Difference between Process shutdown and Emergency Shutdown
Table of Contents
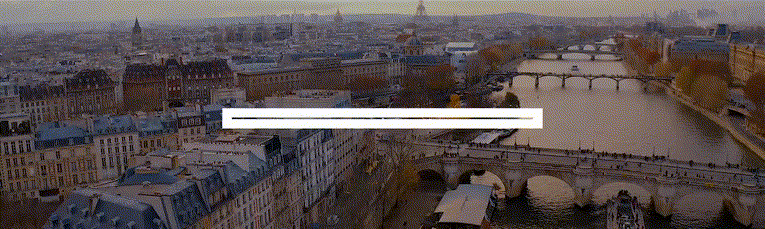
What is Process shutdown (PSD) ?
Process shutdown (PSD) is defined as the automatic isolation and the activation of all part of a process. During a PSD the process remain pressurized.
Basically PSD consist of field mounted sensors. Valves and trip relays, a system logic unit for processing of incoming signals, alarm and MHI units. The system is able to process all input signals and activating output in accordance with the applicable cause and effect matrix chart
Typical action from PSD systems are:
1. Shutdown the whole process 2. Shutdown part of the process 3. Depressurize/Blow down parts of the process
What is Emergency Shutdown (ESD) ?
The Emergency Shutdown (ESD) shall minimize the consequences of emergency situations, related to typically uncontrolled flooding, escape of hydrocarbons, or outbreak of fire in hydrocarbon carrying areas or areas which may otherwise be hazardous. Traditionally risk analyses have concluded that the ESD system is in need of a high Safety Integrity Level , typically SIL 2 or 3.
Basically the system consists of field-mounted sensors, valves and trip relays, system logic for processing of incoming signals, alarm and HMI units. The system is able to process input signals and activating outputs in accordance with the Cause & Effect charts defined for the installation.
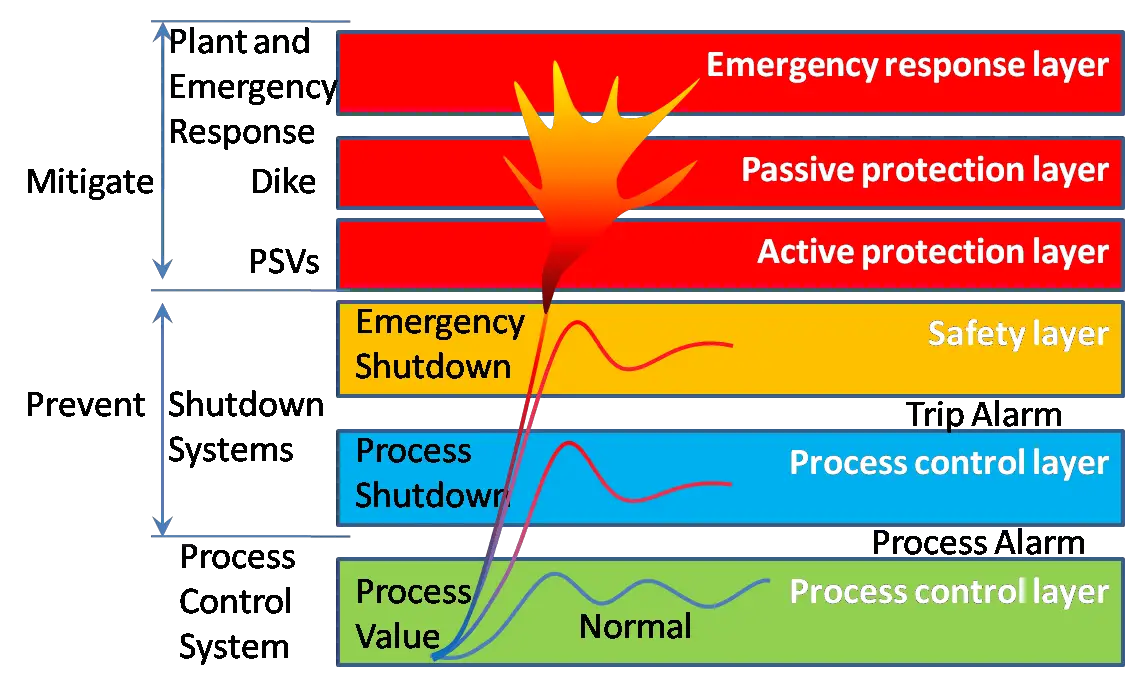
ESD can be automatically initiated by load shedding functions or manually by the operator through push button on the panel. ESD will shutdown and isolate all designated process related equipment, including inlet and outlet ESD valves. Depends on each project some plant will allow the power generation, utilities and fuel gas system keep running during this condition.
