Travel speed simply refers to how fast the arc moves along the weld joint, measured in inches per minute (IPM). In semiautomatic operations, many welding operators feel comfortable with an average of 10 to 12 IPM, but more experienced operators may weld in the 18 to 20 IPM range.
3.5 x 125 = 437.5 ipm.030 inch. 2 inches per amp. 2 x 125 = 250 ipm.035 inch. 1.6 inches per amp. 1.6 x 125 = 200 ipm.045 inch. 1 inch per amp. 1 x 125 = 125 ipm. Examining the beads. ... Travel speed too slow: Traveling too slow introduces too much heat into the weld, resulting in an excessively wide weld bead and poor penetration. On thinner ...
In welding, travel speed refers to the rate at which the welding arc moves along the joint being welded. It is typically measured in inches per minute (IPM) or millimeters per minute (mm/min). In stick welding, the travel speed can significantly influence the shape and quality of the weld bead.
The formula for travel speed in welding can be determined by dividing the length traveled (l) by the time taken (t) to travel that length. In this case, with a length (l) of 150 mm and a time (t) of 68 s, the travel speed can be calculated as 150 mm / 68 s = ~2.2 mm/s or 132 mm/min. Therefore, the formula for travel speed in welding is l / t.
K [Amps 4 / (Weld Travel Speed; ipm x Volts 2)] 0.333. For 0.035 inch diameter solid carbon steel wire, the constant K = 0.0019. Using these equations we find the following when we change wire stickout for 0.035 inch solid wire. Assuming a fixed wire feed speed that produces 200 amps at 3/8 inch wire stickout:
Start with a wire feed speed of around 50-100 IPM and make adjustments based on the material thickness and desired weld penetration. Flux-Cored Arc Welding (FCAW): ... Consider travel speed: The travel speed of the welding torch can also impact the wire feed speed. A slower travel speed may require a lower wire feed speed, while a faster travel ...
Heat Input Calculator. To use the Travel Speed calculator, insert the the time taken to complete the weld and the weld length into boxes of formula 1. Next, input your recorded welding Amps and Volts into formula 2 and it will calculate the Heat Input. 1.TRAVEL SPEED CALCULATOR [Input the time taken & the length of weld]
Heat Input = V x A x 60 / TS Voltage times Amperage times 60 / Travel Speed (ipm) = heat input in joules per inch. Divide by 1000 to get kJ/in. Where travel speed equals: Length welded divided by the time taken to weld the joint, so: (Length welded/ (minutes times 60 plus seconds to weld the length welded)) = travel speed in inches per second. Now multiply by 60 to get travel speed in inches ...
Travel Speed, in/min Effect of Travel Speed on Weld Dimensions Bead Height Bead Width Depth of Fusion 41. Weld Study Constants ... • All the remaining welds were made at 32 volts. • All the remaining welds were made at 24 ipm travel speed. 42. Electrical stick-out (ESO) • If amperage is held constant: • Wire feed speed must increase as ESO
Apply the Result: Use the calculated IPM value to configure your equipment or tool at the appropriate speed for your specific task. Example: Suppose you are working with a CNC machine, and your cutting tool is moving a distance of 12 inches in 0.5 minutes. Using the Inches Per Minute Calculator: Speed (IPM) = 12 inches / 0.5 minutes = 24 IPM
SMAW typically requires a slightly forward travel angle, ranging from 5 to 15 degrees in the direction of welding. This angle promotes adequate penetration and helps control the shape of the weld bead. Gas Metal Arc Welding (GMAW/MIG): For GMAW or MIG welding, a slightly backward travel angle of around 5 to 15 degrees is commonly recommended.
The document discusses how to pre-calculate wire-feed speed, travel speed, and voltage for MIG welding to decrease development time for new welds. It provides formulas to calculate deposition rate based on wire diameter and wire-feed speed. Knowing the deposition rate allows calculating travel speed based on the desired weld size and number of passes. Tables of common weld sizes and their ...
With the voltage and travel speed variables held constant, the increase in WFS and current indicates a substantially deeper weld moving from the 1st to the 5th. Also, note the fingerlike penetration in Welds 3-5 caused by the metal transfer mode in the welding arc changing to "spray metal" transfer mode.
Once you click the calculate button, the required travel speed will be displayed in inches per minute. The deposition rate will also be displayed below the travel speed in lbs. per hour. The tool can be used to quickly setup automated or semi-automated GMAW / MIG welding equipment. Fillet Weld Size 3/16" 1/4" 5/16". Steel Stainless Aluminum.
Formula: IPM = RPM * IPR. where, RPM = Revolutions Per Minute. IPR = Inches Per Revolution. Online cutting speed calculator to calculate Inches Per Minute (IPM) from RPM, IPR values. IPM can be calculated by multiplying both RPM, IPR value.
Dear All , Please recommend about calculate travel speed of Heat in put Ex. V 28 A 150 Time 68 Second Length 150 mm.. A or B are Correct ... Heat Input (Joules per minute) = (Volts x Amps x 60) / Travel Speed (IPM) By Toey TNDT Date 06-22-2015 13:26 Edited 06-22-2015 13:30
Stainless Steel Travel Speed - IPM: 15 IPM Aluminum Travel Speed - IPM ... proper tip selection, the benefits of using a guide and how travel speed... How to Optimize Plasma Cutter Performance. Learn the best practices that will improve your plasma cutting skills, regardless of material or thickness. ...