Typical action from ESD system are:
- Shutdown of part system and equipment
- Isolate hydrocarbon inventories
- Isolate electrical equipment
- Prevent escalation of event
- Stop hydrocarbon flow
- Depressurize/Blow down parts of the process
- Emergency ventilation control
- Close watertight doors and fire doors
Process shutdown (PSD) system is a part of plant (facility) safeguarding system with a purpose to minimize the frequency and consequences of excursions outside the facility operating envelope.
Emergency shutdown (ESD) system is a part of plant (facility) safeguarding system with a purpose to keep the process within the design envelope and to prevent the escalation of abnormal conditions into a major hazardous event.
PSD and ESD can be considered as effects, which are triggered by certain causes, the PSD and ESD are levels of shutdown which discriminate between the seriousness of the causes leading to the appropriate effects.
Articles You May Like :
What is Shutdown Valve ?
ESD Philosophy Guide
Compressor Emergency Shutdown
Shutdown Valve Advantages
Emergency Shutdown System
Share With Your Friends
Recommended articles.
Basics of Motion Controllers
What is a Recorder ?
Troubleshooting with Loop Calibrator
What is Indicator ?
Process Switches and Alarms
4-20mA Junction Box versus Fieldbus (FF) Junction Box
Instrumentation Engineer in Process Plant Project
Troubleshooting Pump Control Circuit
PLC vs PAC – Understanding the Key Differences and Similarities
Types of System Architecture used in Industrial Automation
5 thoughts on “Difference between Process shutdown and Emergency Shutdown”
Process shut down could be attributed to any planned shut down of the unit. It is an anticipated one and planned to attend the process issues during the favorable situation such as unit feed limited due to downstream unit issues, feed quality affects the unit throughput etc. Otherwise shut down time to be planned according to the severity of the issue.
Whereas emergency shutdown, as the terminology explains it is a forced situation on the process unit. One has to act according to the situation. Using the available resources, plan to go for safe shutdown of the unit as per the SOP of the unit.
Application of mind relating to the situation is the most important aspect as emergencies are always different and may be the type of emergency occurs also new. A very good knowledge about the process, plant and facilities available in the unit are the must to handle ESD safely.
As the name suggest, the process shutdown originates from the unwanted process conditions and emergency shutdown originates from emergency related issues.
Process shutdown will be initiated if the control system capture any process abnormalities as defined in the control system design. This system will try to stop propagating the impacts of process abnormalities downstream.
Emergency shutdown will be mostly initiated originating from abnormalities leading to serious safety concerns such as Runaway reactions leading to excessive temperature.
Nice Articles here thanks so much but can you make it printable please
Could anyone provide me with the regulation standard about ESD?
Thank you and Please share an article about relay based type of ESD?
Leave a Comment Cancel reply
More articles.
Modbus Function Command Formats
Single Loop Controller Questions
Cyber Security Multiple Choice Questions and Answers
Instrumentation Earthing
How Process Control Loop Works
Overview of PID Control terms
Explaining Various Types of Analog Instruments

What are the Emergency shutdown procedures?
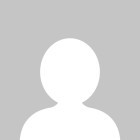
Introduction
• level 1: emergency shutdown and depressurisation of the overall plant, • level 2: emergency shutdown for a process unit within the plant, • level 3: process shutdown for a process unit within the plan, • level 4 process train shutdown within a unit, • level 5: shutdown of individual equipment and utilities, level 1 shutdown – emergency shutdown and depressurisation of the overa ll plant, level 2 shutdown – emergency shutdown for a process unit within the plant., level 3 shutdown – process shutdown for a process unit within the plant.
A Level 3 shutdown shall be initiated by major process or utility failure that may affect all trains within a unit. A Level 3 shutdown will shutdown common equipment for the unit in which the abnormal condition occurs and initiate audible and visual alarms at the CCR.
Level 4 Shutdown – Process Train Shutdown within a Unit
A Level 4 shutdown will shutdown the entire process train in which the abnormal condition is occurring and initiate audible and visual alarms at the CCR, where there is no expected potential for the abnormal condition to propagate to a parallel train
Typical examples include high-high levels in vessels, where carry-over of liquid can have adverse consequences on downstream equipment.
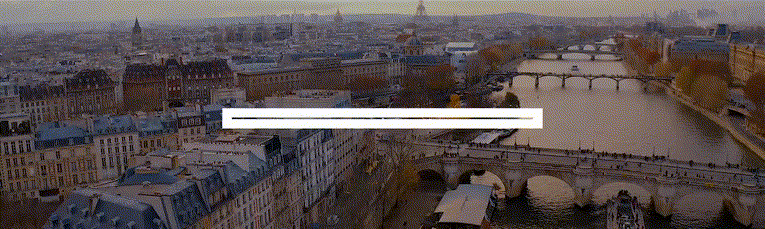
Level 5 Shutdown – Shutdown of Individual Equipment and Utilities
A Level 5 shutdown will shutdown the piece of equipment required to bring an abnormal situation under control and initiate audible and visual alarms at the CCR, where the situation has a low potential for escalation. A typical example isa ‘low-low’ level in a process vessel, which shuts an ESD valve in the vessel outlet line to prevent gas blow by to a lower rated vessel downstream.
Also read Continuous control mode- P, PD, PI & PID control modes
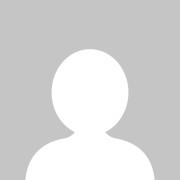
Tube fitting Installation procedure
Electrical safety in power distribution, related articles.
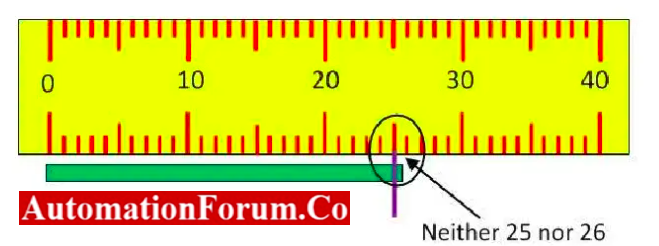
What are the most common Sources of measurement errors in Instrumentation and How can you minimize them?
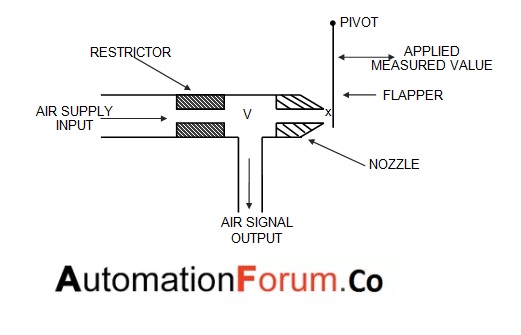
What is a flapper nozzle mechanism?
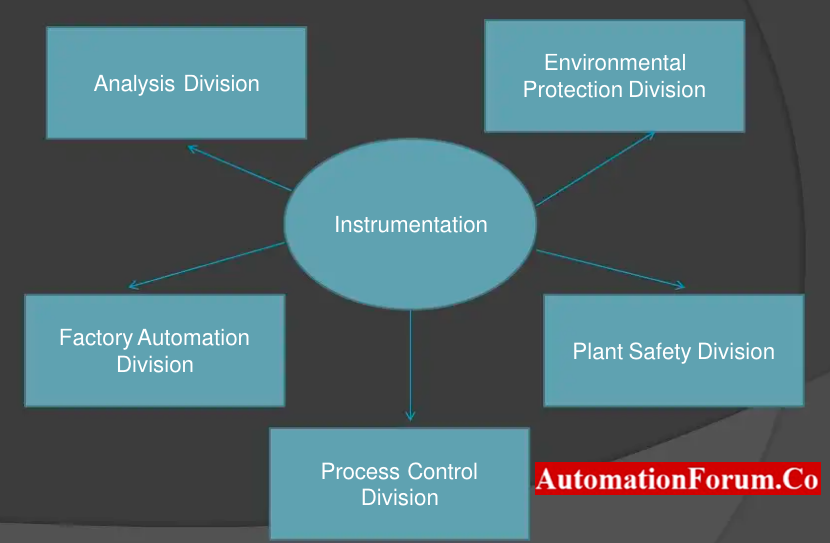
What is Instrumentation?
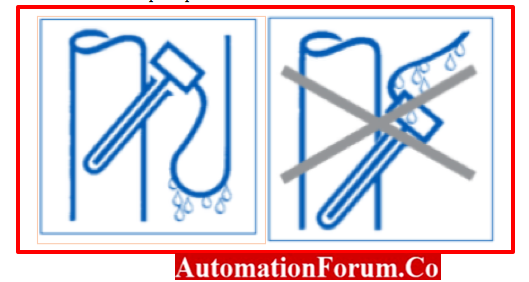
Importance of Sensor Selection and Placement in Instrumentation
Leave a reply cancel reply.
You must be logged in to post a comment.
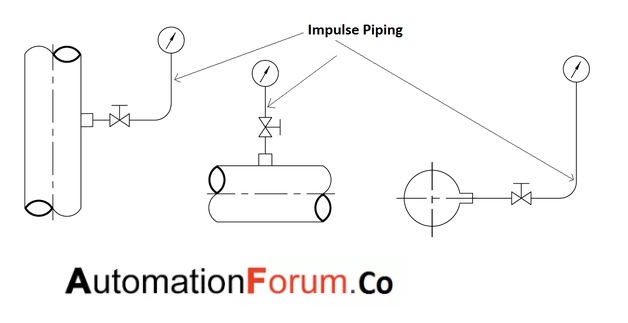
Adblock Detected
- Emerson.com
- About the Blog
Differences in Fire & Gas Systems and Emergency Shutdown Systems
by Jim Cahill | Feb 4, 2011 | Industry , Oil & Gas , Safety | 0 comments
Raphael, whom you may recall from an earlier marine and offshore safety post , is an SIS implementation manager for the European region.
Here’s Mike’s post:
At Emerson Exchange last year, Rafael Lachmann presented on the topic of Fire & Gas System (FGS) solutions with DeltaV SIS . In his presentation, he provided a basic overview of FGS concepts and then he described how DeltaV SIS could be used for FGS applications. He described how emergency shutdown (ESD) systems are different from FGS, how onshore FGS differs from offshore FGS applications, and how DeltaV SIS can be used for FGS applications. For an ESD, a process upset will result in a process shutdown. ESD systems are preventative layers of protection, meaning that they act to prevent a hazardous event like a chemical release, fire, or explosion from occurring. A FGS is a mitigating layer of protection, because the purpose is to reduce the consequence severity of such an event when it occurs. When a combustible gas, a toxic gas, smoke, flame, or heat is detected, then the FGS will respond by annunciating audible and visual alarms and initiate a water deluge, fire suppression system, or a process shutdown. In the event of a gas leak, the FGS can act to prevent it from becoming a fire or explosion by isolating the leak and ignition sources. In the Deepwater Horizon Accident Investigation Report that was issued by BP in September 2010, this was listed as one of the 8 barriers that were breached. The fire and gas system did not prevent hydrocarbon ignition. Hydrocarbons migrated beyond areas on Deepwater Horizon that were electrically classified to areas where the potential for ignition was higher. The heating, ventilation and air conditioning system probably transferred a gas-rich mixture into the engine rooms, causing at least one engine to overspeed, creating a potential source of ignition. A typical ESD safety instrumented function (SIF) is typically quite simple when compared to what is implemented for a FGS. A FGS SIF can be very complex and highly distributed, with 1ooN or 2ooN voting from a large number of detector devices located throughout a unit, process, and plant area. In some cases, a FGS event can initiate a site-wide emergency shutdown. Another important difference is that an ESD is typically designed as normally energized (de-energize-to-trip) so that it is fail-safe. This way, if there is loss of power or connectivity between system components then the SIS will respond by tripping. This results in higher safety integrity, but it can result in increased spurious trips of the process. For FGS, a spurious trip can have dangerous results. For example, initiating a water deluge system inside a building can cause damage to equipment and can be hazardous to personnel. Chemical fire suppression can be dangerous to personnel, and false alarms degrade the willingness to respond by plant personnel. For this reason, it is common to design a FGS as normally de-energized (NDE). In a NDE design, the loop must be energized in order to initiate a trip of the FGS. This means that failures such as loss of power or connectivity between components are covert failures unless there is adequate diagnostics to detect the failures. In a NDE design, line monitoring is essential to detect open and short circuit failures in wiring between logic solver I/O and field devices. The major differences between offshore and onshore FGS design result from the difficulty to evacuate and limited offsite emergency response assistance when an offshore incident occurs. Rafael’s discussion on how onshore FGS differs from offshore FGS will soon be covered in another blog post.
Popular Posts
Share this:, subscribe to podcast.
We invite you to follow us on Facebook, LinkedIn, Twitter and YouTube to stay up to date on the latest news, events and innovations that will help you face and solve your toughest challenges.
Do you want to reuse or translate content?
Just post a link to the entry and send us a quick note so we can share your work. Thank you very much.
Our Global Community
Emerson Exchange 365
The opinions expressed here are the personal opinions of the authors. Content published here is not read or approved by Emerson before it is posted and does not necessarily represent the views and opinions of Emerson.
Privacy Policy | Cookie Policy | Data Protection Statement
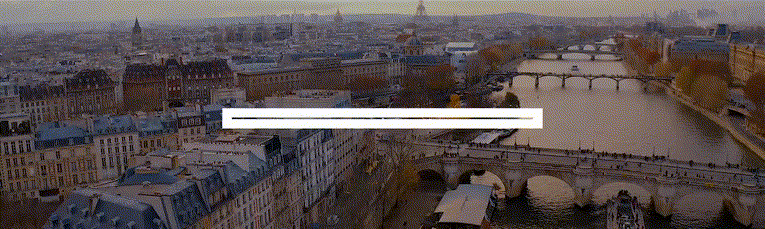
IMAGES
VIDEO
COMMENTS
Table of Contents. Trip: The term Trip refers to an action that is initiated by the control system and which forces a device or devices to a pre-determined state. Example of Trip Signals: Close Valve, Open Valve, Stop motor, etc.
An alarm trip accepts an input signal from a monitoring or control instrument, such as a signal transmitter or sensor. When the monitored variable falls outside of a user-set “Trip” (also called “Set”) Point, the alarm trip activates one or more of its relay outputs.
#1. What is the difference between trip and shutdown in Mark VI. There are few interlocks in gas turbines which will generate a normal shutdown of the unit and will not generate a trip command. These interlocks are. 1. Turbine wheel space temperature. 2. Seismic vibration. 3. Turbine inlet air filter differential pressure. 4.
Here's a summary of each concept: Trip: A trip is an action initiated by the control system that forces a device or devices to a predetermined state. Trips are often related to safety...
PSD vs ESD. Process shutdown (PSD) system is a part of plant (facility) safeguarding system with a purpose to minimize the frequency and consequences of excursions outside the facility operating envelope. Emergency shutdown (ESD) system is a part of plant (facility) safeguarding system with a purpose to keep the process within the design ...
Introduction. To minimise the interruption to production caused by a safety shutdown, the safety system should be divided into 5 hierarchical levels, with progressively wider impact on production. These levels of emergency shutdown are as follows: • Level 1: Emergency shutdown and depressurisation of the overall plant.
shutdown. While limit alarm trips are best known as a sure way to activate a warning light, siren or bell when a process problem occurs, they are also called upon to do much more. In fact, today’s highly flexible and versatile alarm trips can be found working in a wide range of applications, under an impressive list of pseudonyms.
He described how emergency shutdown (ESD) systems are different from FGS, how onshore FGS differs from offshore FGS applications, and how DeltaV SIS can be used for FGS applications. For an ESD, a process upset will result in a process shutdown.
Protection through the use of safety layers. A process plant shutdown system is a functional safety countermeasure crucial in any hazardous process plant such as oil and gas production plants and oil refineries. The concept also applies to non-process facilities such as nuclear plants.
An overview of the emergency controls of a fire alarm system.